As a well-respected and established waste company, located in the West Country, their proven track record gave them the confidence that they could provide both a sterling service and an excellent secondary commodity product.
Although they had the necessary network, systems and key personnel in place, the existing processing machinery limited their ambitions.
Formerly known as Polymer Industries, DCW Polymers are set to increase recycling rates across the South West, continuing to produce high-quality plastic materials to turn into new products.
A Clear Vision
Jason Goozee, Commodities Manager, at DCW Polymers identified labor-intensive processes and process bottlenecks as barriers to scaling up their operations. To this end he engaged with the market, speaking with various suppliers of size reduction equipment.
Armed with a clear brief, to process in excess of 1,000kg per hour of rigid, end of life, plastic product (in the form of full-sized wheelie bins, trays and pipe), to produce high-quality granulated flake.
After a series of offers, DCW Polymers contacted FERCELL to design, supply, install and support a comprehensive size reduction system.
Despite, some extremely competitive pricing from Asian suppliers, DCW Polymers felt that FERCELL’s offer represented a higher level of efficiency and effectiveness and that their implementation method delivered a lower total investment cost, over the life of the plant, and more flexibility during the deployment of the project.
Proposing a Solution
Although DCW Polymers’ aim was to produce quality plastic granules, a multi-stage system was proposed, in which a shredder would do part of the size reduction work, delivering smaller, pre-shred to the granulator. Such an arrangement decreases the load on the granulator while extending the life of the cutting tools, which require less frequent blade turning and sharpening.
The multi-stage system enables the system to be operated in bulk or batch, with minimal operator involvement, you can simply fill the shredder hopper and walk away. It has seamless control for communication between the shredder and the granulator, and its ‘Stop-Go’ technology means pre-shred material is metered into the granulator.
DCW Polymers share the same concerns as the majority of FERCELL’s clients, who demand extra features to deliver higher output, lower energy consumption, noise reduction and extended service life. As such FERCELL base their system designs on the principle of marrying the perfect size, highest energy-efficient, motors with the most advanced cutting configuration to deliver optimized profitability.
Due to limitations with the electrical supply on-site, a dedicated generator was required. FERCELL liaised with DCW Polymers specialist electrical contractor, providing the data for the selection of the optimum kVA generator.
Once, the installation details and plans had been signed off the component parts went into production.
Delivery Time
After a period of excited anticipation, the day of the scheduled delivery arrived. The system arrived in a good time waiting to be lifted by crane and maneuvered into position. The whole process of unloading by crane, assembly, and positioning took less than 10 hours. With the entire installation completed within 24 hours, across three days.
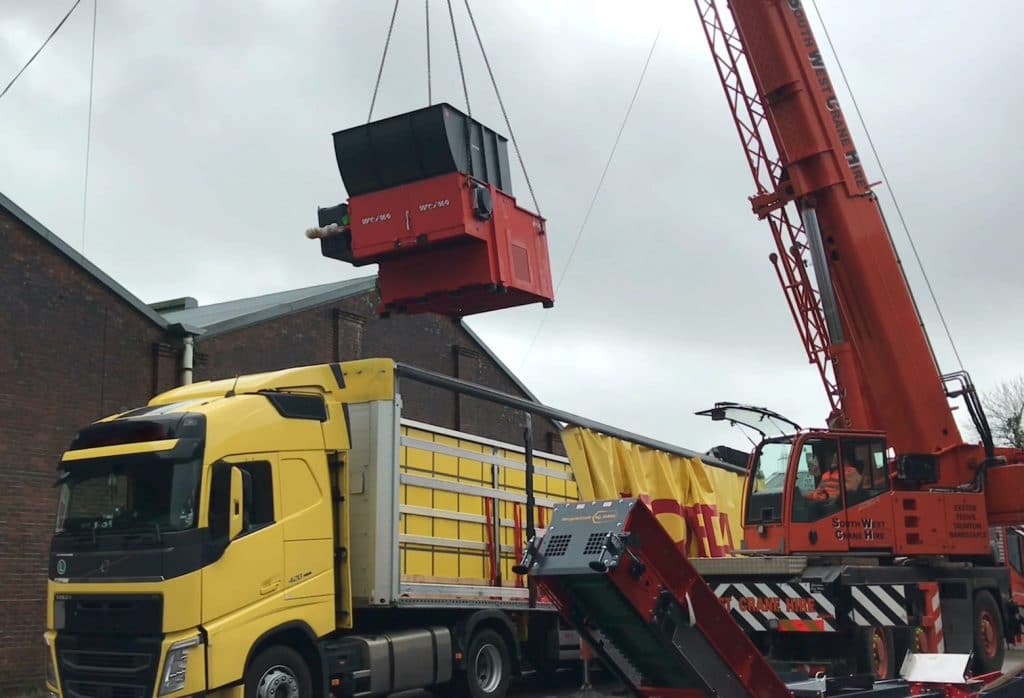
At the end of it, DCW Polymers had a comprehensive system, consisting of a WEIMA WLK1500/75 single-shaft shredder, swan-neck outfeed conveyor (with permanent drum magnet and overband magnetic separation facilities), NEUE-HERBOLD LM600/1000/90 granulator, FERCELL air-handling system, various gantries and platforms, and failsafe control system.
