We travel week in and week out visiting MRF operations all over the U.S. and Canada. We see first-hand the challenges that these sites face: highly-contaminated inbound material streams, inbound stream changes (such as: light-weighting, Amazon effect, reduction of ONP, increase of film and trash), high maintenance costs, increasing end product quality demands, maintaining a safe working environment, sorter labor issues, finding willing candidates to show up every day and dedicate themselves to sorting through trash, etc. etc. Today’s MRF is feeling the brunt of the squeeze!
Some common questions we often hear are:
- Can I just drop in an optical sorter to make a ‘China spec’ grade?
- My temp labor service could only supply me 14 sorters today, but I need 22 to run at capacity – and it’s worse on 2nd shift…What should I do – drop in robots?
- Can my system change its settings (conveyor speeds and screen angles) based on the inbound stream that I am receiving?
Whatever the technology that you are considering – and there are some really cool things out there (robots, optical sorters, material monitoring cameras) – the material needs to be properly prepared FIRST for it to be properly recognized and sorted (or even monitored). Any separation device – a screen, an optical sorter, a robot – likes to be fed a steady diet of consistent material all on a single layer of the conveyor that is feeding the material to the technology. If possible, consistent by size with fines removed, similar by shape, rigidity, and density.
Here are 5 ways to help prepare material before ‘dropping an optical sorter or robot’ into your next retrofit:
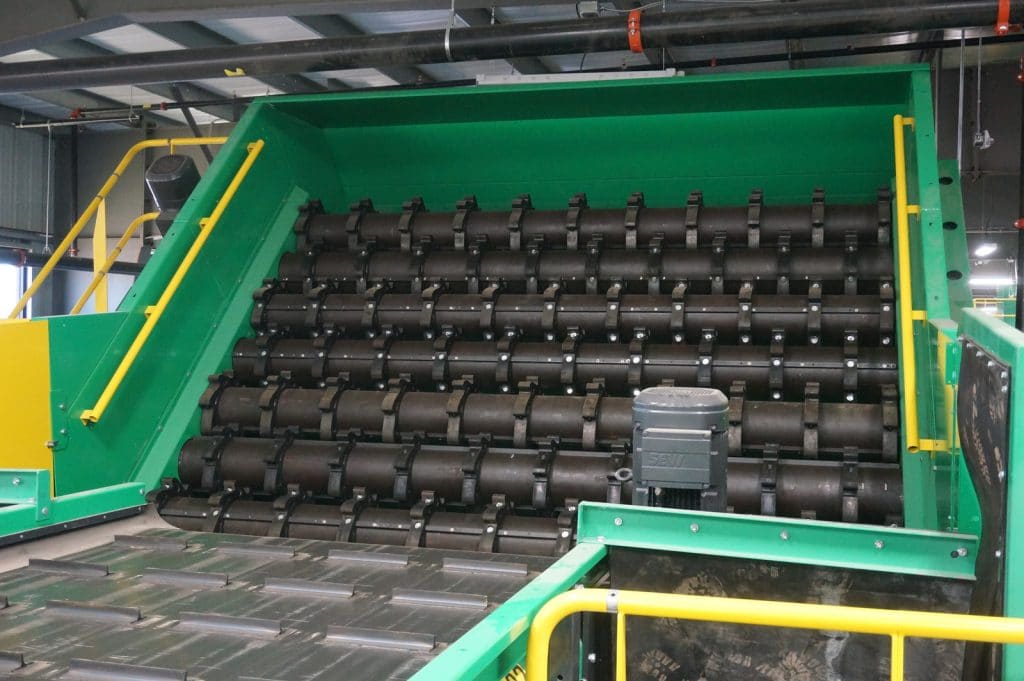
SCREEN FOR SIZE without getting wrapped up
Mechanical screens are still an important piece of the puzzle at a MRF to help screen and separate material into different fraction sizes. They size the material into different size fractions for further sorting or intelligent separation. Large fractions and fines can be removed and a target size can be directed to an intelligent separation device (like an optical sorter or robot). In the last few years screens have been greatly improved. Van Dyk and many other suppliers now offer ‘non-wrapping’ screens that properly size material without allowing film bags to be wrapped around their shafts.
