In the vast field of recycling, the variations of materials, size, processes, and desired outputs can be virtually endless. In addition to paper, plastic bottles, and aluminum cans, industrial recycling can include electronics, LEDs, batteries, catalytic converters, precious metals, medical supplies, construction materials, and more. Today, EV batteries can be nearly as large as the vehicle and laden with valuable materials to reclaim. Even outdated military ammunition and equipment needs to be safely recycled.
“There is so much variability in recycling material, size, and processes that each shredding system really needs to be customized to meet the requirements of a specific application, with consideration of the desired throughput and profitability objectives,” says John Neuens, Industrial Consultant, BCA Industries. The OEM provides complete custom recycling systems for complex industrial and commercial applications.
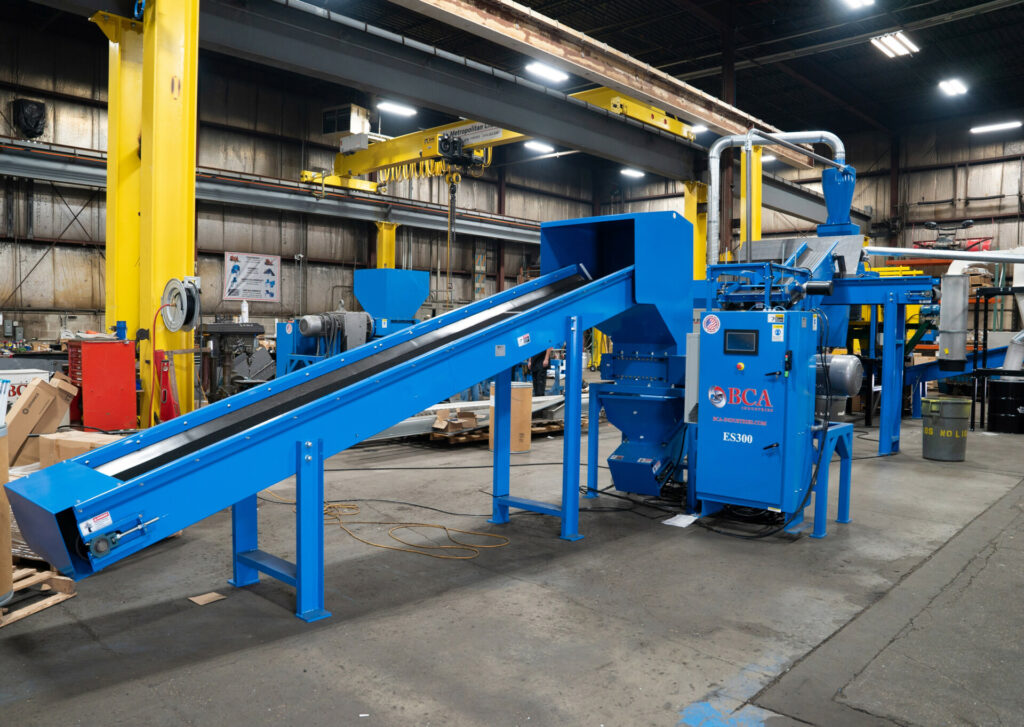
Complicating matters, recycling equipment providers often manufacture only segments of a complete system, necessitating the involvement of engineering firms for the specification and assembly of component parts into a cohesive shredding system.
However, this can lead to a “Frankenstein” system that never works as intended and requires extensive troubleshooting. The system may even lack the necessary reliability and safety standards. When multiple equipment sources are utilized, technical issues can devolve into “finger pointing” and blaming others.
“For optimal efficiency, the shredding system should be designed by a single supplier to ensure seamless coordination and communication among the system’s component parts for achieving the desired output,” says Neuens.
According to Neuens, ongoing technical support and maintenance is also required post-installation. It is common for recyclers to reach out months or years later with the desire to process new materials, many of which have different dimensions and feedstock.
“A single point of contact and accountability is really necessary to design and maintain a custom [recycling] system for optimal productivity throughout its lifespan,” says Neuens.
Complex Systems Require Customization
The need for a recycling system often begins with just an idea of the material that requires shredding. However, the ultimate requirements may involve a complex process of reduction, separation, and destruction – with many steps repeated. Given the array of potential outcomes, Neuens estimates BCA has the capability to design and manufacture literally thousands of shredder systems when considering all the potential markets.
