Many plastics processing operations are facing the question of how to implement recycling on an industrial scale at the highest quality. At this point, new hopes such as biodegradable plastics cannot meet the high expectations placed upon them. The plastic products will only degrade under very specific conditions. Educating consumers on proper disposal is proceeding sluggishly, and the waste industry is struggling to properly exploit this new material stream, especially when it comes to packaging, conventional plastics such as PET, PE, or PVC will remain without competition for the foreseeable future. In order to consistently reduce effects upon the environment caused by the use of plastics, the plastics industry has no choice but to become circular.
In order to increase the percentage of secondary raw material for processing as much as possible, it is preferable from the perspective of the recycling company that waste plastic be as easy to process as new material.
For any of these recycling systems, mechanical equipment design must adapt to meet the changing requirements to handle light (low bulk density) and heavy (high bulk density) materials to ensure proper feeding. This article will address the evolution of recycling and what a processor should consider when evaluating his current feeding equipment and the feeder’s ability to monitor, trend, and react to process variations. The availability of this data and its management in accordance with Industry 4.0 automation can allow the end-user to adapt to future manufacturing requirements which can include greater traceability, flexibility, adaptability, and overall effectiveness.
Time to Make a Difference
Throughout the world, most consumers don’t realize that a majority of their recycled content is sorted locally and in many cases, bundled and shipped to other parts of the world for processing. Most of the plastic content is compressed, bundled, and shipped to other countries for reprocessing primarily due to the cost to reprocess locally or local environmental restrictions that made it impractical to do so.
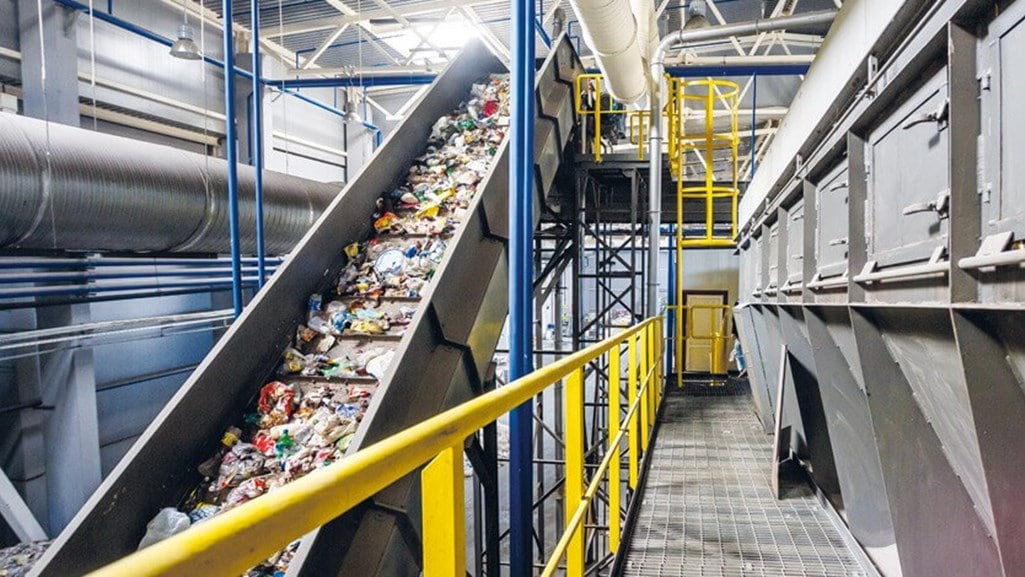
The consumer’s voice has been heard by global government officials and the industry is listening. The plastics industry has recognized that it has to step up and produce more sustainably if it is to meet the needs of end-users’ changing consumption behavior and ever stricter environmental legislation worldwide. Recycling needs to evolve to play a key role in achieving this goal. Many plastics processing operations are facing the question of how to implement recycling on an industrial scale while maintaining the highest quality of end product.
Coperion and Coperion K-Tron are longtime technology solution providers for various recycling applications, e.g. mechanical and chemical recycling, PET recycling, or upcycling. Peter von Hoffmann, General Manager of Business Unit Engineering Plastics & Special Applications at Coperion, is convinced: “Sustainability is becoming more and more important, and the topic of the circular economy is moving further into the foreground for companies. We’re proud that, with our years of process know-how and our visionary technological solutions, we can contribute to a promising, forward-looking, and sustainable plastics recycling approach. Our extruders, feeders, material handling solutions as well as our complete systems capabilities support the plastics industry’s path to a circular economy.”
