Palm decided to commission Entsorgungstechnik BAVARIA GmbH near Munich for the planning and the construction of the sorting plant. The Munich-based company is considered to be the specialist for plant construction in this field for many years.
The sorting plant is designed to process around 200,000 t of waste paper collected from households per year.
The aim of the plant is, in addition to a constantly high end quality, an optimal efficiency and a fully automatic sorting operation.
To achieve the highest possible degree of automation and optimum plant efficiency, the sorting plant has been equipped with the MAX POS control concept for process optimization from Entsorgungstechnik Bavaria GmbH.
The control technology continuously accesses online information about the material composition, e.g. from the near infrared machines.
In addition, material data, such as the degree of moisture, are analyzed directly in the input area and evaluated online. The material flow is thus constantly monitored and controlled in real time.
In order to define the optimum plant configuration for an efficient sorting plant, targeted at the input material, the Palm paper mill, headquartered in Aalen, Germany, in cooperation with Entsorgungstechnik BAVARIA GmbH, carried out tests with English waste paper on several paper sorting plants in advance.
It was a particular challenge to achieve a constantly good final quality despite strongly fluctuating and challenging input quality.
The plant has been equipped with the latest sorting technology including a BAVARIA dosing bunker at the beginning of the processing line. This guarantees a continuous and well separated material output for the further sorting process. The more evenly the material flow is distributed to the conveyor belts, the better the sorting result on the subsequent sorting units.
The sorting system is equipped with the proven BHSt cardboard and fine screens for automatic sorting of cardboard and small impurities. Due to the compact installation dimensions and the high throughput rates, these screening machines are also suitable for narrow installation conditions. Thanks to their long running times and their reliability, the screening units with their rubber – triangular – screening discs are highly efficient and cause only low wear costs even in multi-shift operation. The screening quality can be individually adjusted by simply adjusting the speed.
In order to reliably sort medium-size cardboard boxes from the waste paper fraction, one PaperSpike was used per line. The advantage of this mechanical separation stage is that light, white and printed cardboard and packaging can also be reliably detected due to their rigidity.
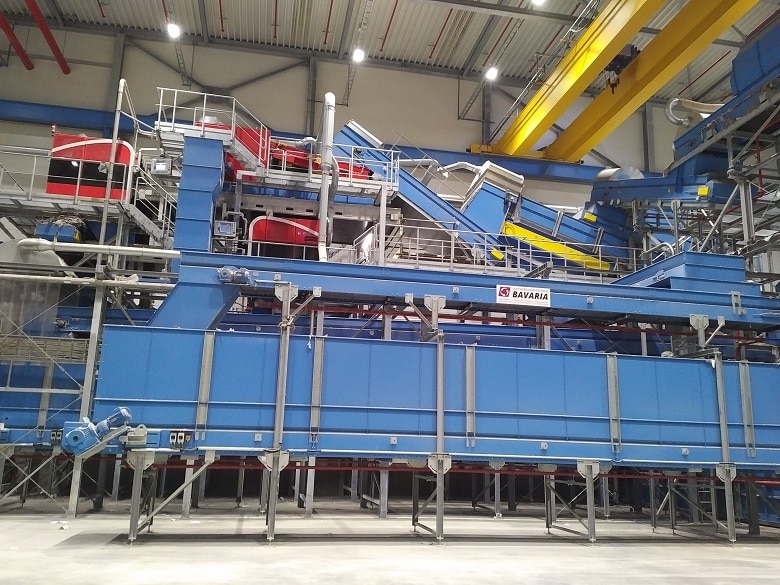
The latest generation of these machines of the Redwave series „2i“ ensures high deinking quality. Using the combined visual and near infrared detection system, grey, brown and printed cardboard as well as non-paper materials can be detected and removed automatically from the deinking stream by using compressed air.
Due to the new sensor technology, the new generation of these machines offers more accurate and faster material recognition.
The plant is equipped with an ultra-modern dedusting system to prevent possible dust accumulation. Extraction points are provided at all hot spots.
The transport air of the dedusting plant is cleaned in a clean air filter and returned to the sorting-halls with a cleanliness of 99. 8%. This dust reduction measure serves not only to increase the quality of work but also to prevent fire risks.
The biggest advantage of the sorting plant is that it does not require the usual manual sorting.
In order to achieve this, BAVARIA has developed the MAX POS process optimization system together with the „Papiertechnischen Stiftung PTS“ (Paper Technology Foundation).
This means that the quality is monitored and optimized during the entire sorting process by real-time monitoring.
The online monitoring collects real-time information about material data, sorting parameters and the current quality status. The automatic information about changes in material composition and belt allocation provides Palm with an early warning system and allows immediate regulatory intervention in the sorting process.
Reliable data on material, plant, processes and influencing factors as well as the recording of statistics and trends support the operator in the operational process and offer greater reliability in the long term.
This leads to a sustainable increase in efficiency and highest quality of process outcome.
Additional operational safety is provided by online monitoring of the aggregate states, such as bearing temperature monitoring.
In addition to the positive effect of preventive maintenance, this increases fire protection precautions. Especially against the background of the strongly fluctuating input qualities and the objective of improving the quality of the raw material recovered paper, this plant offers Palm Paper excellent opportunities for sustainable recycling.