LIPOR is not just any company. The disposal company, founded in 1982. is responsible for waste treatment in eight municipalities in the Greater Porto area, a region which is home to more than one million people. LIPOR processes around 500,000 tons of waste annually with a clear objective – to recycle as much as possible and to protect the environment. In addition to simply recycling waste, the company also utilises comprehensive education and information programmes to boost the public’s environmental awareness.
The old days in the “LIPOR 1” facility are a thing of past – and for good reason. Since 2019, LIPOR has been working on modernising its sorting facilities – an ambitious project aiming to increase capacities and digitalise the entire process. “We had always wanted to bring this technology here,” says Helder Filipe, Head of Operations and Logistics, who is responsible for developing the site. The decision to go with the state-of-the-art solutions from STEINERT was made as the result of extensive research and tests. “We met at a trade fair and arranged a test date right away to see how the machines sort our materials,” continues Filipe.
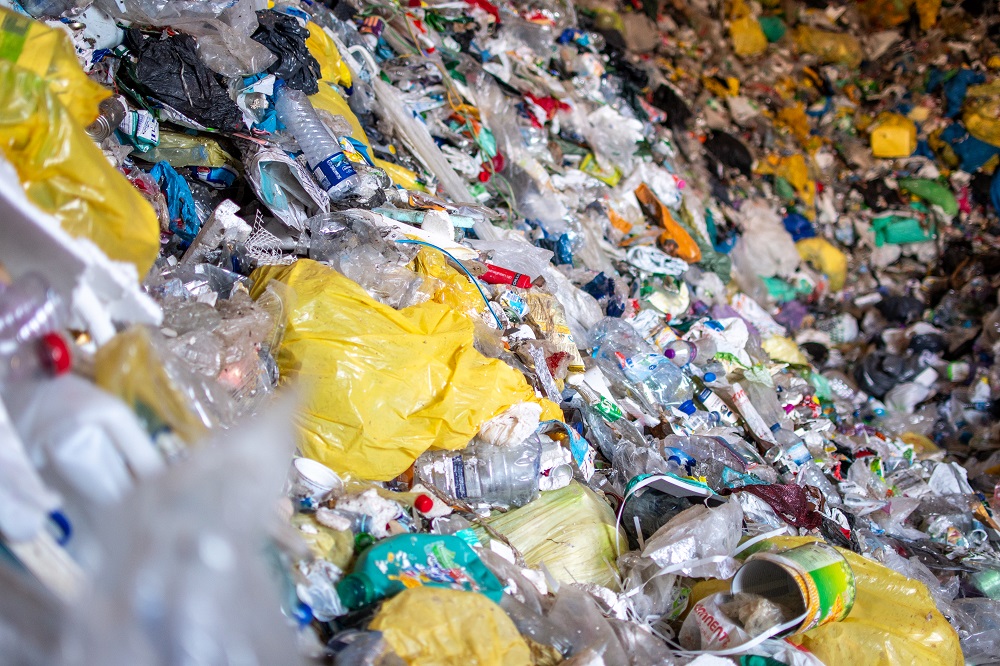
The facility has now been equipped with seven UniSort near-infrared (NIR) sorting systems, two STEINERT UME overhead suspension magnets and one STEINERT CanMaster eddy current separator. This upgrade in technology has revolutionised the company’s working processes. Instead of manually sorting 12,000 to 13,000 tons of waste annually, the facility now processes it two to three times faster at 8 tons per hour – and it does so with a significantly reduced workforce of 12 to 14 employees. “Generally speaking, they no longer have to sort the waste themselves, but rather simply carry out quality controls or undertake maintenance tasks,” says Filipe during a tour around the facility.
The switch to automated processes, however, was not without its challenges. “Of course, there was opposition at the beginning as well as questions about possible job losses,” Filipe openly admits. However, LIPOR found a solution, as the employees have been retrained and many of them have been able to take on other tasks within the company. For Filipe and his colleagues this means one thing above all else – security. “We are still able to continue working in this field, but with machines handling the majority of the work,” he explains. During the tour through the factory, it becomes clear that it is about more than efficiency. It is a flagship project which demonstrates how technology and sustainability can go hand in hand.
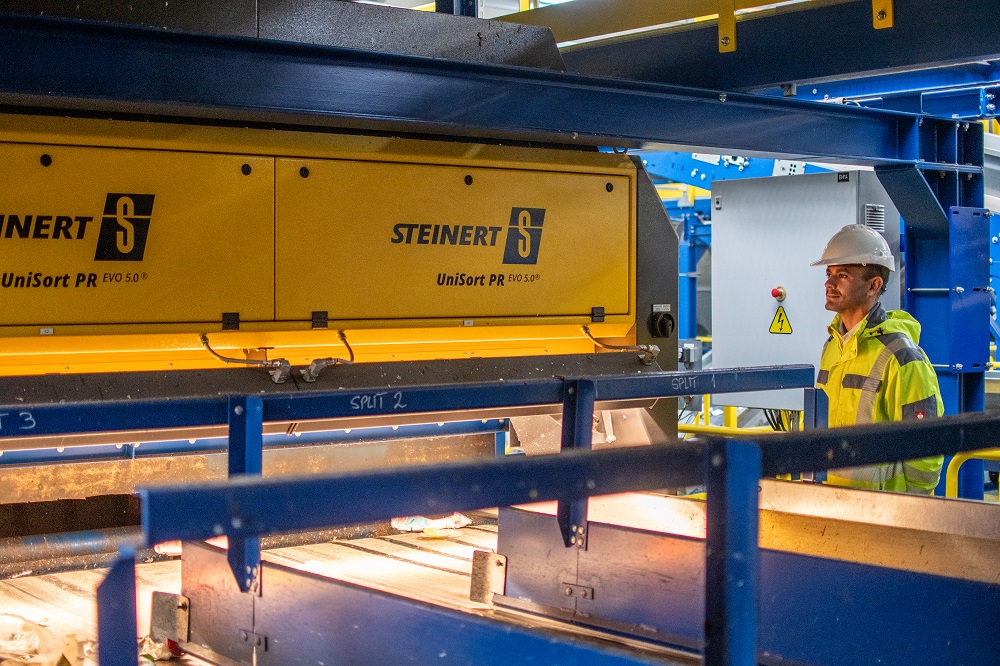
A further benefit of the new facility is the improved material separation. 20 to 25 percent of the materials put in recycling bins in Portugal still cannot be recycled or are contaminated. Thanks to the new sorting systems, LIPOR is able to better utilise these materials, which has resulted in a significant reduction in the amount of waste in a number of sorting fractions such as PET, PP and PE in 3D and 2D as well as TetraPak, cans, iron and paper.
The facility is also able to flexibly adapt the machines to new requirements and material properties. New packaging formats and materials are constantly appearing on the market, making this adaptability indispensable for ensuring the efficiency and quality of the sorting facilities. The separation of thermoformed PET, which has been prescribed by law since the start of the year, poses a particular challenge. Nevertheless, Filipe remains optimistic: “We are continuously collaborating with STEINERT to improve our situation,” he states. “AI and data analysis will play a big role in this. When it comes to our investment in this facility, we can’t afford for the material to call the shots – we have got to be in the driving seat. To ensure that we are less dependent, we have to be able to detect and understand the material so that we can modify the process.” This strategic focus shows how LIPOR is not only addressing environmental challenges, but also economic challenges by using innovative technologies and is therefore playing an active role in shaping the future of waste management.