What is called waste from building and demolition is always under scrutiny, landfill is not an option as all the inert material can be easily processed to be reused. Some, refer to this recycled material as the seventh resource. So why is such a precious material often discarded? Why a company bears the cost of waste disposal instead of reusing the debris?
The answers vary from job site to job site. Sometimes the restriction could be logistics as a lack of roads or busy city centers. Other times the presence of rebar makes the process to difficult and expensive.
The certainties are that continue to accumulate inert material is an unsustainable cost for our planet therefore there are many laws taking place with the aim to reduce the percentage of waste by recycling.
Companies should see recycling as an opportunity not only for the environment but for the company revenue itself. By simply by crushing debris and excavation materials in the same construction site where they were produced a company reduces trips to move the material from the site to the landfill. Limiting the truck journeys, it respects the environment because it is not polluting, and reusing material at the site does not exploit natural resources, and for the company, these are huge savings, no landfill fees, no transport costs and no material purchasing expense.
There are solutions today. Attachments like the MB jaw crusher bucket that travels with the excavator to any site, and transform demolition waste into a resource on-site: for filling the foundations of new constructions, pipe excavations, road surfacing, or in gardens as decoration elements. And if it does not find opportunities for use on the construction site, it becomes a commercial resource: it can be sold to other companies.
A compact jaw crusher transforms the stones into different sizes, depending on what the site requires. And even those materials that some operators consider “difficult” as old light poles, columns, and concrete pipes, railway sleepers, vineyard poles with spring steel can be reduced easily. This because the bucket crusher geometry facilitates the horizontal crushing, separating the concrete portion from the metal rebar.
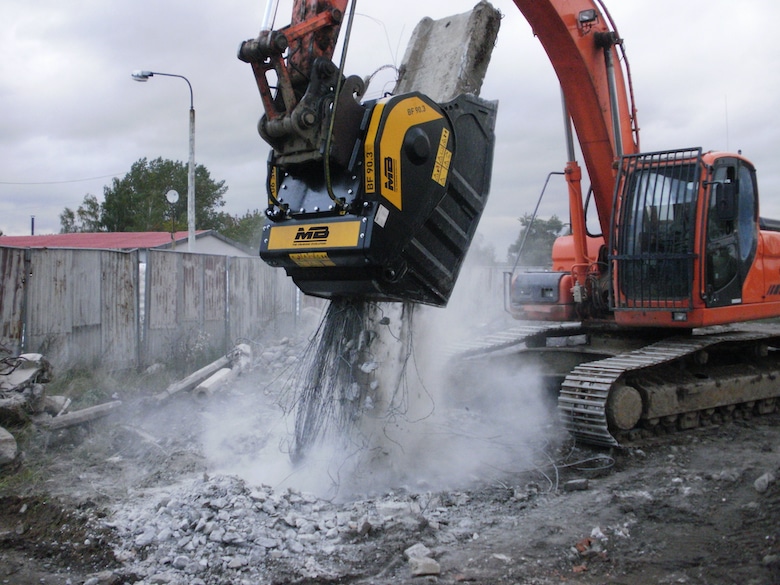
No drawbacks
Disposing of reinforced concrete poles in recycling centers is pricey, even if it’s just the cost of transporting the material. If a company wants to be independent and use a stationary crusher, the rebar in the concrete can easily cut the conveyor belt or jam the machine, which results in downtime, work stops, and wasting time and money. Alternatively, some crush with demolition shears, but it is a slow process.
This doesn’t happen when using MB’s crushers: the iron comes out while the unit is crushing and can be separated from the processed material with the iron separator, which is installed on the MB unit and controlled by the operator from the cabin.
Canceling rental and transportation costs
When the volume of debris is small, the choice seems to be to pile up these materials. Stockpiles take up space, sometimes for years before it is worthy to rent a crusher, also costs bringing the material to a recycling center to the storage areas means hauling fees. The solution is to use a crusher bucket, the lines are suitable even for compact excavators, so even small job sites can benefit from crushing and reusing the waste immediately. Therefore, eliminating rental and transportation costs and there’s no longer a need for large storage areas.
Reach any jobsite
The jaw crusher bucket is installed on and transported with the heavy equipment unit used in the project, eliminating all struggle and expenses commonly associated with jobs in remote areas, where there are no roads or are located in hilly terrain. Reaching the job site is the first expense and obstacle to consider when pricing a job, especially if the location is in an isolated area with limited or no access. Bigger machines require expensive, specialized transportation but by mounting an MB crusher bucket on a piece of equipment, the unit is transported avoiding expensive or complex transportation methods.
Material recovered and immediately reused
Why throw it away when it can be recycled? Instead choose to reduce it on-site with a single machine—a simple and fast operation, adopting new solutions to facilitate the workflow on the construction site is the answer.
Construction sites that adopted MB Crusher units found an easy and inexpensive way to crush and recycle all types of inert material.