The Metallco Group is the Norwegian market leader in recycling non-ferrous metals and steel scrap. Metallco has several production facilities, including shredders, a sorting plant and its own aluminium smelter, producing the highest grade secondary aluminium. In the interview, Feinberg highlights the trend towards shorter lifespans for consumer goods, which in turn means more waste for recycling. In addition, government regulations demand that recycled materials be used in manufacturing new products, leading to an increased demand for Metallco products.
Reliability is key
When searching for technology partners, Feinberg examined various systems, and was impressed by the STEINERT portfolio: “We evaluated four different suppliers and, in the end, we found STEINERT to be the one which was competitive in price and superior in experienced quality. That’s why we chose STEINERT, which so far has proved to be a good choice.”
Feinberg emphasizes the reliability of the machines. “These machines don’t need a lot of maintenance and servicing. This means they’re very reliable and they simply work and work and work for us, which is very good for our company.”
As a fan of classic cars, Feinberg knows the value of quality: “I’m a collector of classic cars, mainly from the 1960s. When I find the right object, I have to pay the price that it costs. I see a parallel to STEINERT here. It gives me a great feeling when I can see the machines are working as they should. You buy the best you can buy for the money that you’re willing to spend.”
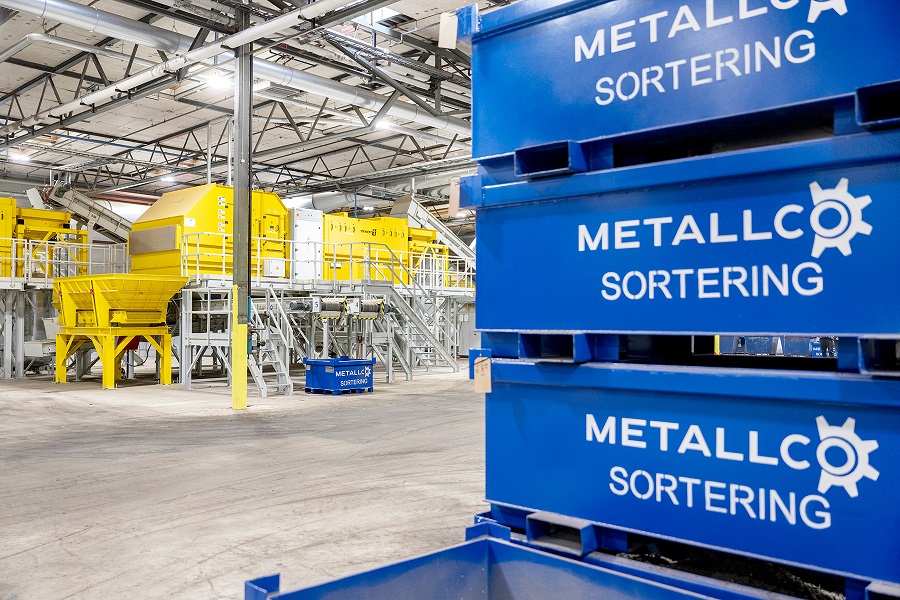
Quality begins with sorting
The first step of metal recovery at Metallco is shredding the scrap that is delivered. “Then, the metal fraction goes into the sorting plant that we just purchased from STEINERT. Here, we sort into heavy and aluminium fractions. Today, we separate cast from wrought aluminium. Soon, with the LIBS machine, we will also be able to separate alloys. This makes it the ultimate solution.”
Along with screening and conveyor technology, the Metallco machine fleet includes magnetic and eddy current separators as well as sensor-based sorting systems. With X-ray transmission, X-ray fluorescence and optical detection systems, the sorting systems utilize a broad range of state-of-the-art sensor-driven detection technologies. Two STEINERT XSS T EVO 5.0 X-ray transmission sorting systems connected in series ensure a high level of purity. CEO Øyvind Frebrich expands on this: “We have installed a STEINERT XSS T downstream of the eddy current separator to separate the aluminium from the heavy metals. We use the second machine, also a STEINERT XSS T, to separate the aluminium into cast and wrought aluminium. We achieve a purity of more than 99% here.” This level of quality is highly sought after and yields a lucrative market price.
Feinberg is also very happy about the quality of the sorting and is looking forward to raising the level even higher in the future with a LIBS system from STEINERT. LIBS is short for Laser Induced Breakdown Spectroscopy and enables the elements in the alloys to be identified and quantified precisely. The latest machine that we have ordered is a LIBS machine, a laser technology that will enable us to sort aluminium alloys from series 1 to 8000.”
Fit for the market
According to Feinberg, Metallco operates in a market that is subject to profound changes. “The life span of consumer products is much shorter, which is resulting in more and more waste. This means that many more people are bringing their waste to our yards for recycling. On top of that, laws and regulations stipulate that the industry needs to dismantle and sort everything which is going out of use. So, if you are tearing down a building, the iron has to be separated from the concrete. Volumes have increased a lot in recent years, as has the demand for recycled products. In addition, government regulations demand that ever more products be produced from recycled materials. It is a win-win situation for our business, I would say.”
In the past, metal mixtures were often sent to China and other emerging markets. There, the mixture is sorted into the separate metal fractions by hand. Stricter import regulations and rising wages are changing the equation and prompting companies such as Metallco to build their own sorting infrastructure: “We think that it will continue to be difficult to export in the future, so we are looking into what opportunities the market still has for us.”
A shared success story
By making smart investments and decisions, the Metallco Group has been able to grow steadily over the decades and is now the market leader for metal recycling in Norway. “There are between 35 and 40 companies in the group and I have been working here for almost 35 years. This has been a long journey. When I started here, there were around 17 or 18 of us. We had only one location that we rented. Today, we have 250 employees working at 25 sites, all of which we own,” Laurie Feinberg says proudly.
Metallco can produce precisely to the level of quality that recycling material customers demand. Øyvind Frebrich sums up just how important a reliable technology partner is for the strategic development of a company. “With open communications, we have overcome sorting challenges and are now producing better quality aluminium. It is important for me to say that the technology from STEINERT is one reason why we are where we are today.”