High Recycling Quotas with Deposit-Return Systems
The basis for an efficient recycling economy is the collection, sorting and recycling of packaging material. Only in this way can valuable raw materials such as paper, plastics, metal and glass be processed and reused. Deposit-return systems have proven themselves in this regard. Higher collection quotas and therefore higher recycling quotas can be achieved in a short time. After a deposit-return system was introduced in Lithuania, the collection quota for PET bottles tripled to about 92% after only 2 years. According to the Reloop organization, almost every European country with deposit-return systems for single use drinks packaging reported a recycling rate of over 85%. Although recycling PET is more expensive than producing new bottles, since non-recycled plastics are often burned, recycling is definitely a plus for the carbon footprint.
For many EU member states, a deposit-return system, in particular for drinks bottles and cans made of PET and aluminium, is nothing new. Apart from Germany, other countries such as Belgium, the Netherlands, Croatia as well as the Scandinavian and Baltic states, also have such systems. Motivated by the planned EU directive, many other EU members such as Austria, the Czech Republic, Portugal, Ireland and Hungary all want to follow suit and introduce deposit-return systems. Romania ,as the 14th European country, recently installed almost 80,000 collection points and presumably has, therefore, the most extensive deposit-return system in the world.
The Organization is decisive
The creation of a modern deposit-return system depends on an effective organization and on effective logistics. Manufacturers, retailers, service partners, recycling companies and government authorities must be listened to and included in the discussion. Depending on where and how the empty containers are collected, it is necessary to create systems not only for counting and invalidating the containers, but also for transporting them as efficiently as possible to the recycling stations.
This is where HSM GmbH + Co. KG provides advice and assistance to the retailers, counting centres and recycling companies in those countries about to introduce the deposit-return systems or to those where it is has already been introduced. As a solution provider both for the invalidation and compaction as well as the further pressing of PET bottles and drinks cans, the company can provide solutions for a significant part of the deposit-return system.
Solutions for Compaction and Invalidation
As the partner to manufacturers of deposit-return machines, HSM also goes with them into new markets. Most of the used drinks containers reach a recycling company via automated collection by the machines which take empty containers. Almost everyone knows the typical “crunching” sound after putting a bottle into the deposit-return machine. That noise is generated when the bottle goes through an HSM Crusher which perforates and compacts the plastic bottles or drinks cans. This not only ensures that the deposit on the container is invalidated, but the container volume is also reduced by up to about 15 to 20% of the original size, thus saving space for both storage and transportation. However, this is often only the first step. For efficient transportation, the bottles must be compressed again to form bales which are easy to handle.
Depending on how the retail or the return system is organized in a country, it is possible to have the additional volume reduction at several points along the way. It either happens on-site or at regional collection centres. As a worldwide leader in the field of baling presses, HSM is also the right address for all these applications.
Compression in the Store itself
Where there are high return quantities, perhaps in larger retail stores or in shopping centres, it is worth pressing the bottles compacted by the on-site crusher into compact, easily transportable bales. Best suited for this task are vertical baling presses. They only take up a little space and generate bales with a weight of up to 350 kg (PET bottles) and a size of 1200 x 780 x max. 1200 mm. Since PET in particular is a particularly abrasive and expansive material, HSM has developed baling presses specially for this material, such as the HSM V-Press 860 E.
Those bottles which, thanks to this type of baling press, have been reduced by up to 90% in volume, can then be taken to a central storage or collection point from where they can be packed together for transportation to a recycling plant.