Although BCA frequently collaborates with engineering firms on large projects, the OEM’s in-house engineering staff can design a complete recycling system that meets the specific requirements of the materials, throughput, and profitability.
“Naturally, customers are looking for durable, quality recycling equipment at a reasonable cost, but the primary reason we are hired is because of our critical thinking [about shredder design], as well as our in-house design and manufacturing capabilities,” says Neuens. BCA’s client roster includes Fortune 500 companies in sectors such as aerospace, automotive, electronics, energy, and consumer goods. The OEM also serves the U.S. Army and Air Force, as well as some of the world’s largest recyclers.
“Working with diverse manufacturers over the years has presented complex problems requiring unique solutions,” says Neuens. “Each time we’ve worked with a different material or a novel recycling situation, we’ve learned something and applied the lesson to the next project.”
Accommodating Process Complexity
Designing and manufacturing a recycling system is particularly challenging when large packages or assembled structures must be efficiently shredded. In the case of EV batteries, the recycler may start with a structure as large as eight feet long, four feet wide, and one foot thick filled with cells.
According to Neuens, the first goal is to separate and reduce the material to a more manageable size. To facilitate this task, the OEM may use vibratory conveyors, which help to separate the packing material from the product and promote feed regularity.
The vibratory conveyors often move partially separated materials to shredders designed to provide primary destruction. A second or even third shredder may be required to reduce the material to achieve the required minimal size.
The material is then separated using various techniques. For example, ferrous materials may be separated using stationary overhead, head pulley, or cross belt magnets. While a magnetic separator may not capture all stainless steel, BCA employs rare earth magnets to attract and capture a significant percentage.
Non-ferrous metals such as copper and aluminum can be effectively separated using a combination of density separation and eddy current separators. Density separation differentiates materials according to varying weights, while eddy current separators utilize a robust magnetic field for the separation of non-ferrous metals from a waste stream.
When very fine material sizes are required, such as 10-20 mesh, granulator or turbo mill systems can be utilized. For rubber, a cracker mill with chilled roller is used for breaking apart, plasticizing and mixing rubber materials.
Even if reduced to small sizes, efficient recycling necessitates the production of uniformly sized materials to facilitate the separation process.
For this task, BCA often implements its patented Triplus knife system technology, which uses the precision grabbing action of the high torque, dual shaft shredder to cut the width of the material, while the bed knife design of the shredder sizes the length. This is accomplished in one operation, which produces accurately sized material in one pass without a screen. The end-product size is based on the size and geometry of the knives.
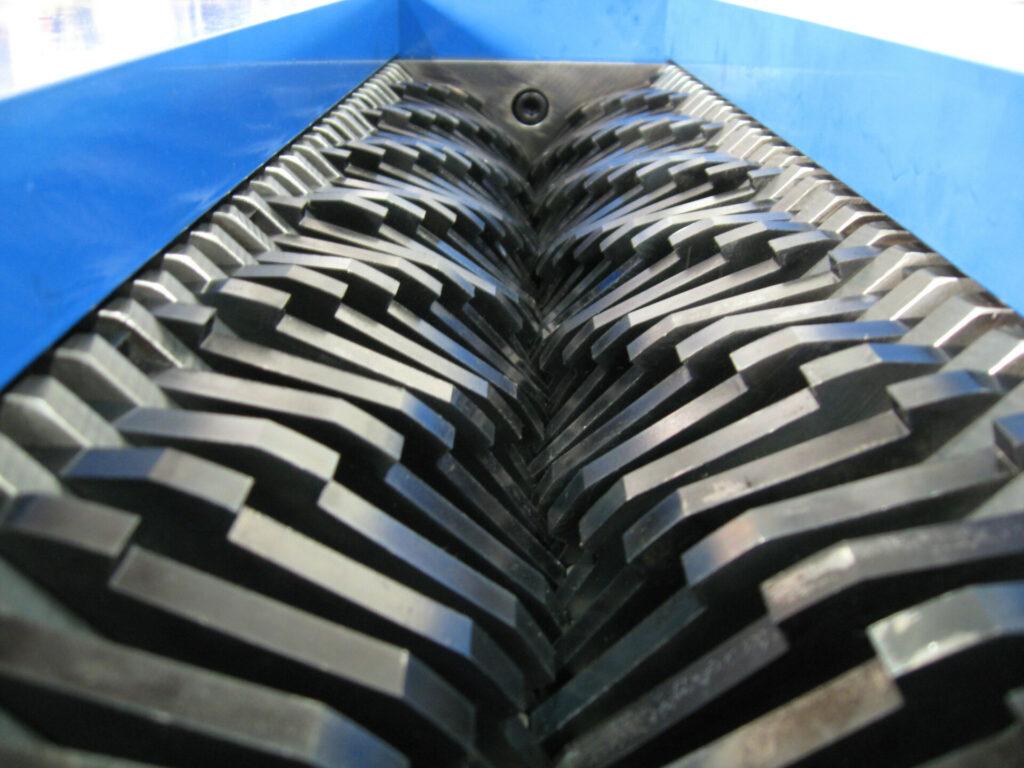
Unlike traditional equipment, the knife system is capable of shredding, chipping, and sizing a wide range of material types and sizes in a single pass without using a screen. A shredder utilizing this design can produce over 85% correctly sized material in one pass with less than 10% oversized material and a tiny percentage of fines.
