Pedersen’s father moved to Africa in the 1960s – a decision that made him what he is today he is convinced. It is the ability to take risks, to leave a safe environment like Denmark and seek opportunities and experiences around the world.
After school and back in Copenhagen, he joined a company in the resource industry that had factories in South America. After some years living in Venezuela, Bolivia, Columbia, Peru, as a technical manager for six plants (and built two aluminum smelters to melt used beverage cans (UBC)), he and his family eventually returned to Denmark for his children to receive their education.
Driven by a vision, taught by failure
The young Pedersen was not proud of what he witnessed the South American industries doing to the environment and its people during his time there. He then set out to find a high-end technology solution for better recovery of resources. His emphasis was on metal processing and reusability, to reduce carbon footprint and the impact of hazardous waste.
In 1989, Ejvind built a plant for melting cans in Denmark, investing eight million Euro. Due to the fall of the Berlin wall, cheap metal overstocked the market and 3 years later he went bankrupt. “I lost everything”, he remembers.
Starting anew with just two
In 2002 Pedersen started ‘from scratch’ and build the company Scanmetals, as we know it today. “Sue and I (his first employee and still in the company) started by handpicking non-ferrous metals in clean material to gain higher value. Believing in his ideas, the entrepreneur finally came back to success. The 2008 financial crisis did affect the company, however, this time his persistence and determination pushed him onwards. “STEINERT was there to help when I needed a solution and they rented me their x-ray (XRT) sorting machine to produce clean aluminum products”, Ejvind explains. This was the start of his financial independence which gave him the opportunity to expand his idea throughout Europe. Today, because of Ejvind’s success, there are now many different sorting plants that exist which are used for upgrading IBA into primary resources.
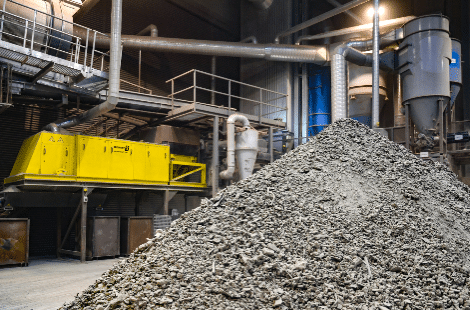
It is all about those fine non-ferrous metals
Ejvind says that six years ago no one believed in the potential of small particles in the incineration bottom ash. “We produce 4 truckloads of aluminum every day”, he points out, “one can imagine that the resource hungry industry is waiting for it!” A significant fact is that these industries do not need to source from primary mining. This can improve their sustainability report by using high quality secondary raw material.
The biggest incinerator in Copenhagen produces about 240,000 tons of bottom ash per year. “We see that approximately 20% of the waste that goes into an incinerator ends up as bottom ash. Within this bottom ash, 2% is metal – pieces that range from 1-100 mm.” At the incinerator, eddy current separation can lift the value in the bottom ash from 2% up to 50-60%. This 50-60% of treated bottom ash is available on the market for sale (approx. 1,000 Euro per ton). “This means we pay 2,000 Euro for 1 ton of metals. The small pieces are important to me.”
Closed-loop production with STEINERT’s accurate separation and sorting technology
Ejvind’s focus is on aluminum and the high-end quality metals acquired from secondary smelters. He invests in the technology for the removal and reduction of free heavy metals and aluminum alloys. The process starts with a non-ferrous metal separator for the ZORBA-recovery from the IBA material, followed by the induction sorting system, which extracts stainless steel in the next step.
Reducing dependency on primary metals
STEINERT XSS T (X-ray transmission) produces very clean aluminum by sorting out heavy metals and high-alloyed aluminum. The sorter detects so accurately that it creates a product quality of 99.9% pure aluminum.
The STEINERT KSS FLI XF (X-ray fluorescence) is a state-of-the-art solution for the separation of the heavy metals into copper, brass, zinc and precious metals. More than 97% purity of heavy metal products have been achieved.
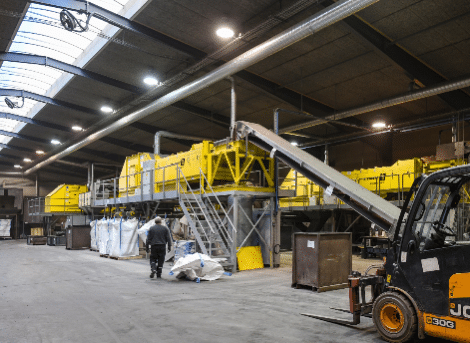
Customers e.g. aluminum smelters, produce beverage cans from almost 100% of Scanmetals’ production of that type of aluminum. Here, the closed-loop approach gets real. In the production of beverage cans, producers have to take pure, new aluminum from mines. Ejvind’s customers are very satisfied with Scanmetals’ recovered resources quality so much so they do not need to buy aluminum from the mines (primary aluminum); it is a real win-win situation because the buyer can also improve their sustainability rates. Also, note that recovered aluminum can also be recycled up to 10 times without losing its quality.