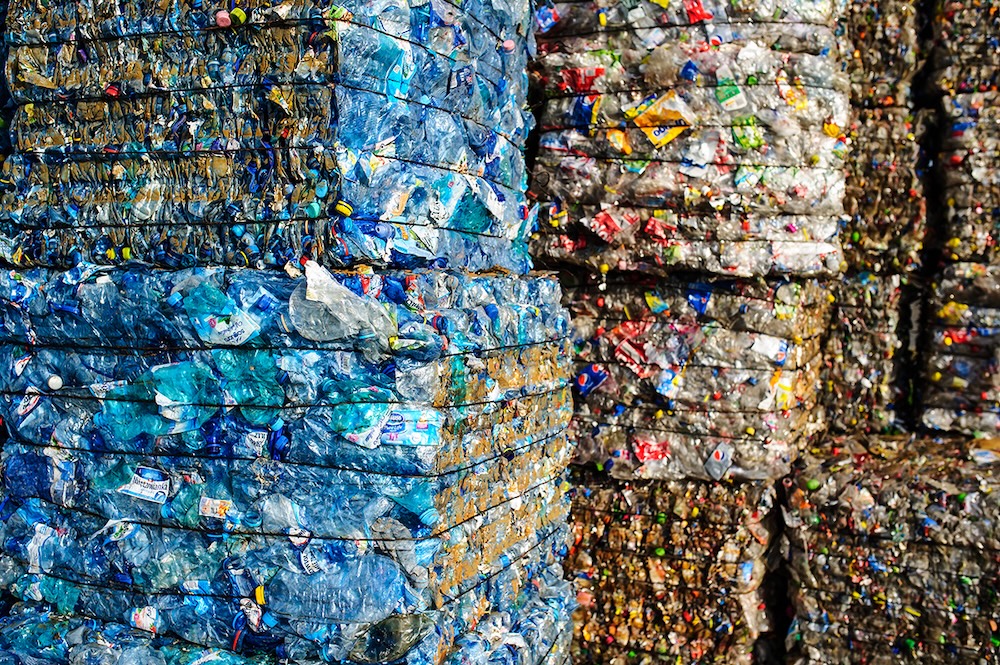
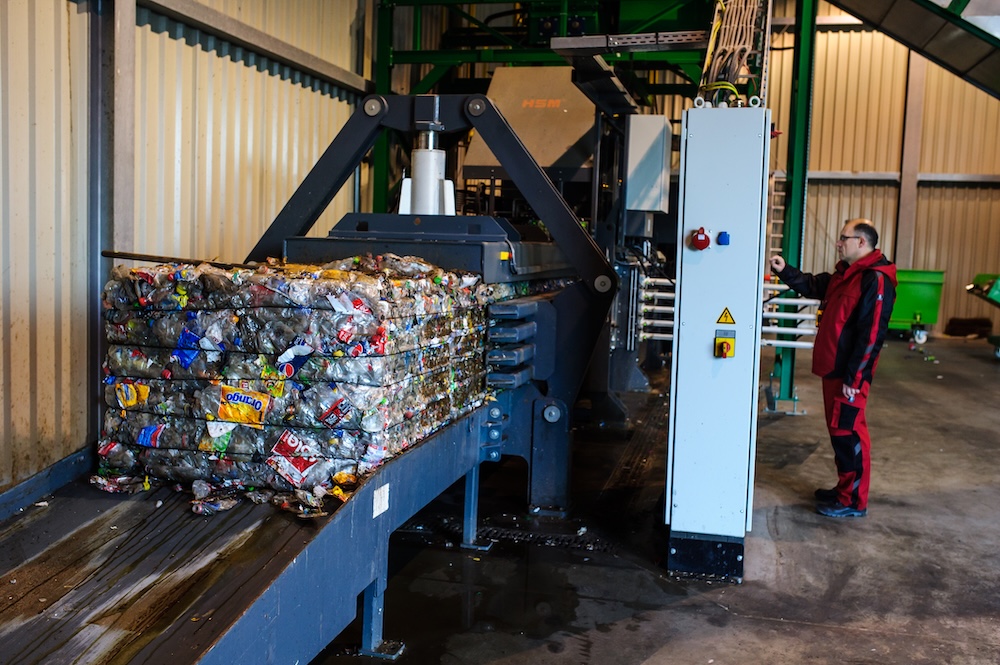
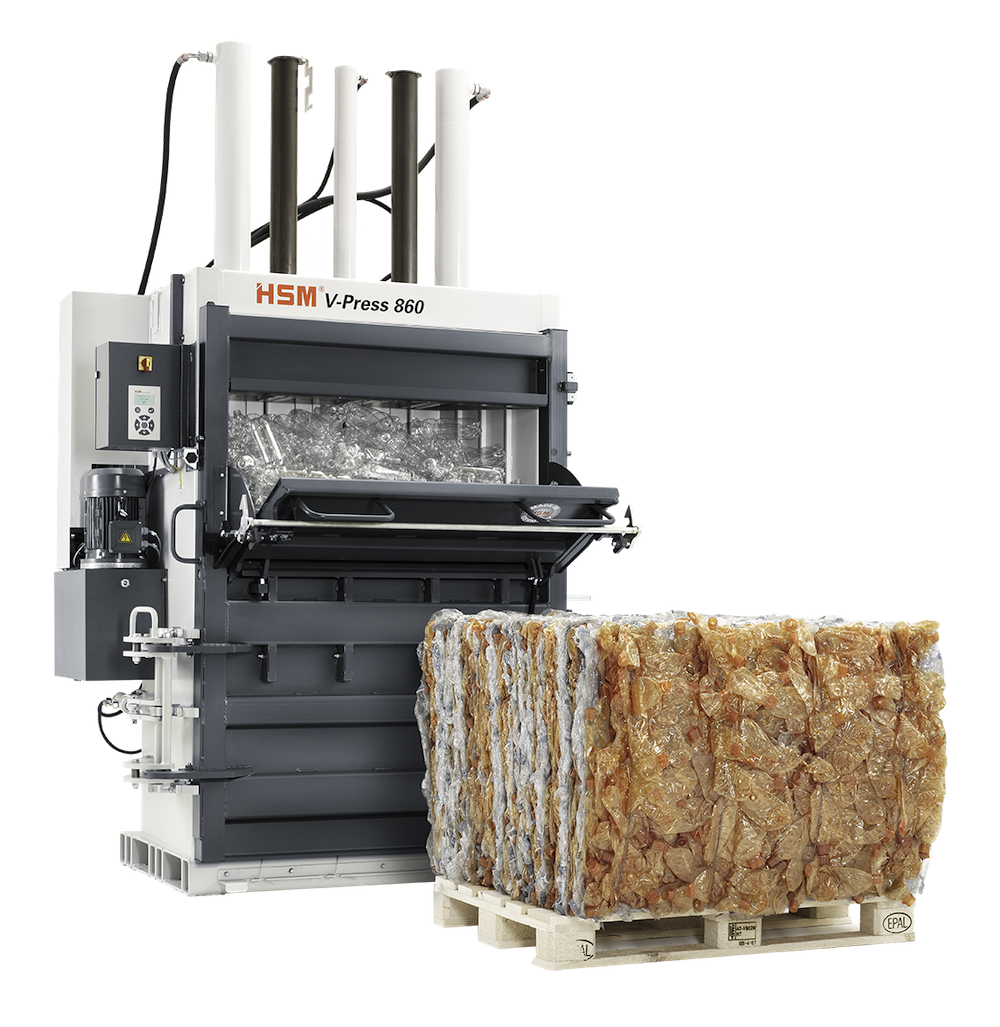
Pressing in Collection or Recycling Centres
In addition to presses which save space and are simple to operate for initial return locations, HSM’s broad baling press spectrum also offers complete disposal systems for the compaction of large quantities of PET bottles and drinks cans. It is therefore possible to combine and compact both material already pre-compacted by a crusher as well as drinks containers collected by smaller retailers in sacks.
The system solutions with fully automatic channel baling presses are always individual solutions adapted to the on-site requirements and can be supplemented with feed-in systems such as conveyor belts as well as other options such as perforators to invalidate and pre-compact those bottles and cans not collected by deposit-return systems. The experienced HSM specialists oversee the projects from the start and provide continuous support and service. These services include arranging transport, installation, and the maintenance and servicing of such systems.
Key Word Reliability
Whether the crusher is part of a deposit-return system or part of a baling press, the reliable operation of the HSM products is guaranteed. HSM is focussed on quality “Made in Germany” and on the location Germany. The production of the crushers and the baling presses is carried out with a very high manufacturing depth of about 90 % and they are only produced in the three sites in Germany; at the HSM Headquarters at Lake Constance and in Reichenbach in the Vogtland. HSM therefore not only keeps its quality promise but also produces as sustainably as possible.
Almost 6.200 m2 of the company’s spaces are heated by heat recovery from the company’s own production. Photovoltaic systems and a gas turbine generate about 25% of the company’s electricity requirements. Additionally, the use of eco friendly and recyclable auxiliary materials, the recycling of metal production waste, re-use of lubricants and cooling lubricants in the production plants as well as transport trips kept to a minimum, are amongst the many items on the HSM ecological agenda.
With suitable product solutions for a significant part of the return process for single-use PET bottles and drinks cans, HSM is, thanks to its extensive experience, the reliable partner for the implementation and operation of efficient deposit-return systems, not only in the EU but world-wide. In addition to the crushers and perforators for the invalidation and baling presses for the compaction of PET and cans, HSM also supplies solutions to empty the drinks containers.