Recycling yards already see a growing e-motor presence in their scrap. Many of them collect these and then sell them to smaller specialized e-motor recycling plants.
These guys are doing a great job and they see their businesses growing. One of these yards is located in the Northern part of the Netherlands. Here, they have designed their own processing line to be able to separate the different parts of the e-motors. At the end their sorting line they still find some mixed materials such as the non-ferrous mix of copper and aluminium. To solve the sortation of this material stream, they were looking at different options and finally chose to use a dry sorting process. Consequently, they decided to look for a suitable and affordable sorting device that would be able to separate the copper from the aluminium parts. Several size ranges had to be sorted; such as the fine cut 1-4mm or the small cut 4-8mm mix. Now that fines sorting is one of our specialities. And here is the solution to the sorting task:
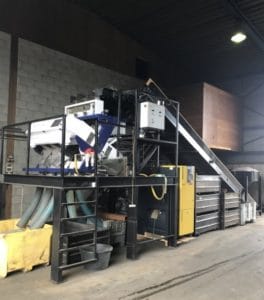
The Sense2Sort optical colour sorter QSS900 was chosen to do the job. This channel sorter is equipped with 6 high resolution CCD-cameras. The material is scanned very accurately using the dual scan mode with one camera at the back and one in the front of the material stream. This way, no part will be missed. We are using a resolution of 5400 pixel which is that high that even smallest colour nuances can be distinguished on a 1 mm material piece. In the so-called detecting area of the machine, at the point where the line scan camera detects the material, a fast industrial computer processes the incoming information of all cameras. Within microseconds, the electronics are able to decide which particle is accepted and which particle has to be ejected.
In the user interface of the machine a program can be chosen that fits the infeed material. The program settings are used to sort the right parts out. Fast solenoid valves located just shortly underneath the detection area can open and close within milliseconds and by means of a short but strong air pressure the unwanted material is pushed into the outlet of the eject stream. The short cycling time of the valves helps to reduce over sorting and loss of good product. The key to successful sorting is the way the machine is designed by the people behind, how the machine is installed at the customer’s site, the preparation of the incoming material and never the less how the service engineer did his work that makes an installation good working and profitable.
At the end we realize a sorting quality of 98-99% on the accept stream. The input material composition varies since the shredded material comes from different stock piles with different kind of material. Same accounts for the size range of the material. Thus, it can happen that we have a 50/50 combination of Cu/Al or even a 40/60 mixture. Depending on the input material and the quantity of unwanted material or impurities in the input we run these material streams in one or two steps. At the end we always achieve a very good product with high purities on both sides, the accept as well as the eject stream.
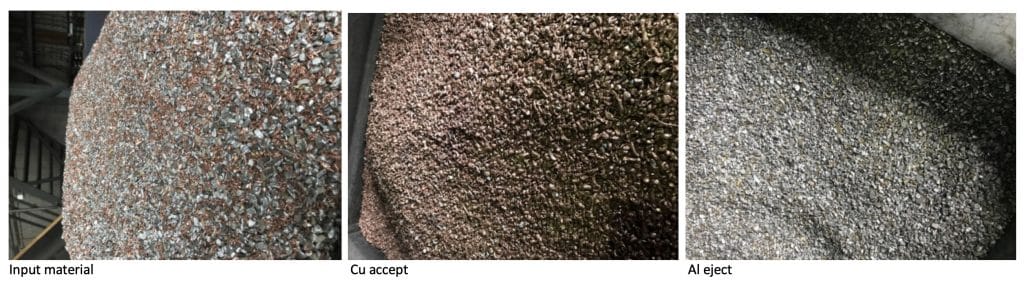
Besides this example you can imagine that this optical sorting machine is able to sort all kinds of fine bulk material. Any kind of pourable material can be processed on our QSS-series. This model is available in multiple combinations and various widths, up to 10 channels in one machine. Each channel has a working width of 300mm.
The material shown in this report we run at 3 t/h. On a 900mm wide machine. The material density in average is around 4 t/m3.
Other possible input material can be granules of any other material like glass, plastic or minerals.
For more information contact Eric van Looy at evanlooy@sense2sort.com or call us at +4915733144059.