The Tyre Recycling Market size was USD 6.00 Billion in 2023 and is expected to reach USD 8.21 Billion by 2032 and grow at a CAGR of 3.55 % over the forecast period of 2024-2032 with only 50% being recycled. The remaining volume often ends up in landfills, incinerators, or illegally dumped, posing severe environmental hazards.
However, OTR tyre recycling business presents a lucrative opportunity because it has one of the highest gate fees and exorbitant demand for recycled rubber products, such as crumb rubber, rubber mulch, tyre-derived fuel (TDF) and pyrolysis.
Therefore, size reduction is one of the crucial aspects which involves the use of advanced technologies and machinery, such as shredders and granulators, to downside OTR tyres into valuable recyclable materials.
Fornnax Technology, one of the leading equipment manufacturers of recycling equipment like primary and secondary shredders, granulators and separation systems with over a decade of expertise in tyre recycling with customized solutions. Fornnax’s machineries have surpassed the industry’s standards for efficiency, reliability, and performance, offering a robust solution for OTR tyre recycling through Crumb Rubber Production Line.
Fornnax’s systems are designed to maximize the purity of output products while maintaining operational efficiency. Furthermore, their comprehensive support before, during, and after sales ensures a seamless experience for customers.
Fornnax Crumb Rubber Tyre Recycling Plant Stages
Fornnax’s crumb rubber recycling process operates through three distinct stages, ensuring a systematic and efficient conversion of OTR tyre waste into high-quality crumb rubber and granules.
Stage 1: Primary Shredding The process begins with the Fornnax SR-Series primary shredder, a high- torque, low-speed unit that efficiently reduces whole tyres into strips approximately 50mm wide and 300mm long. The infeed conveyor system ensures a consistent feed rate, while the integrated screening mechanism recirculates oversized strips (>150mm) for reprocessing, achieving uniform shred sizes.
Stage 2: Secondary Shredding Next, the Fornnax R-Series secondary shredder processes the primary shred into 20-30 mm rubber mulch. This heavy-duty, medium-speed equipment features an advanced screening system and over-band magnet, effectively liberating ferrous metals from the bead and tread areas. The resulting rubber mulch, with up to 98% steel-free content, is ideal for Tyre Derived Fuel (TDF) applications or further granulation.
Stage 3A: Primary Granulation In this stage, the Fornnax TR-Series granulator receives steel-free rubber chips via a conveyor feed system. Designed for high-efficiency downsizing, this unit liberates 50% of the textile content, which is then separated using Classifier-1. The granulated material is conveyed pneumatically for further reduction or directed to the Auto Bag Filling System for packaging.
Stage 3B: Final Granulation The final granulation stage involves the Fornnax TR-Series granulator, which processes the primary granulated material into rubber granules sized 0.8-4 mm. This high-speed unit, equipped with a sophisticated screening system and secondary magnetic separation, ensures the removal of residual steel (1-2%) and textile, delivering rubber granules with up to 99.9% purity.
Versatility in Input and Output
The Fornnax Tyre Recycling System is designed to process a wide range of input materials, including all types of waste tyres, regardless of size. Our Primary Shredder Technology, developed as part of the Crumb Rubber Production Line, can handle various sizes of OTR scrap tyres without any specific requirements or limitations. Through Fornnax’s advanced size reduction technology, we produce several valuable products:
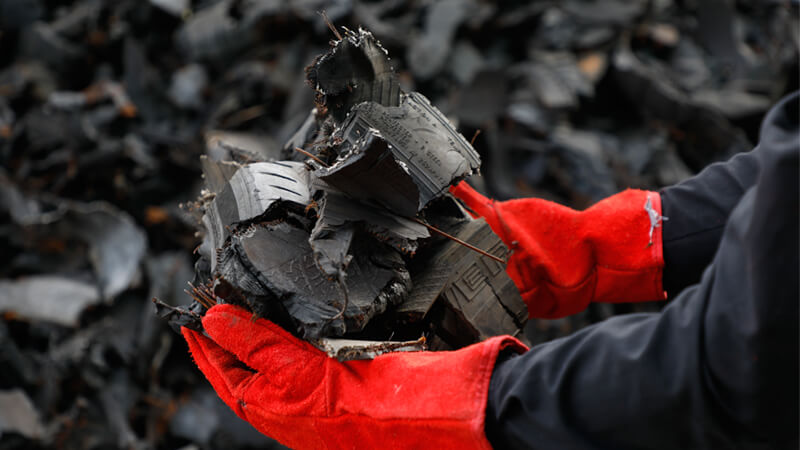
- Tyre shreds (approximately 50-300 mm) are produced from our SR-Series Primary Shredders without screening and can be used as tyre-derived aggregate (TDA) in various civil engineering applications.
