This provides protection for plastic injection moulding machines. The combi-separator can also be used to separate copper fractions from cable shredders, resulting in a higher yield per kilo, and for processing mixed metals, in which non-ferrous metals and pieces of weakly magnetic stainless steel are separated from each other. This simplifies subsequent separation steps, so the machine quickly pays for itself.
How it works
In the first step, the magnetic separator separates the easy, large pieces of ferrous metals from the product flow using an
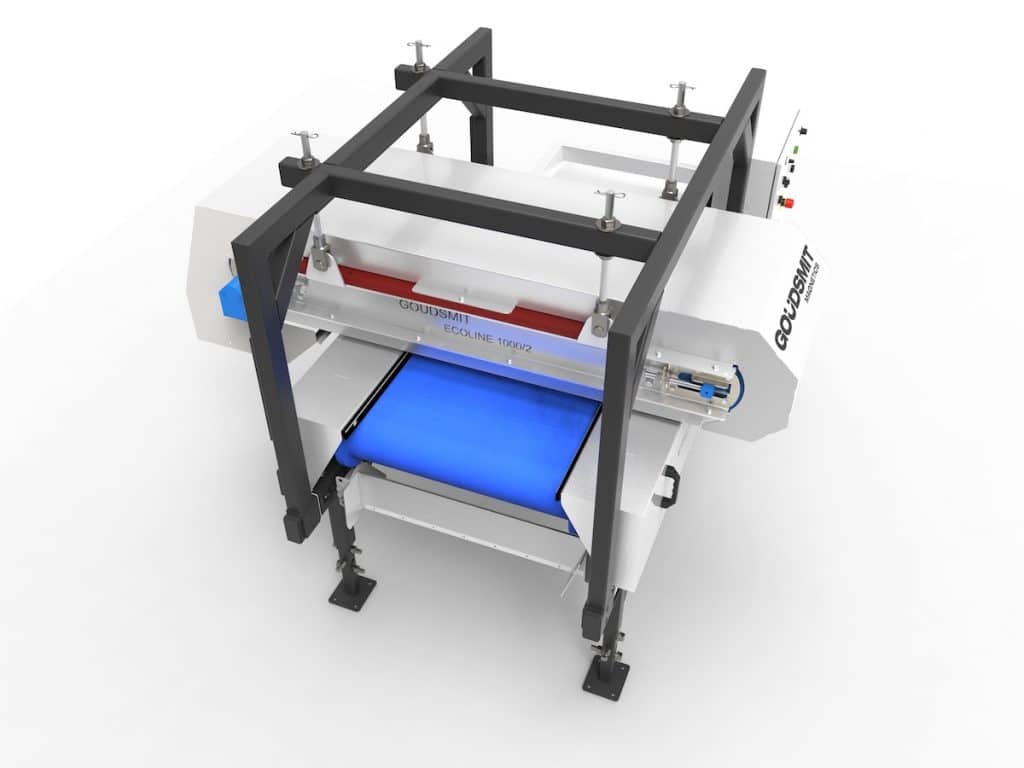
Return on investment (ROI)
In addition to upgrading copper fractions, which increases the value per kilo, the high-gradient separator protects plastic injection moulding machines. In plastic recycling, stainless steel balls and springs are separated to create secondary plastics. If metals remain in the plastic, you lose more material at the metal detectors, the filters of injection moulding machines become clogged more quickly and there is a high risk of wear damage to the augers of the injection moulding machines. For mixed metals, the magnet separates the non-ferrous metals from the weakly magnetic stainless steel. This simplifies subsequent separation steps, so the machine quickly pays for itself.