At Umweltkontor Bergkamen we show how two experienced industry specialists successfully cooperate. The comprehensive modernization of the waste wood processing plant by ALLRECO GmbH and SPALECK GmbH & Co. KG is marked by a significant improvement in efficiency, profitability, and sustainability.
Improving profitability and efficiency
Umweltkontor Bergkamen is part of the Geiger Group and with a capacity of several hundred thousand tons per year is one of the most competent and efficient waste disposal companies in Germany when it comes to waste wood. True to their company philosophy: “Raw materials are the most valuable thing that can be recovered” in 2022 the company from the Ruhr area commissioned ALLRECO GmbH with a groundbreaking modernization project. The goal was to renew the processing plant, which had become outdated after 75,000 working hours and to significantly improve profitability and productivity.
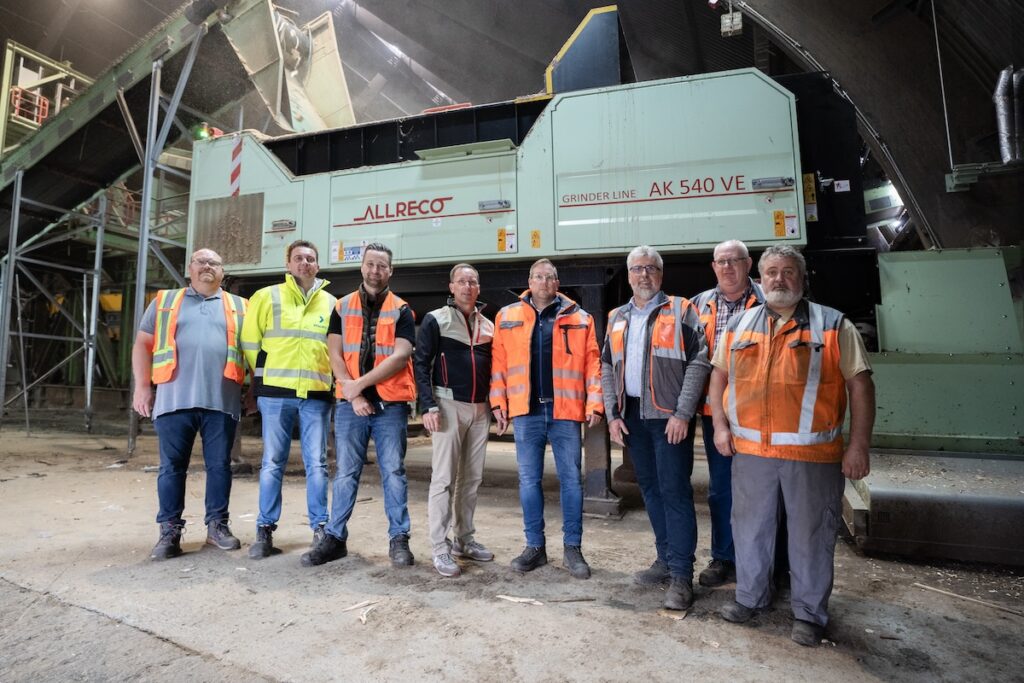
Strong partnership for optimum customer solution
For recycling specialist, ALLRECO, it was clear that only the best result is acceptable in order to fully meet the requirements of Umweltkontor Bergkamen to best return the waste wood as raw material back into the circular economy. With this aim in mind, the Velbert-based company entered into a cooperation with the traditional mechanical engineering company SPALECK. Henning Strunz, Managing Director of ALLRECO GmbH, said: “The cooperation was solution-oriented focused on the customer. This kind of well-functioning team play enabled the smooth integration of the new pieces of equipment into the existing plant. This makes waste wood processing in Umweltkontor Bergkamen a prime example of innovative and sustainable industrial solutions.”