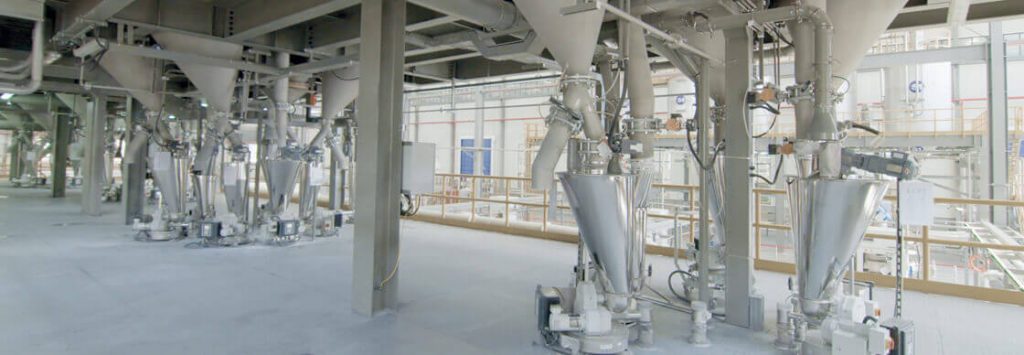
Evolution of Recycling – Challenges of feeding materials into the process
One notable difference between primary and secondary materials is especially important during feeding. Like practically any recycling material, waste plastics are heterogeneous in size, form, and bulk density. Therefore, the correct choice of feeding technology is very important in ensuring optimal bulk material flow.
The most appropriate feeding technology for the application in question needs to be both technically suitable and at the same time economically efficient in terms of investment and operation. It is helpful to rely on providers like Coperion K-Tron who have mastered various technologies and can thus offer the right feeding system for any case. Some vendors offer, for example, weigh belt, vibratory, and screw feeders, in addition to others. Each technology has its own advantages – what is decisive is the process know-how that brings operational requirements and processes together.
Single screw extruders, ubiquitous in plastics recycling, are operated primarily using volumetric feeders, which are only suited for feeding bulk materials with consistent density. When handling secondary raw materials, the bulk material characteristics described above can quickly lead to irregularities in flow behavior.
In contrast, twin-screw extruders are usually operated with gravimetric feeders, which operate far more precisely and, thanks to the weight signal, can react better to fluctuations in bulk density and material flow. Moreover, their feeding performance is precisely documented.
Improved Robustness – Options for Handling Difficult to Flow Materials
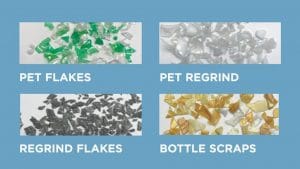
Prior to picking the proper feeder, it is important to ensure that the material will be able to make it through the hopper to the feeding device. Due to variations in material sizes, bridging (arching) or rat-holing may occur. Strands of recyclates that mesh together tend to form a bridge above the screw extraction device that can result in the feeder starving for material. The end result could be catastrophic to the integrity of the product recipe and result in off-spec product being generated. To combat this problem, vendors resort to external agitation.
Coperion K-Tron Solution: Using Vibration for Poor Flowing Materials
In the case of loss-in-weight (LIW) feeders, external vibration including the use of standard vibrators on feeder hoppers can cause interference with the LIW signal if the control system cannot filter out this vibration. Alternatively, there are some new control technologies available that utilize vibration applied to the hopper (such as the Coperion K-Tron ActiFlow™ bulk solid activator) that include an external drive tied directly into the weight system controls. This drive operates at a variable frequency and amplitude-based upon the weighing and control system detecting non-uniform material flow by weight. This real-time device activates the external vibration when there is an upset in the LIW signal, such as in the case of rat holes or material bridges. This type of “smart” vibration device is also self-tuning, with the controller adjusting the frequency and amplitude to compensate for changes in the hopper fill level or material flow, thus preventing bridges or rat holes before they can form.
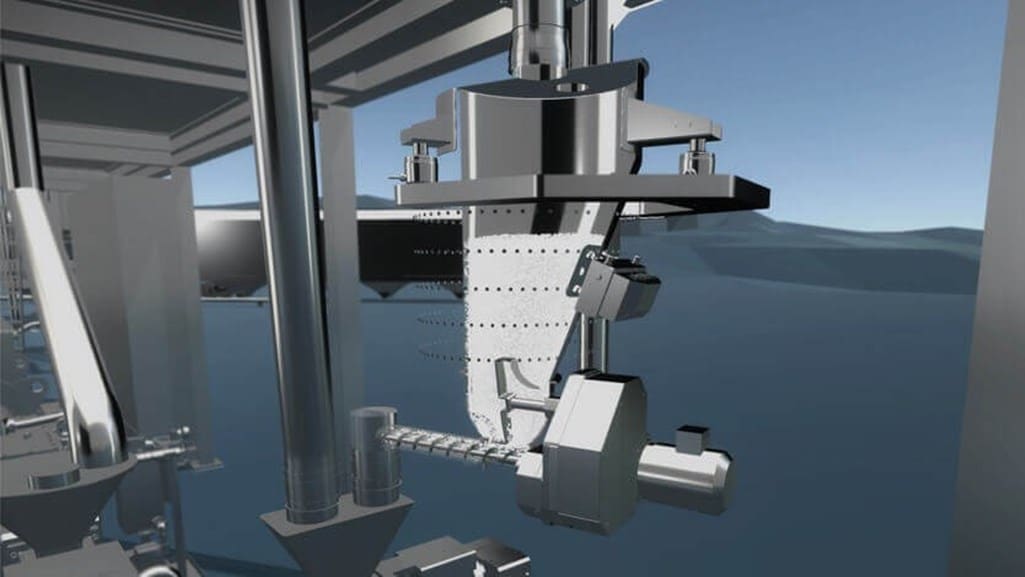
Feeding Technology
As comparatively simply constructed components, weigh belt feeders are reliable, gravimetric feeders that offer high precision and efficient process control. They can reliably feed large volumes of bulk material and materials with varying flow properties since they weigh the bulk material prior to discharge and actively adapt belt speed. Weigh belt feeders are suited, for example, for processing recyclates with fluctuating bulk density.
