To truly reduce textile waste we need to reduce contamination, reduce sorting complexity, and reduce the barriers that keep textile-to-textile recycling from scaling. That’s where advanced preparation technologies Today’s textile waste is highly heterogeneous. A single load might include pure cotton T-shirts, polyester blends, and wool sweaters, all mixed with non-textile elements. Compressing that chaos won’t make it recyclable. What’s needed is a smarter form of reduction — one that breaks the problem into manageable parts.
Technology to the rescue
Manual sorting is no longer viable. Human sorters can’t reliably detect fiber blends or spot small contaminants. Visual inspection is slow, inconsistent, and too dependent on garment labels — which are often missing or wrong.
Enter automation. Modern recycling lines use AI, robotics, and near-infrared (NIR) spectroscopy to scan garments for fiber type and color in milliseconds. This ensures a consistent and accurate classification, unlocking higher throughput and feedstock quality.
Belgian machine builder Valvan developed two standout innovations in this space: Fibersort® and Trimclean®.
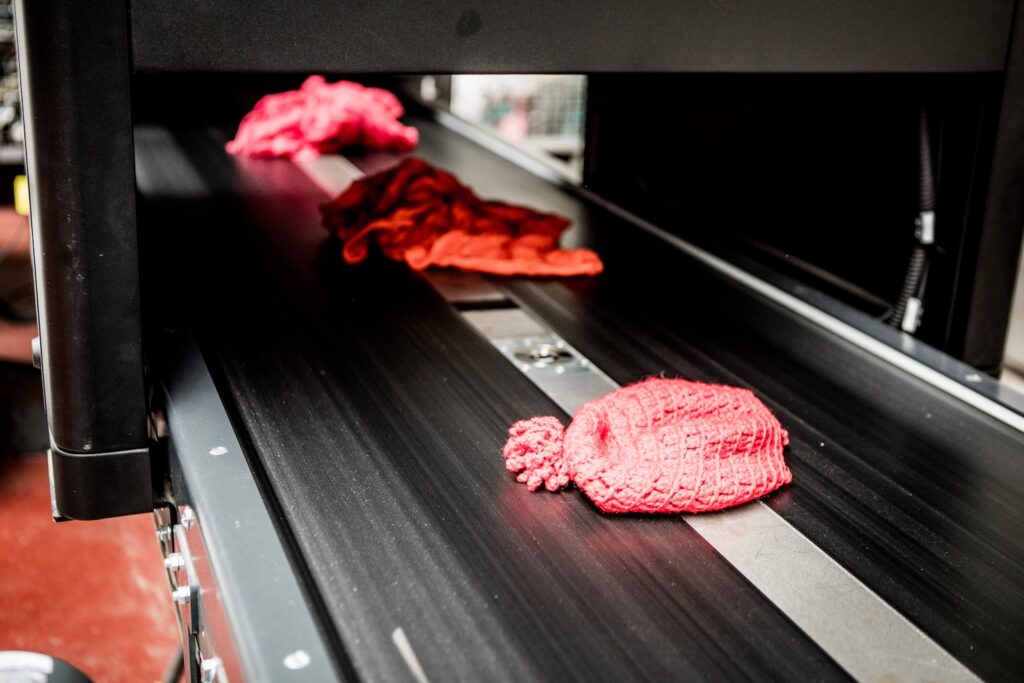
Fibersort: know your material
The first step in any recycling process is understanding what you’re dealing with. Fibersort automatically scans each item’s fiber composition and color using a combination of 3D cameras, RGB imaging, and NIR spectrometry. It identifies whether a garment is made of cotton, polyester, wool, or a blend — and then sends it to the correct output stream.
The result? Homogeneous batches that are ideal for mechanical or chemical recycling. Fibersort even sorts by color, which can eliminate the need for re-dyeing down the line. It’s a massive leap from relying on guesswork or garment tags.
Trimclean: purity through precision
Even after fibersorting, textiles often carry unwanted elements — metal buttons, plastic tags, velcro, or synthetic linings. Trimclean tackles these with surgical accuracy. Processing pre-cut textile clippings, it uses patented dual-sided camera inspection, metal detection, NIR scanning, and AI to identify and separate contaminants.
