With the newly developed WEIMA PUEHLER C.200 chip press, the drainage and compaction of loose chips are possible in just one automated work step. Liquids can be recovered in the process. Best of all: The compact machine can be placed directly at the chip conveyor next to the machining center.
A well-known problem
Every metalworking company knows the sight all too well: tipping containers that are notoriously overflowing with voluminous chip balls and that need to be emptied manually on a regular basis. This situation should be avoided in the case of low-staffed to fully automated multi-shift operation of a CNC machining center, especially during the night or even over the weekend.
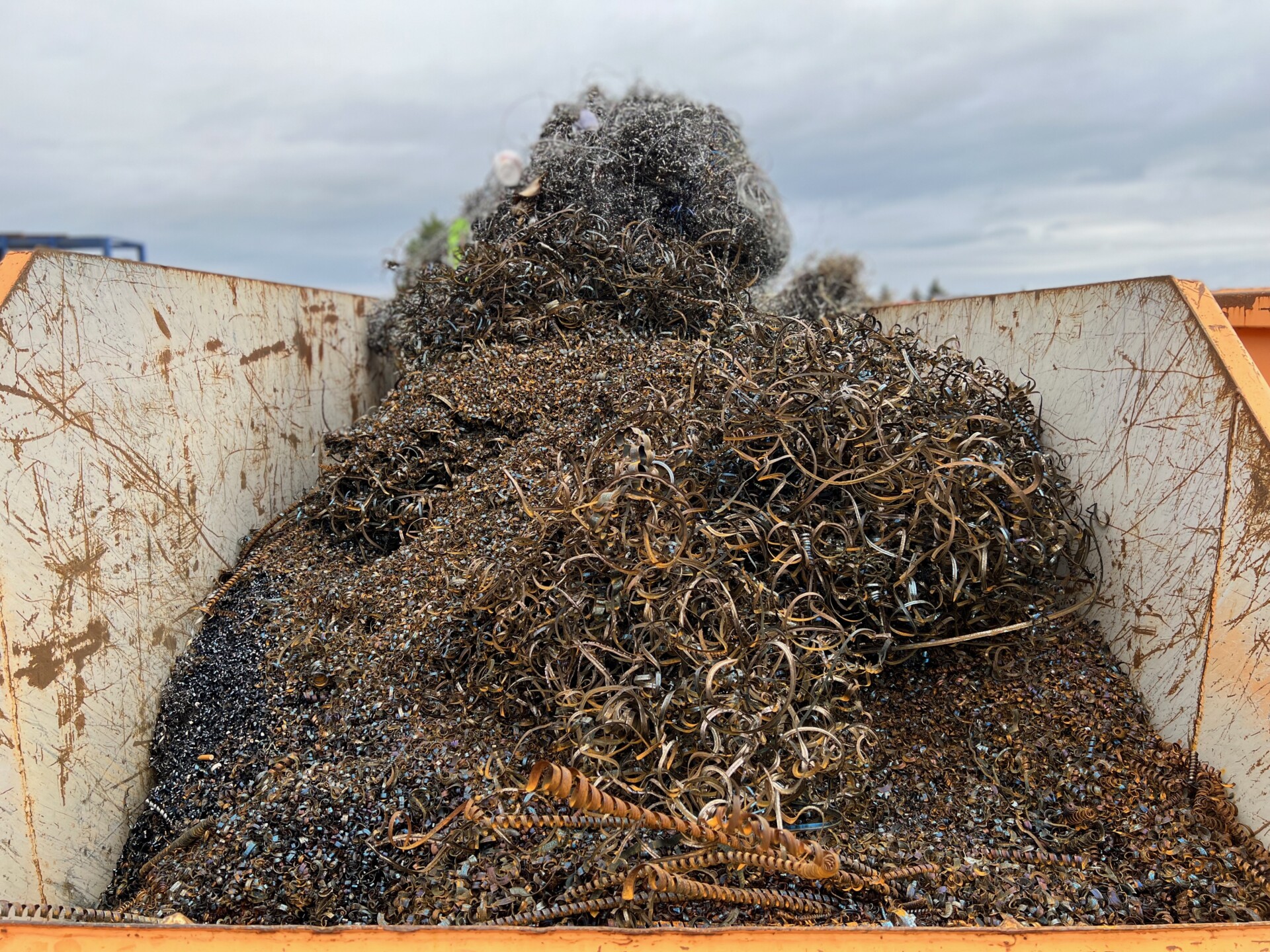
