Recyclers must swiftly adapt to prepare for the significant surge in recycling of LED lighting products, as the global shift towards energy-efficient LED lighting is projected to grow at a compound annual rate of 11.0% from 2023 to 2030, according to Grand View Research. The challenge lies in the disposal of large volumes of used bulbs with varying sizes, shapes, and diode densities. LED lighting manufacturers must also recycle defective products to reclaim valuable materials that can include gallium, indium, and other metals from electronic chips, as well as glass and plastic. The gallium and indium can be separated later by further processing.
To maximize recycling yield, however, the key is to effectively dismantle intricate LED configurations and then efficiently separate them into valuable materials. This requires recyclers to adapt their processes and systems to cater to the distinct characteristics of LEDs, which differ from traditional incandescent and fluorescent bulbs.
“Recycling LEDs is an emerging form of electronics recycling that lacks a comprehensive system for effective material separation and plant environment control. There are unique challenges in the process and few systems are specifically designed for both efficient recycling and the maximized extraction of saleable materials,” says John Neuens, Industrial Consultant, BCA Industries, a developer and manufacturer of industrial shredding and recycling equipment.
“Companies that have historically produced electronics and light bulbs are also venturing into the LED market and looking to recover material from defective products as well,” adds Neuens. He notes that LEDs are essentially a fusion of lighting and electronics, consisting of various components like a chip, heat sink, circuit board/driver, housing, base, and lens/optics.
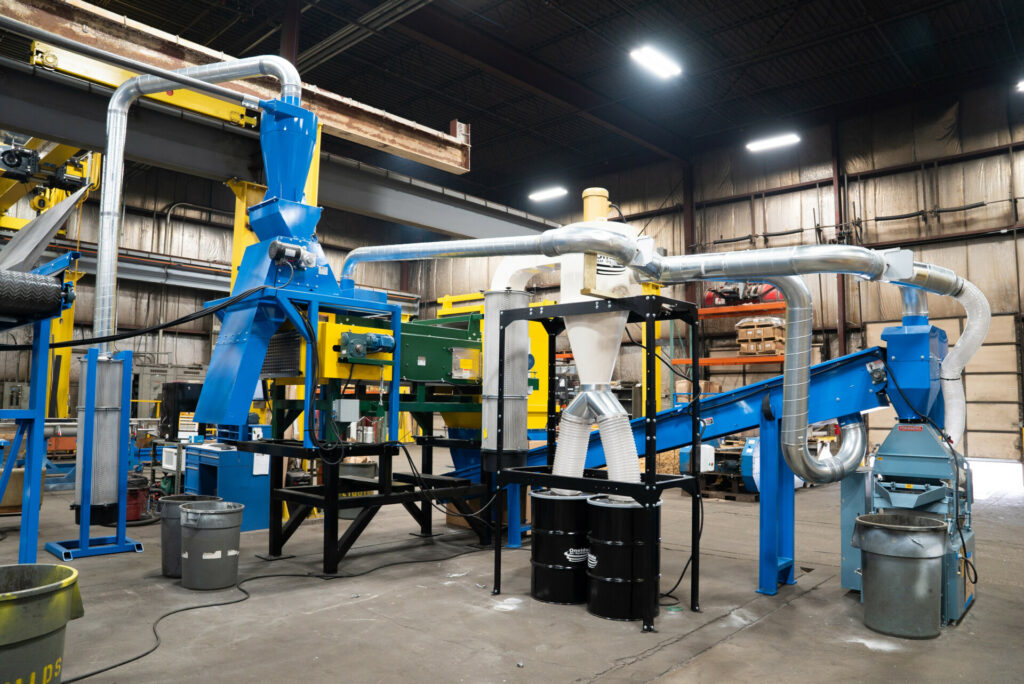
Unfortunately, recyclers have encountered obstacles in achieving profitability and scale-up due to the use of recycling systems not specifically designed for LEDs. As a result, the outcomes have been inconsistent and inefficient.
