Societal pressure for more responsible clothing
From fibre producers to consumers, awareness is growing according to the “The French and recycling” survey conducted by OpinionWay in 2022, 61% of consumers say they are “more sensitive to sustainable development criteria” when buying a garment, and 58% are prepared to pay more for a responsible product. Textile reuse is gaining importance, as is the second-hand market or “upcycling”, which gives used textiles a second life. However, the production of new clothes from recycled sources remains infinitesimal. with an annual European production of 4 million tonnes of so-called TLC waste (Clothing Textiles, Household Linen, Footwear), only 1% is recycled into new clothes, the rest being transformed into insulation materials, mattress padding etc.
A growing regulatory framework
In response to environmental and societal challenges, a regulatory framework and new objectives are gradually being put in place. As part of the European Green Deal, the European Commission wants to put the textile sector at the heart of this new green strategy, with the obligation to collect textiles separately by 2025, and to make them more sustainable, repairable, reusable and – ultimately – recyclable by 2030.
A strong growth potential
The recycling steps
The collection comes from several sources: households via voluntary drop-off points, second-hand clothes shops, and some clothing manufacturers themselves. After collection comes the manual sorting phase, which will classify the textiles into two categories: reuse or recovery. All used textiles destined for re-use will be sent to second-hand clothes shops or sent abroad to be re-used. Textiles destined for recovery will then undergo preparatory sorting. It is precisely at this stage that the machines developed by Pellenc ST come into play, with the ambition of being able to process increasingly large volumes. This preparatory sorting will generate three streams: material destined for energy recovery (RDF), material destined for mechanical recycling and material destined for chemical recycling.
An industry still under construction
Current recycling rates in developed countries show that there is still room for improvement and that the industry as a whole needs to be structured. The challenge is to increase the volume of waste to create the conditions for better recycling.
Challenges still to be overcome
Ensure enough volume
All those involved in recycling are faced with the challenge of obtaining a regular supply of large quantities of used textiles. To get off the ground, the sector will need investment and support from the public authorities to ensure that textile waste can be collected massively and processed industrially.
Mass sorting
Optimising sorting is key to guaranteeing economic viability because manual sorting is not enough. Given the increase in expected volumes, automated sorting is becoming an essential solution for achieving the ambitious targets set by legislators. For this reason, operators will have to turn to equipment manufacturers who provide optical sorting and tearing solutions with industrial capacities. This is where Pellenc ST comes in, deploying an optical sorting technology that has already proved its worth in other markets, particularly waste packaging sorting.
Contaminant removal and fine sorting
The majority of textiles sent for recycling contain undesirables (zips, buttons, rivets, etc.). To extract them, the technique used is manual removal. This is a costly method because of the labour involved. So, recyclers are also looking at new technologies anticipating the increase in volumes. Two methods are being considered: mechanical (cutting textiles and then removing contaminants) and automation (sorting before tearing using cameras to spot undesirables). For the moment, mechanical processes are still under development and are therefore difficult to evaluate but optical sorters are more advanced. They can identify the nature of textiles when manual sorters can’t.They use near-infrared and visible spectrometry to separate materials according to their material and/or colour. They can even go as far as multi-material textile sorting. Today’s mechanical recycling industries are looking in particular for natural fibres such as cotton (preferably light-coloured because they are easier to recycle). As far as chemical recycling is concerned, synthetic fibres – polyester in particular – are the most sought-after and will undergo a depolymerisation process to extract virgin material.
