Smurfit Kappa’s Nybro (Sweden) plant produces good-looking cardboard, the kind used for packages on display – boxes for bag-in-box wines, for example. When the cardboard is cut to the correct shapes needed for the end product, trims is generated. These cardboard clippings are transported via pipes in the ceiling and on the roof of the building to a pair of compactors standing outside. From there the compacted trim is transported away from the plant.
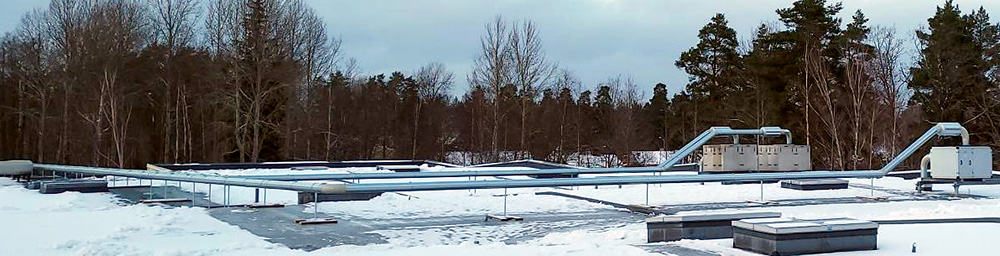
Pipes lead long pieces of trim to chopper fans (the boxes) which cut the cardboard into smaller pieces. The trim is then transported to two compactors
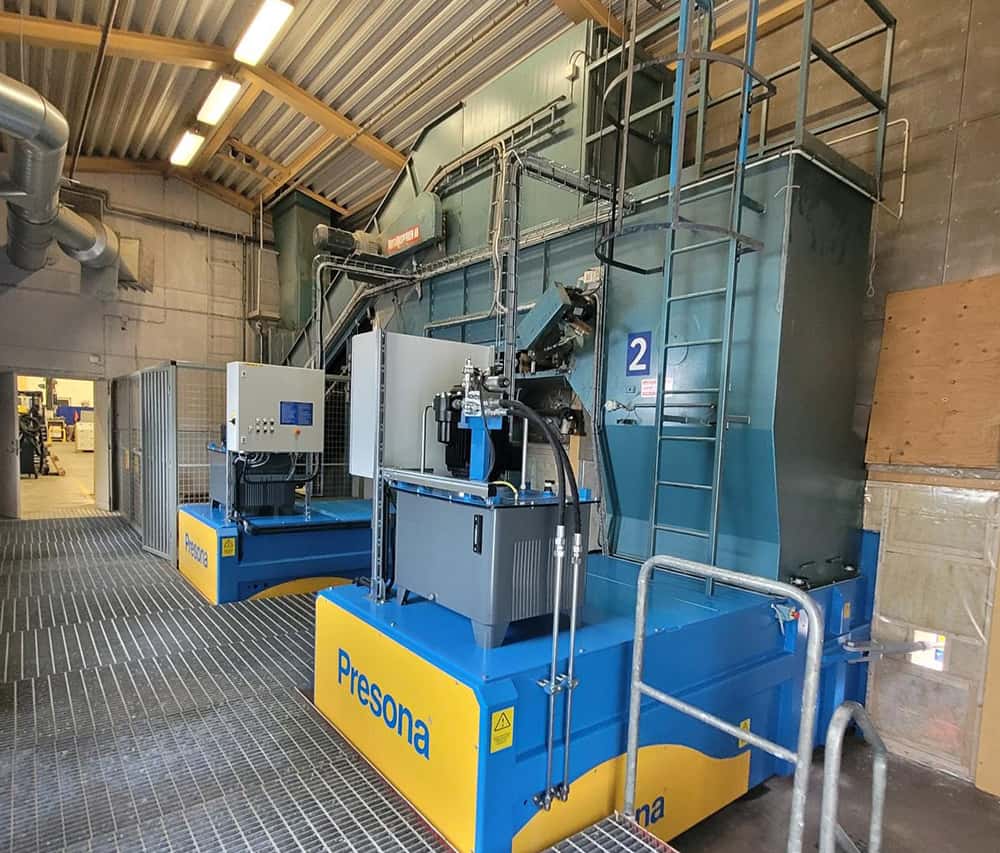
Trim from both the old and new machines is transported to two compactors. These compactors were installed in 2022 and replaced two Presona compactors from 1986.”
Extraction needed
When Smurfit Kappa decided to upgrade their machinery they contacted longtime supplier Presona to help with the trim extraction.
– The big challenge was that we wanted to run both the old and the new laminator at the same time while we conducted tests and staff training on the new equipment, says Smurfit Kappa operations manager Eric Johansson.
The simple solution would have been to build a totally new and separate trim extraction system for the new machine, but Smurfit Kappa wanted to keep as much as possible of the old Presona extraction system which has been working very well for many years. This way Smurfit Kappa would save money and keep a system they knew was functioning as it should be. The solution: An expanded system that shares several vital components like the main fan, filter and compactors.
Air pressure can be tricky
While that may sound easy, actually doing it is another thing completely. Working with air pressure and transporting materials with the help of fans can be challenging – especially if you want a robust and reliable solution that will keep going and going and going…
Presona has extensive experience in finding solutions for demanding use cases and this challenge was no different. Smurfit Kappa is very happy with the delivery.
– Presona delivered a better solution than the one we ordered. The Presona team is solution-oriented and we received many good suggestions during our discussions with them, says Smurfit Kappa maintenance manager Kalevi Nordström.
When the new laminator is fully up and running the old machine will be decommissioned with several of its extraction system parts serving as spares for the new sections of the system.
The new laminator
Bobst Masterflute Touch – the most modern inline laminator in Northern Europe. It is 78 meters long (100 meters when the logistics systems is included) and can produce 220 meters of quality cardboard per minute.