St. Nazaire harbour (Brittany) needed a very powerful material handling machine at short notice. The ATLAS 57 t 520 MH material handling machine was able to satisfy the high requirements and was delivered on time. The on-site task is to load scrap metal onto ships. These operations must be carried out quickly, smoothly and economically all year round. A sophisticated design and the Deutz six-cylinder engine with 7.8 litre cubic capacity and 230 kW/313 hp output and EU Stage V constitute the solid foundation for this.
High handling capacity
The ATLAS material handling machine has been specially designed for loading and unloading ships. The cab can be extended 3 m high and 2.5 m to the front. This ensures a clear overview, excellent all-round visibility and, most importantly, the field of vision required to see into the ship’s hold. A special boom has been designed to provide an optimum grip in the hold. The main arm features a slight bend in the centre, giving it a somewhat banana-like appearance. This makes it possible to reach over the land side of the vessel and onto what is on the seaward side of the vessel, even at high tide and when the vessel is afloat. The maximum reach is just under 20 metres. The slewing mechanism is controlled by two swivelling gears and the slewing brake is equipped with an automatic multi-disc parking brake. The upper carriage reaches a speed of 5.2 rotations per minute. That’s more than speedy considering the loads that are moved here. The positive effect of this is that it is possible to work with a high handling capacity and low costs. An overload warning device and pipe breakage protection for the lifting and stick cylinders enhance safety.
A friendly cab
It goes without saying that the cab is equipped with air conditioning as standard. A rear-view camera and a side view camera on the right are also included as standard. What is particularly important is that the cab is quiet. The design ensures that only 70 dB(A) of noise is measured in the cab. A high-contrast display, which can be controlled digitally or by direct command, a comfortable driver’s seat plus the best view of the working area transform the cab into a space for well-being.
Made from a single mould
The undercarriage is equipped with special heavy-duty excavator axles. The steering axle features automatic oscillating axle blocking. The outriggers and cab entrance have been redesigned. The guiding principle was greater safety and easier access for the driver. The ATLAS E851 5 shell gripper is used here in St. Nazaire. It can hold 700 litres of scrap metal with a single handle. “Thanks to the fact that we at ATLAS are in a position to respond in detail and quickly to customer requests, both when it comes to design as well as production, means that the result is a machine consistently customised from a single mould in terms of quality. This offers economic advantages and makes us unique on the market,” explains Brahim Stitou, Managing Director of ATLAS GmbH.
First ATLAS 520MH in France – economical
The ATLAS 520MH is the first material handling machine on this scale that ATLAS has exported to France. Pemservices, the distributor, delivered it to Terminal Grand Quest TGO in Montoir de Bretagne. ATLAS specialists from Ganderkesee were on site to help with familiarisation. They also trained the drivers of the ATLAS machine. A smaller model of the ATLAS 350MH has already been in use there for years. Work is carried out at Saint Nazaire. Close to the large shipyard responsible for building the gigantic cruise ships. The low cost per tonne handled was an important reason why TGO opted for the ATLAS. Rapid work and low servicing provide a good basis for cost-effective work. This is what the ATLAS 520MH delivers.
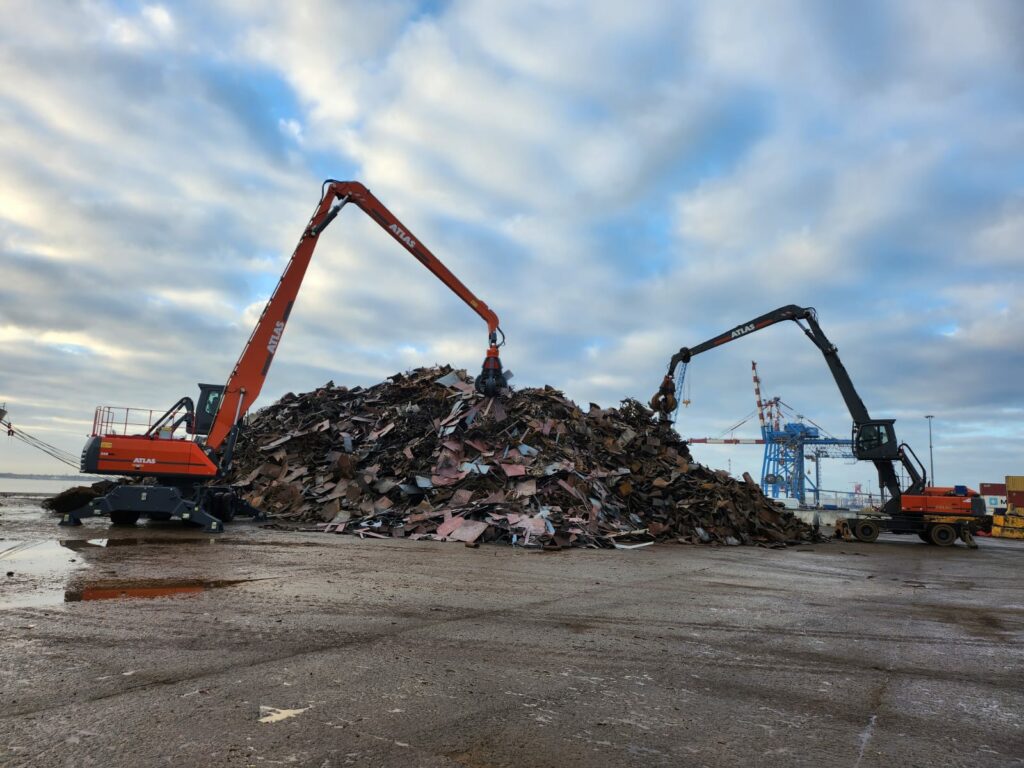