Plastic mixtures that consist of many different plastics are usually worthless. Only clean and pure fractions can be reused for high-grade new products.
1. Typical composition of mixed plastics
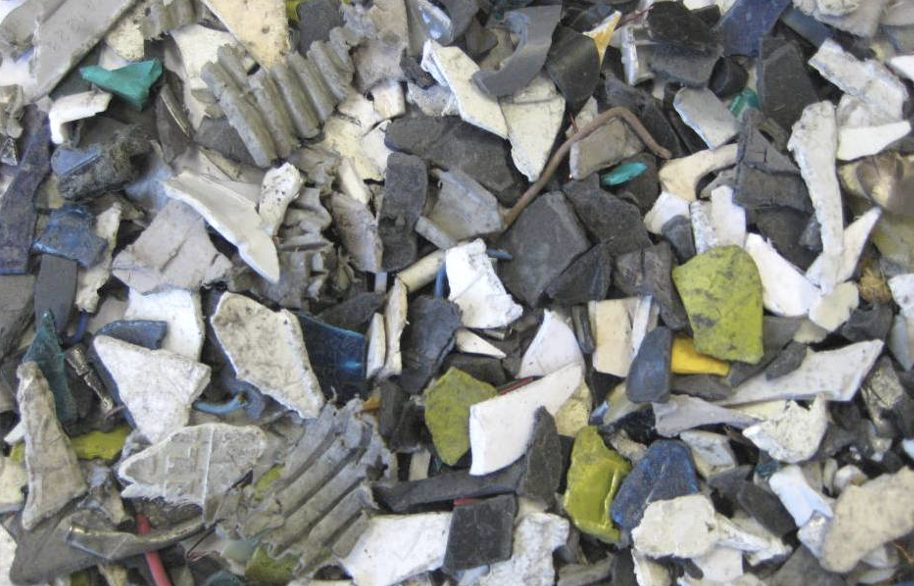
Mixed plastics often remain after valuable metal fractions have been separated. The volume share of plastics in electronic scrap, amounts for example to 15% of the total volume. In relation to the total quantity of electronic scrap materials recycled in Europe, this already amounts to several 100,000 tonnes per year.
Due to the mechanical processing technologies used for electronic scrap, plastic fractions are then very often interspersed with all kinds of undesirable foreign materials such as wood, glass, rubber, residual metals and others.
The largest problem with these mixed plastics is therefore the complexity and composition as well as the impurities, which hamper the processing of such fractions. Intensive evaluation has shown that, for example, more than 60 different plastics are found in electronic scrap, which can be more or less contaminated with additives, fillers, flame retardants, etc. A processing technology to achieve clean plastics must therefore be able to deal not only with the undesirable foreign substances, but also with a large number of different polymers.
Figure 1 below shows that ABS, PS and PP, for example, make up the majority of plastic materials. The other plastics described above account for less than half.
It therefore makes sense to concentrate on the significant amounts of plastics during reprocessing. Recovery of plastics that are present in the low single-digit percentages is unlikely to be worthwhile.
2. Processing technologies
The “bulk plastics” in electronic scrap, for example, are PS, ABS and PP. These materials lie fortunately in density ranges that are accessible for the use separation processes based on density, such as the float-sink separation technique. This is a particularly economical process, which – assuming fractions are of appropriate density – results in concentrated plastic that can then be further processed by dry electrostatic processes.
For example, it is easy to separate polyolefins from a plastic mixture using a simple water separation stage. PS and ABS can be separated using water with a higher density (e.g. a salt solution). A salt solution in water then enables production of highly concentrated PP/PE and PS/ABS mixtures.
In particular, undesirable flame-retardant plastics go through this process into the heavy residual fraction, where PVC, glass, residual metals and other undesirable substances also end up. This residual fraction is thermally recycled, for example.