Neuens adds that it is also important to consider how the material will be packaged for shipping. This could involve totes, steel drums, super sack bags, or even open-top truck trailers. “The outfeed system needs to be designed to accommodate how the client wants to ship the material,” says Neuens.
Ensuring seamless integration and communication among all component parts through the PLC-based control system with user-friendly touchscreen interfaces is a critical challenge in shredding system design.
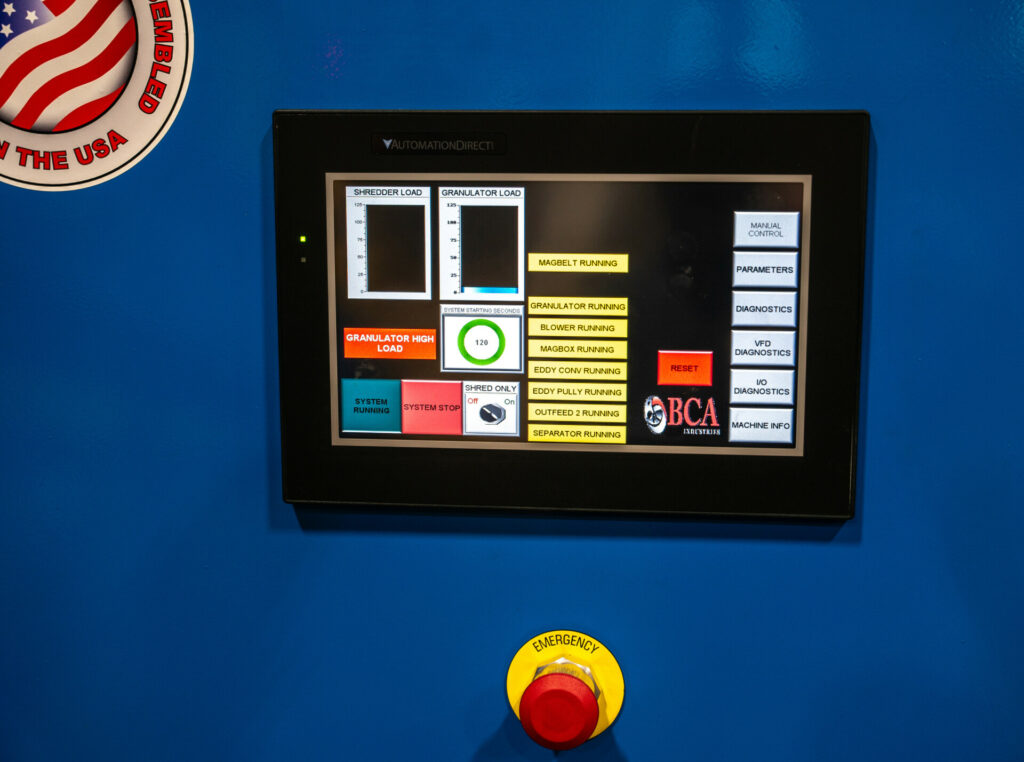
“Engaging a third-party to develop a control system becomes significantly more challenging and costly when the component parts are sourced from multiple manufacturers,” says Neuens, adding that BCA programs the PLCs and provides a copy of the software to the system owner so it can be reprogrammed in the future, if needed.
