From Manual to Machine: The Evolution of Waste Sorting
Historically, waste sorting has been a labor-intensive process involving manual picking and rudimentary mechanical separation based on size, weight, and magnetic properties. While these methods have served their purpose for decades, they often result in contamination, misclassification, and inefficiencies that compromise the quality of recycled materials.
With the introduction of AI, recycling facilities can now automate sorting decisions with greater accuracy and speed. AI technologies are not just replacing manual labor—they are transforming the logic behind sorting by enabling real-time identification and classification of waste streams based on material type, shape, color, and even chemical composition.
Machine Learning: Teaching Systems to Recognize Waste
At the core of AI-driven recycling is machine learning (ML), a subset of AI that enables systems to learn from data without being explicitly programmed. ML algorithms can be trained on thousands of labeled images of recyclable materials to identify patterns and make predictions. These models improve over time as they are exposed to more data, allowing for increasingly accurate classification of waste items.
Supervised learning models, such as convolutional neural networks (CNNs), are particularly effective in recognizing waste based on images. For example, a CNN can distinguish between PET bottles and HDPE containers based on subtle visual features. More advanced models are being trained to recognize multilayer packaging, composites, and electronic components, which were previously considered too complex for automated sorting.
Computer Vision: Seeing Waste in Real Time
Computer vision technologies enable recycling systems to “see” and interpret visual information. High-resolution cameras, combined with real-time image processing, enable machines to detect and classify waste items on conveyor belts with remarkable precision. These systems operate under various lighting conditions and at high speeds, making them suitable for industrial-scale applications.
Recent advancements in edge computing have enabled the deployment of computer vision models directly on sorting lines, thereby minimizing latency and enhancing decision-making. This is particularly useful in materials recovery facilities (MRFs), where rapid and accurate sorting is essential to maintain throughput.
Robotic Sorting Arms: Precision Meets Performance
One of the most visible applications of AI in recycling is the use of robotic sorting arms. These robots are equipped with AI-enabled vision systems and suction or gripper mechanisms, allowing them to pick, sort, and separate waste items with high accuracy.
Companies like AMP Robotics and ZenRobotics have developed robotic systems capable of performing up to 80 picks per minute, rivaling the efficiency of human sorters. These robots can be trained to target specific materials—such as aluminum cans, cardboard, or certain types of plastic—based on operational priorities and market demand.
Robotic sorting offers several advantages over manual labor, including reduced exposure to hazardous materials, consistent sorting quality, and 24/7 operation with minimal downtime.
Sensor Fusion: Beyond What the Eye Can See
While computer vision excels at recognizing visual cues, some materials require more advanced detection methods. This is where sensor fusion comes into play. By combining data from multiple sensors—such as near-infrared (NIR) spectroscopy, X-ray fluorescence (XRF), and hyperspectral imaging—AI systems can analyze the physical and chemical properties of waste items.
For instance, NIR sensors can distinguish between different types of plastic polymers, while XRF is used to detect the presence of metals, including rare-earth elements, in electronic waste. AI models synthesize this multispectral data to make informed decisions about how each item should be sorted.
Sensor fusion significantly enhances the granularity and accuracy of material classification, particularly for complex waste streams such as electrical and electronic equipment (WEEE), automotive shredder residue (ASR), and multi-material packaging.
Data Analytics and Predictive Maintenance
AI in recycling isn’t limited to real-time sorting decisions. It also plays a crucial role in operational analytics. Data collected from sensors, cameras, and robotic systems can be analyzed to identify bottlenecks, forecast material flow, and optimize equipment performance.
Predictive maintenance is one such application. AI algorithms analyze historical and real-time machine data to detect patterns that precede equipment failure. This enables recycling facilities to perform proactive maintenance, reducing unplanned downtime and extending the lifespan of their machinery.
Moreover, analytics platforms can provide valuable insights into material recovery rates, contamination levels, and market trends, enabling data-driven decision-making at both operational and strategic levels.
The Role of Digital Twins and Simulation
Digital twins—virtual replicas of physical systems—are increasingly used to simulate and optimize waste sorting operations. These models integrate real-time data from recycling equipment to mirror the behavior of the actual system.
By using AI-powered simulations, facility managers can test different configurations, sorting strategies, and throughput scenarios without disrupting live operations. This helps improve process efficiency, reduce energy consumption, and fine-tune the deployment of AI models across different waste categories.
