The Olympus is designed to combine the throughput capacity of disc screens with the low-maintenance reliability of ballistic separators, without the traditional trade-offs.
Solving a Common Challenge in Recycling Facilities
In the world of single-stream material recovery, two technologies have long dominated 2D/3D separation: disc screens and ballistic separators.
Disc screens are fast and capable of handling high volumes, but are prone to jamming, especially with films, bags, or oversized paper. Their high-maintenance needs can result in frequent system shutdowns.
Ballistic separators offer lower maintenance and more reliable performance, but their slower throughput often limits scalability.
The Olympus was built to do both, without compromise.
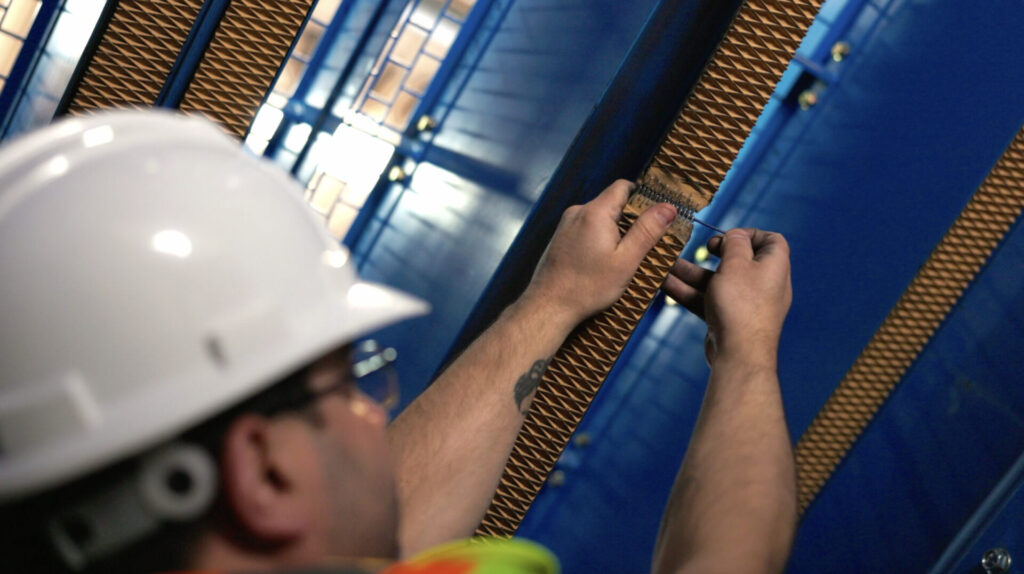
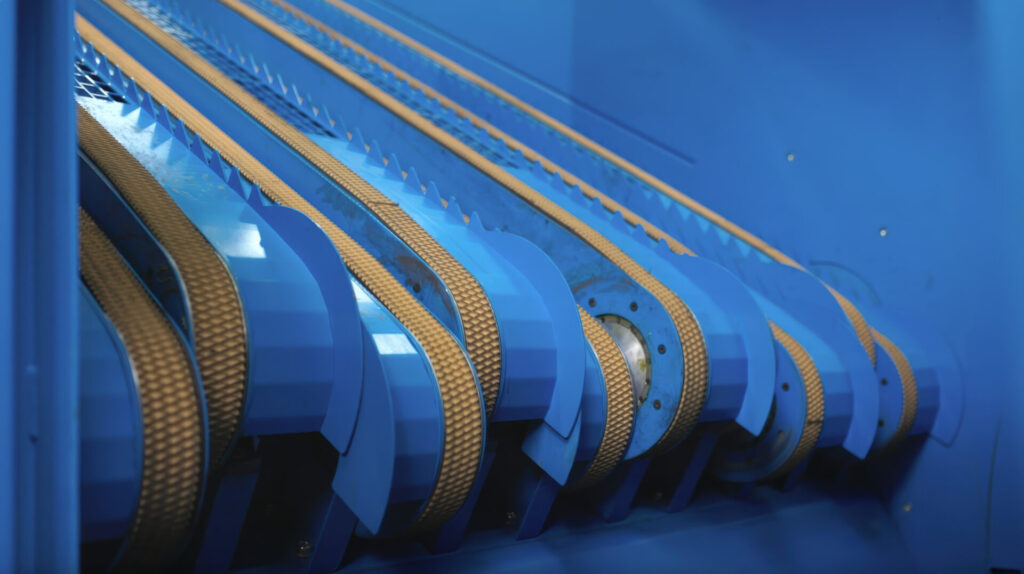
Engineering Built for the Real World
Sparta designed the Olympus from the ground up with one goal in mind: create a smarter, faster, and more accessible separation system that works under real operating conditions.