According to Neuens, a leading multi-location recycler reached out to BCA with the aim of enhancing the efficiency of their LED reclamation process. The OEM responded by developing a system specifically designed for LED lights. This system effectively separates and recovers the maximum amount of valuable material. After successful development and implementation, the system is now available to other recyclers. It is particularly valuable for those involved in the electronic separation/destruction industry, especially those who previously recycled standard light bulbs.
The LED recycling system is engineered to maximize the precision and accuracy of separation, resulting in higher market value for the extracted materials. The original system was initially intended to handle a capacity of 1.5 tons of LED bulbs per hour. However, it has the flexibility to be tailored to any desired volume and customized to meet the specific mix of products received by the recycler.
“LEDs, while longer-lasting and more energy-efficient than other bulbs, still require effective recycling. Disposing even a small amount of recyclable materials in landfills should be avoided,” says Neuens.
The Challenges of Recycling LEDs
Efficiently recycling LEDs is an extremely complex process involving sequential mechanical reduction and separation. This entails not only cutting and crushing but also magnetic, electrostatic, and gravity separation and classification.
To ensure health and safety, it is crucial to have adequate environmental controls in place at every stage of the process. These controls should effectively manage and collect dust, as well as other possible contaminants that may pose hazards.
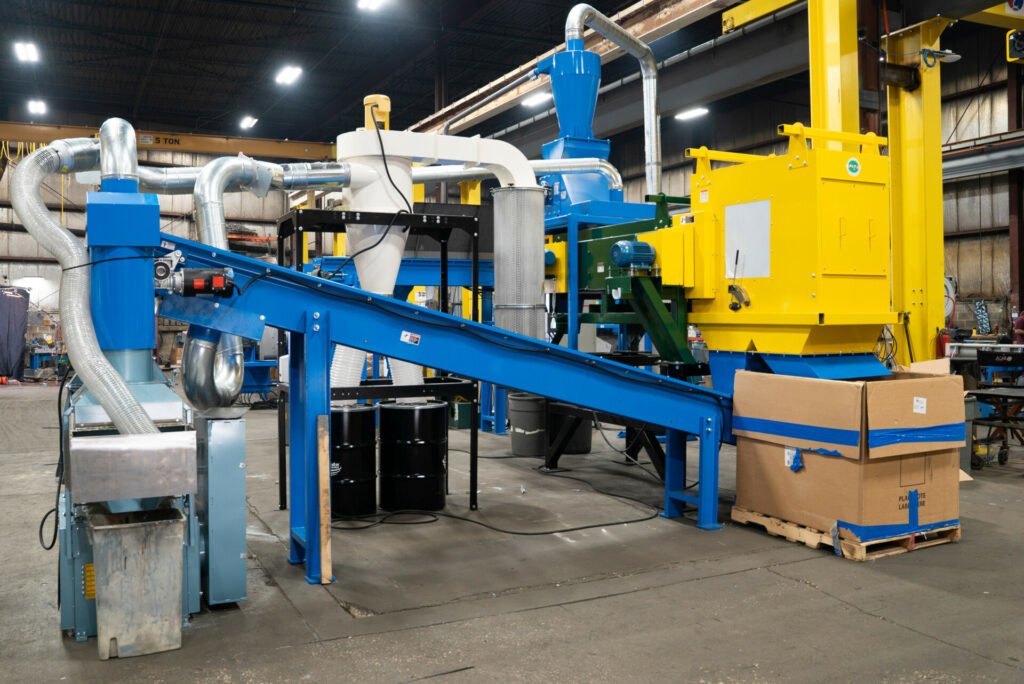
The objective is to maximize the recovery of usable material, isolating it into the most saleable form. However, complex issues can arise when assembling and implementing systems like these in a piecemeal manner. Problems frequently occur during installation and persist throughout production, leading to decreased efficiency, quality, and profitability. If an issue arises, “finger pointing” often occurs between multiple vendors, with each blaming the other while the core issues remain unresolved.
Even hiring a third-party engineering company or integrator may not resolve the situation if those involved do not have a clear understanding of the design and functioning of the component parts. This understanding is crucial when reconfiguration or modification is required to accommodate the recycler’s specific circumstances.
