Whereas, the Eccentric magnetic pole technology is based on a concentric axis, through the bearing and adjustment device to adjust the concentric magnetic roller to the outer barrel side, and then the magnetic roller can be adjusted up and down according to the material situation within 15 degrees to control the starting point of the material to improve the sorting rate of small materials.
Concentric type and Eccentric type sorting machine in comparison:
In concentric designs, the rotor is located in the center, leading to higher wear since the magnetic field interacts more directly with all materials.
In eccentric designs, the magnetic rotor is offset from the center of the outer drum. This minimizes the direct exposure of the rotor to abrasive materials, reducing wear and tear.
Consider this…
Concentric separators may still be preferred for simpler applications with uniform materials or where cost is a primary concern.
The choice between an eccentric and concentric eddy current magnetic separator often depends on the specific application, material type, and separation efficiency required. Here’s why an eccentric eddy current separator is often preferred:
- Reduced Maintenance and Wear (Optimized Belt Drive and Rotor Drum adjustment running cycles)
- Better Material Flow Control: Eccentric separators provide better control over the trajectory of non-ferrous metals and waste streams. This ensures more precise separation by adjusting the point of maximum magnetic force.
- Minimized Magnetic Interaction with Ferrous Metals: Ferrous contamination can stick to the drum in concentric designs due to the consistent high magnetic field around the rotor. Eccentric designs localize the magnetic force to a specific zone, reducing the risk of ferrous material buildup.
- Improved Separation Efficiency: Eccentric systems allow for a more dynamic adjustment of the magnetic field, which can be fine-tuned to optimize separation for specific materials or particle sizes. They reduce the effects of “shadowing,” where one material shields another from the magnetic field, leading to higher recovery rates.
- Adaptability for Varying Materials: Eccentric systems are often more versatile for handling materials with different densities, shapes, and sizes due to their localized and adjustable field strength.
- Energy Efficiency: Since the magnetic field in eccentric systems is focused on a smaller area, they often consume less energy for the same separation results compared to concentric designs.
What are the most typical processed material for magnetic separation?
Plastic Film – Woven Bag – Wood Pallet – Copper Cable Wire – PET Bottle – Plastic Pipe – Tire, Rubber – Radiator – Cardboard Carton – Medical Waste – Textile – Aluminium Scrap – Medical Waste – Animal Bone – Plastic Pallet Tray – Organic Waste – E-Waste (Printed Circuit Board) – Vehicle Bumper – Coconut Husk – Aluminium Foil – Plastic Drum Barrel – PVC – Reinforced Fiber Hose- Other
In summary, eccentric eddy current separators are generally more efficient, adaptable, and durable, making them the preferred choice in complex or high-demand separation processes.
In this context IDEMAG has been manufacturing and evolved into the stages of Eddy-Current machines with the EVO series.
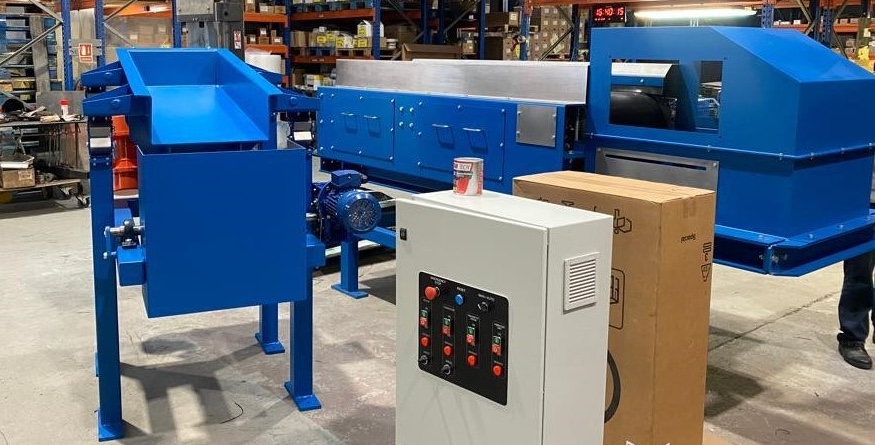
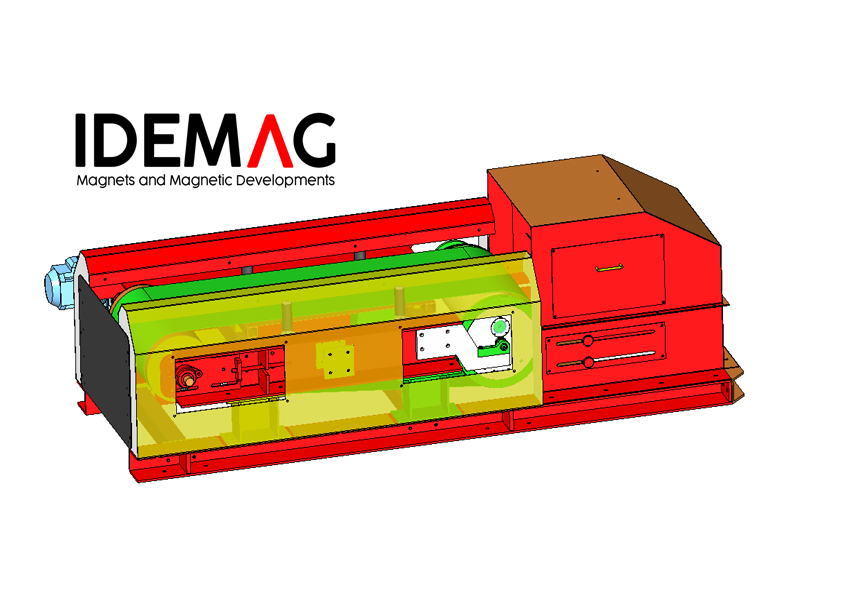
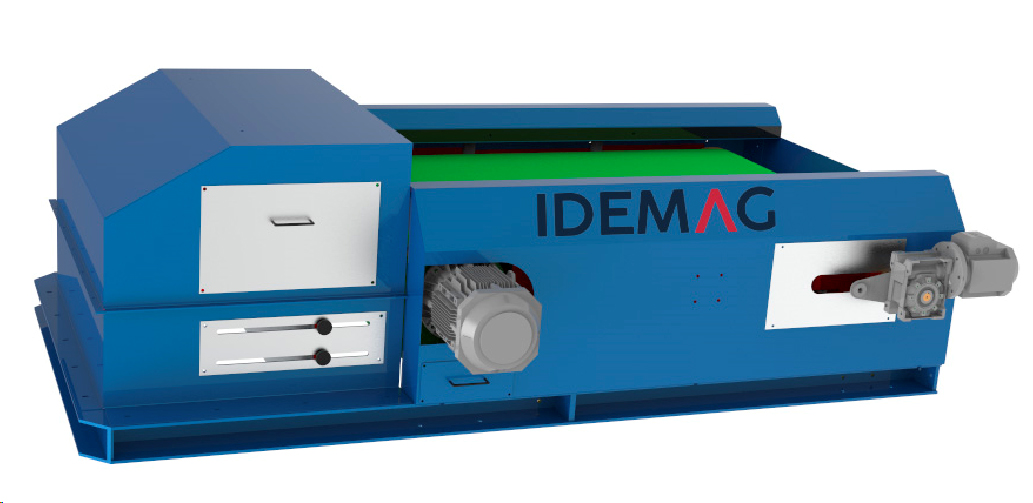