For nearly 150 years, FANTONI S.p.A. has been a benchmark in producing engineered wood products like Medium-Density Fibreboard (MDF). Four years after commissioning one of Europe’s most advanced sorting facilities, a revisit to their headquarters confirms the lasting success of a truly visionary project. Where many in the industry struggle to achieve 15-20% recycled content, enabled by STEINERT, FANTONI now routinely produces premium MDF panels with up to 70% recycled material in their core layers. The facility processes approximately 450,000 tonnes of recycled wood annually, a testament to a bold engineering vision that has redefined what is possible in sustainable manufacturing.
The Engineering Challenge: Purity on an Industrial Scale
The raw material for this process is post-consumer wood waste, a complex and contaminated stream containing everything from nails, plastics, and glass to stones and minerals. For particleboard, which FANTONI has successfully made from 100% recycled wood for years, the tolerance for impurities is higher. For high-quality, furniture-grade MDF, however, any contamination can compromise the board’s structural integrity, surface finish, and severely damage critical downstream equipment.
“We decided to take a different approach,” explains Marco Fantoni, a member of FANTONI’s board. “We designed the plant ourselves, with our own process engineering, and selected the best technological machines for each specific task.” This engineer-led approach, backed by a €150 million investment, demanded a partner who could provide not just machines, but a robust, integrated, and—above all—reliable solution.
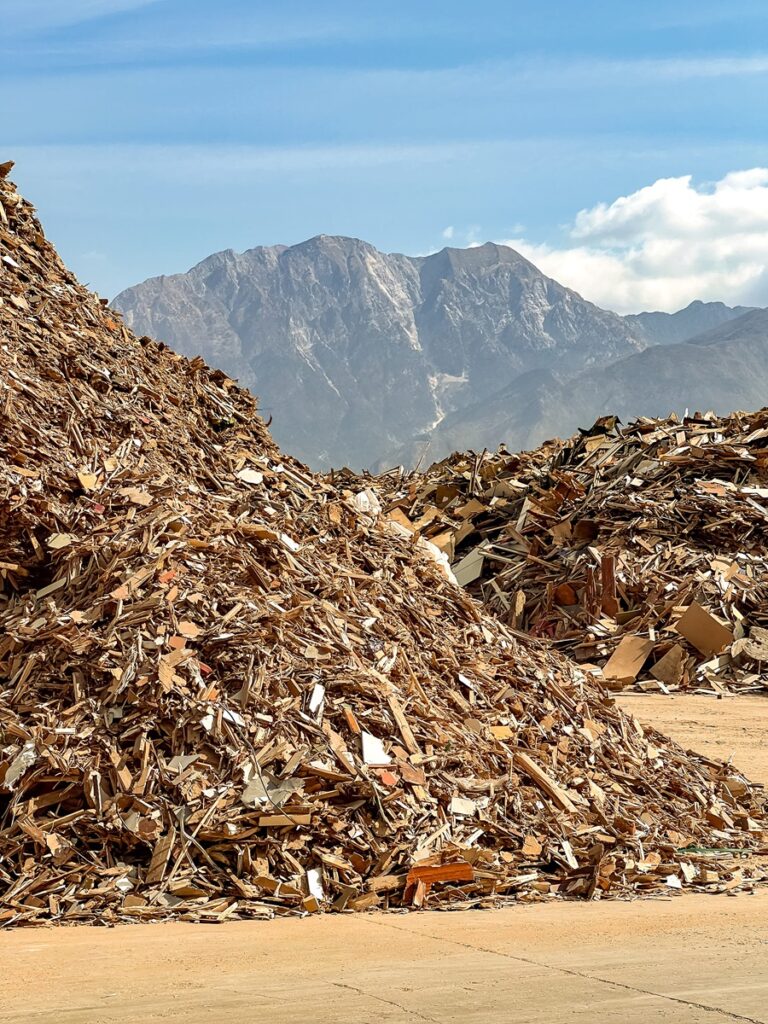
Engineering Excellence Proven Over Time
For FANTONI, reliability is paramount. The decision to engineer the sorting plant in-house demanded technology that could withstand the rigors of continuous industrial operation. Four years later, the verdict is clear. “The mechanical construction is quite robust,” reflects Fantoni. “After almost four years of continuous operation, I have to say that we were right about the concept we had.” This long-term stability is the foundation of their success. As Fantoni notes with satisfaction: “The fact that I’m not aware of recent maintenance problems speaks volumes about the system’s reliability.”