SEPARATE 2D FROM 3D: ballistic or elliptical separators
An elliptical or ballistic separator (not unlike the elliptical trainer that you might see at your local gym) performs highly accurate separation of 2D and 3D materials. Paddles “walk” 2-dimensional objects over the screen (items like film bags, and light sheet paper). Items with rigidity (bottles, cans, 3D cardboard) bounce backward.
Also, the paddles have true 2-inch holes in them to allow the last bit of glass fines to fall through those holes. With minimal maintenance and no star changing required, the elliptical separator has clearly overtaken the final clean up task from a commingled or polishing screen at a MRF. With its ability to remove light sheet paper and film and remove fines, it is becoming a ‘must have’ to properly prepare your container line for further processing (whether that’s optical sorters, robots, or even humans).
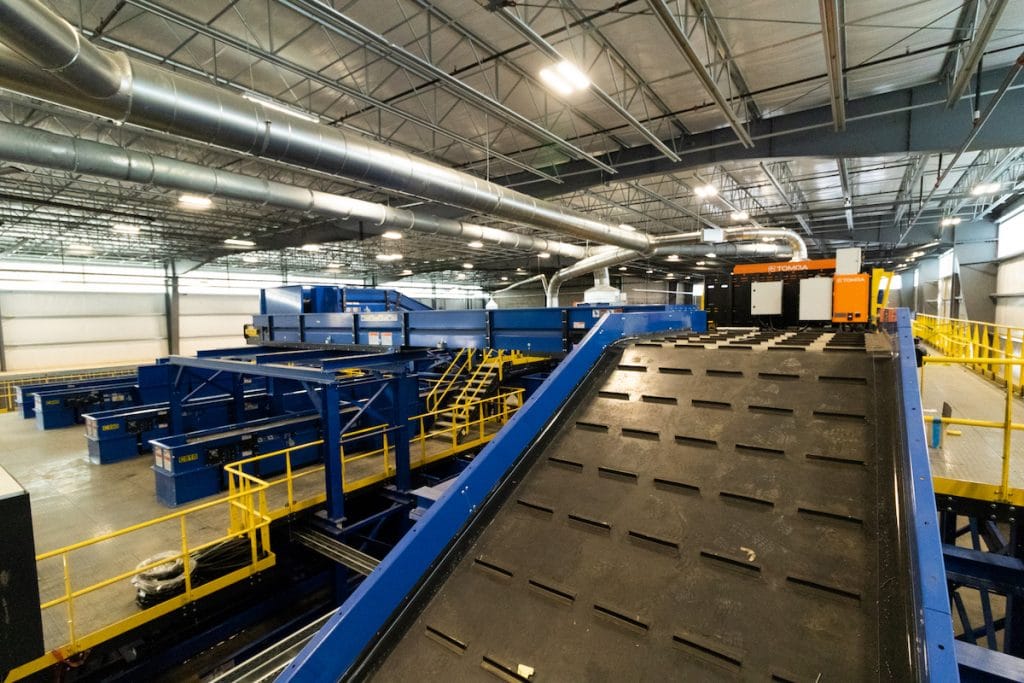
CONVEYOR BELTS: how they play a part
Conveyor belts and sequencing play a large role in the success of any intelligent separation device. Why? The goal is to get the material to a single layer to give the separation device a chance to succeed.
Here are some tactics to thin out material:
- Placing two conveyors in succession and setting them at different speeds
- Whenever possible, feed subsequent conveyors in line instead of at 90-degree angles
- Use wider transfer conveyors directly prior to the intelligent separation device
- Use proper cleats on inclining conveyors that help space material and not clump it together
- Have all conveyors on variable speed drives to give maximum flexibility to properly sequence the conveyors
These are all small details, but they all play a part in properly preparing the material for intelligent separation.
