Every year, approximately 300 million tons of plastic are produced, and it is estimated that, in five years, by 2025, there could be almost all that amount spilled into the oceans (250 million tons). The figures are so atrocious that they are difficult to imagine or assimilate. However, there are also data that instill hope. For example, the fact that since 1998 Spain has recycled about 14 million tons of containers. Or that, in 2018, it was able to recycle 78.8% of domestic containers, the highest figure ever registered and that almost reaches the one required by the European 2030 Agenda (80%).
A two-decade journey that must continue and in which PICVISA participates and progresses with determination, designing, manufacturing and supplying optic separation solutions for material classification, waste recovery, and valuation. PICVISA has been in the recycling sector for more than 15 years providing separation equipment, developing its service-oriented activity with professionalism, innovation, efficiency, and sustainability. The company’s equipment allows recycling plants to work with the latest technology, which means having greater profitability, less rejection, reduced impurities and optimized time. But what are these machines that have improved the recycling process?
ECOGLASS y ECOPACK: optical separators for glass and plastic
The final consumer knows this type of waste as those belonging to the green container (glass) and yellow container (plastic). The optical separators ECOGLASS and ECOPACK allow you to automatically classify and separate different types of materials, by composition (NIR), color (VIS) and/or shape (this, thanks to deep learning technology).
ECOGLASS models work in glass recovery and cleaning processes in different flows. They are designed according to a versatile concept that is easily adapted to different processes where the material is crushed and requires separating or cleaning according to color and shape criteria. In addition, they can also detect lead contents in glass and ferrous and non-ferrous metals.
One of the most recent projects that has opted for the PICVISA team is the new glass recovery line at the Centro Integral de Valoración de Residuos in Maresme (Barcelona), in which the ECOGLASS SG1500F optical separator is the angular part and it is expected to recycle about 4,500 tons of glass per year.
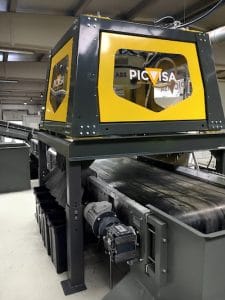
As for ECOPACK equipment (EP-1000, EP-1500, EP-2000, EP-2500 and EP-3000), these are designed to work on acceleration belts from 1000 mm to 3000 mm with different separation options (Double Bar or MultiTrack). Thanks to the flexibility of the multispectral vision, ECOPACK can be configured to make quick changes in the classification of new materials that need to be separated in the recycling of plastic containers, such as PET, PE, PP, PS or for the tetra pack, and even for paper and cardboard.
These are systems in constant evolution. Without going any further, during 2019, PICVISA introduced several improvements in them -in their sensors, software, maintenance, and user control- which allowed a further optimization of the process.
ECOPICK and BRAIN by PICVISA: Artificial Intelligence and more Deep Learning
Applying its innovative value, PICVISA’s latest machinery contribution to the recycling sector is ECOPICK, a “Delta” robot with Artificial Intelligence capable of recognizing and classifying a wide variety of objects on a conveyor belt, replacing the -until now- manual labor. Through artificial vision, ECOPICK carries out the material control: it scans them, identifies them among the other waste and separates them for later recycling. In short, automation gives this robotic arm efficiency in its selection, increases the recovery of the remains and encourages the circular economy.
Both ECOPICK and the ECOGLASS and ECOPACK optical separators are a reality thanks to PICVISA’s commitment to advanced technologies such as Deep Learning, the algorithm used as Artificial Intelligence’s learning method. In fact, the company has Brain by PICVISA, a complement for ECOGLASS and ECOPACK based on Deep Learning that allows choosing between six different applications, each one of them focused on solving a different problem.
The effectiveness of all these solutions can be checked at the PICVISA Test Center in Calaf (Barcelona), an 800 m2 plant where you can confirm the performance and production of PICVISA products in real operating conditions, and witness first-hand how the company has revolutionized and continues to make the recycling sector evolve.