However, after its removal from the wet paper pulp, the rejects have a high amount of moisture, leaving waste processing facilities with the challenge to optimize the drying process.
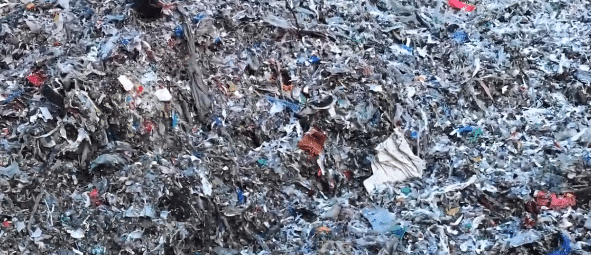
Unnecessary costs due to moisture
Depending on the facility, paper pulp rejects contain around 70% moisture when they enter the drying process. In the initial dewatering step, around a third of the moisture is removed. The rejects then typically have two destinations. W hen not destined for alternative fuel, rejects are often transported and disposed of with the remaining moisture, unnecessarily increasing transport and gate fee costs due to the weight of the moisture. When prepared for alternative fuel, a second drying process is often required to increase the calorific value, costing additional time and energy.
Optimising the dewatering process
What if the initial dewatering step could be improved? With contents reaching lower moisture levels in the initial step, a lot of energy and money could be saved in further treatments as well transport and gate fee costs.
In the case of conversion to fuel, a higher calorific value will mean easier and better incineration without requiring additional heating. Pellet production or reuse of paper rejects in general could become much more economical and sustainable while preventing material going to landfill.
Separation of liquids and solids under extreme pressure
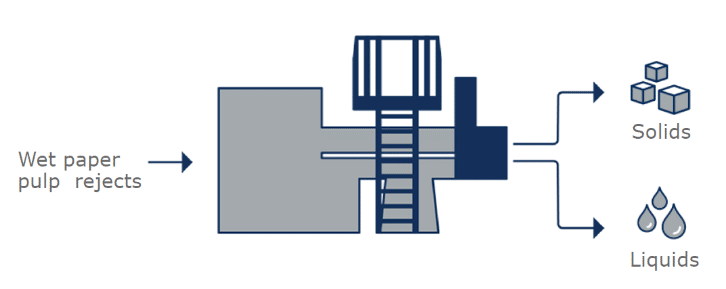
Royal Dutch Kusters Engineering provides this solution with its separation technique, the Organic Liquefying Press (OLP). The technology allows the user to separate moisture from solid waste fractions in a smart and energy efficient way. recent tests revealed its potential in dewatering paper pulp rejects, enabling at least 40 to 50% moisture reduction for any input and any level of initial moisture.
Dewatering test with the OLP at 40% initial moisture
Would you like to learn more about the potential of the OLP for your input material? Download the brochure or find more details on the webpage on Dewatering Paper Pulp Rejects