A quality system includes programmable software to adapt the system for various input types and materials.
“When it comes to recycling batteries, the process varies depending on the size of the battery packs or individual cells being handled. To optimize the system effectively, programming software is essential to accommodate for this variability,” says Neuens.
Post Installation Modifications and Support
Successful system implementation would ideally extend to simplifying maintenance and operator training post-installation as well. As part of their service, BCA trains operators and creates online video manuals to expedite the productivity of new users.
“We do our best to ‘futureproof’ the system to ensure there is continuity if a trained employee suddenly leaves,” says Neuens.
This entails being prepared to make adjustments when customers reach out in the future to modify the system for new material types or sizes, which is a common request.
“Often the customer doesn’t know what the future holds in terms of recycling,” says Neuens, adding that it is common for recyclers to start with one feedstock and then request processing of additional materials of different types, sizes, or geometries.
Implementing system changes may not be as straightforward as customers perceive.
“If a system is initially designed for processing specific feedstock, customers might seek to modify it to handle tougher materials or larger sizes. This adaptation could necessitate intricate adjustments across various aspects of the system to accommodate such changes. Potential modifications might include upgrading to a larger shredder, chamber, or knives,” says Neuens.
Even the seemingly straightforward decision to switch to a hopper of a different size can pose challenges.
“The geometry of the hopper significantly impacts performance. The hopper plays a crucial role in material orientation during the feeding process and therefore must be properly implemented,” says Neuens.
In the industrial sector, the complexities of modern recycling demand an approach that prioritizes integration and customization. The variability in materials and processes calls for recycling systems that are not only tailored to specific applications but also maintained as cohesive units.
By consolidating design, installation, and ongoing support with one provider, companies can streamline operations, reduce troubleshooting, and adapt more readily to evolving materials and processing requirements. Taking this approach will not only optimize productivity and ROI but also ensure that recycling efforts are sustainable and future ready.
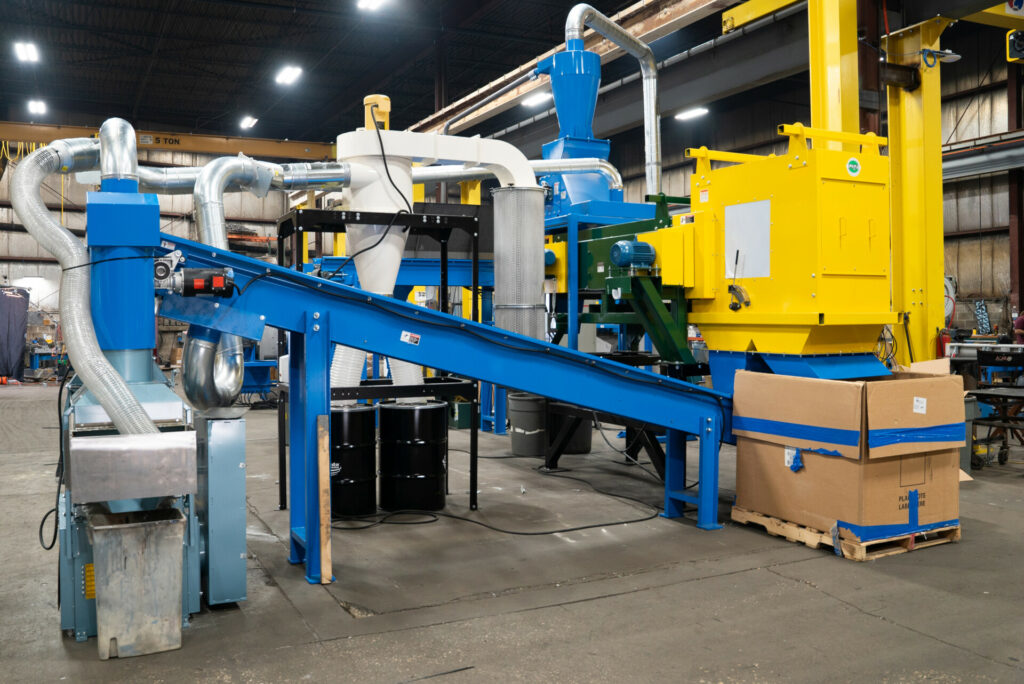