There is an ideology that glass is infinitely recyclable and can be made into new glass repeatedly without degrading its quality. Even though this may be possible in an ideal world, the realities are far more challenging than this message suggests. The public, industry, and even Government have consistently been misinformed and ill-advised as to what is realistic and practical. The industry faces many challenges, but none greater than misinformation. It is a technical impossibility for all used glass to be considered as furnace ready feedstock, this is grossly misleading in so many ways resulting in a large percentage of waste glass ending up in landfills as a daily cover or used as a low-value aggregate substitute.
People need to understand the whole recycling process, its challenges, regionality, and of course which technologies are available and capable of processing 100% of all incoming glass, significantly enhancing the quality of all waste glass, not just that considered as Remelt feedstock. Promoting the use of the cullet as being low CO2 is misleading, the reality is the CO2 is calculated as arriving at the furnace with no CO2 footprint from its recovery, reprocessing, or disposal of glass not suitable for Remelt.
All Remelt furnaces require high-quality feedstock to minimize rejects and maintain quality. Almost all used glass containers have some form of label, cap, seal, or sleeve. For an optical sorter to operate the glass bottle must be broken, labels removed or abraded, and necks crushed to remove sealing rings and caps. This action of breaking and crushing creates a quantity of glass too small for cost-effective optical color sorting. At the most basic level of processing and recovery, the message of the ‘the only true glass recycling is bottle to bottle’ is already challenged.
There are many other factors that challenge the cost-effectiveness of producing furnace-ready cullet such as Furnace capacity, distance, collection strategies, MRF design, quality, and value. In almost all cases it is the low value of glass that determines its status within the waste hierarchy. Currently, most collection systems and MRF lines consider glass as a low-value material and treat it accordingly, often removing it early in the process along with heavily contaminated rejected materials. Often this material is sieved at 12mm (1/2”) to remove the fines for landfill daily cover and the remainder is sent for further cleaning, processing, and recovery.
Clearly, source-segregated glass collections are the best way of maintaining glass quality, but the costs are often too high to be economically viable, while all the time glass has a low or negative value. It is this vicious cycle that is a factor in holding back the development of glass recycling. To increase the uptake of glass collection and remove the glass from MRF, 100% of the incoming glass must be adequately monetized to warrant the investment.
Spain, Portugal, China, and Thailand are a few countries that have a Remelt capacity equal to its consumption. Often a country will produce a bottle color that is different to that of the containers being imported, whether that be green for wine or amber for beer, a perfect example of a mismatch between Remelt capacity and glass consumption is that of the USA. With a conservative Remelt capacity of circa 5 million tonnes across all states and consumers generating 12.5 million tonnes of waste container glass annually there will always be challenges for any recycler.
It is unfortunate the public, Industry and legislators believe ‘bottle to bottle’ is the only true recycling. Inevitably with such disparity between demand and supply in the glass recycling system, like most other countries around the world the USA finds itself in crisis with the vast majority of the 7.5m tonnes surplus going to low-value aggregates or landfills as landfill daily cover.
Things are no different in the UK, despite current statistics showing the UK has an excellent recycling rate of 68.8%, in actual fact of the 2.3m tonnes of waste glass produced, 750k tonnes is used to create new containers in the UK, 600k is exported “to be recycled” the remainder as landfill daily cover or aggregates. The figure of 68.8% is based on the glass being considered to have been recycled if it has gone through a recycling plant and has been weighed on the weighbridge, not that it has been used in the creation of another product. Additionally, in the UK landfill gate fees are averaging £125 ($160) per tonne. However, like in so many other countries because glass is technically inert it is allowed for use as landfill daily cover and this reduces disposal at landfills to a little over £15 ($20) per tonne! Such a low gate fee is seen as an economically viable option by many for the cullet that cannot be used by the Remelt industry.
It is plain to see from these two examples that supply and demand are not and cannot be matched to Remelt. In the UK this could be further exacerbated in 2021 when tariffs may apply on exported material destined for consumption in the EU.
