While many pressing plants had to close at the end of the 1990s due to the triumph of the compact disc (CD), the record industry has managed to remain successful in the music business to this day. This is now paying off, as records have once again become a sought-after medium in recent years, which is not only appreciated by music lovers. In addition to the nostalgia and collector’s value, the quality of the analog sound is increasingly preferred.
One-stop-shop for artists
The company’s manufacturing process proves that supposedly outdated technology can pursue modern sustainability goals. Record Industry sees itself as a full-service provider. Artists can record and mix music directly in the company’s own recording studio. Next, the audio is cut into either a lacquer disc or copper plate (DMM) using a cutting lathe, which translates the audio signal into a modulated groove. This master is then processed through several steps in a galvanic (electroplating) process to create stampers, metal molds that are used to press the grooves into vinyl, producing the final record. So-called pucks (similar in shape to those used in ice hockey) made of special PVC are used in the pressing process. The pucks are then shaped into thin records using pressure and heat. After a short cooling period, they are placed in fully automated paper sleeves for protection. The final step is packaging in the respective covers and sleeves. The record is ready to be sold and played.
From puck to record – and back again
During each pressing process, an approx. 20 mm wide protrusion of PVC material – i.e. the remainder of the puck – is created on the outside due to the process. This is sheared off, giving the record its final circular shape. Next to each of the almost 40 pressing machines is a compact C-series granulator from Wanner in Wertheim, Germany. The production waste is automatically discharged from the pressing machine and transported into the granulator’s hopper. Within seconds, the offcuts are shredded into flakes approx. 4 mm in size and fed to the extruder via a mixing chute. This results in no waste, as the edge trimmings are processed directly inline.
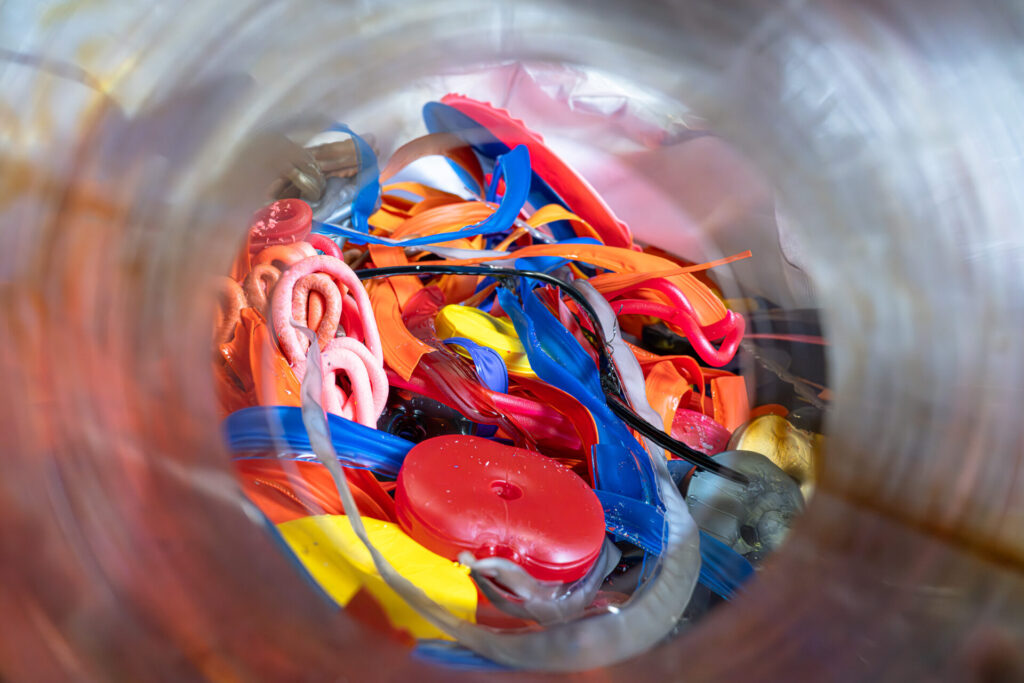
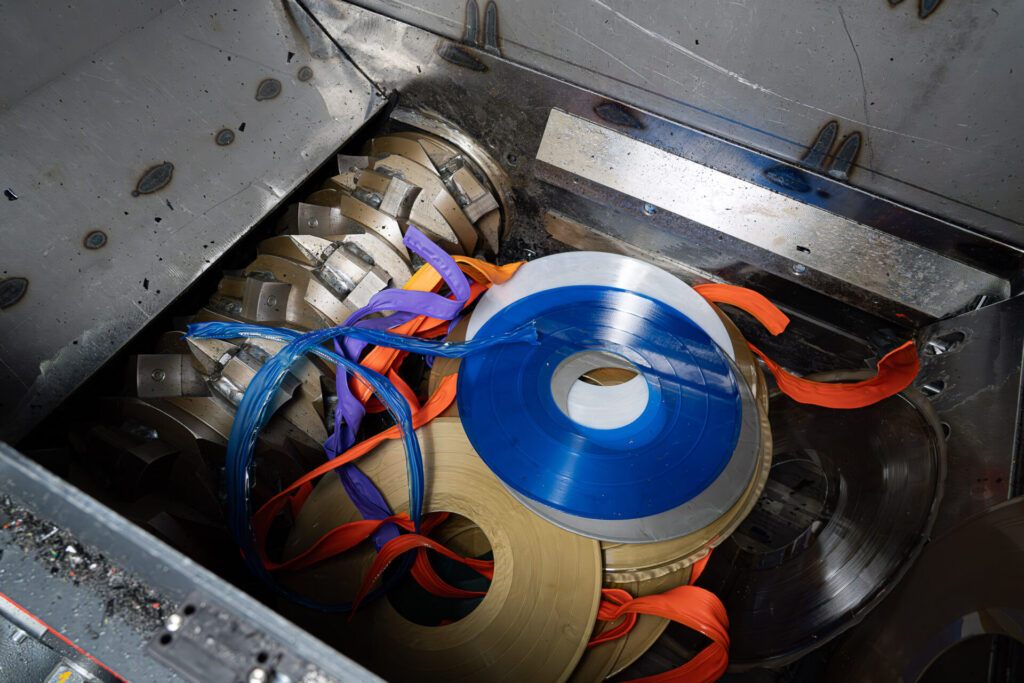
Modern recycling line with WEIMA pre-shredder and Wanner granulator
Occasionally, pucks or individual records do not meet Record Industry’s quality requirements. As the pucks are too massive and the records too large for the small granulators, they have to be processed separately. Record Industry therefore set up an additional recycling line in the building next to the pressing machines. A WEIMA WLK 4 single-shaft shredder was put into operation there at the end of 2024 for shredding predominantly mixed PVC residues. Material can be loaded manually or by forklift from big bags via a conveyor belt. The WEIMA shredder pre-shreds the PVC to approx. 