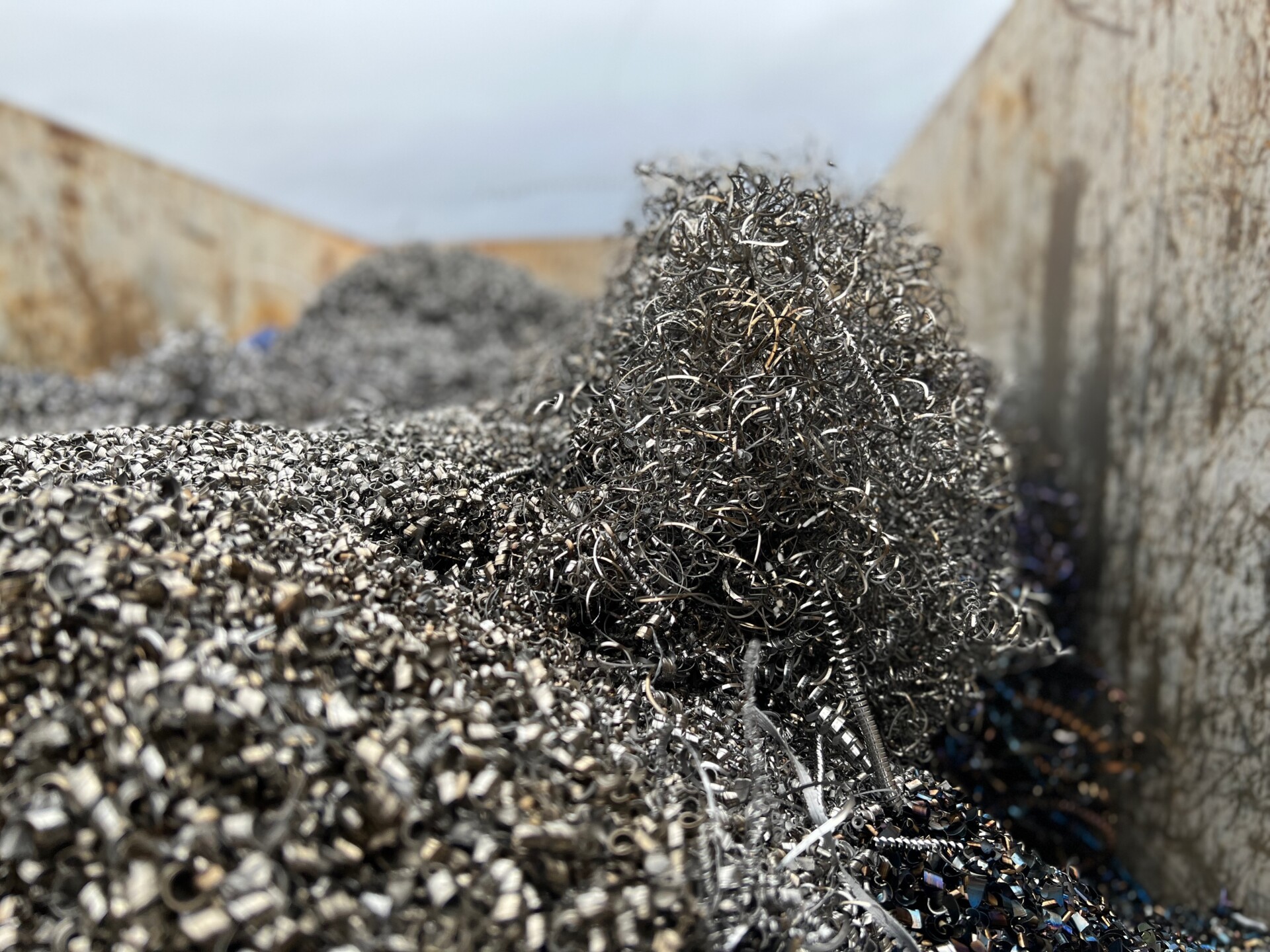
No screw conveyor susceptible to interfering substances required
In order to achieve the highest process reliability, WEIMA offers a robust all-round carefree package with proven technology in the form of the PUEHLER C.200 chip press. Like all WEIMA compaction machines, it also uses hydraulic pressure for the pressing process. Thanks to a low-maintenance press stamp, no screw conveyor or separate pre-compression are required. The major disadvantages of augers include their high susceptibility to impurities and increased wear. Foreign objects and extra-long or ball-like chips are simply pressed together with the PUEHLER press. Without damaging the machine. Without bridging. Without wrapping.