Key innovations include:
Circular Motion Paddle System: Enables quick separation of 3D materials while minimizing wear and power consumption.
Electronically Adjustable Mesh Screens: Allows operators to fine-tune incline angles through the onboard HMI to optimize material stratification.
Precision Belt System: Easy belt tracking and replacement with a gas-strut cylinder mechanism, tool-free and single-operator friendly.
Five-Speed Adjustable Fans: Offers precise airflow control to support higher purity in both 2D and 3D fractions.
Modular Shaft Design: Enables fast paddle swaps without dismantling the entire line, minimizing downtime, and simplifying maintenance.
Integrated HMI Interface: Offers real-time control, diagnostics, and upgrade capabilities, giving operators full visibility and system control.
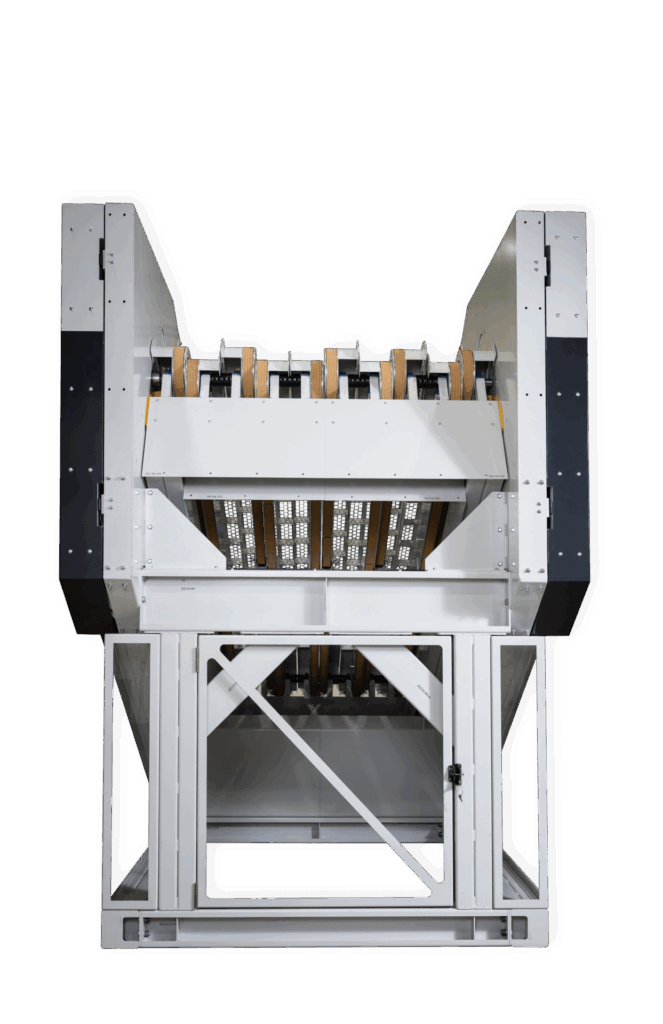
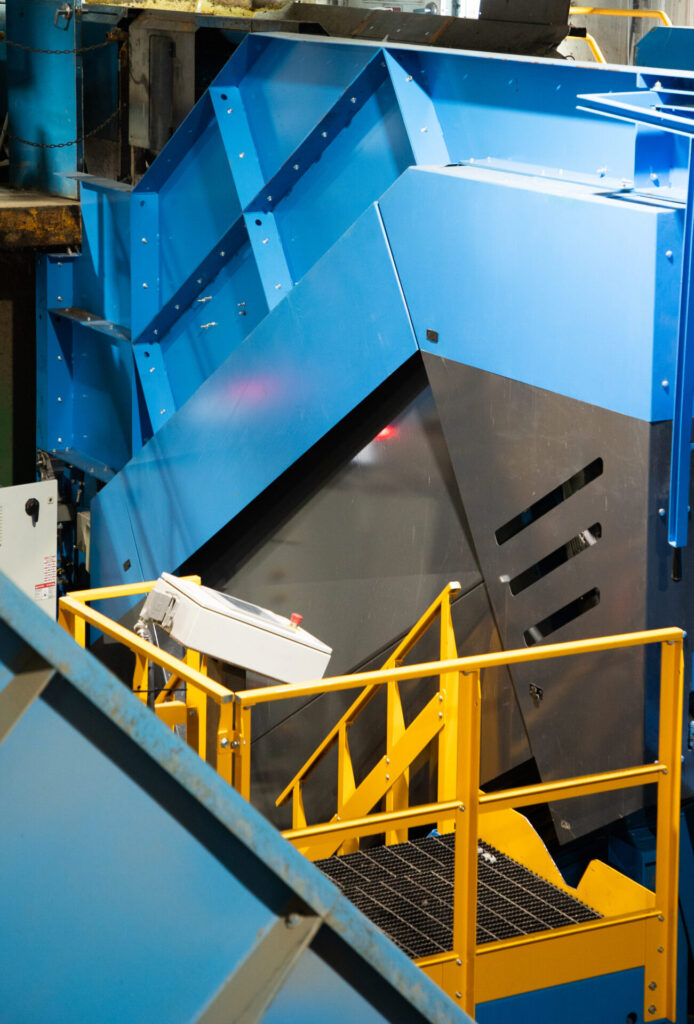
Field Deployment in Action
As the first facility to integrate the Olympus into its single-stream recovery line, Eco360 in Moncton, NB, has provided invaluable insight into how the system performs under real-world conditions. Installed in October 2024, the unit in operation features a 10-paddle configuration powered by two 10hp motors and is currently processing approximately 7 tons per hour.
With over 1,200 run-time hours logged to date, early operational data points to the Olympus’ core strengths: streamlined maintenance, responsive controls, and practical serviceability. Cleaning routines, initially requiring two 30-minute sessions daily, are already trending toward a single 30-minute session, while full-system greasing, currently done every three weeks, is expected to shift to every two months as confidence grows.
