According to the UN’s Global E-scrap Monitor 20201, global E-scrap will reach 74 million metric tons (Mt) by 2030, making it the fastest growing waste stream in the world. E-scrap comprises a variety of discarded electronic products, including TVs, PCs, mobile phones, household appliances such as washing machines, freezers, vacuum cleaners and even some children’s toys. It typically contains a complex mix of materials, some of which are hazardous and must therefore be managed carefully. Furthermore, E-scrap often contains a significant amount of valuable and scarce raw materials, such as stainless steel, aluminum, gold, silver, copper, brass, indium and platinum.
Europe is the third-largest generator of E-scrap behind China and North and South America and has the highest collection and recycling rates at 42.5%2. There are two directives governing the management of E-scrap in the EU: the WEEE (Waste from Electrical and Electronic Equipment) Directive and the RoHS (Restriction of Hazardous Substances) Directive, both of which were introduced in 2003. The WEEE Directive aims to contribute to sustainable production and consumption by firstly preventing E-scrap and then by stimulating the re-use, recycling and recovery of secondary valuable raw materials. The RoHS Directive sets restrictions on European manufacturers as to the material content of new electronic equipment they place on the market in order to prevent the risks posed to human health and the environment. For E-scrap, this means the safe removal of any harmful substances.
Pre-shredding prior to sensor-based sorting
In addition to adhering to legislation, the overall goal of E-scrap processors is to cost-effectively recover valuable secondary raw materials which are as pure as possible and which would otherwise be sent to landfill or poorly processed.
The treatment of E-scrap can vary enormously according to the type of material and the technology that is used. Some treatment facilities use large-scale shredding technologies while others dismantle the material manually or use automation or, in some cases, a combination of both.
