Founded in 1929, Grundon has evolved to become a total waste management service provider, offering the collection, treatment, recovery, recycling, and disposal of non-hazardous waste streams as well as dealing with all aspects of hazardous waste, including contaminated waste, clinical and healthcare waste, and waste electrical and electronic equipment (WEEE). The company operates from a range of industry-leading, state-of-the-art treatment facilities, enabling Grundon to offer its customers the most modern, compliant, and environmentally friendly methods of recycling and waste disposal.
Seeking to stay ahead of the market and maximize efficiency, Grundon researched options to enhance their waste sorting process, particularly in picking food-grade plastics, such as HDPE and PET, which they had not done before. The challenge was to increase efficiency, pick higher-value products, and facilitate their recycling and reuse at a higher level.
A solution to pick more products, effectively and efficiently
The solution was a ZenRobotics Fast Picker – a robotic system to pick more products with greater effectiveness and efficiency. Grundon collaborated closely with ZenRobotics throughout the implementation process. ZenRobotics provided realistic expectations regarding the machine’s capabilities, what it could pick, the cleanliness of the picking process, and its overall efficiency. The commissioning process was seamless, and by integrating the Fast Picker into their operations, Grundon is now able to sort food-grade plastics, including milk bottles and soft drink bottles, allowing these valuable materials to achieve higher market value, and be recycled as food-grade plastics.
Ed Fagan, Head of Projects Engineering & Design at Grundon expressed his satisfaction with ZenRobotics’ support throughout the installation and commissioning phases, “The Fast Picker arrived on schedule, meticulously packaged, and the installation was completed smoothly over a long weekend. The commissioning process, which included a comprehensive three-week training session, ensured a seamless transition. Since its installation, the Fast Picker has been running for over a year without major breakdowns, reflecting its reliability and efficiency.”
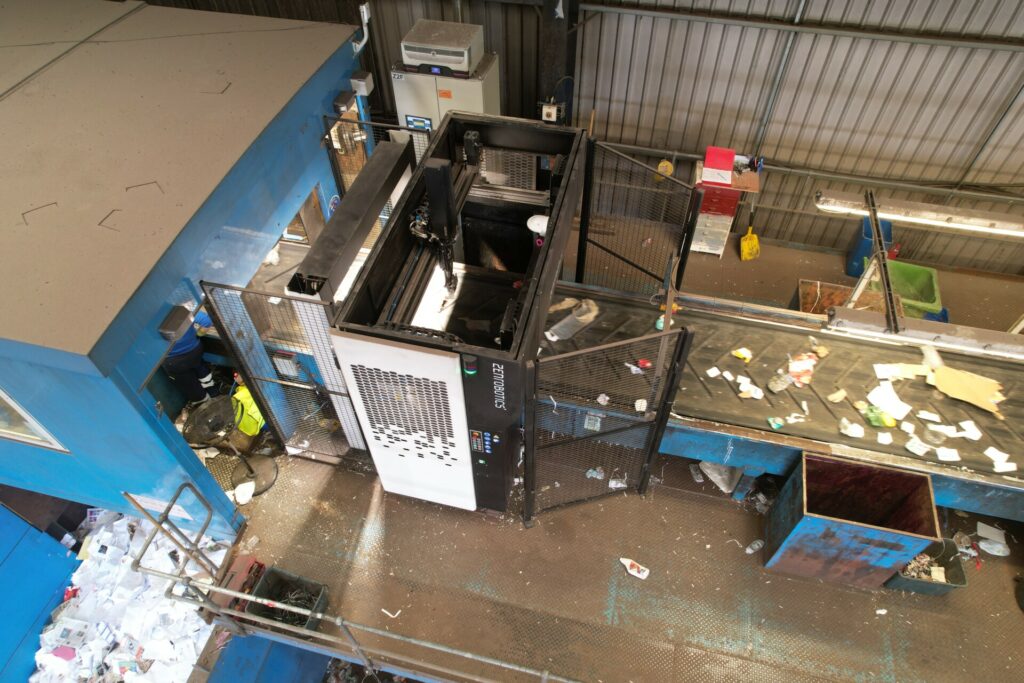
Improvements in accuracy, environmental impact, and safety
The Fast Picker has enabled Grundon’s to pick more products efficiently and accurately, surpassing their previous capabilities. The picking process became faster, allowing for improved productivity and throughput.
It has also enhanced environmental impact of their operations, as by effectively sorting food-grade plastics, Grundon can sell them as higher-value products. This not only increased market value but also facilitated their recycling and reuse at a higher level, contributing to a more sustainable waste management process.
Finally, the Fast Picker’s presence on the sorting line has reduced the need for human intervention, enhancing safety for human pickers. With the Fast Picker handling certain products, human pickers can focus on their tasks with improved safety.
Artificial Intelligence and Robotics Integral to the Future of Waste Management
Grundon foresees Artificial Intelligence (AI) and robotics as integral to the future of Material Recovery Facilities (MRFs). The combination of AI and robotics allows for the capture of valuable information on the sorting line, which can be used to optimize future recycling processes. The company envisions future plants equipped with multiple robots and optical sorters, all interconnected through a central brain, enabling adaptive sorting based on the specific materials being processed.
Michael McMenamin, Regional Sales Manager, ZenRobotics said, “The demands of our customers are constantly evolving and meeting their needs with a sustainable approach that supports them in extracting as much value from waste while increasing efficiency and safety of their operations is what we at ZenRobotics are all about. Having the Fast Picker installed at Grundon, who are pioneers in waste management, is a huge testament to the ability of our equipment to support the circular economy improve operational efficiency.”