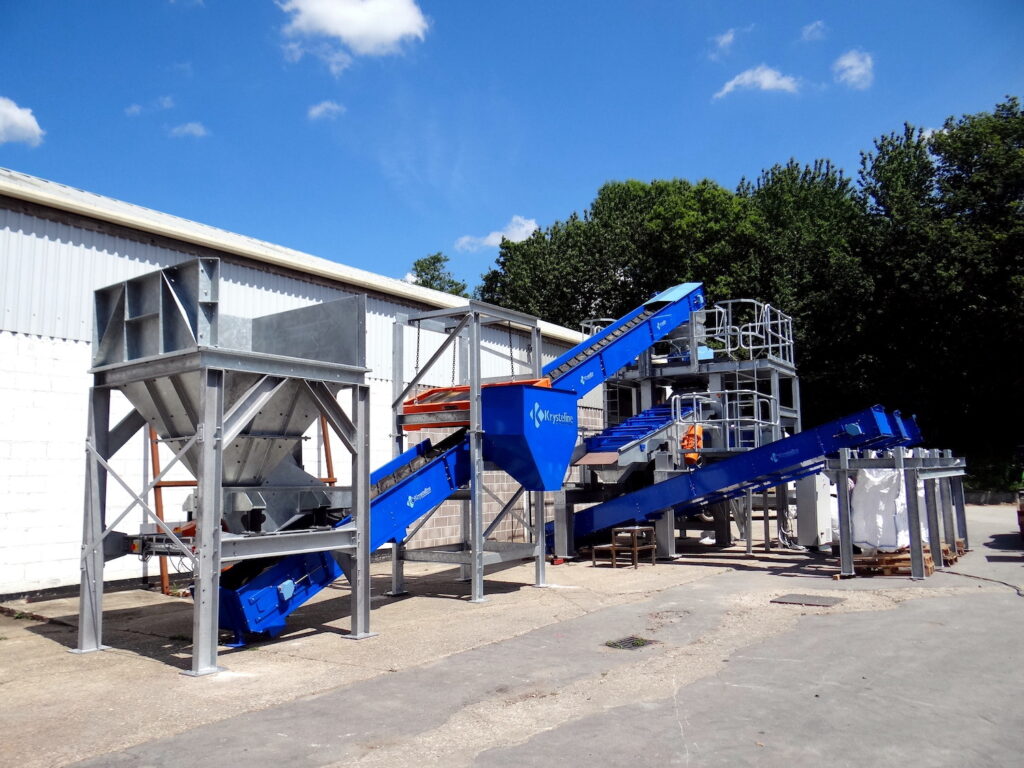
The Challenge
The price per tonne paid by the Remelt industry is proportionally low compared to say plastic, but the processing costs may often be higher. In most cases, any glass recycler is operating on very slim margins which limits investment in new technologies which could reach new, non-Remelt markets. Resulting in landfill daily cover being the lowest cost route of disposal, something which is rarely admitted by the industry or legislators.
The glass that cannot be used for Remelt is often sized <12mm (1/2”) and comingled with Ceramic, Stone, and Porcelain (CSP). This glass is certainly the most challenging aspect of glass recycling due to its high levels of multi-product contaminants and difficulty to be optically color sorted.
It is evidently clear it is key for glass to be in a quality appropriate for its intended marketplace for an effective recycling program to exist. Many recycling programs are mandated for a percentage of glass recovered to go to Remelt. Where there is no Remelt site within economic distance such an ill-conceived contract challenges the economics of any recycling program and often creates a negative CO2 footprint. In no way is it suggested that glass should not be going to Remelt, just the right glass at the right price in the right location.
An efficient glass recycling plan or strategy requires the buy-in of multiple end-users, producers, cullet users, collectors, recyclers, and of course Government. Often this is the case, but the message is of course ‘glass to glass’ which suits the Remelt industry but handicaps all other industries as well as the recycler. To convert all glass there is a need to work with stakeholders to re-focus glass recycling towards the process of ‘economic recovery and re-use of ALL waste glass.’
So, what is the Solution?
Achieving a significantly higher recycling rate and one which commands lower CO2 across all uses requires several strategic changes. Clearly, the marketing message needs updating to be more realistic and inclusive.
Any new strategy must consider landfill daily cover as just landfill. As with any well-conceived strategy, economic viability must be at its forefront. When landfill daily cover is considered recycling there needs to be some serious change! The UK has a well-conceived PRN system where revenue can be generated to help cover the processing costs. In recent times the PRN has been broken down into Remelt and Non-Remelt, following the narrative that in some way Non-Remelt was holding back the value of PRNs, time has proven this not to be correct. In the past PRNs have been issued against the simple crushing of glass as a material suitable for subbase, with little care for quality or cleanliness. It would make sense for this material to have a lower PRN value. However, for markets that require sizeable investments, often greater than that required for cullet, the PRN value should be higher. Surely it should be the true CO2 value that determines the PRN value. Having a clear indication of the CO2 footprint of recycled glass at its various stages will undoubtedly help industrial partners increase their use of recycled products and decrease their own CO2 footprint.
If CO2 is a major factor in any business strategy, does it not make more sense for the CO2 footprint of any recycled product to determine its value? If the PRN value increases as the CO2 footprint decreases it will surely increase the potential for strategic investment into technology that can process and recycle all glass, not just a proportion.