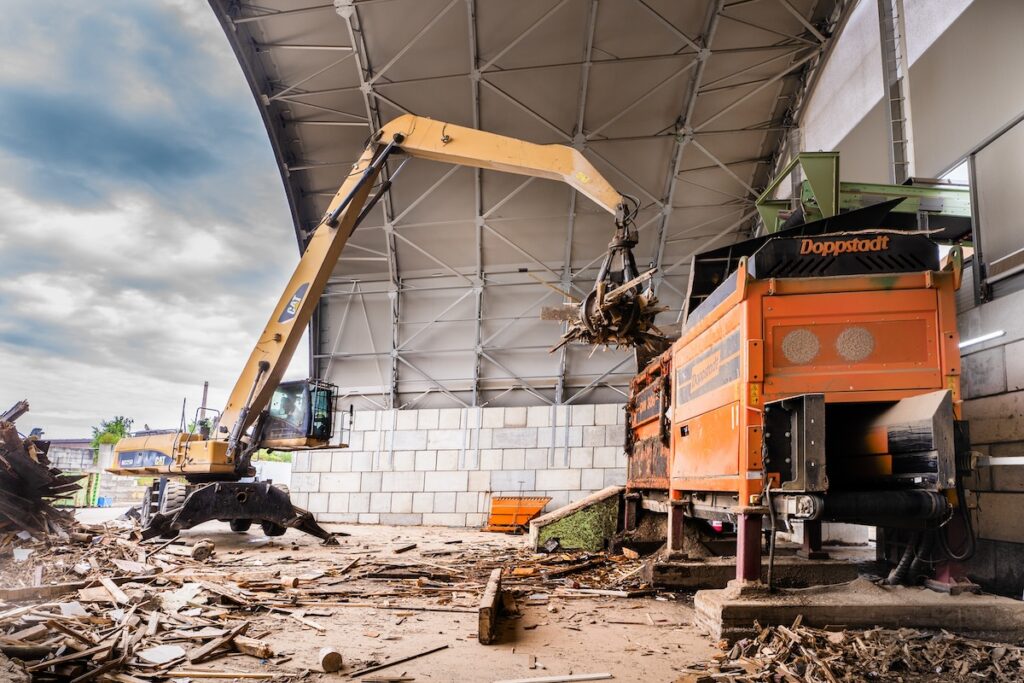
Three core machines for efficient processing
After intensive planning, it was clear that the most efficient and resource-saving solution for Umweltkontor Bergkamen was to replace their long-standing “Grizzly” shredder with three core machines: A slow-speed pre-shredder from Doppstadt, the DW306 CERON from 2012, out of the existing inventory of the Geiger Group, followed by a 2 m x 6 m vibrating screening machine with isolation-frame from SPALECK, and a high-speed secondary shredder, the AK540 VE, from ALLRECO. The subdivision of the shredding process into two stages and the integration of the screening machine allowed for very efficient operating methods of the process. The grain size distribution of the final product improved and now contains significantly less fines. Therefore, much less energy is consumed and less wear parts are needed. Shredding takes place to a maximum of 120 mm, which is screened from the material flow.
