There is a conveyor for every conceivable application in sorting installations. Whether it is feeding a baler, moving material trough optical separators or storing materials in feeding bunkers, Bollegraaf has a conveyor for your recycling needs. Bollegraaf chain conveyors are characterized by their long service life, robust construction, low maintenance costs and great ease of maintenance. The chain conveyors are used for heavy-duty applications in the sorting process, such as feeding a baler or sorting installation.
Functional Description
Our new robust chain conveyor design promises to transform your material handling operations. With a focus on maximizing availability, improving maintenance accessibility, and enhancing overall efficiency and lifespan, our renewed chain conveyor design is set to revolutionize the industry. The steel frame of the chain conveyor consists of plates on both sides that are connected by means of angled steel profiles. The running surface of the chain is at- tached to this frame. The entire running surface for the chain, both the straight and curved sections, are interchan- geable as they are bolted to the lower frame. Next to this, there is a wide impact beam for the feeding section.
1. Maintenance Hatches
Maintenance hatches have been placed strategically in the frame of the conveyor. This allows for maximum access to the inside of the conveyor, enabling the maintenance team to carry out tasks with more ease and efficiency.
2. Inspection Hatches
Inspection hatches have been placed strategically in the frame of the conveyor. This allows for maximum inspection to the inside of the conveyor.
3. Removable Maintenance
By reducing welding to a minimum, we have introduced an innovative removable maintenance cap, accessing the top chain has never been easier.
4. Integrated Cable Guiding
Our chain conveyor design integrates a state-of-the-art cable guiding system inside the updated sidewalls and frame.
5. Drive Section
The chain conveyor is driven by a geared motor mounted on the shaft. The drive shaft is mounted with two self-adjusting ball bearings. Rubber buffers protect the motor from shocks during start-up. The type of drive motor (and gear reductor) depends on the width, speed and length of the conveyor.
6. Emergency Stop Pull (Pull Cord)
Every moving part is shielded and the operator is protected from falling material. The machine is also equipped with both emergency stops and stop pull cords that stop the conveyor immediately in dangerous situations. Optionally, the belt can be equipped with an automatic person detection system that switches off the belt immediately as soon as an operator is detected.
7. Tensioning Section
The chain is tensioned by two tensioning sections. The chain can be tensioned from the back, where often there is the most space available. The bearings have been greased for at least 10,000 hours of operation and therefore require very little maintenance.
8. Belt Package + Cleats
The belt package consists of the chain, belt carriers, a rubber belt and optionally cleats. The chain has a pitch of 6’’ and is equipped with hollow links. Between the chains, steel tubes are bolted every 300 mm as carriers to which the rubber belt is attached. The belt carriers can be replaced without interrupting the chain. The rubber belt is wear-resistant, and oil- and grease- resistant versions are optionally available. The belt can be equipped with cleats, varying in heights of 50 mm or 100 mm and spacings of 600 mm or 900 mm.
9. Replaceable Wear Strips
Easily replaceable wear strips are positioned between the belt and sidewalls.
10. Safe Underplate Protection
The underplate protection guarantees enhanced worker safety by preventing accidents when installing or opening the panels.
11. Debris Releasing Gaps
Strategically placed debris releasing gaps are placed along the chain rails. The chain rails in the radius up and down are distanced from the chassis to prevent material buildup. These rails are designed to be picked up easily.
12. Radius Rails
The new radius rails are now easier to replace as they are split in two to increase maintenance ease.