For example, if there isn’t a Remelt furnace in reasonable proximity to the MRF then surely other marketplaces for the waste glass (where it can be used locally) should be seen as being low CO2. But, how do we stimulate interest in alternative products to fuel such a system?
Currently, there is no independent body/organization which is focused on the development of the whole glass industry. As always R&D, and the associated Universities and Industrial Partners, are imperative in any successful market development. Considerable work in the commercialization of glass sand for Cement is one great example of how the industry has cooperated with Universities and the Government to create a low CO2 product that has pent up demand.
As always, the gap between where we are today and what industrial partners want in the future is one that investors find challenging. It takes vision and tenacity to seize an opportunity, change how society thinks and create a strategy more fitting for a modern world.
Technology is evolving fast, Optical sorters are improving their efficiency but still struggle with the economical separation of the smaller sizes. The <12mm material has always been the challenge, its diversity of contaminating, variable moisture content as well as putrescible content challenge most systems. These difficult materials challenge Industry to evolve, establish new technology, challenge the norm, and create low CO2 products from material previously only considered suitable for landfill daily cover.
A higher quality standard than PAS 102 could lead to terracing of product quality, PRN & CO2 values and support a system where industry cooperates with legislators to develop products and create demand. Creating an independent glass authority could provide the conduit between industry, the recyclers, and investors.
Focusing on End Markets
Establishing and developing economic markets for the <12mm (1/2”) glass with a low CO2 footprint is driving innovation. A few examples of products are:
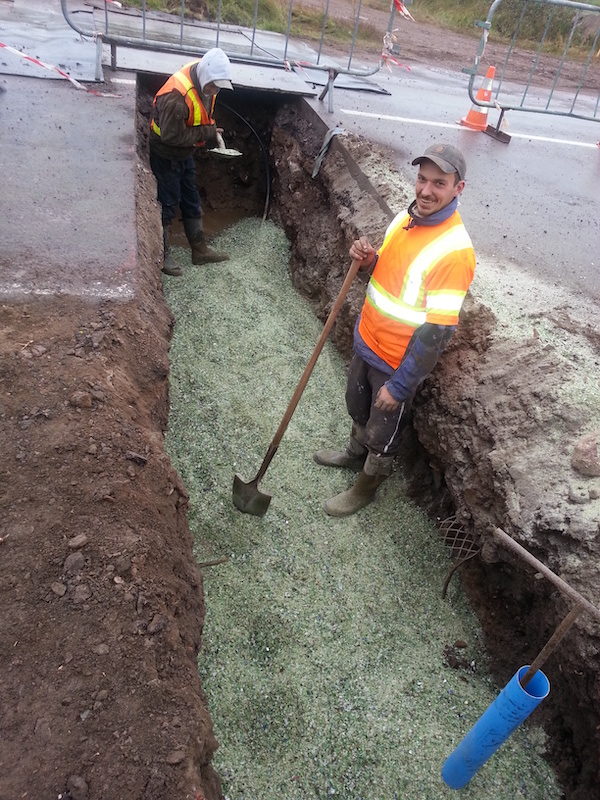
- Cementitious materials, as supplements to Ordinary Portland Cement (OPC)
- Silicon Fertilizers
- Foam glass
- Fibreglass & Glass wool
- Asphalt sand
- Water filtration
- Expendable abrasive
- Fillers for plastic, paint, adhesives, mastic and caulking
Additionally, in many locations and Islands around the world, no Remelt industry exists, and exporting is prohibitive. Creating sustainability and employment by creating an aggregate substitute for French drains, trench fill, and pre-cast concrete blocks is low CO2 use of waste glass in these areas. A well-conceived cost-effective plant will produce quality aggregates to replace marine sand often the cause of ASR in concrete due to its high salinity.
Krysteline Strategy
The start point of any recycling initiative in any country or region should be the capability to recycle effectively while establishing a variety of markets across a broad spectrum of industries to create a stable platform and revenue stream.
Our technology is developed from a different perspective than others. We sought solutions for the enhancement of the most challenging glass in the waste stream, recovering and refining glass that cannot be used in the Remelt industry. A comprehensive range of technologies provides processing plants and solutions for a diverse global market.
Krysteline’s technology and strategy are in no way designed to use Remelt cullet as feedstock for other marketplaces, in fact, our strategic partnership with PICVISA is proof we consider all-glass equally in each project and are committed to long term sustainability of a process that creates ultra-high quality cullet for Remelt through our innovative glass clean-up systems which enhance cullet quality prior to optical sorting.
Krysteline understands for some people, producing non-Remelt could be considered detrimental. But it is clearly a greater understanding of the current system and the issues it faces is vital for its very survival. It’s time to develop a more inclusive strategy one of ‘Glass recycling, the process of economic recovery and use of ALL waste glass’.