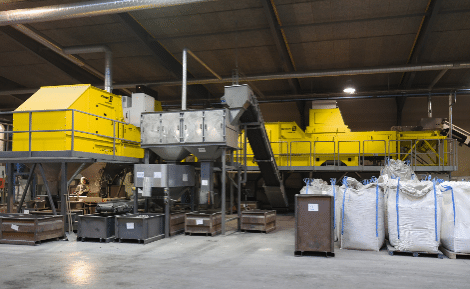
“As reliable and efficient as a German car”
Scanmetals is comfortable in the knowledge it can source all its magnetic and sensor sorting solutions from one partner. That includes the non-ferrous metal separators, induction sorting, XRT, and XRF – essentially making life easier and allowing for more productive time to be spent on new recovery ideas.
“Put it this way”, Ejvind says, “There is no doubt that German cars are the best in the world. That is a fact”, he states. “I would put STEINERT on the same platform – efficient like a German Audi, reliable like a German Volkswagen. All my production people trust them. The machines are easy to handle and all the technical components are easy to understand and use.”
Scanmetals’ consequent market and demand orientation makes the company successful
Not only is material quality the key to success, but also the delivery time of the resources – “just in time”. This makes reliable machinery a crucial factor for material recovery success. When the company supplies aluminum to smelters – delivering to brands such as BMW “just in time” – Scanmetals need to deliver on time too. Ejvind Pedersen has tailored his business in accordance with his customer’s needs and market demands.
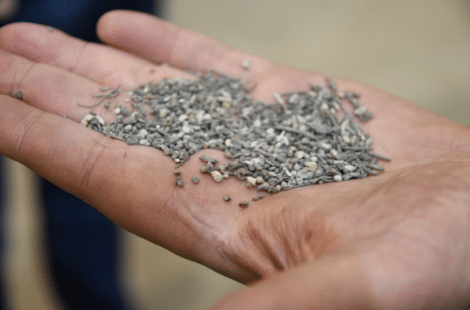
Downtime is a critical situation. “If we would be late, another supplier would be preferred. But we have very little downtime”, Ejvind admits, “The Service department of STEINERT is highly educated and helps us right away.”
Winner of the prestigious “EY Entrepreneur of the year 2018” Award
At the awards ceremony, Ernst & Young awarded Ejvind Pedersen with the prize for “Innovation”. This was for his contribution to the industry via impressive business growth rates, innovative strength, and social commitment.
During his acceptance speech, again, Ejvind took a chance. He asked if somebody would invest in his idea, to bring his idea to the world by creating jobs that save resources. “I learned from mistakes. I made a business that is so strong and a new idea that has a lot of future. I always had challenges, I always had a possibility and I succeeded. That gave me confidence.”
Asking what is special about this prize, he says, “Being recognized for my work. I felt I achieved something in life. They saw the ideas I have and that I can make them come true. That is also what the prize means: “Being an entrepreneur”.
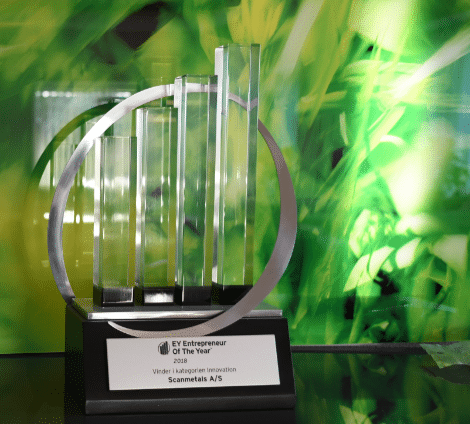
One week after the award, Ejvind succeeded again. The family of Lego called and came on board. They trusted in his ideas and plan to invest for expansion of his next projects in Europe – so that the material continues to stay in the loop.
Throughout his life experiences, Ejvind has also managed to accomplish learning 7 different languages, and he is also worldly and cultured. These challenges, attributes, and achievements contribute to the exceptional person he is today. STEINERT takes its hat off to this winning entrepreneur and looks forward to continuing to work alongside him and his new ideas in the future.
Last but not least:
Scanmetals can build and put a new plant into operation within a year after environmental permission has been granted. They will operate the new plant themselves, in joint ventures or in cooperation.