3. Processing of PS-ABS mixtures
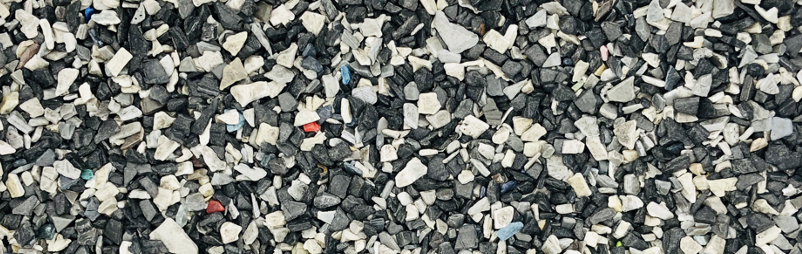
PS and ABS are the “favourites” in terms of added value and yield – but only if these materials are available in high purity. ABS and PS in a non-separated mixed fraction can only be processed with great difficulty with the aid of expensive additives.
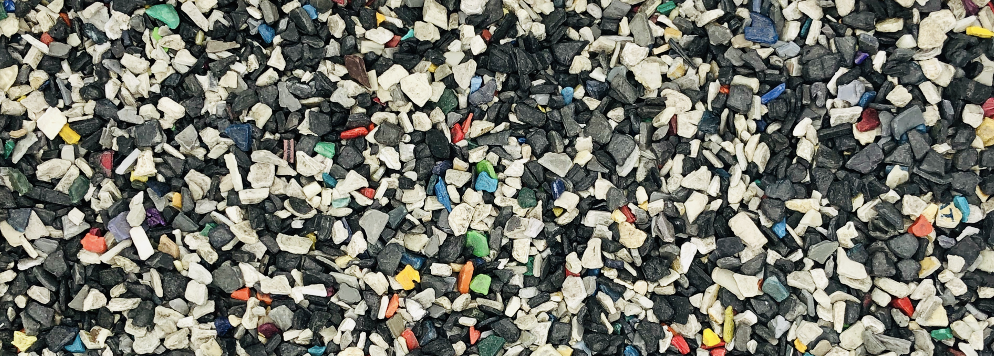
While optical sorting methods using infrared spectroscopy, or other methods, are still in the starting blocks due to the predominantly black colour of plastic mixtures, this type of separation has not been a problem for electrostatic separation technology, already for decades. Electrostatic separators can easily separate black ABS-PS mixtures into pure fractions.
4. Electrostatic plastic-from-plastic separation
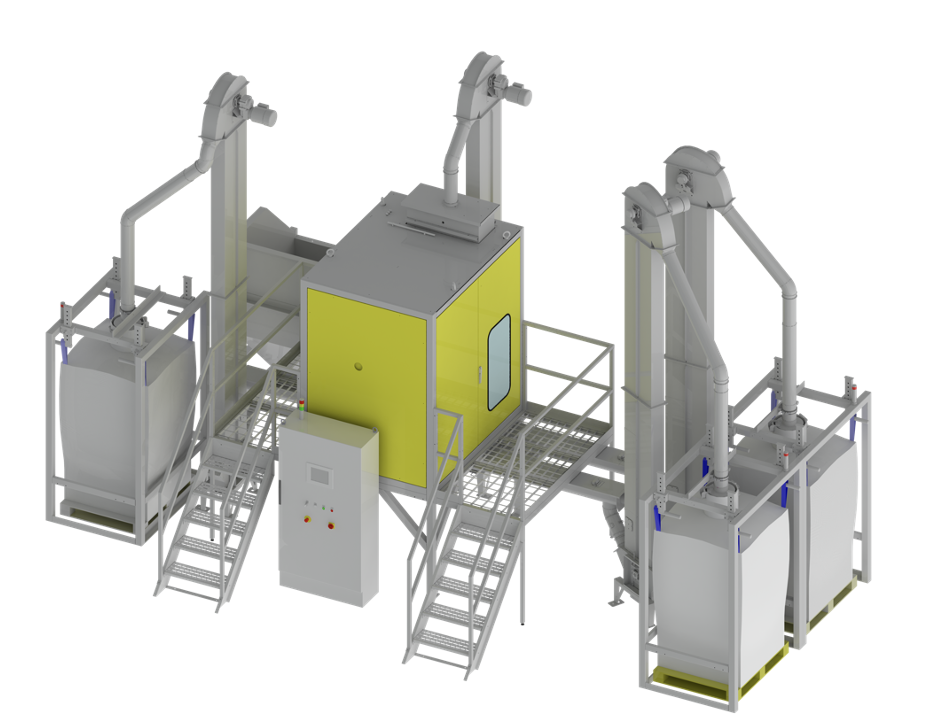
ABS and PS essentially differ in their electrostatic chargeability. When one of these two plastics in a mixture of the two is selectively charged in an electrostatic separator, the ABS becomes positively charged and the PS negatively, due to different “dielectric constants”. As the charging is highly selective, subsequent separation in a high-voltage field results in very good purity of both products.