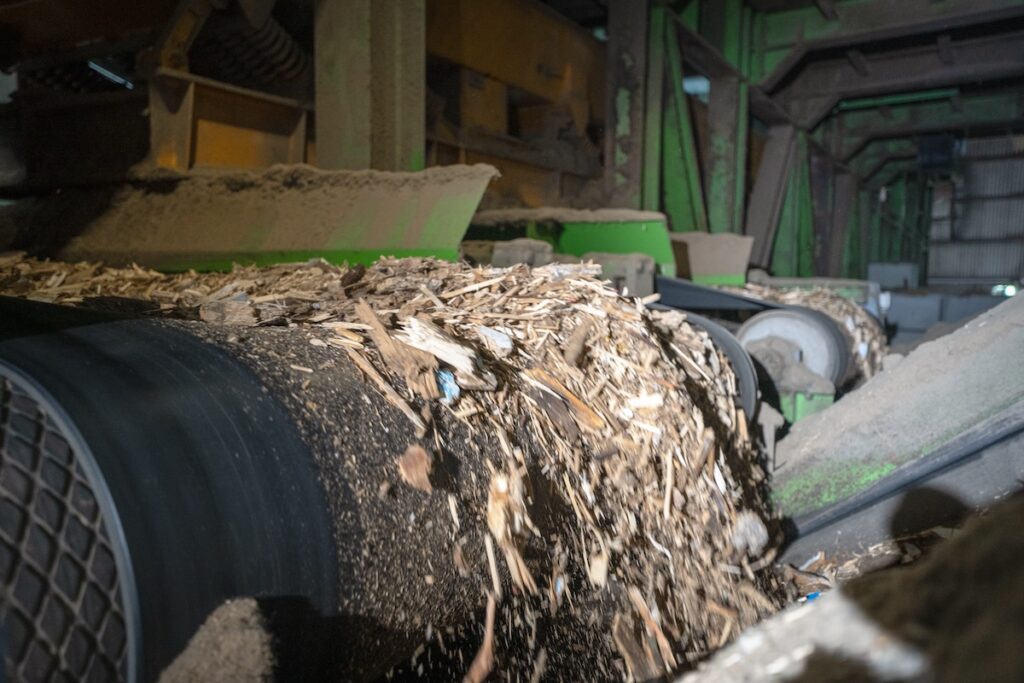
Improved material recycling and thermal recovery
The result is an output with less dust and very good grain size distribution close to target. Especially for material that is fed into thermal recovery, the production costs and effort required to produce the target grain fraction have now been significantly improved. The same applies to material recycling. The integration of the new high-speed ALLRECO AK540 VE secondary shredder ensures a particularly homogeneous material quality. The AK540 VE puts a completely different strain on the material, so that even small nails and screws can be separated by the subsequent separation technology. Henning Strunz summarizes: “In the end, we have replaced a large machine with a small factory but are much more flexible and can significantly reduce production costs.”
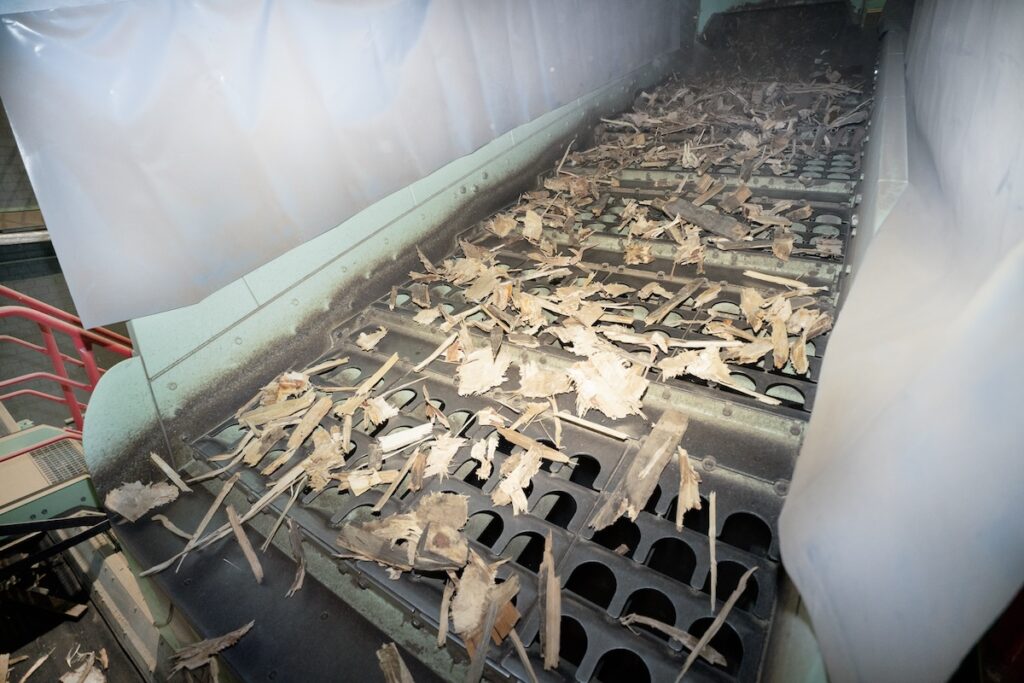
3D screening without long parts for optimal utilization
The screening quality of the power plant input material is one of the decisive factors for its efficiency, safety, and environmental compatibility. The material must be classified very precisely and accurately by size to ensure that the high dimensional requirements for the combustion process are met. Christian Lake, Sales Manager at the screening machine specialist SPALECK: “This is exactly where our SPALECK 3D screening technology comes in. In contrast to traditional and conventional screening, our special 3D screening panels enable screening in 3 dimensions. This means that the material from the pre-shredder can be screened very precisely in 3 dimensions. The advantage for the operator is that the long parts which are unwanted for thermal utilization are safely removed and the power plant thus receives exactly the required material grain size. To ensure the optimal set-up of our machine, we carried out extensive material analyses and screening tests in our test center during the project phase. This enabled us to configure a machine that was tailored to Umweltkontor Bergkamen in every detail and that generates an ideal material from the moment it is put into operation.”
