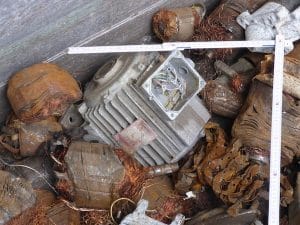
Electric motors and motor armatures represent a small fraction of waste from incineration or large shredders, and it is difficult to cleanly separate them by type. Yet they contain a good deal of valuable copper, with up to 22 percent copper by content.
This impressive new procedure features a Rotorshredder optimized for this process, subsequent materials separation, and the purification of copper in a rotor impact mill.
Innovations emerge from different paths. In this case, a Dutch customer approached the team at BHS-Sonthofen, a leader in impact crushing technology.
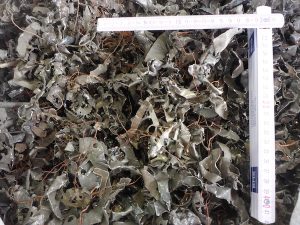
Their goal was to optimize a process for recycling electric motors and motor armatures in order to significantly increase Non Ferrous metals concentrations, without impacting operational efficiency.
This request was based on ever increasing demand for high purity metals – a trend that has been going on for several years and is becoming more and more pronounced, especially in Asia.
The traditional method uses a hammer mill to crush the meatballs. Given the traditional design of the hammer mill, crushed parts come into contact with each other. The resulting new metal compounds become entangled and subsequently almost impossible to separate into single stream fractions.
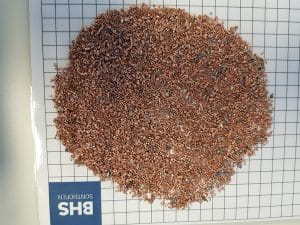
In addition, the ejectors in the hammer mill are designed in such a way that the individual parts inevitably jam. The greatest challenge faced by the BHS engineering team was to treat the materials in such a way that clean separation could be achieved.
Impact crushing with the Rotorshredder
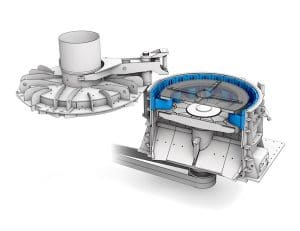
The experts at BHS have many years of experience as well as in-depth knowledge of the process – and this paid off. “The most important requirement, along with high product quality, was that the discharged material be of the highest purity possible. In order to attain this goal, we conducted a thorough and in-depth analysis of the process together with the customer. Multiple detailed tests performed at our technical center with the customer’s material served as the foundation for this analysis,” says Nikolas Kaufeisen, Sales Manager at BHS-Sonthofen. “The result is a solution that improves the process in several ways, one that is tailored exactly for this specific application.” The meatballs can be selectively broken apart in the BHS Rotorshredder. The hammers, mounted on a vertical shaft, transfer impact forces to the feed material, and the pieces collide with the openings of the grid segments in the doors, which work like stators. The engineers at BHS adapted the mounting brackets for the grid segments especially for this application. This was done in such a way that the adhesions from waste incineration cannot collect behind them, which would cause the machine to constantly block. Grid fixings arranged vertically instead of horizontally prevent material from collecting behind the grid openings. The ejection system is also designed in such a way that the shredded parts drop down across the full width of the discharge conveyor belt and do not come in contact with each other again. This ensures that the material cannot become entangled.
After the material is discharged, the shredded metal runs under an overhead magnet mounted in line to the discharge conveyor belt, which separates the ferrous fraction from the rest of the material. BHS also optimized the process here. If the overhead magnet had been installed diagonally to the conveyor belt, as would typically be the case, then longer iron parts would drag over the belt and become entangled with other parts. Thanks to this change, the remaining parts move along the conveyor without becoming caught or stuck on the belt. A cross-flow sifter then uses a stream of air to release the copper portion of the material from stainless steel parts and heated, non-magnetic iron parts.
Copper is treated in rotor impact mill to deliver high metal concentrate quality
The rotor impact mill (RPMX) from BHS is well-suited to removing impurities from copper fractions extracted from the material. This is an upgrade to the traditional rotor impact mill, a high-performance crusher with a vertical shaft and unique impeller rotor. The RPMX for recycling applications stands out because of its higher circumferential speed and a smaller milling gap. Copper wires can also be processed, even though their small size had made it difficult to recycle them until now. The quality of the individual parts improves significantly with the rotor impact mill: Discoloration on the surface of the wire caused by oxidation during waste incineration is removed. The machine also releases the remaining insulation from the copper wires and ensures the optimal particle shape enabling clean separation by type, using air separation systems.
The result is a high-quality metal concentrate that is of the same quality as copper recycled from cables. The customer is highly satisfied with the process. They now have two of these systems in use in the Netherlands and another one in western France.