The prerequisite for your successful separation is that the ABS-PS mixture has the correct particle size of < 10 mm and is dust-free. The most important criterion, however, is the moisture content of the material. Only dry ground material can be sufficiently electrostatically charged.
5. Electrostatic separators in practice
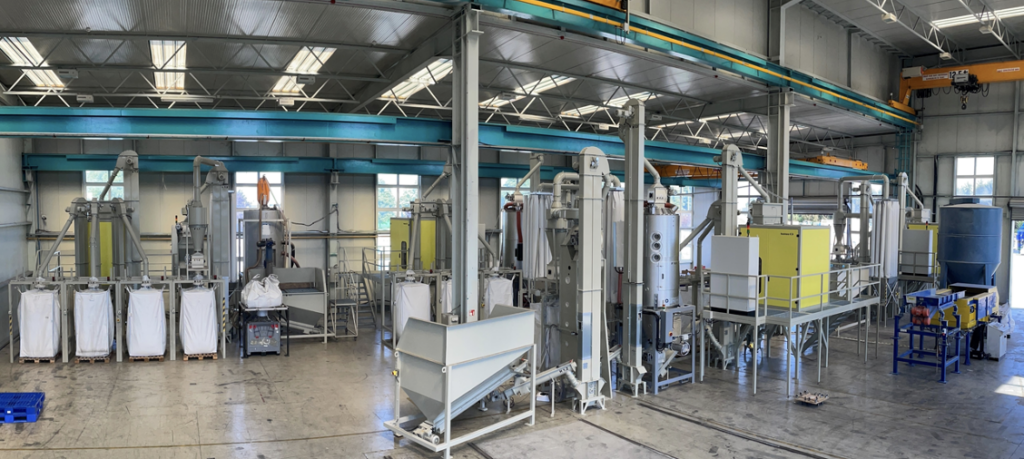
Electrostatic separators for plastic-from-plastic separation are supplied as complete systems including a charging unit and high-voltage electrode system for material separation. For technological reasons, throughputs achievable with one unit are approx. 1,000 kg/h. Connection of several units in parallel enables larger amounts of material to be easily separated.
In the separation of ABS-PS mixtures, for example, the ABS is separated as a high‑purity fraction in a first separation stage. The PS is also recovered as a pure fraction in a subsequent second separation stage. Due to the special electrostatic charging unit, it is also possible to simultaneously separate a filled polypropylene fraction, as it is in the same density range as ABS and PS.
6. Foreign substances in a good product
When processing PS and ABS from car shredders or electronic scrap, it is found that after passing through the various separation stages, there are still small amounts of unwanted foreign substances such as wood or rubber in the ground material. It is essential to separate these substances to ensure subsequent processing into high‑grade compounds or even directly into products. While wood can be separated by melt filtration, rubber or other elastomer fractions pose more serious problems. Especially at high pressure in an extruder, these elastomers are pressed through the melt filters and lead to a reduction in the quality of the finished product.