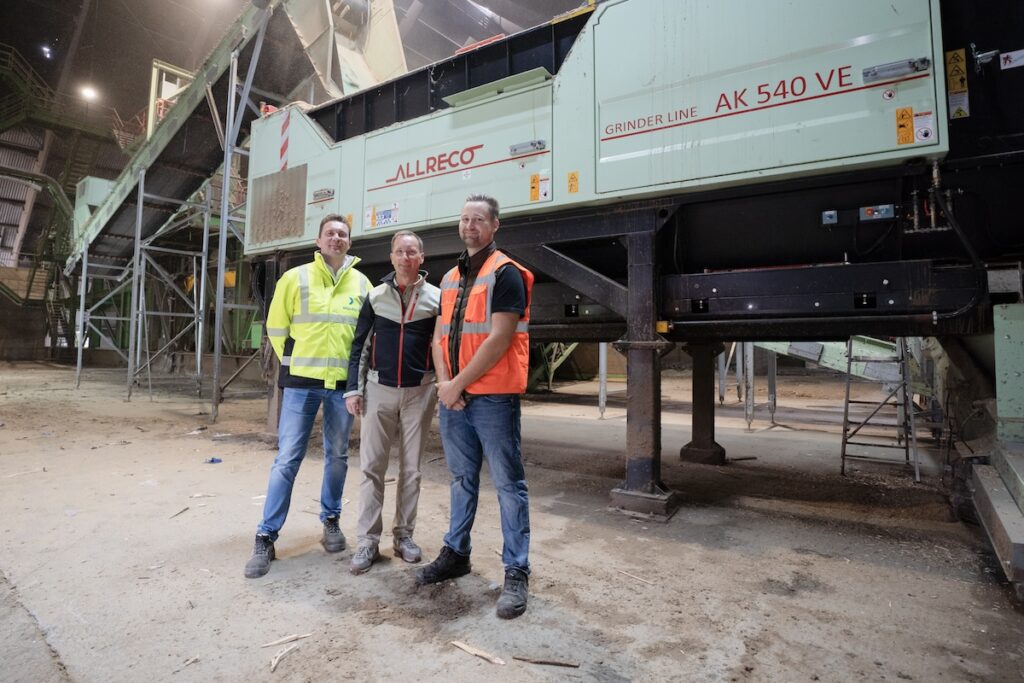
Integration into the existing plant
Another challenge was to integrate the new machines swift and safely into the existing plant structure without affecting the existing process. In teamwork with the technicians on site and after a joint analysis, it was clear: a SPALECK vibrating screen with an Isolation-frame offers the best and most stable solution. The vibrating screen, which is also available with SPALECK´s SmartSUSPENSION air suspension systems, enables the machine to start and stop optimally with minimal impact on the steel structure and the machine environment. After the customer dismantled the old shredder, ALLRECO installed the new components in November 2023. Christian Lake from SPALECK: “Thanks to ALLRECO’s experience in rethinking, replanning, and retrofitting into existing processes, we managed to find the perfect solution for Umweltkontor Bergkamen with minimal changes to the existing steel structure.”
