Recycling of plastics is not only crucial for climate neutrality, it also conserves valuable resources and the environment. Many sectors of the plastics industry are consequently undergoing a transition. The aim is to increase the recycling rate and use the advantages of plastic in such a way that no damage is caused to the environment. “We’re seeing an increasing demand for high-quality plastic recyclates,” says Martina Schmidt, head of the Recycling and Waste Division at Vecoplan AG. “Many manufacturers are introducing closed cycles because it gives them direct control.” Vecoplan is one of the leading suppliers of machinery and equipment for processing primary and secondary raw materials for thermal and material recycling. For years, it has been a successful and reliable partner to the recycling industry. Now, in a further contribution to closed-loop recycling, the system provider is offering additional processing options. “Plastics recycling at a suitable level of cleanliness is becoming increasingly important,” says Schmidt. “By offering this to our customers, we can give them even greater support. At the end of the process chain they get a material that is ready for the extruder.”
At its new technology centre in Neunkhausen, Vecoplan has installed a demonstration and test facility called the Cleanikum, which covers some 600 square metres. Together with Vecoplan’s experts, customers can run cleaning tests with film waste and thin-walled hard plastics made from polyolefins like LDPE, HDPE and PP. The facility, which features a new combination of machines for cleaning plastic, processes it to yield high-quality extrudable flakes that can find use in the manufacture of consumer goods, packaging and cosmetics. “Our approach is purposely different from conventional solutions,” says Martina Schmidt. “Our developers have optimised the processing method to provide better cleaning quality while reducing energy and water consumption.” Vecoplan’s engineers worked closely with a network of experts to achieve this practical solution.
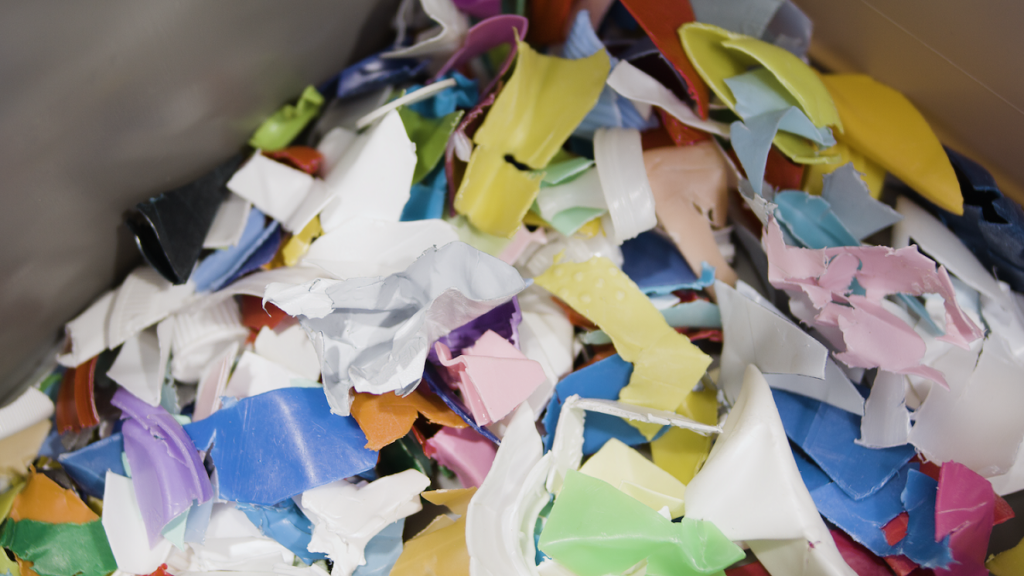
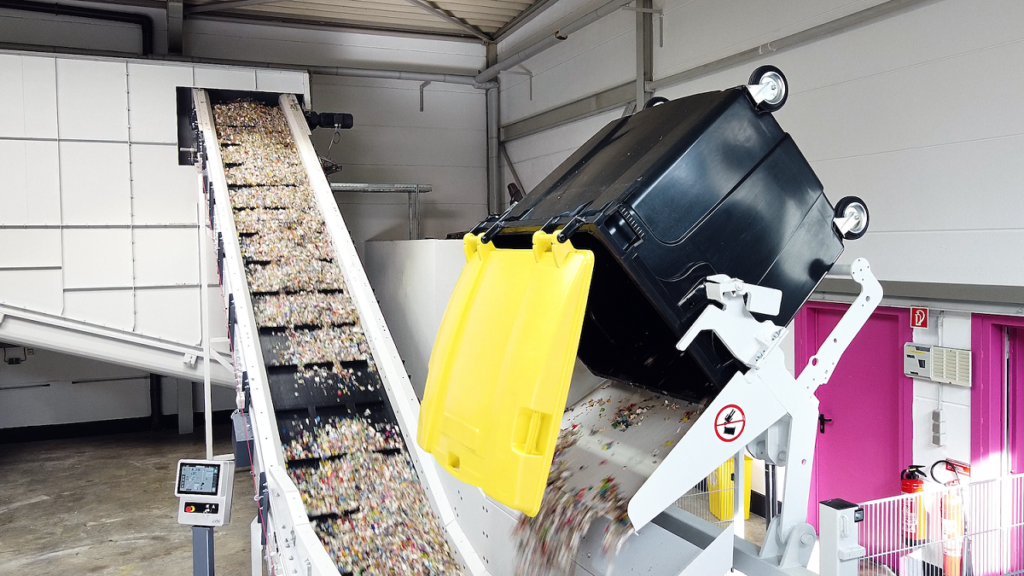
New process
The Cleanikum demonstrates the systematic use of cleaning and separation technologies that help to cut back on the use of energy and water. Post-consumer waste can be cleaned in a cold or hot process and with or without lye – depending on the degree of contamination and the quality requirements for the recyclate. The combined demonstration and testing facility is able to handle polyolefins in the form of plastic film or used bottles.