6.1 Wood separation
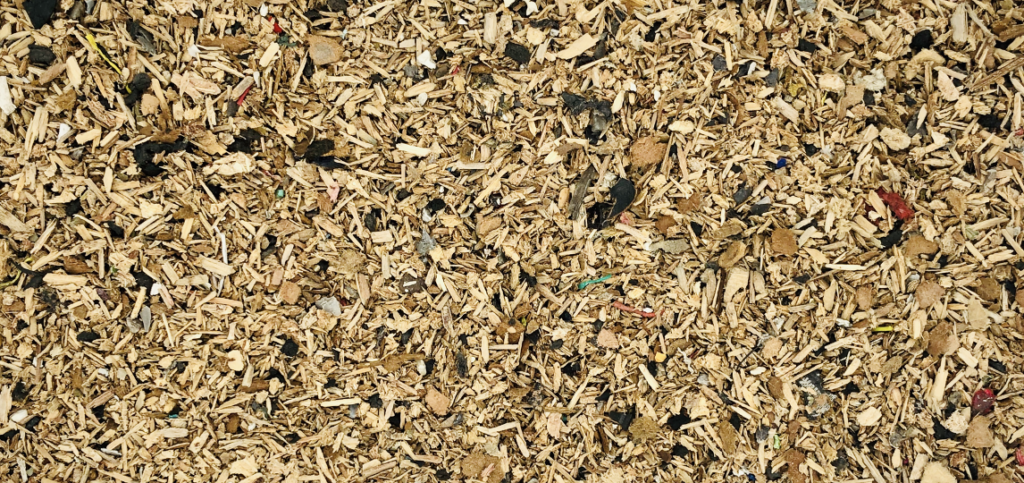
Wood is usually moist and therefore conductive. For this reason, wood present in plastic can easily be separated with the help of an electrostatic separator of the “conductor/non-conductor separator” type, such as the hamos KWS equipment. A highly concentrated conductive fraction is obtained, which also contains rubber particles, cardboard and other unwanted conductive residues.
6.2 Rubber separation
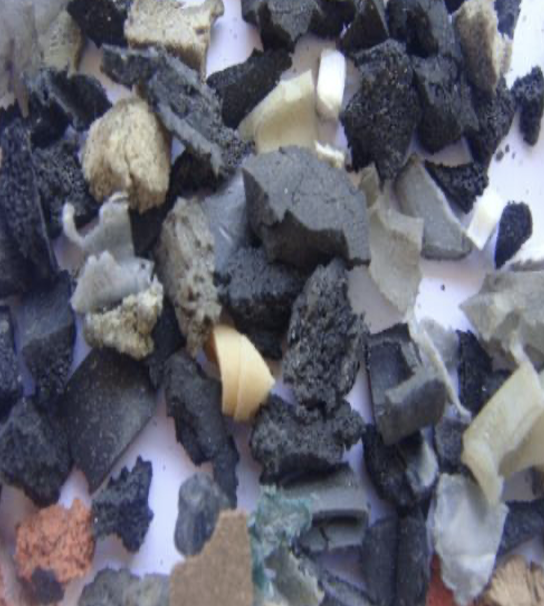
Separation of an unwanted rubber fraction is more difficult.
Since this fraction also contains silicones, chlorinated rubbers and other elastomers, special attention must be paid here to separating these foreign substances as completely as possible.
The “hamos RSS rubber separator” is used for this purpose.
This equipment succeeds in separating the undesired rubber fraction almost completely from ground material. Due to the physical characteristics of electrostatic separation, the rubber is mainly collected in the PS fraction, whereas the ABS fraction is already rubber-free after electrostatic separation. Therefore, only the PS fraction needs to be re-separated.
7. Conclusion
It is possible to separate pure and very clean PS, ABS and PP fractions with a combination of wet and dry processing methods, even from very complex mixtures of different hard plastics. Our customers running the hamos recycling systems for the separation of ABS, PS and PP already for many years.