The STEINERT Advantage: Integrated Technology for Unmatched Purity
FANTONI’s success hinges on a multi-stage sorting process, for which STEINERT was chosen as the sole sorting technology provider—a key advantage that eliminates the complexity of coordinating multiple suppliers. The integrated system includes:
- Metal Separation: The process begins with magnetic separation and eddy current technology to remove both ferrous and non-ferrous metals, protecting downstream machinery.
- Dense Contaminant Removal: STEINERT XSS® T X-ray transmission sorters then remove dense foreign materials like glass and stones. “The X-ray does an excellent job of extracting materials that could be dangerous for the process itself,” notes Mr. Fantoni.
- Wood Purity and Species Separation: The final, crucial step is handled by STEINERT UniSort systems, enhanced with proprietary Hyperspectral Imaging (HSI) technology. HSI technology uses advanced spectral analysis to identify material composition at the molecular level, enabling precise separation of different wood types and reliable removal of contaminants, including difficult-to-detect black plastics. Unlike conventional approaches requiring complex AI overlays, STEINERT’s HSI provides a robust, native solution that reduces complexity and operational costs. “Detecting black material was a challenge, and STEINERT was very well prepared in this respect,” Fantoni recalls.
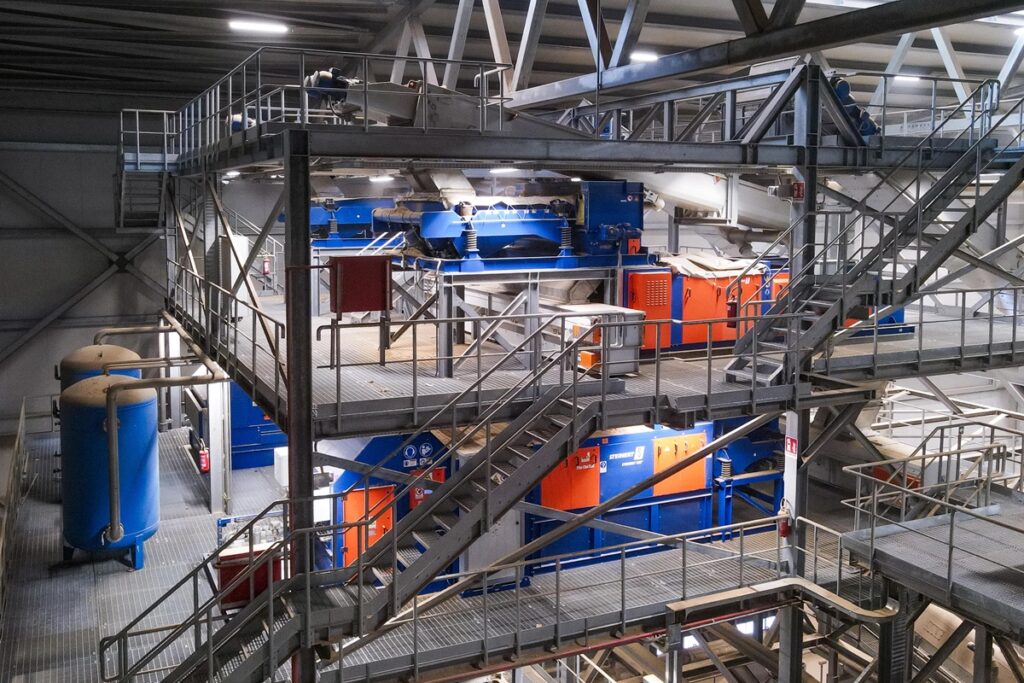
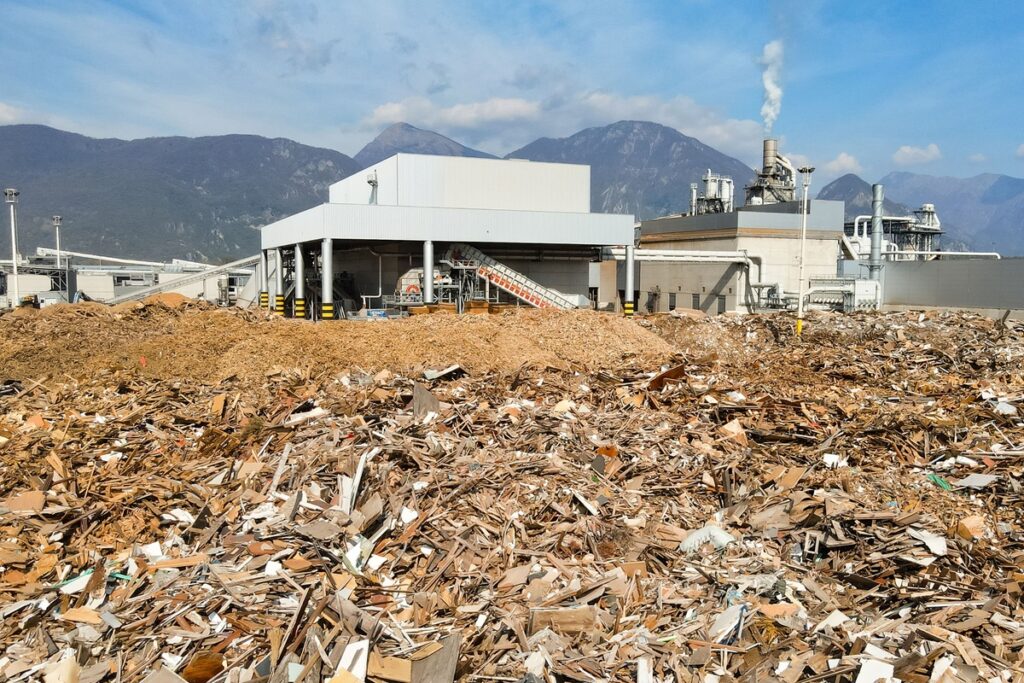
A Partnership in Engineering Excellence
The collaboration went beyond supplying machines—it was a true engineering partnership. Marco Fantoni emphasizes the importance of the extensive trials conducted at STEINERT’s Test Center in Cologne: “The relationship was very good. I must stress the importance of the tests we did at the Test Center, where your team illustrated the different technologies and what was most suitable for our needs.”
This partnership extended to on-site support during the crucial startup phase, where STEINERT teams worked to optimize the machines for different material flows. “Startup was a very important moment where we had to prove efficiency in terms of cleanliness and learn how to optimize machine settings,” Fantoni reflects. “Having your teams here for the necessary period was of utmost importance.”