25 mm flakes before it is reshredded to approx. 4 mm granulate via a further conveyor belt with metal detector in a Wanner granulator of the Dynamic series. To improve the processability of the material, the resulting recyclate is fed through a dedusting system to remove the fine dust from the ground material.
Colorful variety for sustainable products
The end product is high-quality PVC flakes that can be reused in the record pressing production process. The colorful mixture of flakes creates an individual marbled coloration during pressing. Record Industry is proud to now have a 100% recycled product in its range thanks to these colorful records. The result of the collaboration with the shredding specialists from WEIMA and Wanner is correspondingly positive:
“The pressing of our records is virtually waste-free thanks to the smooth cooperation with the technicians from WEIMA and Wanner. We make maximum use of our material resources and can supply our artists with a truly sustainable product. This is in keeping with the spirit of the times and is also economically attractive for us.” Dennis Borst, Technical Manager at Record Industry
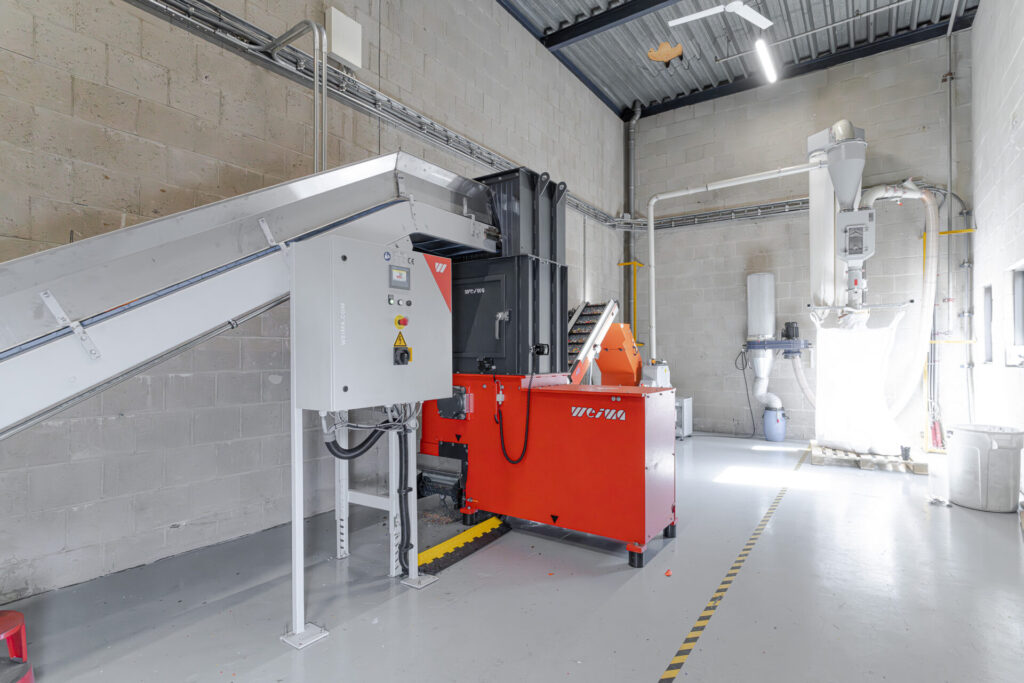
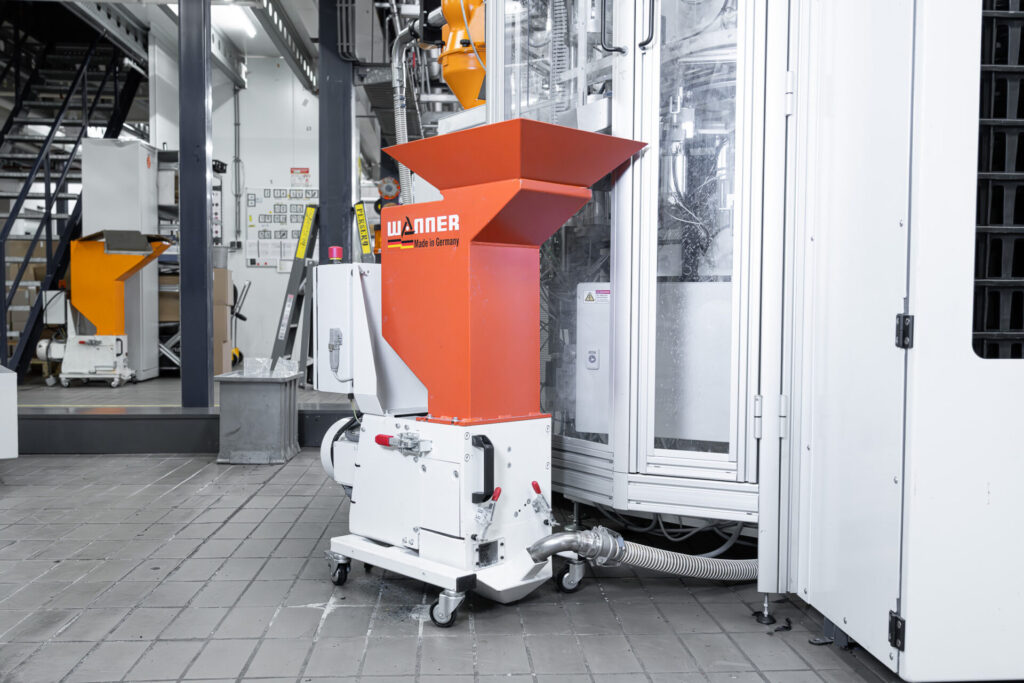
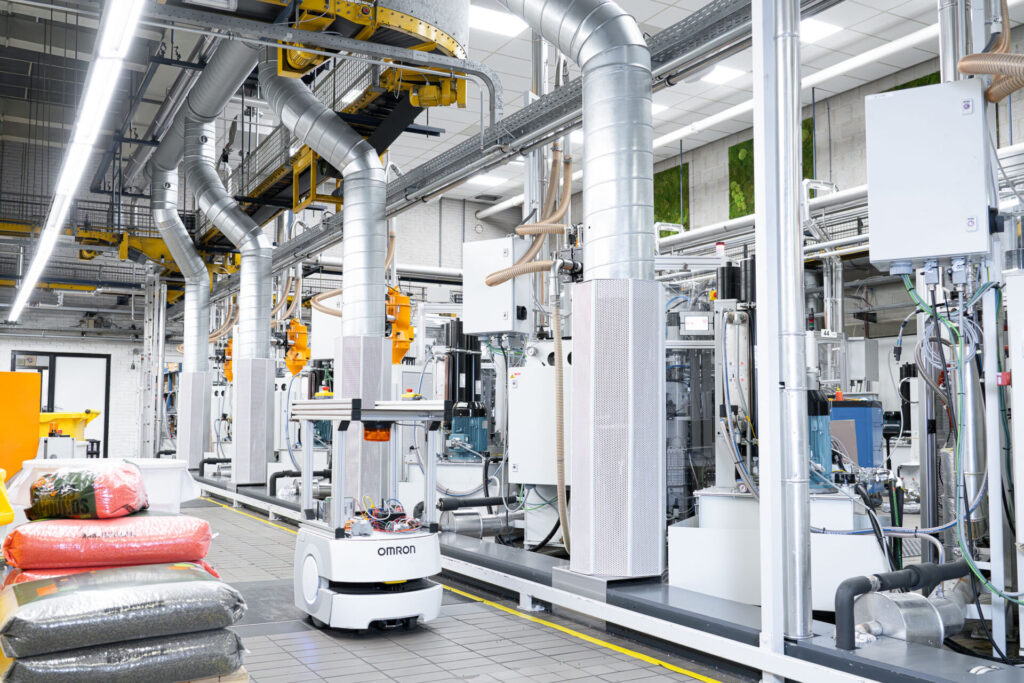