Aerosol Recycling
All
Aerosol Recycling
Aluminum Recycling
Battery Recycling
Construction and Demolition Waste Recycling
E-Waste Recycling
End-of-Life Vehicles (ELV) Recycling
Fats & Waste Cooking Oil Recycling
Food Waste Recycling
Glass Recycling
Metals Recycling
Municipal Solid Waste (MSW) Processing
Paper Recycling
Plastic Recycling
Recycle Cardboard
Rubber Recycling
Textile recycling
Tire Recycling
Wood Recycling
The aerosol industry produces over 16 billion cans annually, yet less than 10% are recycled, missing a critical opportunity to...
Read more
For the past decade, DESPRAY Environmental has led the way in making aerosol recycling safer, more efficient, and fully sustainable. Since the founding...
Read more
Despray proudly announces their most recent collaboration with GDB International. GDB International has acquired a Despray "DS500" state-of-the-art aerosol recycling...
Read more
Despray Environmental, the world leader in aerosol recycling technology, proudly announces a monumental achievement. The combined efforts of DeSpray cofounders...
Read more
Aerosol cans pose a unique hazard during disposal due to their pressurized contents and residual chemicals. Historically, improper handling led to workplace explosions and environmental contamination. Today, engineering advancements offer robust solutions for safely managing these materials.
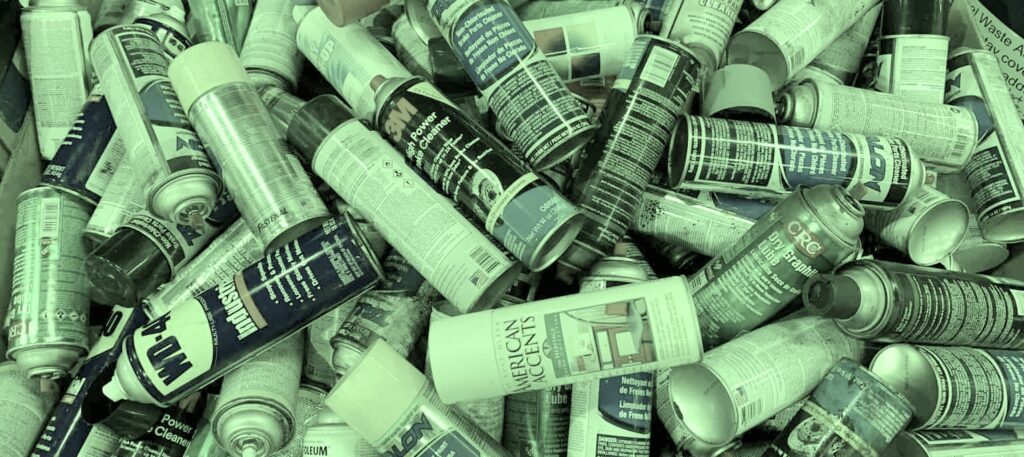