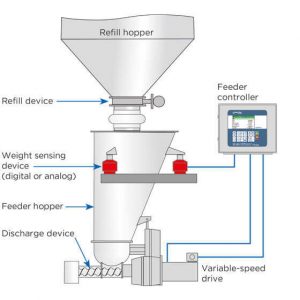
In many applications the weigh belt feeder is combined with a screw feeder as a pre-feeding system in order to smooth out the mass flow or to reliably transport materials that tend to form bridges onto the belt. One further advantage is that depending upon the situation, weigh belt feeders, even with pre-feeders, often require less vertical clearance than other fixtures. Many weigh belt feeders are also available with optional heat-resistant silicone belts for applications where the bulk material is coming from a heated process upstream.
If smaller recyclates or flakes are being fed, or if glass fiber is added into compounding processes, vibratory feeders could be a viable alternative. These feeders are available in various sizes with a selection of tray configurations to choose from, appropriate for the application in question and for conveying a wide range of bulk materials. The absence of mechanical parts that are subject to wear is advantageous for continuous operation – vibratory feeders are practically maintenance-free as a result. The bulk material experiences no mechanical impact, either. The key to successful implementation is to ensure the material will flow from the extension hopper above the vibratory feeding module without an arch or bridge being formed.
However, in particular, for companies who are dedicated to using the largest recyclate quantities possible, these feeding technologies are insufficient. If the material presents very irregular sizes or forms, under certain circumstances a screw feeder must be used – generally with a single screw. The feeder’s rotating screw conveys and feeds the material from a hopper into the process below. Using the screw and the horizontal agitator, a uniform mass flow is ensured. Screw feeders are available in various sizes and configurations. One must differentiate between single and twin screw feeding. Both forms are available in gravimetric and volumetric designs.
Twin-screw feeders in particular are also implemented at a later point in time along the value chain, for example, in compounding. Here, the technology distinguishes itself through the precise feeding of finer bulk materials, which are primarily suitable for additives. Thanks to the high precision of the corresponding weighing technology and control algorithms, additional materials are fed precisely into the process according to the recipe, and the end product’s quality is constantly optimized.
The Feeder Controller
The LIW feeder consists of a feed hopper, refill device, discharge device with a variable-speed drive, weight sensing device (either digital or analog), and controller. A feeder operator sets the material feed rate (called the setpoint) by sending information to the feeder’s controller.
When the feeder is in operation the discharge device draws material from the feed hopper and meters it to the downstream process. The weight-sensing device continuously reports the material weight in the hopper (called net weight) to the controller. The controller calculates an actual feed rate based on the loss in net weight, compares it to the setpoint, and increases or decreases the discharge device’s drive speed to accelerate or slow the net weight change (the loss of material in the hopper) so the feed rate matches the setpoint.
To prevent feeding interruptions, the controller periodically commands the refill device to refill the feed hopper with material. During each brief refill cycle, the net weight signal from the hopper is increasing, so it can’t be used as a control signal to determine how much material is being delivered to the process. To compensate for this, the LIW feeder temporarily operates in volumetric mode during refill.
The feeder controller can be integrated into a supervisory process control system that monitors all the feeders and other equipment in your process.
Improved Productivity by Trending Feeder Performance
The LIW feeder’s ability to collect process data in real-time can help you catch small process problems before they become big ones. Today’s advanced controllers can include communication via a wide variety of protocols, with some even including built-in Ethernet and optional Wi-Fi modules. The capacity of newer controllers is sufficient to store historical data records for an extended period of time. This data can include the feeder’s feed rate, net weight, and drive-speed-to-feed rate relationship (called the feed factor).
Summary
As today’s recycling processes continue to evolve, sustainability and circular economy will drive solutions providers to become more forward-thinking in providing better solutions. As a result, manufacturers and processors face the challenge of reconciling the demands placed upon them with technical and economic feasibility. The design of your feeding equipment and the advantages that it will offer to your process will be more important than ever. The investment you make in the feeder must ensure maximum reliability and flexibility. A solid mechanical feeding solution married with today’s state-of-the-art controllers will result in a robust, highly accurate feeding system for many years to come and they give you the assurance that you are well prepared for future recycling challenges.