The MAS portfolio’s core is a conical, co-rotating twin-screw extruder, complemented by a continuous melt filtration system and a drying and cleaning machine for waterless pre-treated plastic fractions.
MAS emphasizes gentle material handling, precise process control, and energy efficiency.
Conical co-rotating twin-screw extruder – Designed for recycling processes
The MAS twin-screw extruder features a conical, co-rotating screw design specifically developed for recycling applications. Unlike conventional parallel screw extruders, the conical geometry allows for a more compact layout and high specific torque transmission.
The screw geometry is specifically designed to ensure thorough melt homogenization and efficient degassing under varying processing conditions. This is especially important when dealing with moisture-sensitive feedstocks or materials with inconsistent bulk densities, such as post-consumer PET or polyolefins.
Key process parameters such as temperature profiles, screw speed, and pressure can be precisely controlled. PET processing for bottle-to-bottle or tray-to-tray applications allows recyclers to maintain critical quality factors such as intrinsic viscosity (IV), acetaldehyde (AA) levels, and color stability — essential for meeting EFSA or FDA regulatory standards.
Continuous melt filtration with CDF
MAS’s Continuous Disc Filter (CDF) enables high-throughput, continuous melt filtration. The rotating disc-based design reliably removes contaminants like paper, wood, or unmelted polymer residues without interrupting extrusion.
Advantages of intelligent, adaptive CDF include:
- Stable pressure conditions during filtration
- Automated discharge of solid residues
- Long service life and low maintenance
The system is especially well-suited for recycling streams with variable input quality, ensuring consistent melt purity and improved product quality downstream.
DRD System: Water-free drying and cleaning of plastic fractions
The DRD (Double Rotor Disc) system is MAS’s solution for dry mechanical cleaning of pre-shredded plastic waste. Unlike traditional wet washing systems, DRD combines friction, airflow, and rotor agitation to clean and dry material in a single process, without water.
This approach is efficient for lightweight films, rigid plastics, or lightly contaminated post-consumer fractions. It significantly reduces water and energy consumption while eliminating complex wastewater treatment needs.
Extended applications: Biopolymers
MAS technologies are not limited to conventional plastics. Biopolymers typically require low-shear, temperature-controlled processing. The MAS extruder design ensures gentle material handling, preserving molecular structure and processability properties.
Conclusion
MAS Austria provides technically advanced systems for plastics recycling and compounding. The modular combination of conical twin-screw extrusion, continuous melt filtration, and dry cleaning enables customized line configurations tailored to specific application requirements.
With precise control over the recycling process, innovative tools, high energy efficiency, and a strong focus on material quality, MAS offers reliable technology for implementing industrial-scale circular economy solutions in mechanical recycling, biopolymer processing, or chemical recycling applications.
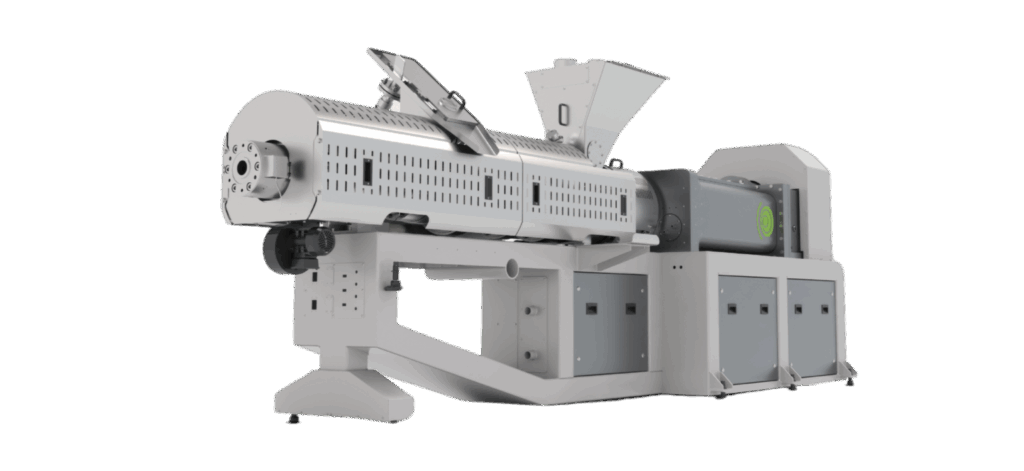