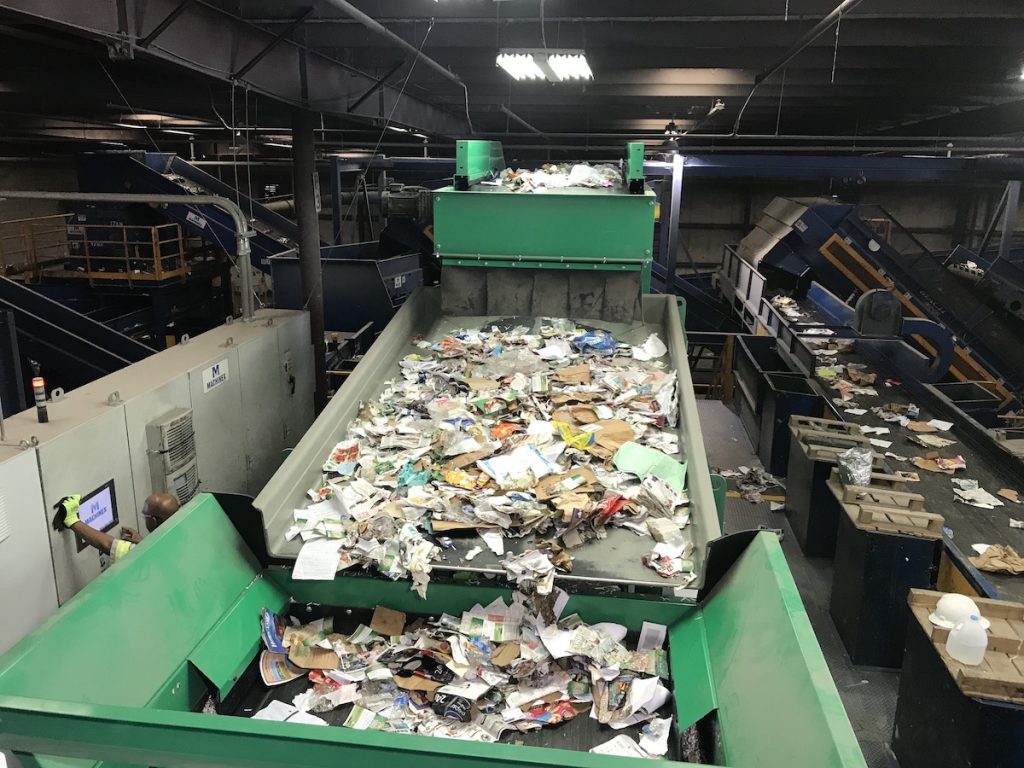
SHAKE THINGS UP: vibratory feeders and disc spreaders
If the system has the extra height needed, a vibratory feeder or a disc spreader could be the perfect tool to help spread the material across a wide belt for single layer coverage to an intelligent separation device. If a customer is buying an 8-ft wide optical sorter, but the incline conveyor that is feeding the 8ft wide acceleration conveyor is only 4ft wide – this could be a problem. The material will not get spread across those 8 feet and only 50% of the optical will be utilized.The vibratory feeder or the disc spreader helps spread the material as it drops on the full width of the optical sorter’s acceleration conveyor.
KEEP THINGS STILL: wind tunnels eliminate floating and drifting
Whatever it’s named (ours is DeftAir), the addition of a wind tunnel to an optical sorter’s acceleration conveyor is a good way to help process light materials at a higher throughput. Typically, light sheet paper and film starts to fly up and drift when a conveyor speed approaches 550-600 feet per minute. A wind tunnel added to an acceleration conveyor applies air flow at the same speed as the conveyor to stabilize the light floating materials and allow the acceleration conveyor to operate at higher rates of speed (upwards of 800-1000 feet per minute). This allows more throughput to pass under an optical sorter and still be at a recognizable single layer. Recovery rates will rise while accuracy is maintained or even improved.