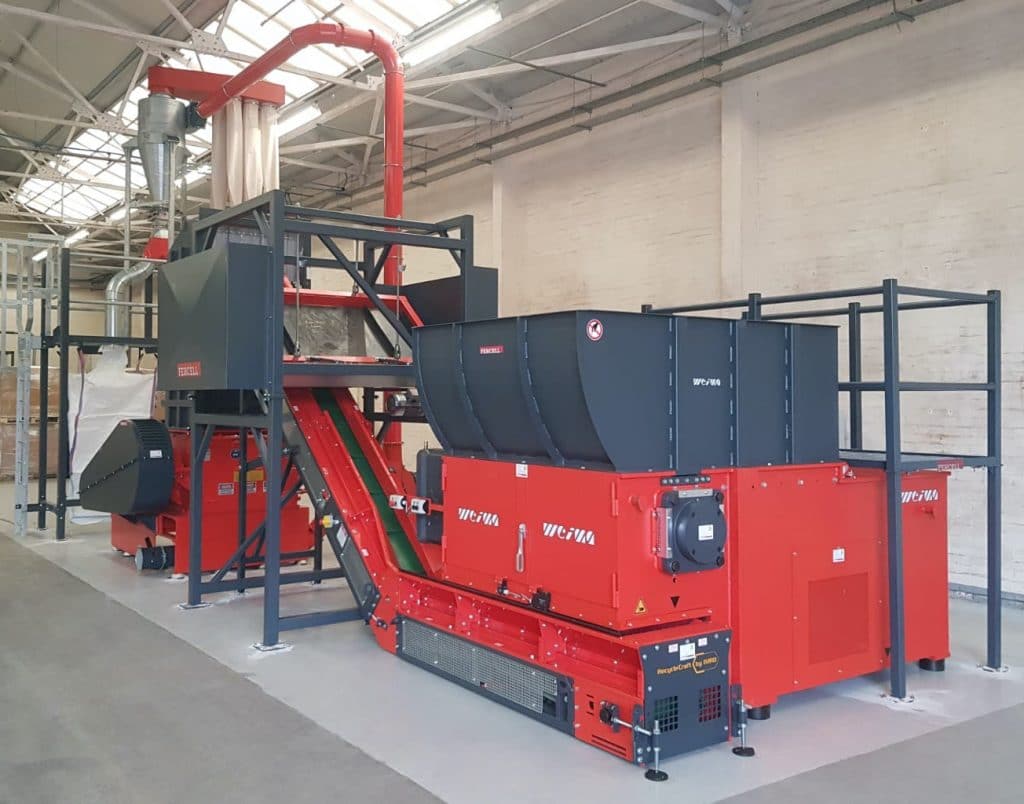
How it Works
The WLK-Series are the plastics workhorse of the WEIMA single-shaft range of shredders designed for high throughput rates, shredding almost all types of plastic, including purge, automotive scrap, pipes, blow-molded materials (PE/PET/PP bottles, buckets, and containers). With an operating width of 1.5m, the WLK1500/75 at DCW is capable of taking all of their process materials without the need to first reduce in size, which they were doing manually, by bandsaw, improving safety and capacities. The WLK1500 was specified with ‘large-format’, four-side, cutting tools because of the specific resilience to metal contamination.
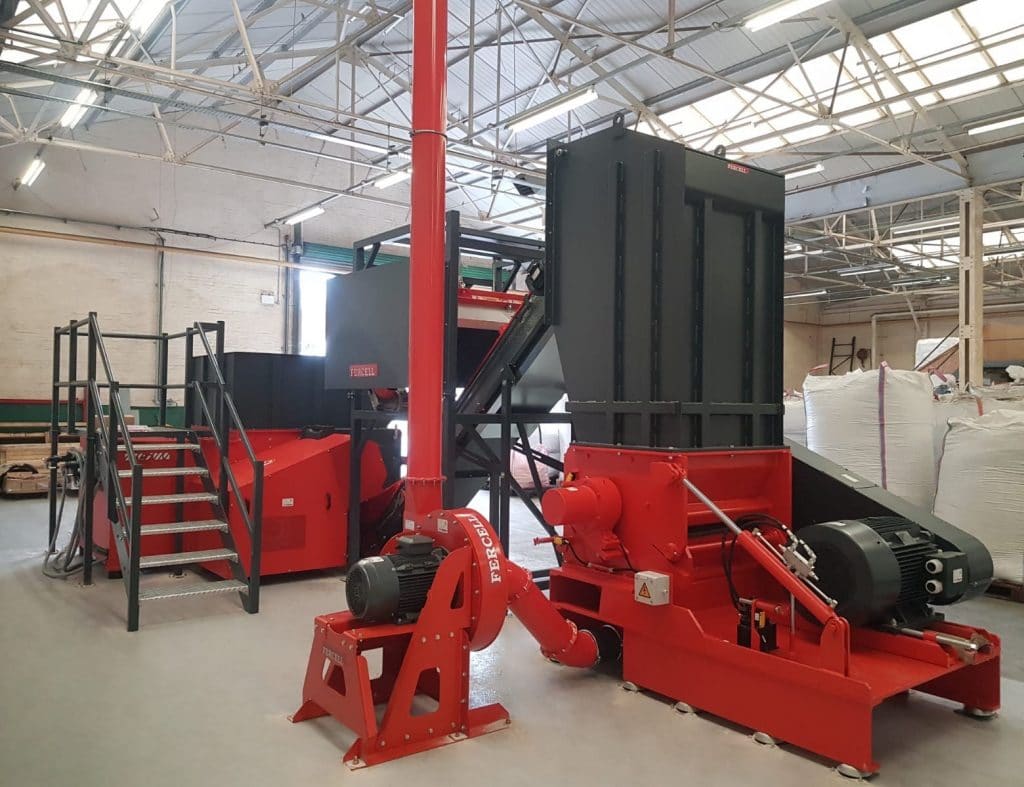
The LM-Series is designed and manufactured specifically as a heavy-duty option, with the ability to granulate pre-shredded material to sizes from 4,0mm to 12,0mm and process from 250 to 2,500 Kgs per hour (subject to the machine size, material type, and screen size). Clients looking to granulate at higher throughputs are served by the SM-Series, which can process up to 8,000 Kgs per hour.