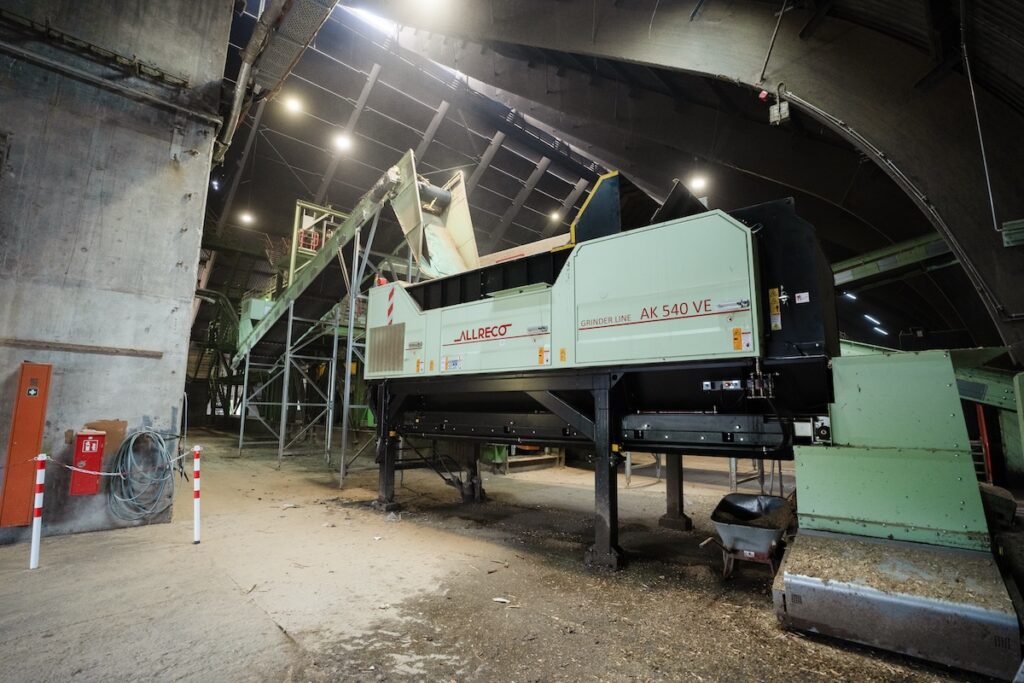
The best result for everyone
The modernization in Bergkamen is an example of the future of waste wood processing, which is characterized by advanced technology, sustainable processes and efficient production methods. Olav Meyer, Managing Director of Umweltkontor Bergkamen, concluded: We are now much more flexible and profitable. The new, more efficient shredding and improved material distribution not only leads to an optimized output with a lower proportion of fine grain, but also to reduced energy consumption. In other words, a significant reduction in our operating costs. Thanks to the expertise of ALLRECO and SPALECK and their close cooperation, we have managed a project that sets new standards in terms of efficiency and sustainability in waste wood processing.”
ALLRECO GmbH
ALLRECO, with a long Doppstadt history, has been a direct holding of LIG since 2021. Our core business is machines and plants for the processing of waste wood, domestic and commercial waste, biomass, and the production of substitute fuels.
SPALECK GmbH & Co. KG
SPALECK is one of the leading international manufacturers of conveying and separation technology. Founded in 1869, the company today specialises in manufacturing screening machines for the recycling industry and is a trendsetter for innovative, sustainable recycling processes. The SPALECK Group employs around 500 people worldwide.
Umweltkontor Bergkamen GmbH
Umweltkontor Bergkamen is a specialist in waste wood disposal and processing. The company site covers an area of 125,000 m². The capacity of the sorting and processing plant is several hundred thousand tons per year. With the Geiger Group and the Green Angels as shareholders, the company is a certified waste disposal company and a competent partner for all matters relating to waste wood.