2 in 1: Low-maintenance drainage and compaction that saves money
Many cubic meters of chips are turned into easy-to-handle pellets with a diameter of 200 mm and low residual moisture. How is that possible? Because during the compaction process, the liquids adhering to the chips are pressed out. Lubricant or coolant enters a collecting tray via sieve holes. From there, it can be pumped out and, if necessary, returned to the recycling circuit. This saves costs in two ways: Fewer new coolants need to be procured. And the disposal costs of the chips are significantly lower due to the reduced weight.
Universal application thanks to plug-and-play installation
The PUEHLER C.200 press can be easily placed under any common chip conveyor discharge from a turning, milling, drilling, or sawing center. The machine feet on rollers are height-adjustable. The generous hopper offers plenty of room for picking up large chip quantities and also acts as a material buffer. Once in the pressing chamber, the chips are pressed and drained using a horizontally movable pressing cylinder together with a press stamp. The hydraulic unit works with a 4 kW unit in the pressure range up to 200 bar. The Siemens PLC control system can flexibly adjust the press cycles dependent on time. A simple signal connects the press and processing machine. Pressing occurs only when the chip conveyor is also in operation. To minimize downtime, accurate diagnostic messages are displayed for troubleshooting.
Material compaction by a factor of 10
The material can be discharged in two ways: (1) Two half shells on the conical discharge pipe are closed hydraulically and thus hold the pellets produced by the pressing cylinder. (2) Two half shells on the conically shaped discharge pipe hold the generated pellets by means of a strong preload using disk springs. The degree of compaction is up to 1:10, depending on the material.
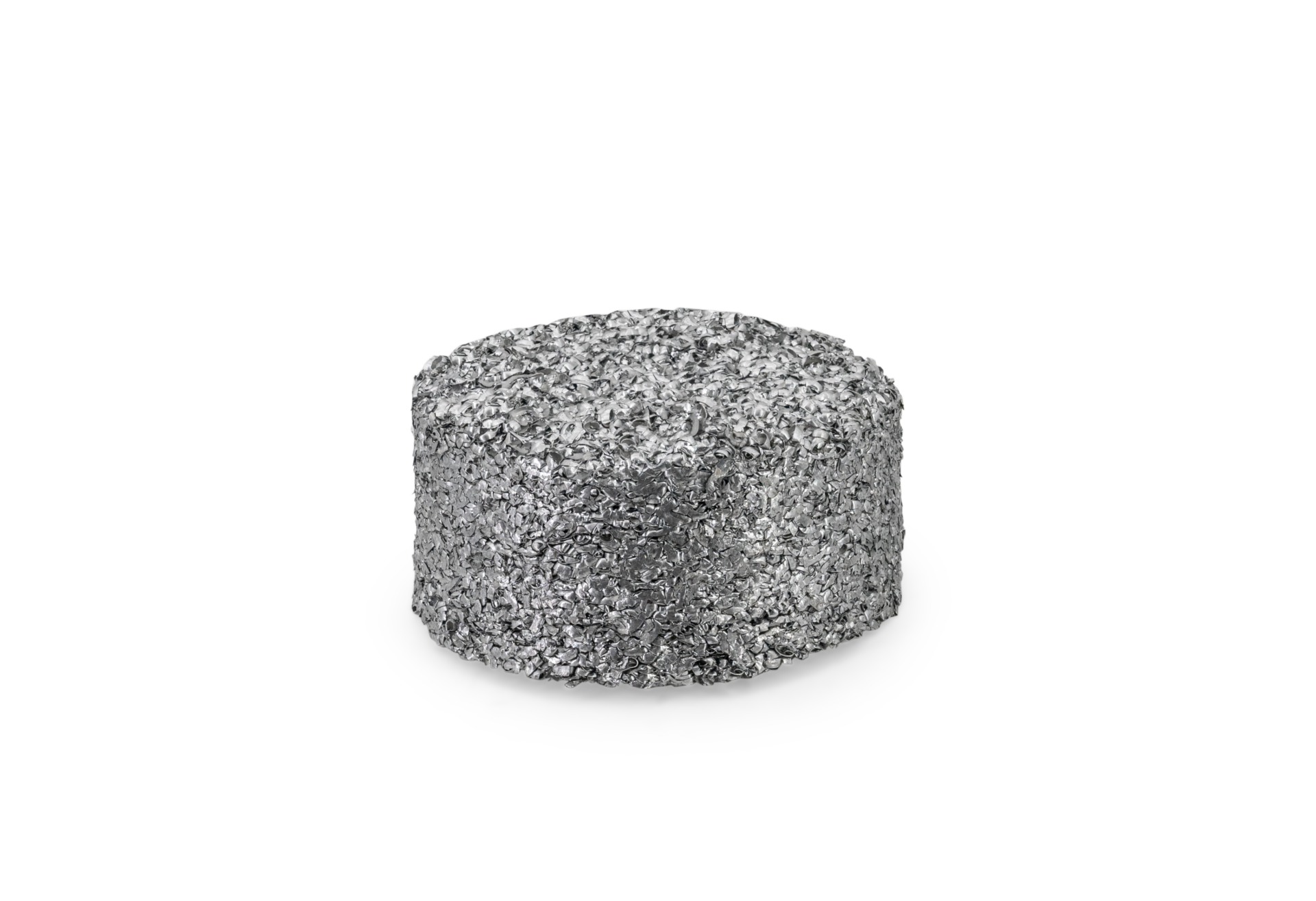
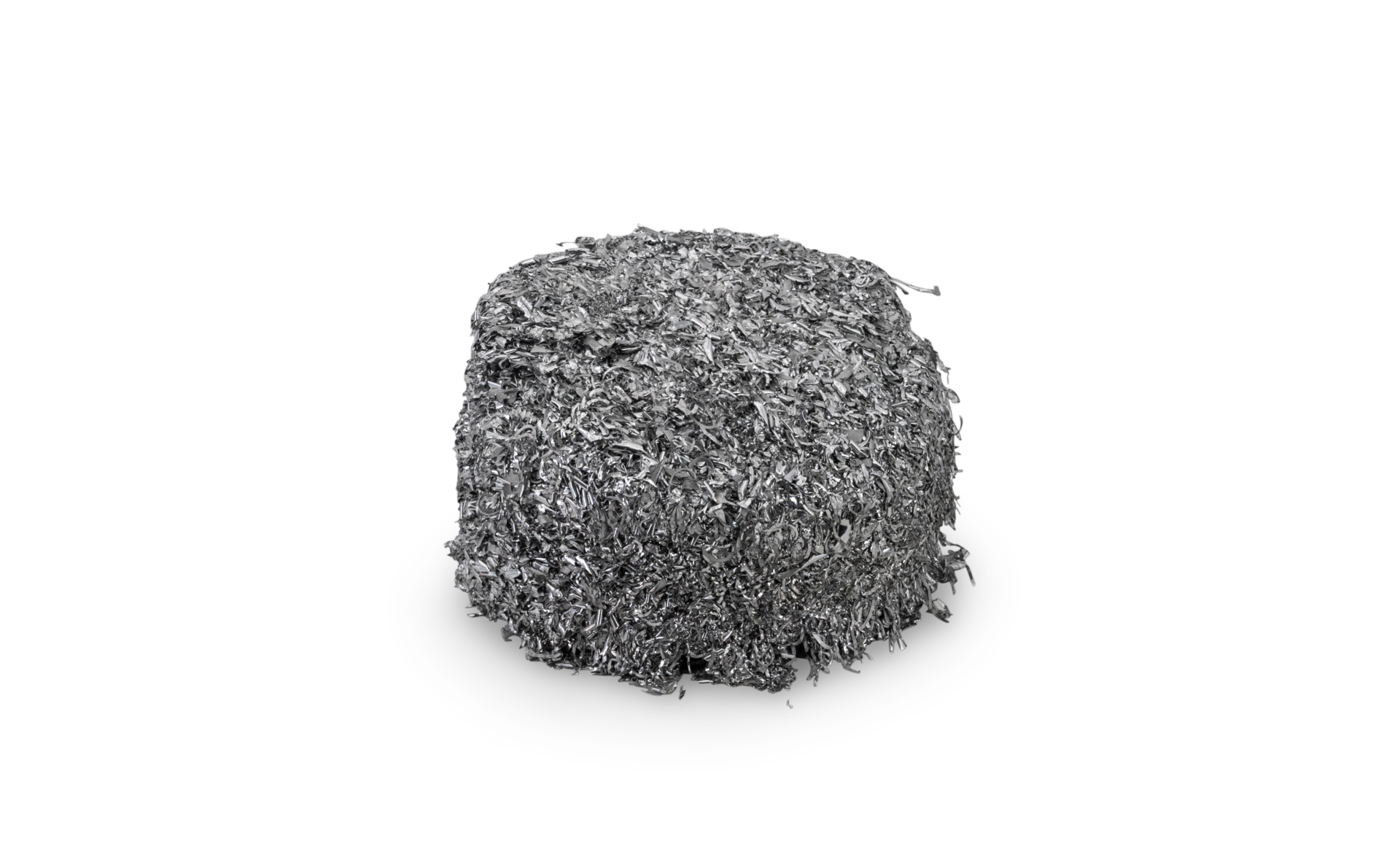