In the meantime, the recycler may experience a decrease in production or even a complete halt.
Optimizing LED Recycling
To meet increased LED volumes and avoid such issues, a recycler with over a dozen locations turned to BCA to design a complete end-to-end system tailored to meet their needs. According to Neuens, the LED-specific system that BCA designed for the recycler is comprised of various integrated equipment that functions in concert.
Initially, an infeed conveyor brings inoperable LED bulbs to a dual shaft shredder. Next, a series of magnets are used to recover ferrous metals that could otherwise be trapped under other material. The conveyed material is further reduced by a granulator, a single shaft machine with a bed knife that crushes and cuts, and additional magnets are used to capture the finer ferrous material. An eddy current separator is then utilized to extract non-ferrous metals like copper and aluminum.
Other processes such as vibratory screening and density separation are utilized to extract additional valuable materials like glass and plastics of varying weights.
Throughout the reduction and separation process, stringent environmental controls are implemented to capture minuscule dust particles, mitigating potential health risks. An air system specifically collects and filters out fine dust particles to protect worker health and essentially eliminate potential combustive risk.
For optimal results, additional adjustment or customization may be required based on the recycler’s specific location, process, and expected LED volumes.
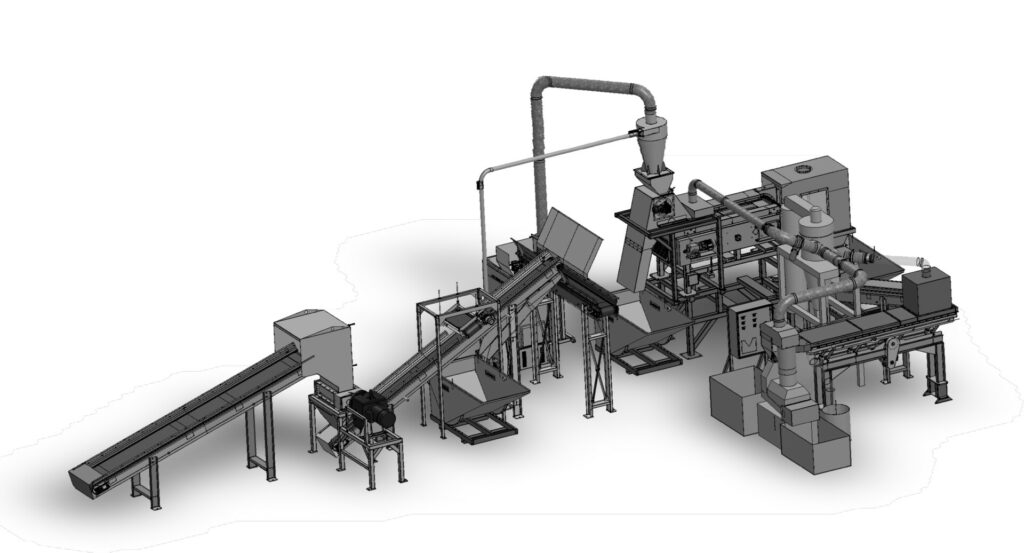
“To achieve greater volumes, modifying the shredder size is often necessary. However, from an engineering perspective, it can be challenging to precisely adjust, measure, and accommodate the tonnage and quality of each material without a thorough understanding of the system. Several factors, including chamber size, RPMs, variable frequency drives, and software programming changes, come into play. This necessitates comprehensive system integration,” says Neuens.
BCA spent a month setting up, testing, and fine-tuning the recycler’s LED processing system, making various adjustments and enhancements to customize it according to their specific requirements.
“These new systems are specifically built to efficiently recycle LEDs from initial feed to controlling the plant environment, all the way to producing the maximum amount of salable material, including ferrous metals, aluminum, copper, light plastic, heavy plastic and glass, when separation is complete,” says Neuens. “Most of the material we recover is an eighth of an inch to a quarter of an inch and can be recycled for use in other areas.”
One example is glass, which can be used in shot peening to clean and finish metals or other surfaces less aggressively than sandblasting.