“We rely on mechanical dry pre-cleaning, which means there is no conventional pre-wash,” says Schmidt. “This lowers our use of fresh water, and we can significantly reduce the quantity of waste water. The facility thus demonstrates processes that are economical in the use of water, an important resource.”
High cleaning quality
The required degree of cleanliness can be customized according to the user’s requirements. In addition to wet or dry mechanical cleaning, the Cleanikum can demonstrate temperature-controlled intensive heating using a sodium hydroxide (NaOH) solution, for example when the regranulate is needed for the consumer goods or cosmetics industry. This is an effective means of dissolving greasy and oily impurities and of removing adhesives from labels.
Efficient water treatment
Vecoplan prepares the cleaning lye in the Cleanikum separately from the process water. Instead of using the lye or process water until it is saturated with contaminants and then cleaning it, the waste water is fed via collection lines at every point in the facility to a specially designed water treatment system where it is cleaned and returned to each component. “This reduces our use of fresh water and lye while also improving the cleaning quality,” says Schmidt. “It is our contribution to sustainable recycling.”
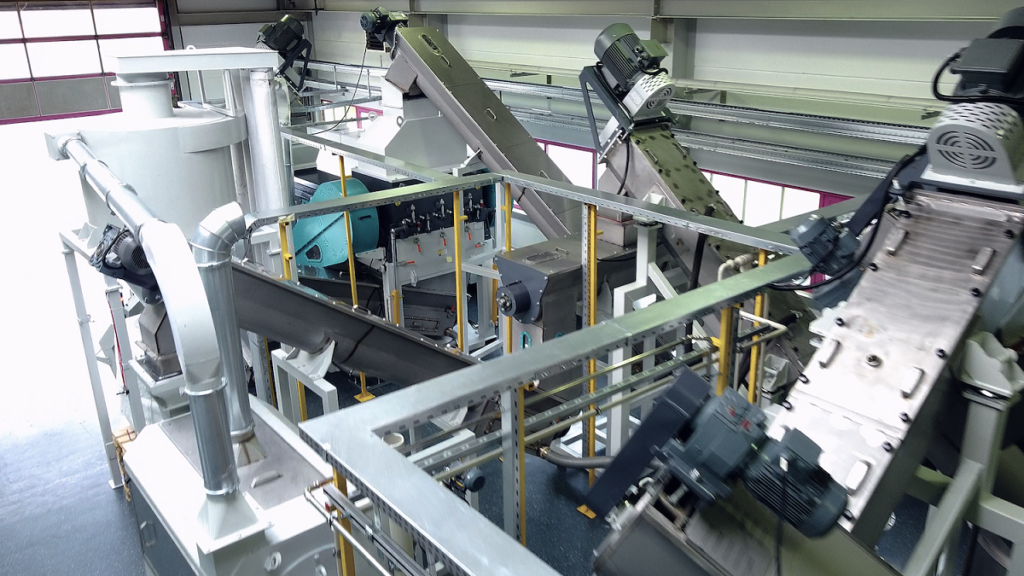
Processing of plastic film
In post-shredding, a wet granulator shreds the cleaned plastic film to the particle size required for drying and extruding. A combined friction separator and dewatering screw then dries the material mechanically to a residual moisture of five to six percent. The use of mechanical instead of thermal drying demonstrates how it is possible to improve the environmental footprint of plastics recycling.
Processing of hard plastics
After dry and wet cleaning, thin-walled hard plastics are sent directly to a turbo dryer, which ideally can reduce the residual moisture to only two percent. The processed plastic flakes are then ready for subsequent sorting or extruding.
“This process gives our customers a highly reliable means of processing plastics,” explains Martina Schmidt. “Closed-loop recycling helps them to achieve better-quality recyclate and reduces the burden on the environment.”