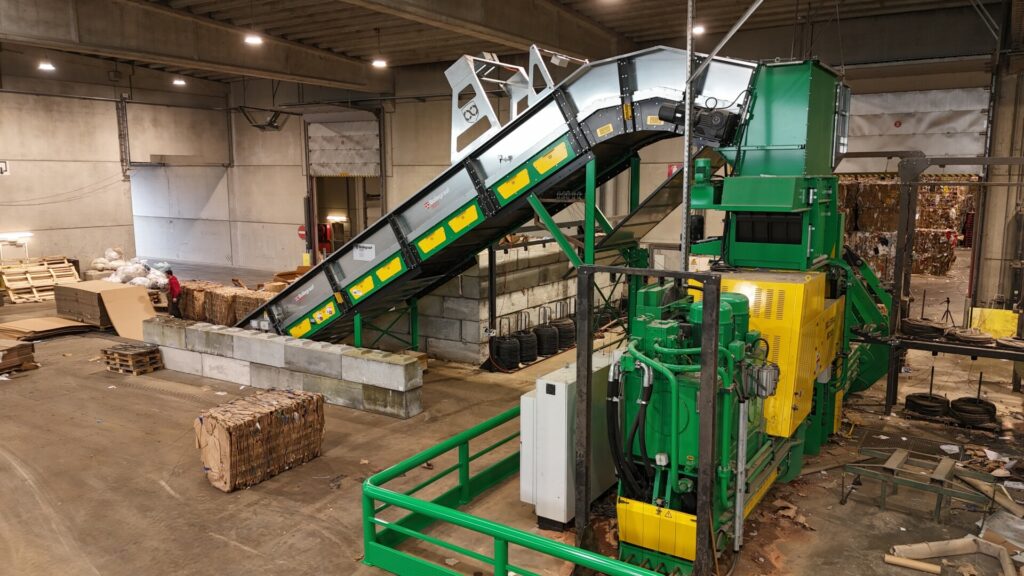
The Advantages
- Minimal downtime – An increased number of maintenance hatches strategically placed throughout the conveyor allows for maximum access to the internal components. This enables the maintenance team to carry out tasks with increased ease and efficiency. Because of the innovative removable maintenance cap, accessing the top chain has never been easier. This feature ensures quick and hassle-free inspection, cleaning, adjustment, and replacement of the chain. By reducing maintenance time, your operation will experience minimal downtime, leading to enhanced productivity and increased profits.
- Extended lifespan – Easily replaceable wear strips positioned between the belt and sidewalls extend the lifespan of your conveyor system. This not only ensures optimal performance and reduced downtime but also minimizes maintenance costs in the long run. Next to this, the design includes strategically placed debris-releasing gaps along the chain rails. These gaps facilitate the release of debris or contaminants that may accumulate during operation. The wide impact beam also results in a longer lifespan and less wear and tear of the belt package cleats.
- Safety first – Safety is our utmost priority, which is why our chain conveyor design includes improved underplate protection. This feature guarantees enhanced worker safety by preventing accidents whilst installing or opening these panels. This improvement creates a safer work environment, boosting employee morale and overall productivity.
- Great aesthetics – Our chain conveyors have a modern and appealing aesthetic. We understand the importance of a visually pleasing workplace, and our design team has carefully crafted a conveyor system that combines functionality with an attractive appearance. There is a state-of-the-art cable guiding system inside the updated sidewalls. This thoughtful inclusion ensures that cables are neatly organized and protected.
The Options
- BOSS – Bollegraaf Operational Safety System – BOSS puts an electromagnetic field around the danger zone of the top section of the feed conveyor and the opening of e.g. the baler. Every operator that works around the conveyor carries a transponder. When an operator falls onto the conveyor and the transponder reaches the electromagnetic field, the conveyor and baler will stop immediately. Preventing accidents from happening.
- Variable frequency drive – Automatic adjustment to the most efficient engine frequency. Energy saving idle mode when waiting. Reduces current peaks during engine startup.
- Chain lubrication module – Reducing the need for manual chain lubrication. Two different types of lubrication are available.
- Motor left or right – The motor can be placed left or right, depending on the installation requirements.
- Bordoflex – In case of fine and/or wet material, Bollegraaf offers a Bordoflex option to prevent this debris from reaching the chain.
- Reversible rotation of the belt
Technical Specifications
Section length (mm) | 500 / 600 / 700 / 800 / 900 / 1000 / 1500 / 2000 / 2500 |
Sidewall height (mm) | 300 / 500 / 800 / 1200 |
Width (mm) | 1200 / 1400 / 1500 / 1600 / 1800 / 2000 |
Rubber belt types | RA / ROS (oil resistant) / Bordoflex (ROS) |
Cleat height (mm) | none / 50 / 100 |
Motor types | KA87 – 2700Nm / KA97 – 3900Nm / KA107 – 6500Nm |
Incline degree angle (o) | 25 / 30 / 35 / 40 / 45 |
Decline degree angle (o) | 0 / 10 / 15 / 20 / 30 |
Speed (m / minute) | 1,5 -24 |