As the industry strives to enhance throughput and tackle challenging feed materials, advanced shredder technology has become essential. Companies like Herbold Meckesheim are at the forefront, developing sophisticated solutions that cater to the needs of modern washing plants.
The Challenges of Contaminated Plastics
One of the primary challenges in plastic recycling is the processing of heavily contaminated materials sourced from the post-consumer sector. This necessitates shredders that can handle large volumes of plastics laden with various impurities, including minerals. To address this, integrated washing plants are increasingly adopting stage concepts that utilize technology tailored to different processing steps. Key considerations include energy efficiency and the implementation of diverse motor and transmission systems, such as belt drives and hydraulic systems, alongside traditional gear-driven options.
As recycling operations become more demanding, the focus on machine longevity has intensified. Shredders must exhibit high resistance to contaminants, extended service life for cutting blades, and robust construction to withstand potential damage. To facilitate maintenance, accessibility to all machine components, particularly the rotor, is crucial. This design philosophy allows for the easy replacement of wear parts, such as knives and plates, while efficient overload protection minimizes downtime—an essential requirement in today’s fast-paced recycling environment.
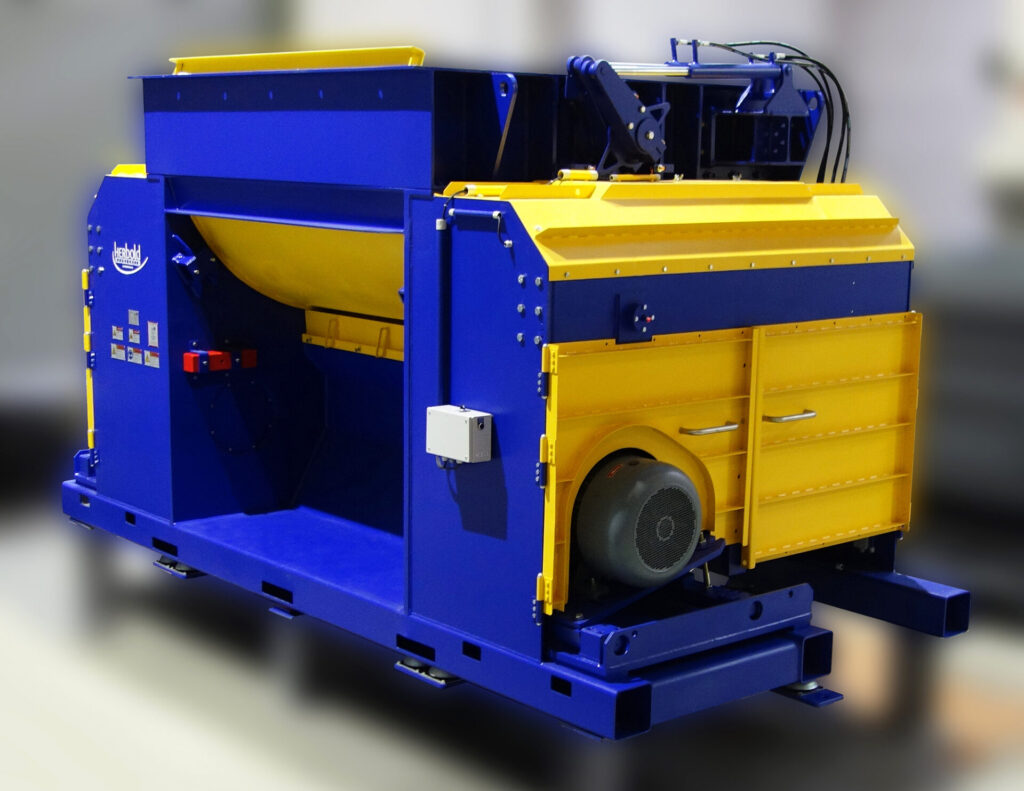
Innovative Solutions in Shredder Technology
A prime example of cutting-edge shredder technology is the Herbold Meckesheim single-shaft shredder model 60/210. This machine is engineered to handle high throughputs and entire bales of plastic, making it suitable for both dry and wet size reduction processes. Its robust construction is complemented by a maintenance-friendly design, featuring a large double-wing door and a hydraulically swing-away grinding chamber trough, which enhances accessibility for operators.
The 60/210’s standout feature is its externally mounted, wear-protected rotor, which allows for customizable knife configurations within cassettes. This design includes screwed-on armor plates, eliminating the need for time-consuming hard facing. Additionally, replaceable stator knives are positioned opposite the rotor, with an optional second row available for enhanced performance. The machine’s energy-efficient double-sided belt drive, characterized by large flywheel masses, minimizes maintenance needs and eliminates the risk of gearbox failures. An overload clutch further protects the machine from potential damage caused by foreign objects.
Another noteworthy innovation is the double-shaft shredder DWS 45/160, also from Herbold Meckesheim. This model boasts a large rotor contact surface, resulting in exceptional ingestion performance. It is particularly adept at processing materials that traditional shredders struggle to handle, such as big bags and large containers. The DWS 45/160 ensures uniform and consistent granule sizes, whether operating in dry or wet conditions, thanks to its customizable screen selection. Unlike conventional twin-shaft shredders, this model avoids the production of long strips, enhancing the quality of the output.
Focus on Future Developments
The ongoing refinement of shredder technology focuses on enhancing wear protection, simplifying maintenance, and reducing personnel requirements. Current engineering efforts at Herbold Meckesheim emphasize the exploration of various rotor designs and modular configurations that can adapt to the flexible requirements of washing lines. This flexibility is crucial as recycling operations continue to evolve, necessitating equipment that can seamlessly integrate into diverse processing environments.
As the plastic recycling industry faces increasing pressures to improve efficiency and sustainability, the role of advanced shredders cannot be overstated. Innovations from companies like Herbold Meckesheim are setting new standards in shredder technology, enabling recycling plants to process contaminated materials effectively while maximizing energy efficiency and minimizing maintenance needs. The future of plastic recycling hinges on these technological advancements, ensuring that the industry can meet the challenges of today and tomorrow.