Worry-free automatic operation
The press can be used automatically by means of precise fill-level sensors in the feed hopper. The machine switches on automatically when a certain fill level is reached in the hopper. In order to prevent wear on machine components, the machine also automatically switches to stand-by as soon as the fill level falls below a certain level.
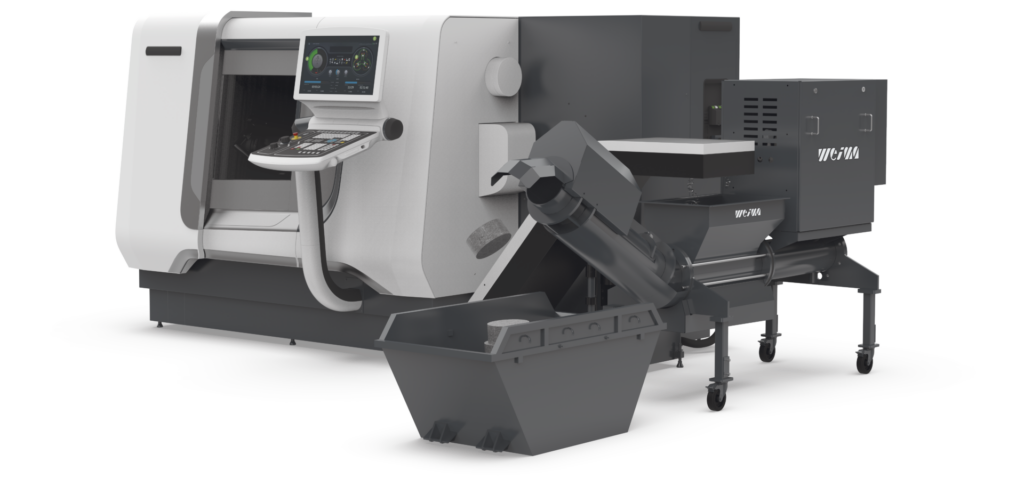
Press for metal AND plastic chips
Due to its solid mechanical structure with a minimum of moving parts, the WEIMA PUEHLER C.200 can be used not only for chips made of aluminum, steel, copper, etc. but also for many types of plastic. One application example is the draining and pressing of fines from the washing system. In the course of post-consumer plastic recycling, material streams are cleaned after crushing before being processed further (e.g., extrusion). Due to the process, plastic particles that are no longer usable accrue and have been drained before disposal due to their high weight.
