Black plastics represent a particular challenge because they cannot be detected with the optical sorting technology found in standard recycling plants. STEINERT technology allows black plastics to be sorted from the general waste stream and to be sorted into pure grades. This enables plastic-processing companies to respond to the new challenges of the circular economy in a cost-effective manner and to be equipped for all the processes involved in plastic recovery and processing in equal measure.
Since 2011, STEINERT has been developing detection technology for very challenging sorting applications and providing forward-looking reference projects, which document that plastics and the environment are compatible.
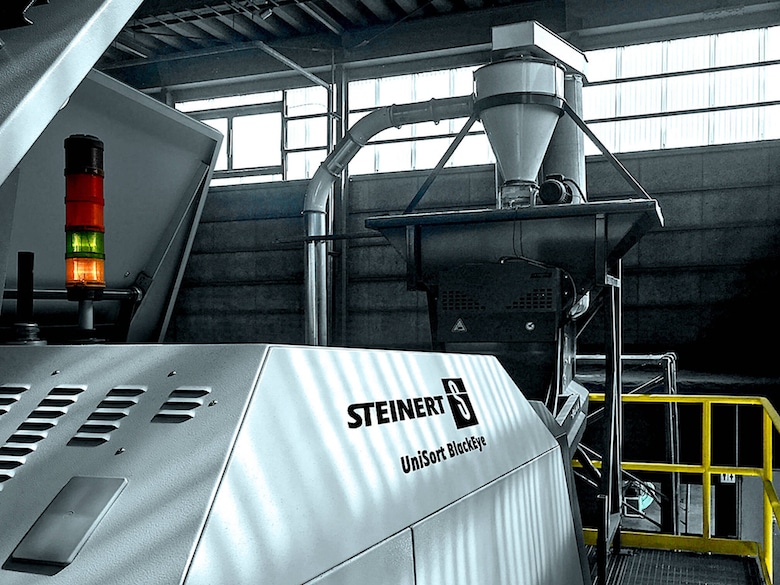
For example, STEINERT was the first company to be able to detect black plastics and thereby positively separate them, allowing recycling rates to be increased. Sophisticated airflow technology also makes STEINERT the only company to be able to cost-effectively sort flat and lightweight black materials. What’s more, the pure-grade separation of black polyolefins (PO) into their constituent parts, such as polyethylene (PE) and polypropylene (PP), but also polystyrene (PS) and acrylonitrile butadiene styrene copolymers (ABS) allows polymer granulates to be replaced by mint-condition recyclates.
Turning plastic residues into new goods – thanks to the pure-grade separation
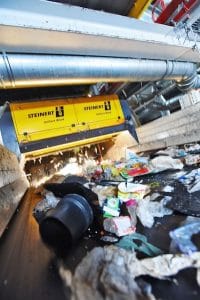
Plastic-processing companies, in particular, can, therefore, benefit from STEINERT products and separate plastic residues containing a high proportion of black content at a large-scale industry level and then upgrade them to a plastic granulate with properties similar to those of the primary raw material in order for it to be used to manufacture durable quality products. This procedure means that a significant percentage of new plastics can be replaced with recycled materials today, thereby saving hundreds of thousands of tons of CO2 every year.
State-of-the-art technologies coupled with 130 years of process know-how allow international customers to combine cost-effectiveness with sustainability to comply with stricter legislation and the sense of responsibility demanded by society and therefore take one step closer to a genuinely closed resource cycle and more environmentally-sound future.
Prepare to be impressed by STEINERT’s technology and vast experience and let us work with you to put you on track for the future. Come and visit us at the K Trade Fair running between 16 and 23 October in Düsseldorf, Germany. You can talk to our experts about your plastic sorting tasks on stand B23 in Hall 9.0.