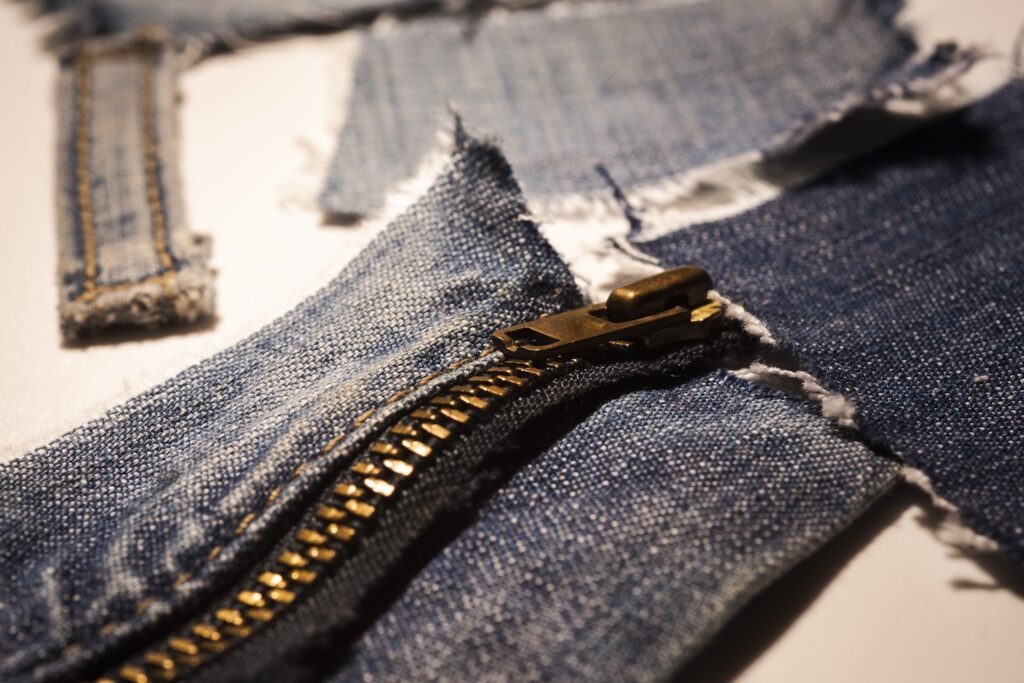
The result is high-purity output: clean clippings that are ready to become new garments. While 10–15% of material may be lost in the process, the trade-off is worth it. Contamination ruins batches — precision protects them.
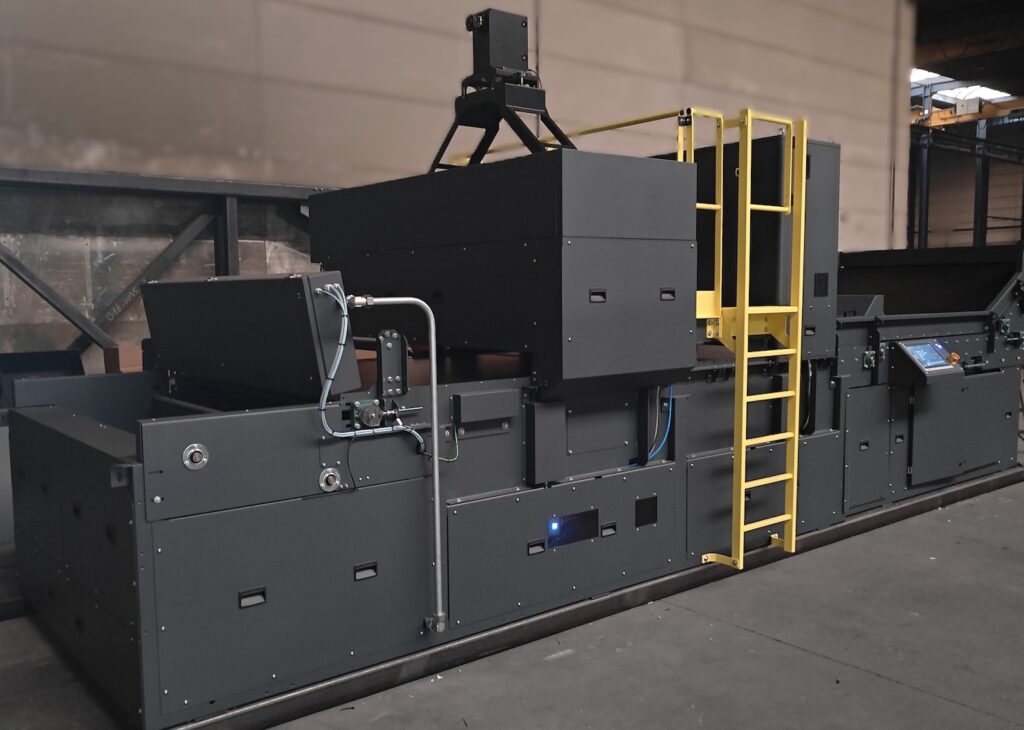
Smarter input, stronger output
Together, Fibersort and Trimclean reduce complexity at its source. Fibersort ensures recyclers know exactly what a textile is made of. Trimclean ensures it’s only that. This refined input leads to better recycled yarns, fewer machine breakdowns, and a higher percentage of textiles re-entering the production cycle — instead of being downcycled or landfilled.