Twice as good – for greater flexibility
In the duo version, the two self-sufficient press stamps of the PUEHLER C.200 Duo can be filled one after the other with the aid of a movable partition plate in the hopper. To reduce downtimes, both compression chambers can be used alternately. In the event of a malfunction, the machine automatically switches to the available pressing channel.
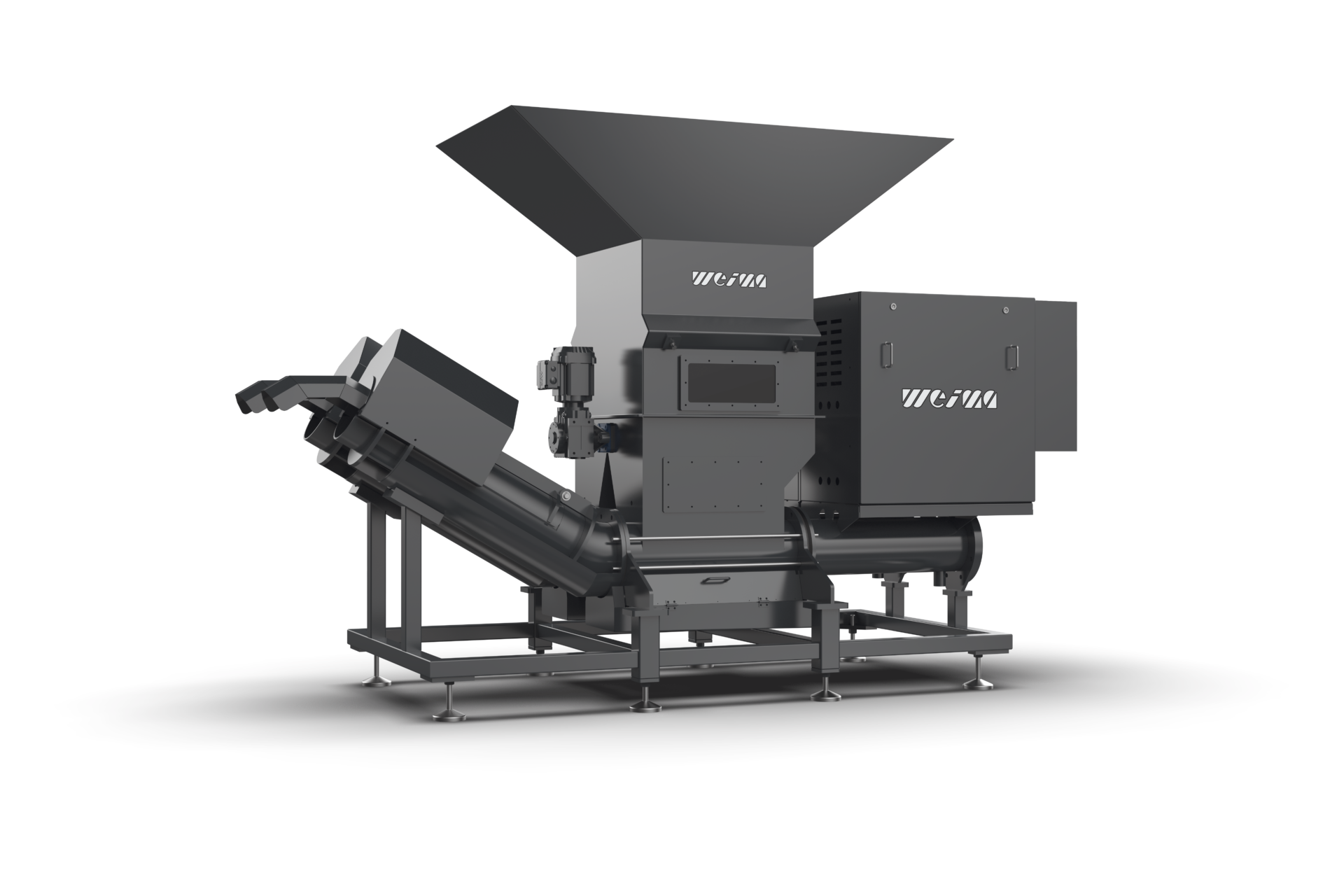
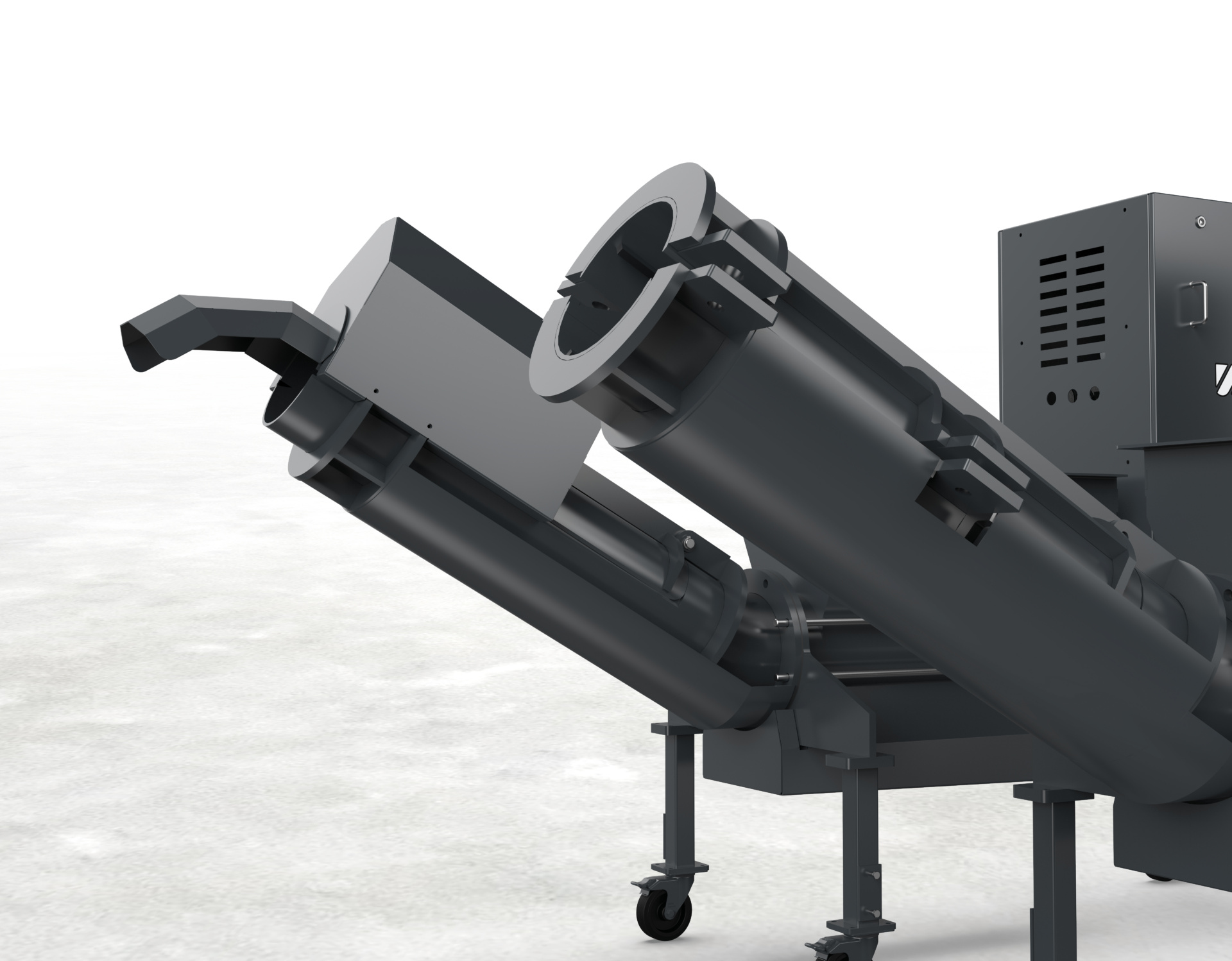