Real-World Applications and Case Studies
Numerous pilot projects and commercial installations are demonstrating the real-world impact of AI-driven recycling systems:
- AMP Robotics has deployed over 300 robotic sorting systems in North America, Europe, and Asia, reportedly achieving recovery rates of over 90% for specific materials.
- Greyparrot, a UK-based startup, offers AI-powered waste analytics that provide real-time insights into material composition, helping facilities comply with regulatory requirements.
- Tomra Sorting integrates AI into its optical sorters to improve the separation of food-grade and non-food-grade plastics.
These initiatives highlight the scalability and adaptability of AI across various waste streams, including packaging, textiles, construction and demolition waste, and organic waste.
Challenges and Limitations
Despite the promise of AI in waste sorting, several challenges remain. Data quality and quantity are critical for training accurate models, and acquiring representative datasets for diverse waste streams can be time-consuming and expensive.
Integration with existing infrastructure is another hurdle. Many recycling facilities operate with legacy equipment that may not be compatible with modern AI systems without significant retrofitting.
Furthermore, AI models can be sensitive to changes in lighting, contamination, and object orientation. Ensuring robustness in dynamic environments requires continuous model updates and performance monitoring.
Finally, ethical concerns related to labor displacement must be addressed. While AI reduces the need for manual sorting, it is essential to invest in retraining programs and create new opportunities in the green economy.
Outlook: Toward Autonomous Recycling Facilities
As AI technologies continue to mature, the vision of fully autonomous recycling facilities is becoming more realistic. These “smart MRFs” will feature end-to-end automation, encompassing waste intake and material recognition, robotic sorting, data analytics, and outbound logistics.
Integration with blockchain technology may also enable real-time tracking of recycled materials, enhancing transparency and traceability in the supply chain.
Ultimately, AI-driven innovative recycling represents a critical step toward achieving circular economy goals. By increasing the efficiency, accuracy, and scalability of waste sorting, AI has the potential to close the loop on material use and create a more sustainable future.
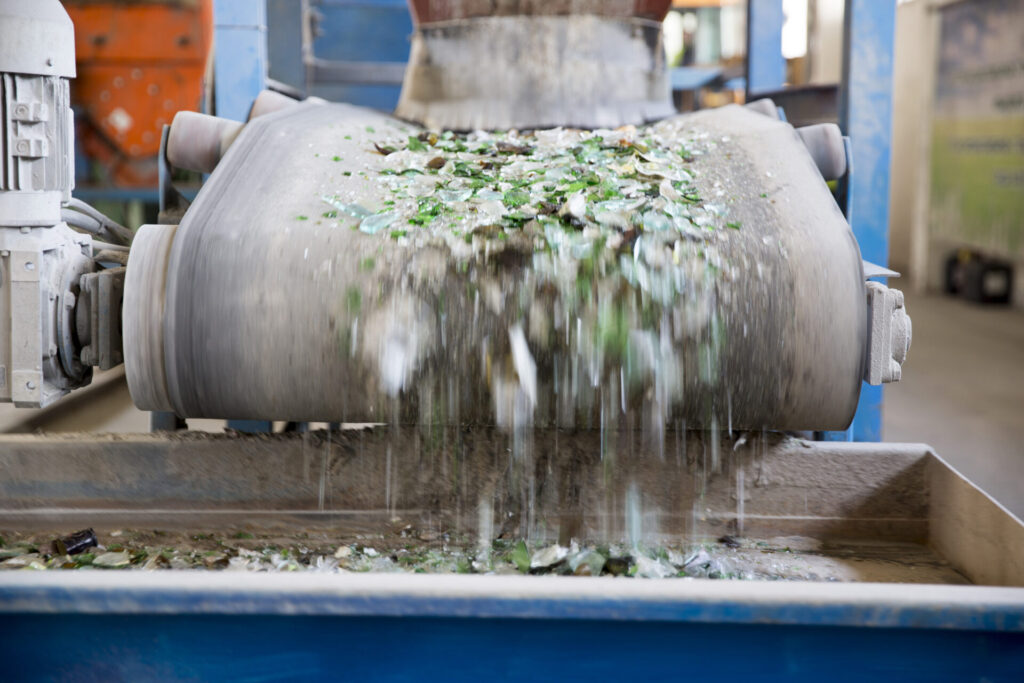