The ALB which provides significant savings to sites producing mid to large volumes of cardboard has seen success across Europe being installed across thousands of retailers, including the likes of ALDI. This model is also installed with manufacturers, among many other sectors.
Typical savings from the ALB’s patented cart feeding system are around 4,000 hours per site, per annum, or around £60,000 per annum in labor cost.
How the system works
The machine is fed from carts that are equivalent volume to an 1100 liter bin. These are strategically placed around the site at the point of production and once full, rather than unloading the cardboard manually into a press chamber, the cart is pushed into the side of the machine which then feeds the material through into the chamber for baling.
This machine also allows for feeding of over-sized cardboard that can’t fit in the carts, through the standard door to the front of the machine in case of any one-off large boxes (for example, a box which contained a bicycle).
This machine also allows for feeding of over-sized cardboard that can’t fit in the carts, through the standard door to the front of the machine in case of any one-off large boxes (for example, a box which contained a bicycle).
How does it compare to older, standard automated systems?
The ALB provides an automated baling solution, within a 2047mm wide by 2173mm (max) floor space, where any other automated solution would require 3-4 x more space.
A key difference with the ALB compared to significantly larger, competitor models are that they are generally positioned outside exposed to the elements. The models then suffer greater levels of depreciation, reduced returns on investment from higher maintenance costs and an earlier requirement to replace.
Operatives then spend time breaking down cardboard boxes to flat pack the material to make the best use of the bin before walking across the site to where the baler is usually placed, which typically again isn’t anywhere convenient as most businesses do not want to take up valuable floor space. This means that staff spend excessive time flat packing material and walking back and forth to remotely placed machines to make the best use of their time.
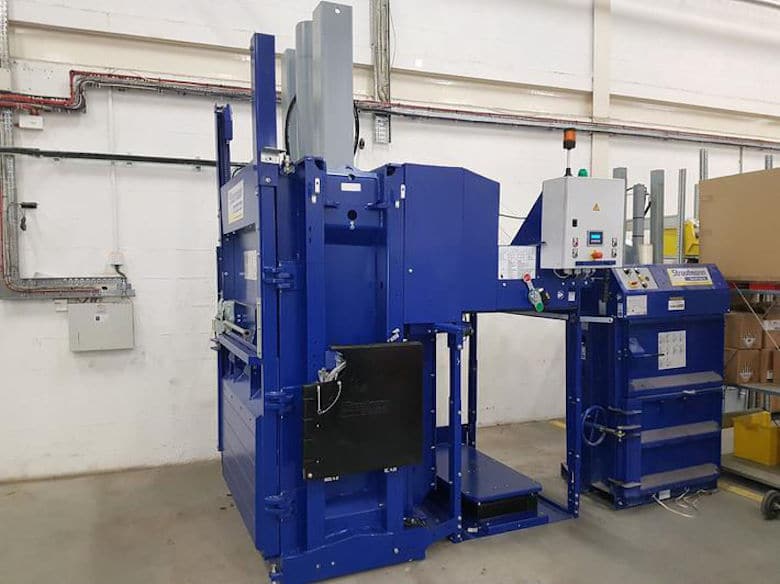
Equally, larger machines require access to all sides of the baler for feeding wire through, as well as for maintenance access and bale ejection. The AutoLoad Baler does not have this requirement, can be placed within the small footprint (2047 x 2173mm), in corners, odd spots of free space, under racking and so on.
At many fulfillment Centres across the UK, the ALB is close to the point of production, for maximum benefit. Forklifts then move the ejected bales to the recycling compounds which are typically outside which ensures the best use of all space.
Saving labor, space, time, manual handling requirements and creating a more positive baling operation for those businesses like Hilti & ALDI who invest in this model.