Shredding E-scrap prior to sorting with any sensor-based sorting technology is an essential stage in the process. Using pre-shredding, hammer mills or vertical shredders, valuable components such as printed circuit boards (PCBs), cables and valuable metals can be recovered, and batteries, capacitors and other harmful materials can be safely removed.
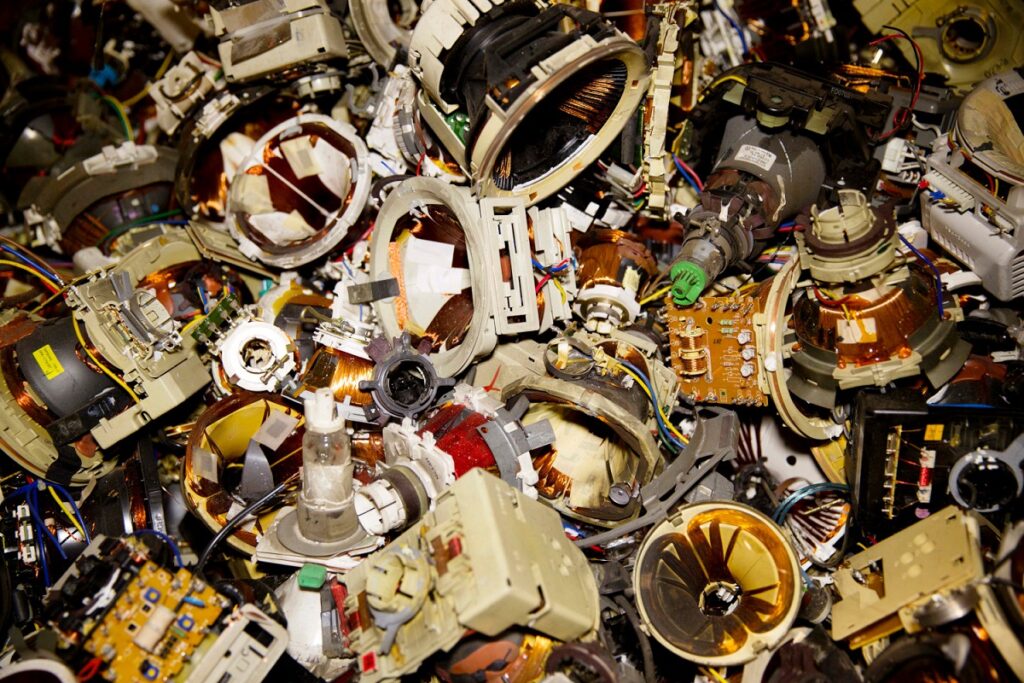
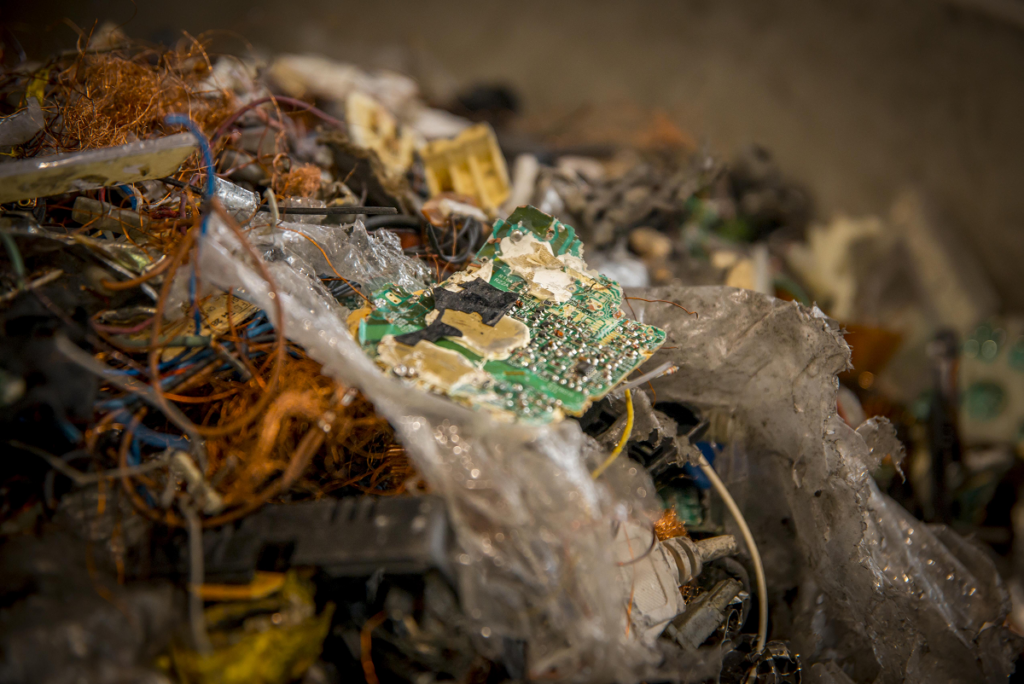
Using flexible sensor-based sorting technology to target different materials
There is no ‘one size fits all’ solution when it comes to designing an E-scrap recycling plant but typically a large-scale plant includes a first step of pre-shredding and the manual removal of hazardous material such as batteries and easy-to-pick valuables like large PCBs. After this, a second shredding step is normally used to downsize the material to make it suitable for further sorting. A magnet removes the ferrous fraction and then the material is screened to ensure more efficient sensor-based sorting later in the process. Once pre-shredding has taken place, there are a number of different flexible sensor-based sorting solutions that can increase the product yield, generate material fractions of significantly increased purity and detect hazardous substances.
- Targeting aluminum – In a typical plant design, an eddy current separator is used to remove the non-ferrous metals which consist of a mix of aluminum, copper, brass and PCBs (Zorba). Once the non-ferrous metals have been removed, an X-TRACT™ unit can then be introduced to achieve extremely accurate separation of high purity aluminum from heavy metals. X-TRACT™ uses X-ray technology to detect materials based on their density. The software-based solution can guarantee premium remelt quality recycled aluminum by ejecting the heavy metal contaminants such as magnesium.