Beyond Wood Waste: A Truly Circular Model
Perhaps FANTONI’s most significant breakthrough is pioneering a process that recycles not just post-consumer wood, but end-of-life MDF panels themselves. “We can also use waste MDF again in the process, which is very important because recycling MDF itself is a known problem,” explains Marco Fantoni. This creates a truly circular production model where today’s furniture becomes tomorrow’s raw material.
Market Leadership Through Innovation
Today, FANTONI produces a three-layer MDF panel where virgin wood forms the flawless outer surfaces and recycled content comprises the core, processed on Europe’s longest press at 65.5 meters. The sophisticated production process integrates STEINERT’s sorting systems with fiber refinement, resin application, and thermal drying.
The company backs its environmental claims with scientific rigor, investing in Life Cycle Analysis (LCA) studies and Environmental Product Declarations (EPD). “We have invested a lot in making LCA studies and EPD certification of the material to have recycled wood that is scientifically proven,” Marco Fantoni explains.
“With this technology and this project, we are now well ahead of the curve in using recycled wood for fibreboard production,” states Marco Fantoni.
The Path Forward
FANTONI’s facility demonstrates that achieving 70% recycled content in premium wood panels requires proven technology and engineering excellence. As regulatory requirements increasingly drive demand for recycled content, this approach offers a roadmap for the industry’s sustainable future—proving that environmental responsibility and market leadership can advance together.
Manufacturers seeking similar sustainable production solutions can leverage STEINERT’s comprehensive sorting technologies and engineering expertise to achieve environmental goals and operational excellence. Those interested in learning more can explore the technical details and capabilities on STEINERT’s website, www.steinertglobal.com, and contact a specialist.
