The production waste that accumulates is shredded and recycled with a powerful 160 kW WEIMA WLK 30 Super Jumbo single-shaft shredder so that it can be integrated back into the manufacturing process.
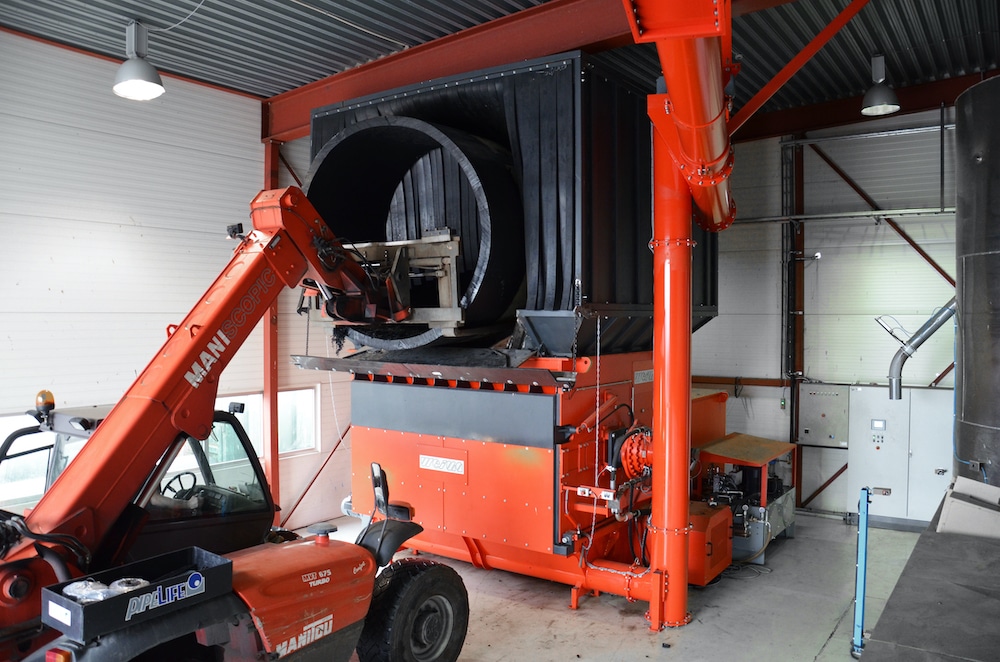
The Pipelife location in Stathelle stands out prominently from a great distance. The reason for this is the deep black pipes up to 500 meters long floating in the middle of a picturesque Norwegian fjord. Primarily for reasons of space, the pipes are extruded directly out onto the open water. They are stored there until they are picked up for delivery by maritime shipping. This is not an everyday event and it usually draws many curious onlookers who come and celebrate the completion of the process. This is how to present a true mammoth project!
Before, voluminous pipe waste had to be painstakingly cut into DIN A3-size pieces by employees with chain saws and then packed onto pallets to be transported away. The mountains of waste were growing steadily and taking up valuable storage space. A solution had to be found for the problem as quickly as possible. Finally, they came across the experienced shredding specialist WEIMA from Ilsfeld, Germany, who had already successfully implemented similar projects in Asia.
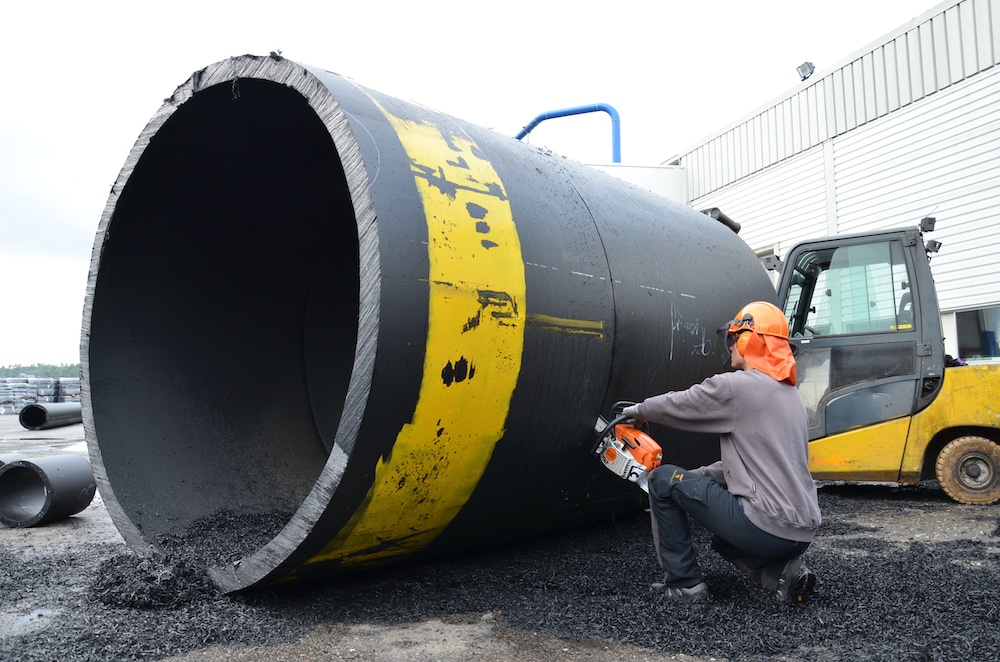
The way to achieve the objective was clear: First, shred pipe pieces that could no longer be used with the WEIMA WLK 30 Super Jumbo shredder. Then supply the shredded material via a screw conveyor to a granulator. The extruder used after this, which includes drying, ultimately converts old PE plastic waste into recycled regranulate, which in turn can be supplied into the raw material cycle. It is stored in giant silos on the company grounds. Nothing goes to waste in this sustainable solution.