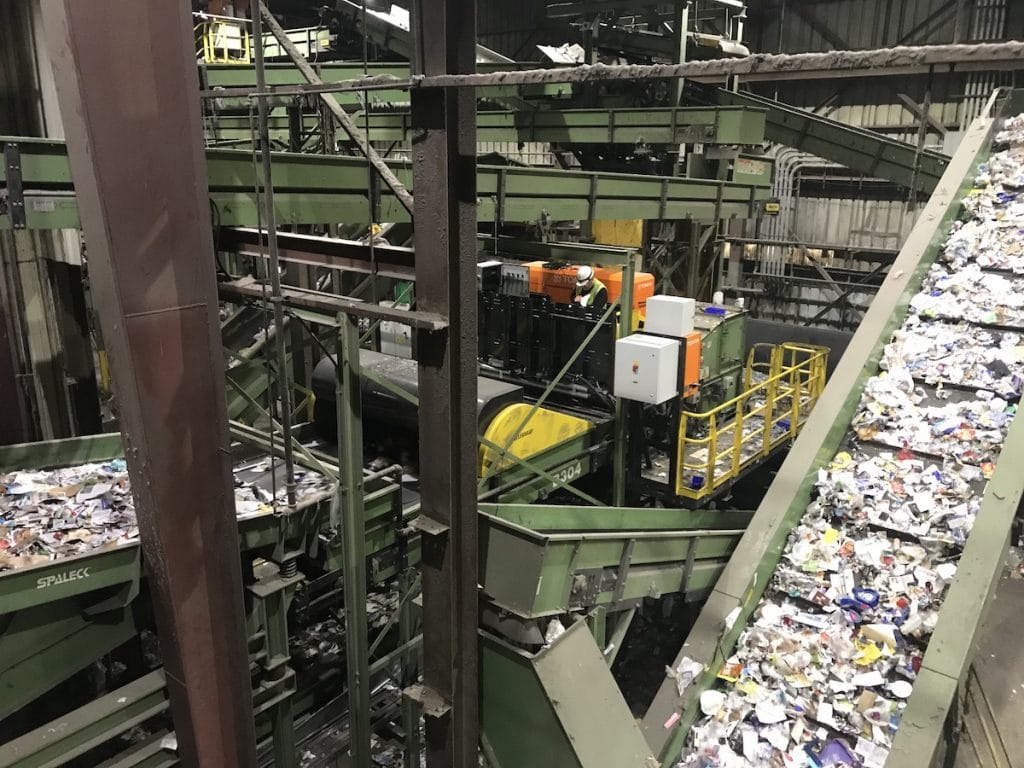
WHY VAN DYK?
We know how challenging it is to run your operation. You’re under constant pressure to meet goals in the face of changing end markets. You’re considering a retrofit, but don’t know if a particular upgrade will actually get you the results you need.
When you hear talk about the latest robot or optical sorter, remember that an intelligent sorter is only as good as its material feed. It is all about the way it’s fed. You may be in the market for a new sorter, but also consider the possibility that you may not be getting the most out of the equipment that you already have.
If you think your optical sorter or robot is not reaching its full sorting potential, give us a call today. We are working on solutions for our customers, and operations like yours, every day. With our help, you can streamline your system, overcome your challenges, and turn them into
profit-making opportunities.
Don’t forget, we have a material test center at our headquarter campus that is outfitted with the equipment and principles described in this document. Bring a sample of your plant’s material and test drive our machines before making a commitment. Call to schedule your test today.
We have engineers located in and dedicated to the following regions:
Northeast Midwest
Mid-Atlantic Pacific Northwest
Southeast Pacific Southwest
Southwest Canada
Call us today to reach your local engineer and set up a consultation.
203-967-1100 Or email us! info@vdrs.com