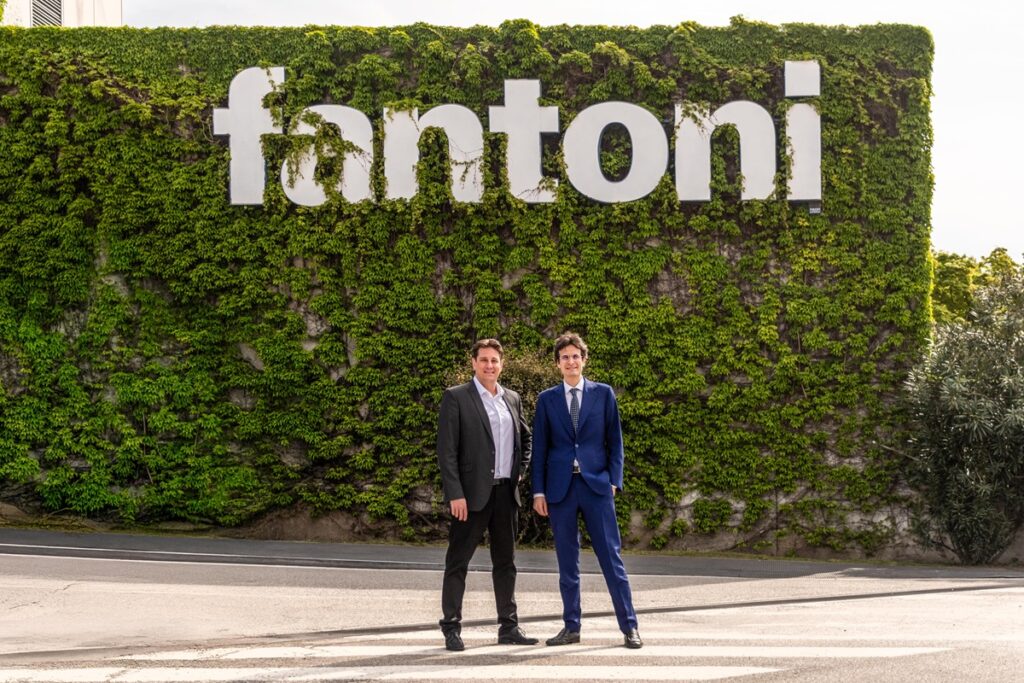
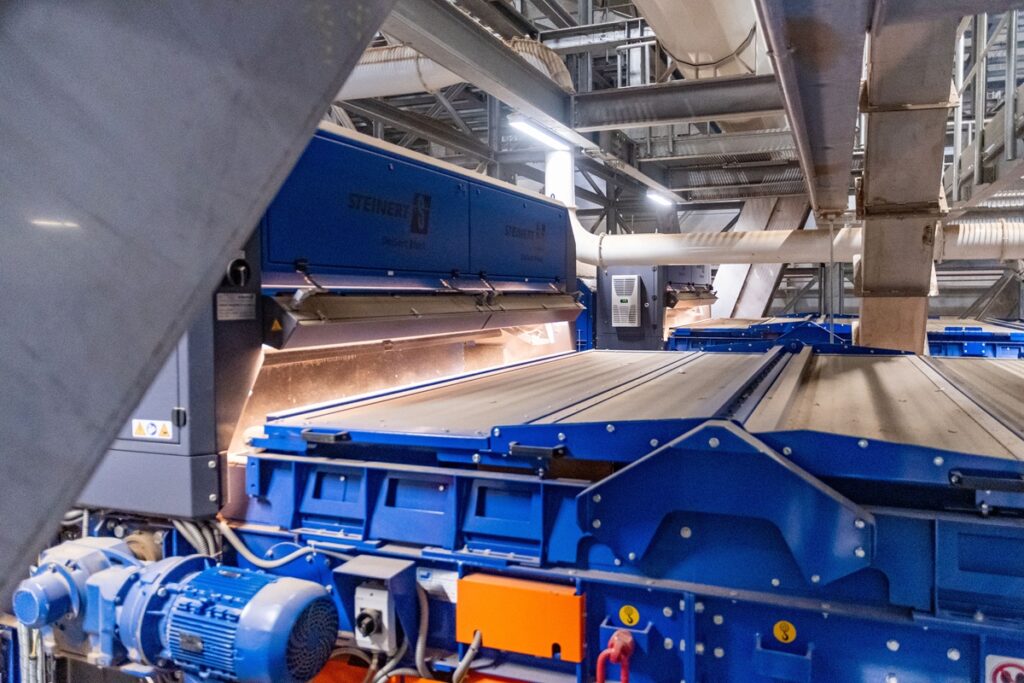