Designed for resilience, the Olympus enables quick paddle swaps, just under three hours for a full pair replacement, ensuring that even in the case of a mechanical issue, downtime remains minimal.
Operators are also using the system’s adjustable deck angles to respond to changing 2D material quality in real time. This kind of process control is essential in today’s MRF environments, where feedstock variability is more the norm than the exception.
Control, Flexibility, and Operator-Centric Design
Instrumentation and control are often afterthoughts in material handling equipment. The Olympus flips that mindset.
Its HMI-driven control system is built into the core of the machine, allowing operators to:
- Adjust performance in real time based on material conditions
- Reduce intervention and manual adjustments
- Access system diagnostics and alerts for preventive maintenance
- Implement future performance upgrades via simple software updates
This approach not only reduces learning curves for staff, but also improves uptime and productivity, something especially critical for facilities with limited resources or high labor turnover.
Innovation Driven by Need
The Olympus was not born from a product roadmap; it came from field feedback. Sparta’s engineering team had spent years hearing the same frustrations from clients: too much maintenance, not enough flexibility, and the constant challenge of balancing throughput with material purity.
The result is a system that does not ask facilities to choose between speed and simplicity. Instead, the Olympus sets a new benchmark by fusing the strengths of both legacy technologies into one future-ready platform.
And it is already proving its value in the field.
For Eco360 and other early adopters, the Olympus represents more than just a machine. It’s a sign of where the recycling industry is headed toward smarter, cleaner, and more resilient operations.