Prior to this, there was a smaller system in place, which wasn’t allowing the customer to achieve optimum material throughput results or expected delivery times and was ultimately stacking up unplanned maintenance and repair costs. The new system needed to be able to handle high-density extruded polystyrene material efficiently and seamlessly.
The new system recycles extruded polystyrene, a lightweight material commonly used in the construction industry. Any product waste from offcuts and returns is broken down and repurposed for further use in manufacturing processes.
Compacting XPS Waste
Fercell installed a comprehensive XPS recycling system. Waste is processed through an automated facility, with product loaded onto a conveyor for transport to a HEGER T-Rex breaker. From here, the material is reduced in size before entering a transport system which automatically transfers the product to one of two storage silos, beneath which are three HEGER Tiger 400 presses. The system is integrated with an automatic unloading system employing robots, which significantly expands operating capabilities onsite.
Any waste XPS material is shredded using the T-Rex pre-breaker, with the output extracted for further processing. Suitable for processing both small and large quantities of material, it is suitable for processing board thickness up to 300mm, efficiently reducing in size waste material ready for transporting to a storage silo in preparation for compaction.
Material is fed from the storage silos to the HEGER Tiger 400 presses. These presses offer the opportunity to save on transport and disposal costs, as well as generate revenue or savings on recycled raw materials. Operation is fully automated with an advanced PC control touch panel.
Each press line is equipped with H2O cooling jacket and H2O dowsing systems, along with hydraulic cooling for continuous operations in prevention of any overheating of product. The discharge line on each Tiger 400 press has a guillotine, which automatically cuts the block to length, which can be adjusted and pre-programmed depending on requirements. Following which there is a robot unloading system, which means the system is operated with minimal human interaction.
The installation efficiently compacts any foam waste into easy-to-handle stackable blocks for repurposing in production.
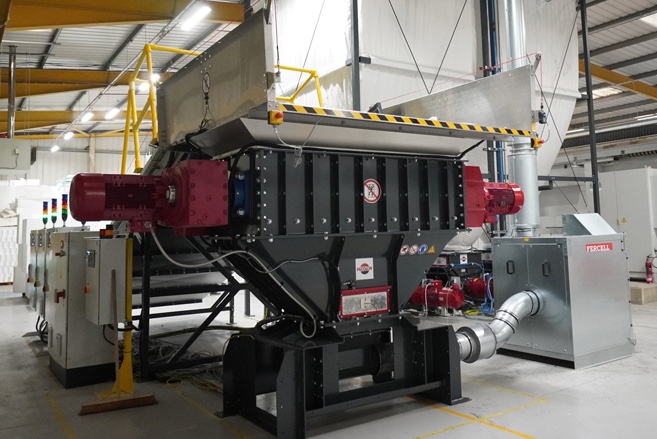
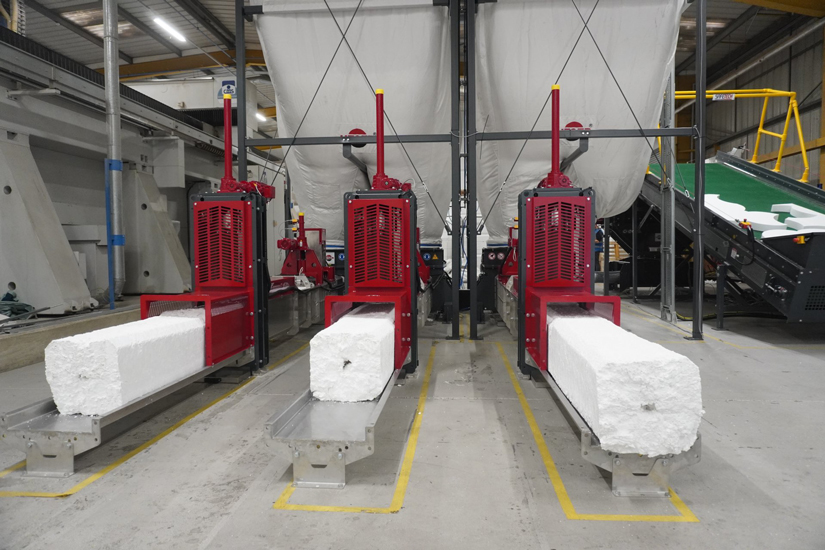