Case Study and Implemented Project
“Choose your cleaning process” this is the project’s guiding principle for offering clients unparalleled technology flexibility. Designed as the washing lines of tomorrow, this system is engineered to handle 2,5 tons per hour of post-consumer plastic film, ensuring efficient and customizable cleaning solutions tailored to different clients’ needs.
The design of the plant has been guided by principles of sustainability, aiming to minimize:
- CO2 Emissions: by selecting the washing processes, carbon dioxide emissions are reduced, contributing to a lower carbon footprint of the recycled plastic lifecycle.
- Water Usage: advanced technologies allow for efficient water use, reducing consumption and improving water resource management.
- Plant Operating Costs: operational efficiency and the ability to tailor the process to the specific needs of the material being processed, help lower operational costs, making plastic recycling economically sustainable.
This innovative plant supplied to an important Multinational Company offers various washing modes, adaptable to the specific needs of the material being processed:
- Dry Cleaning: This type of cleaning is particularly suitable for (a) dry, relatively clean materials free from sinking bodies, or (b) preparing feedstock for chemical recycling, especially with dry mixed polyolefin. It offers the significant advantage of completely eliminate water consumption, thereby making the process more sustainable.
Applications close-up – The dry friction cleaning is performed by a dry friction washer with customizable settings. This allows a dynamic approach for the end user, who can adjust the machine based on the characteristics of the material being treated. - Cold Washing: Used for selected, moist material with medium-high contamination and almost zero oil or grease content. This mode is effective in treating materials that do not require special washing process to remove hazardous contaminants.
Applications close-up – The cold washing is the typical plastic cleaning process. Friction washers and washing tanks allow the separation of the heavy bodies and the removal of not hazardous contamination from the plastic. - Hot Washing – Rinsing: Designed for selected material with food grade future application. Hot washing ensures a deep cleaning, necessary for removing the toughest impurities, thus guaranteeing high-quality material for subsequent recycling.
Applications close-up – Tecnofer’s plastic film hot washing system is designed to process material combining a long residence time in a hot chemical solution with high grade friction effect. The result of this process is the removal of hazardous contaminants, producing highest quality plastic grade. - Drying System: Tecnofer approaches the drying of the flexible plastic through mechanical and (when necessary) thermal drying.
Applications close-up – Mechanical drying is performed by a high-performance squeezer, followed by thermal drying using a special fluid bed system. The combination of these two units reduces humidity from 50% to 2% with an energy consumption of only 0.17 kW/kg. This unparalleled performance is the result of decades of research and development aimed at maximizing plant efficiency and client satisfaction.
The described washing line project represents a significant step towards more efficient and sustainable plastic recycling process. Thanks to the flexibility of washing modes and the focus on reducing environmental impacts, this kind of washing line offers advanced solutions to the current challenges of plastic waste recycling. By adopting these technologies, it is possible not only to improve the quality of recycled material but also to contribute to environmental protection and the promotion of more responsible industrial practices.
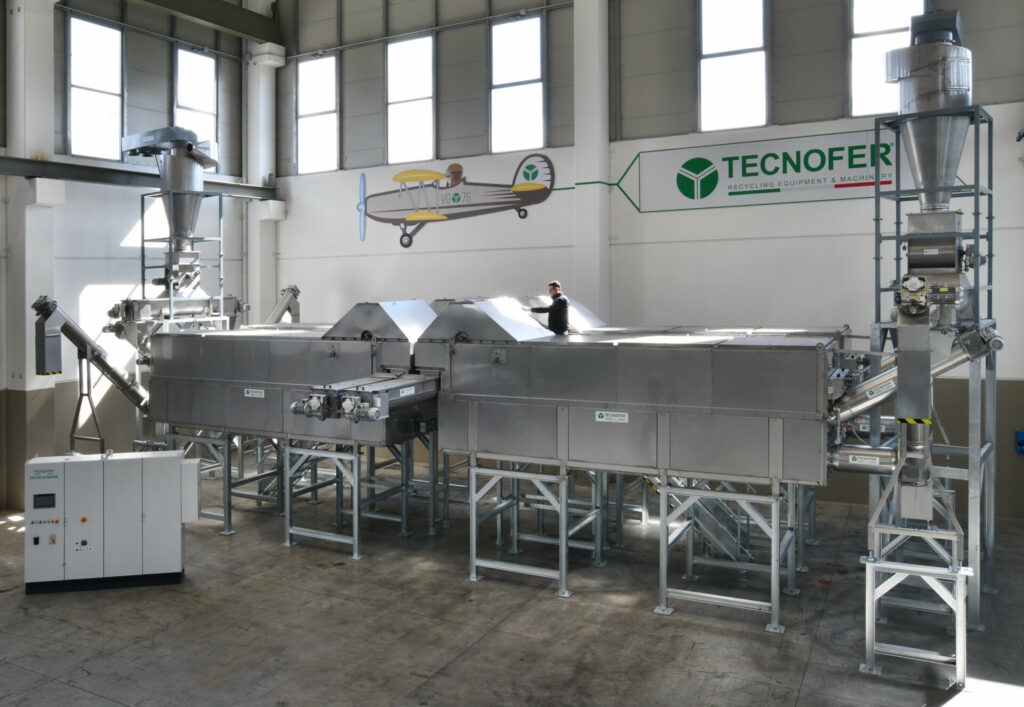