However, its durability means that it does not break down easily when it is discarded, so that plastic waste is building up in landfills and flooding our oceans. Responsible use of plastic, and its re-introduction into the production cycle at the end of its life through recycling, have become a necessity in order to address this issue effectively.
STADLER is constantly searching for ways to maximize the efficiency of the recycling process and the quality of the output, investing every year 5% of its revenues in Research and development. It saw an opportunity to improve the process for plastic bottles and developed a specific solution to remove the labels.
Rok Mežič, Head of R&D Slovenia, who led the development process of this machine, explains: “Bottles make up a large proportion of plastic waste, and they present a particular issue to the recycling industry: the labels are made of a different polymer and color than the bottles, which negatively affects the accuracy of the sorting process. At STADLER we saw the need to address this issue, and developed a Delabeler to remove the labels automatically at the beginning of the process in order to achieve high-quality sorting and good purity rates.”
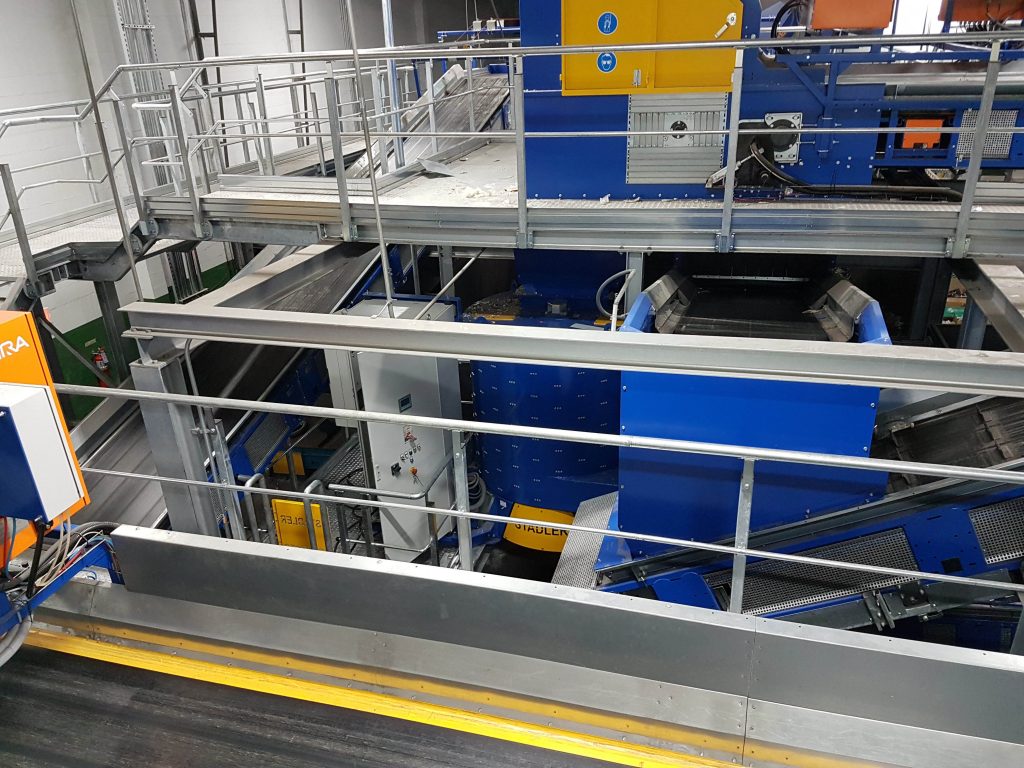
The powerful STADLER Delabeler removes labels from bottles of all types, achieving a quality standard of up to 80 percent of labels removed. It processes a mass flow of up to nine tons per hour – depending on the particle size and material composition.
The STADLER Delabeler’s robust overall construction and extremely high resistance to impurities and troubling materials result in excellent durability and mean that it will deliver consistently high performance throughout its long life cycle. It is equipped with blades made from high-tensile steel that is attached to the rotor at one end so that they can oscillate freely, and to the housing´s inner wall at the other. The machine’s quality features include the rotor with rotating arms, the belt drive with tensioning pulley, the quality motor and gearbox from SEW, the maintenance doors with safety lock, and the electrical cabinet with frequency inverter and adjustable rotor speed – from 20 to 60 Hz (80 to 240 rpm).
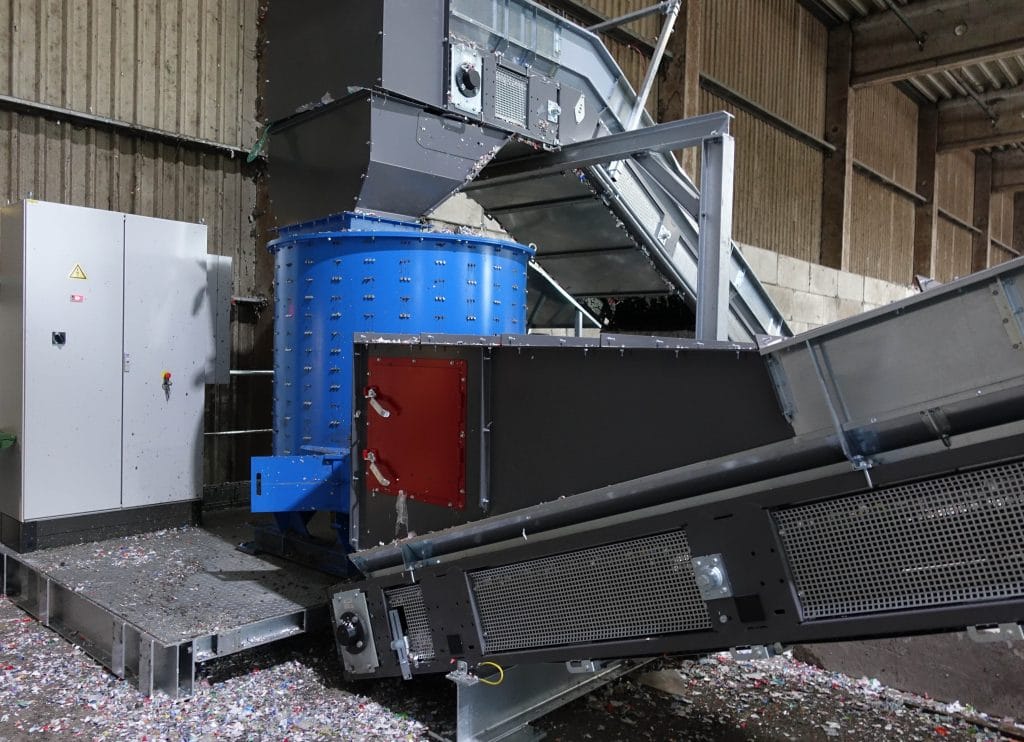
Testing is a key element of STADLER’s product development process. Trying out the machine in different recycling plants enables the company to integrate feedback from the customers and identify any areas for improvement or tweaks to optimize its performance. The STADLER Delabeler was tested in the United States, Romania, and in two recycling plants in Germany. The customers involved were impressed by the difference made by the Delabeler to their process – so much so that they all purchased the machine once the tests were completed.
STADLER is always anticipating the evolution of the recycling industry, developing products to meet new market needs and constantly improving its processes to address its clients’ changing requirements – and in doing so, contributes to addressing the global issue of plastic waste.