- Tyre shreds (50-150 mm) are produced from our SR-Series Dual Shaft Shredders with a disc classifier screen and can be used as raw materials for secondary processors, such as rubber chips or rubber granule manufacturers.
- Tyre shreds (50-80 mm) are produced from our SR-Series Dual Shaft Shredders with a trammel screen and can be used as Tyre Derived Fuel (TDF) in various industries, including cement kilns, paper and pulp mill boilers, and power plants.
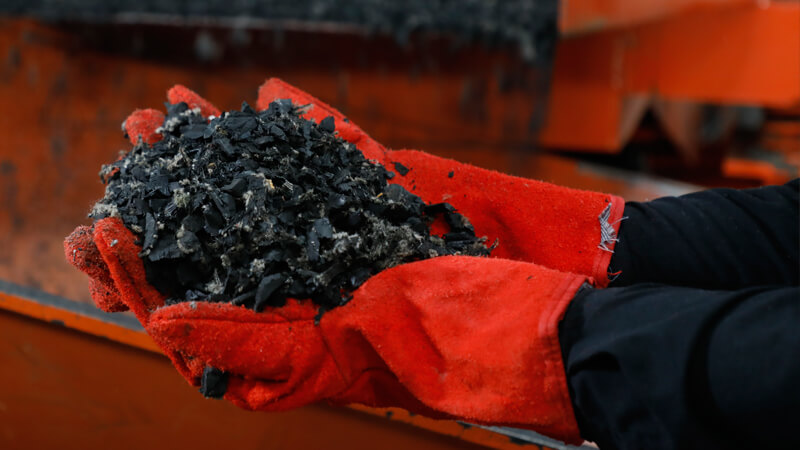
- Steel-free chips/rubber mulch (approximately 12-30 mm) are produced from our R-Series Secondary Shredders with an over-band magnet and can be used in landscaping, playgrounds, civil engineering applications, high value TDF and pyrolysis.
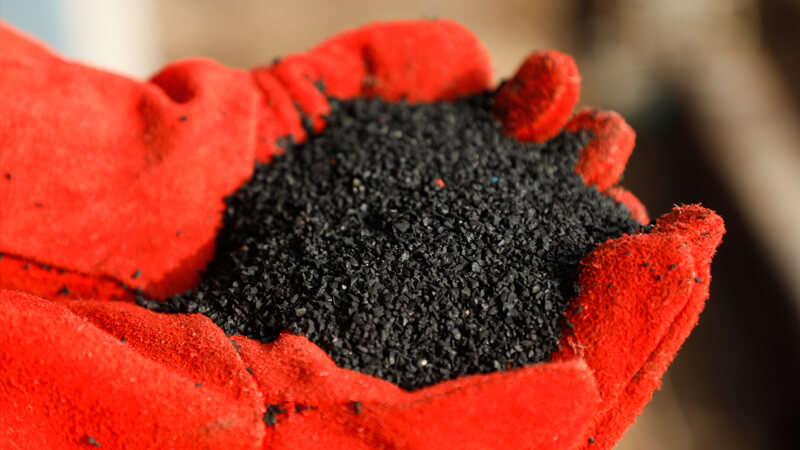
- High-quality rubber granules (approximately 0.8-4 mm) are produced from our robust Granulator with a fibre separation system and can be used in various applications, including sports surfaces, road construction, reclaimed rubber sheets, rubber mats, automotive parts, and more.