The shredding process is both simple and ingenious. To keep the effort required as low as possible, the feed hopper was dimensioned so that even pipeline sections 2.5 meters in diameter could be loaded into the shredder in one piece with a forklift truck. The rest is taken care of by the innovative, high-throughput V rotor, fitted with 135 cutting blades, which reduces the 10 cm thick pipe walls to pieces no larger than 50 mm.
The steel colossus is driven by WEIMA’s powerful 160 kW hydraulic drive. Stopping, starting, and reversing is possible at any time, even under the most difficult conditions and at full load. With its simple design and fast response time, the hydraulic drive is nearly insensitive to foreign objects. Extremely high torques and the rotational speed can be adjusted flexibly, quickly, uniformly, and steplessly, without creating power peaks and without having to use a frequency inverter. Due to the low connected load with the same or higher throughput, less electrical power is required, which makes it possible to reduce operating costs overall.
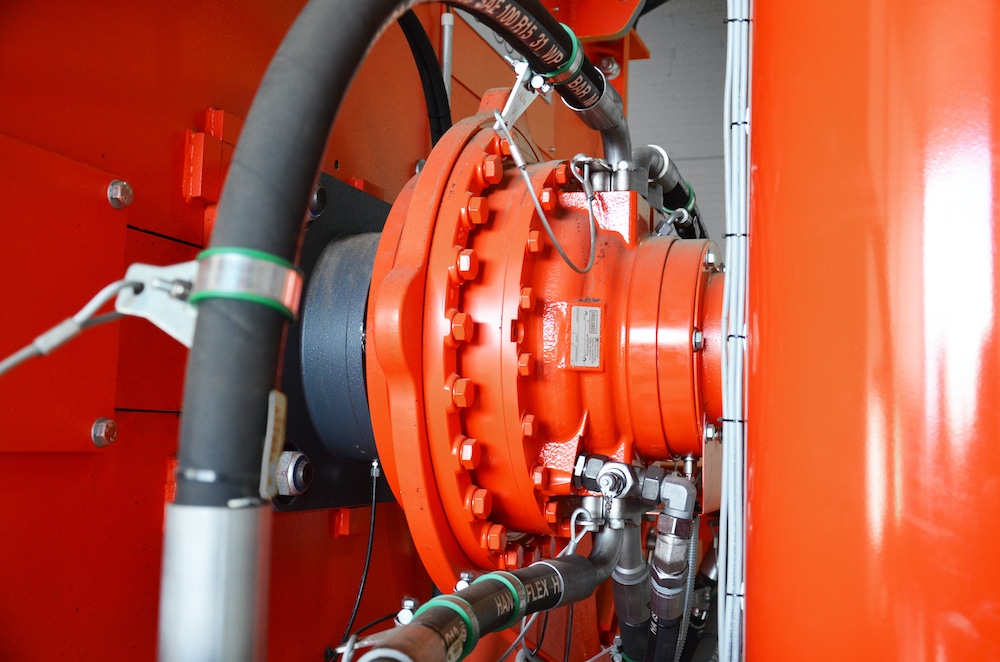
Reconditioning PE waste has benefits beyond financial considerations. This technological advantage provides impressive confirmation of the company’s vision of continuously improving “the quality of life through innovative and highly effective solutions to protect water and energy“. As WEIMA sees it, everything fits together perfectly.