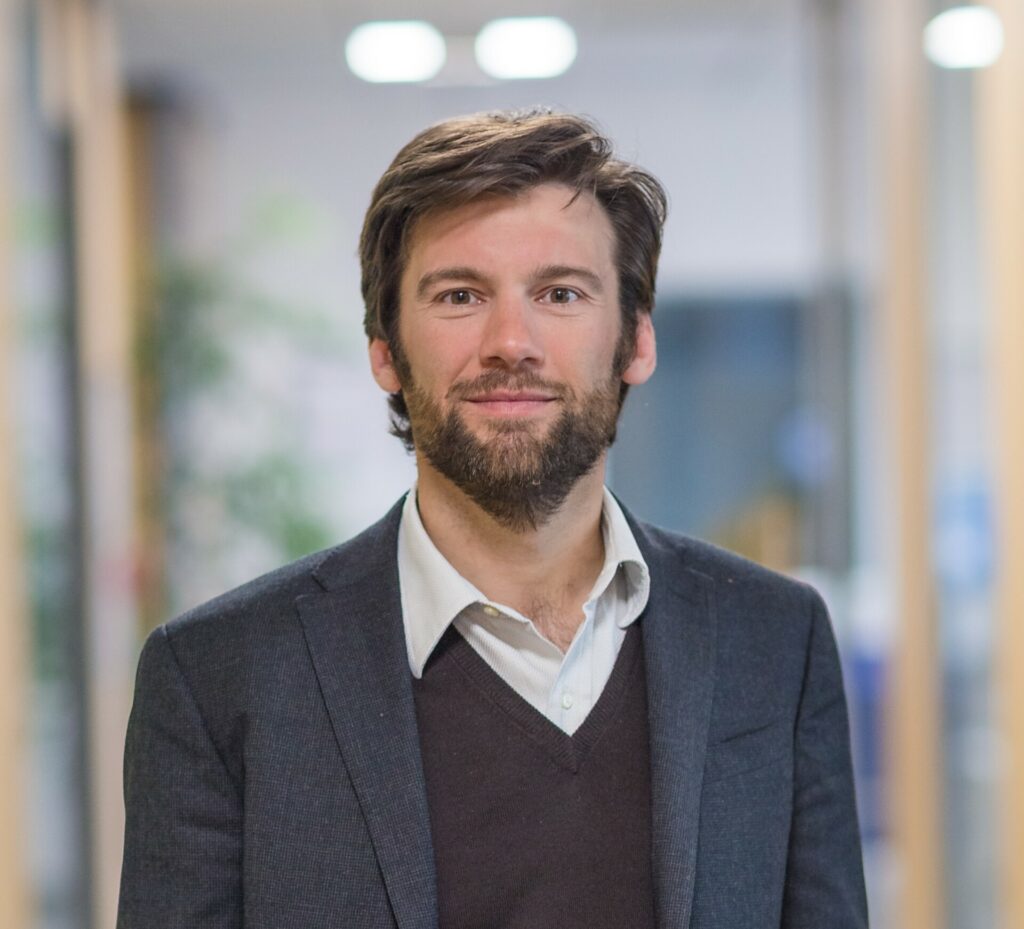
“Textile recycling is on the cusp of a veritable revolution. Automated recycling has already proved its worth, now it’s a question of speeding up its industrial implementation. Pellenc ST is supporting market players to create a sustainable and increasingly circular economy.”
Jean Henin
But promising pilot projects with Pellenc ST
The first automated sorting line in France
International technology group ANDRITZ entered an ambitious partnership with Pellenc ST and Nouvelles Fibres Textiles to set up the very first industrial-scale automatic textile sorting line in France combining automated sorting and recycling technology.
The new textile sorting line being built is the first to combine Pellenc ST’s automated sorting technologies with ANDRITZ’s recycling technologies. It will process post-consumer textile wastes to produce recycled fibre engineered for the spinning, nonwoven and composite industries. Starting operations in mid-2023, it will serve as a production line for Nouvelles Fibres Textiles, as an R&D line for the three partners, and as a test and demonstration centre for their customers.The aim is to demonstrate the viability of the industrial process and to build a second plant by 2025 capable of processing 25,000 tons of used textiles a year.
A pioneering project in Spain
In March 2023, Insertega, a Spanish specialist in the collection and sorting of textiles, chose Pellenc ST as part of a pioneering operation to automate its production site. Thanks to spectroscopy, the sorting equipment developed by Pellenc ST separates natural fibres from synthetic ones and sorts them by colour. More specifically, Pellenc ST’s Mistral+ CONNECT DVI optical separator was installed, to separate three textile fractions (pure cotton, polyester, and a mixture of both).