- Targeting valuable heavy non-ferrous metals – Once the X-TRACT™ has separated the aluminum from heavy metals, the remaining mix of heavy non-ferrous metals can then be further sorted using a COMBISENSE™ unit. COMBISENSE™ sorts out different metals – such as copper, brass, grey metals and PCBs – by color and electromagnetic properties. By passing the material through a series of further sorting steps using the COMBISENSE™ unit it is possible to significantly increase the purity of the different target heavy non-ferrous metals end products, such as PCBs and copper. The metal content, color, shape and size of each passing object is identified, and the targeted fractions are recovered.
- Targeting metals from non-metals – After the infeed material has passed through an eddy current separator, the dropped material consists of plastics and other non-metals, but also includes the metals that are not removed by the eddy current separator, such as stainless steel, copper wires, compounds of plastic and metals, and some PCB parts. At this stage, our FINDER unit, which uses electromagnetic fields to recognize different metals, can be used to recover all metals from the non-metals. This minimizes the loss of valuables into the plastics and also ensures the quality of the plastic end products at a later stage. The FINDER unit is extremely flexible and, depending on the customer’s target fractions, can be used to distinguish between stainless steel and copper wire, and produce a clean non-metal fraction.
- Targeting valuable plastics – The sorting and recovery of plastics from E-scrap can be done in various ways depending on what fractions are required and the volumes to be processed. Different combinations of sensors can be used to identify and separate different plastics, transforming the material into reusable granules. E-scrap contains hazardous substances or persistent organic pollutants (POPs), such as brominated flame retardants, which must not be reused or recycled. Our X-TRACT technology can be used to remove these materials and our AUTOSORT NIR technology can be used to remove the remaining visible polymers in the <1000ppm brominated content. The non-visible polymers can then be dried and sorted by polymer type using NIR spectroscopy into individual polymer groups for re-sale.
Latest developments in plant design
The typical E-scrap plant design described above is well proven and widely used, but in recent years we have worked with customers to introduce some new and innovative alternative applications of our technology.
For example, we recently installed a COMBISENSE™ unit which uses a visual spectrometer sensor to remove visible copper, such as wire bundles attached to iron or small engines. When incorporated after magnetic separation, this solution makes the ferrous fraction much cleaner and far more likely to pass visual inspections at the steel mill.
Instead of using an eddy current separator first directly after the magnet, some of our customers have used our FINDER™ unit to recover all the metals, including the non-ferrous metals such as aluminum and copper. This is achieved using a Laser Object Detection (LOD) sensor within the FINDER™ unit. The bulk volume of the material – the plastics – is therefore removed upfront which means there is less material to go through the later sorting steps. Consequently, very few metals are lost, it is much easier to upgrade the metals and less footprint is required for equipment as only smaller sorting units are needed.
Finally, another new development implemented by some customers is sorting out PCBs before they enter the eddy current separator using either our COMBISENSE™ unit which uses color and electromagnetic sensors, or our AUTOSORT™ unit which uses near-infrared technology. By recovering the PCBs in just one step at this stage, there is no need to sort them from both the non-ferrous metals and the stainless steel and copper fraction. This potentially saves a sorting step and again makes the later sorting steps easier and more efficient.
Greater separation of E-scrap is a means for processors to gain a more robust trading position in the global marketplace. As sensor-based sorting solutions can be incorporated at different stages in the process, they are very flexible and can be used to target different valuable monofractions. Today, many of our customers are using our technology to target copper and other precious metals due to their high market value.
Looking to the future, we expect to see more and more forward-thinking E-scrap processors invest in flexible sensor-based sorting technology as a means of creating more monofractions to meet industry demand. This will put them in a much stronger position to shift stock, grow their customer base and, ultimately, increase their profit margins as the recovered monofractions can be sold at much higher prices and often traded locally, helping to close the loop on metals recycling.