FERCELL have deployed the LM and SM-Series in different configurations, including stacked, where the granulator sits beneath the shredder to provide maximum throughput capacity, and horizontal when there are metal contamination risks, and effective metal detection and separation facilities are essential to protect the granulator. DCW Polymers uses a horizontal configuration, which has a three-stage metal separation, drum, belt and grid.
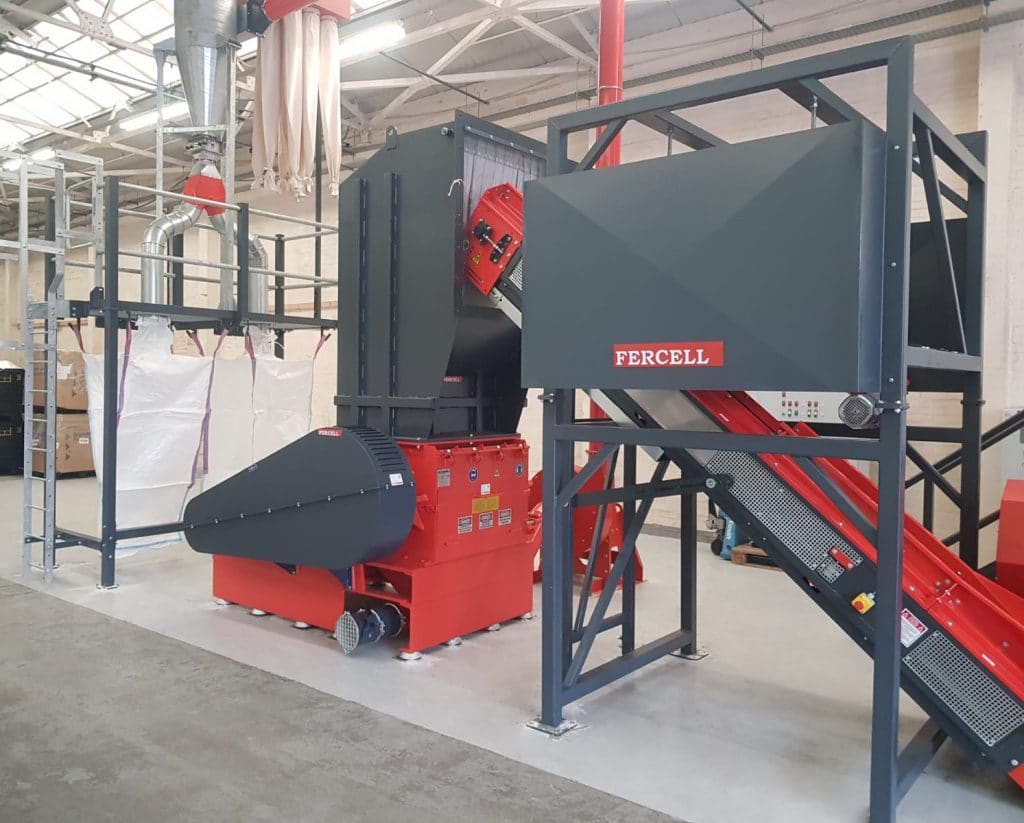
Following the connection of the services, one of FERCELL’s factory-trained engineers returned to the site where they completed the cold/hot testing, plant commissioning, and operator training.
The recycling system installed is capable of processing more than 100 tonnes of plastic a week, which will allow DCW to turn bulky plastic items such as fuel tanks, crates, and old play equipment into plastic granules that can be used again for manufacturing.