According to Neuens, fully integrating the system to meet the recycler’s needs is also a top priority. To this end, the OEM conducted Factory Acceptance Testing (FAT) to verify that newly manufactured equipment met its intended purpose, as well as Site Acceptance Testing (SAT) to ensure that the system performed as required at the specific location.
“Recyclers want a complete, integrated LED material recovery system backed by a manufacturer’s warranty. They want a single developer and one phone number to call to quickly resolve any problems,” says Neuens.
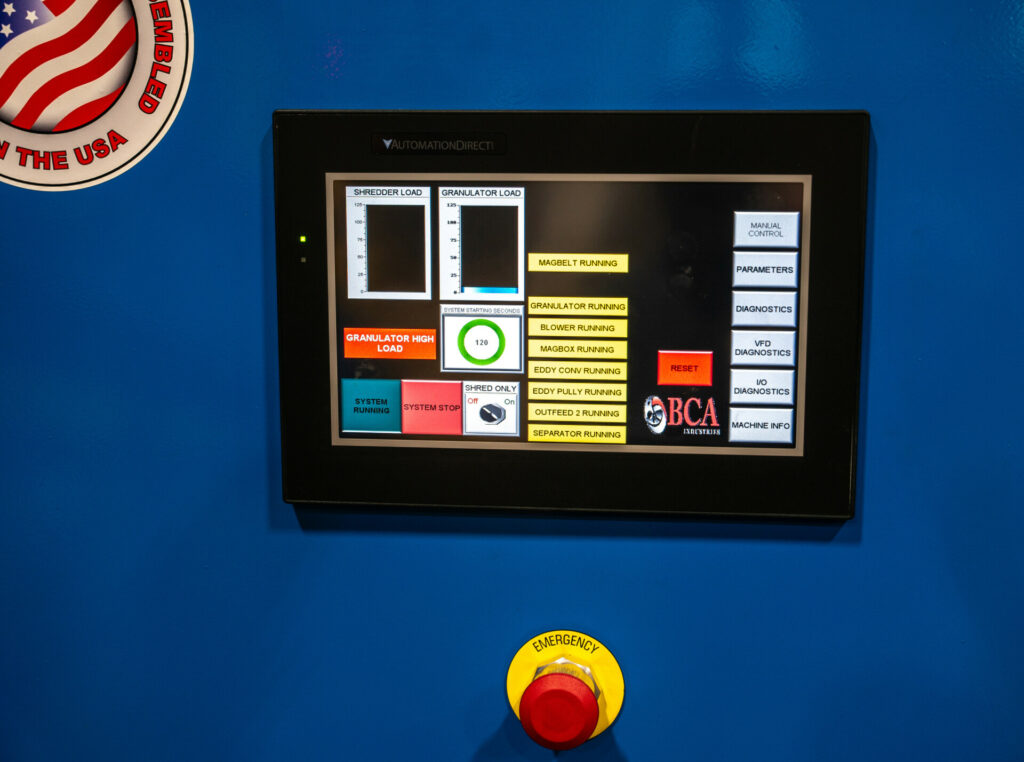
To minimize issues and expedite maintenance and training for those who purchase the LED recovery system, BCA offers comprehensive walk-through videos that provide detailed guidance. This helps to prevent the loss of critical knowledge that can occur when experienced personnel leave. Watching the tutorials also facilitates getting any new employees quickly up to speed on using the equipment.
According to Neuens, the designers “walk through” every element of the machine and system, including operation, maintenance, safety, and programming. They point out how to properly operate the equipment, what needs to be greased/oiled, and what the fluid levels should be. They not only teach important safety tips, but also what the software fault codes are and how to correct the issue.
“Our tutorial videos can be very specific, down to how to change knives, how to tune a machine, and what to look for if a valve goes bad,” says Neuens.
As the use of LED lighting continues to grow worldwide, the need to efficiently accommodate the volumes of bulbs to be recycled will only increase. Recyclers that quickly adopt fully integrated, LED-specific recycling systems will find that their fortunes will rise with the increased demand far into the future.