The reintroduction of recyclate into the production cycle makes an important contribution to environmental protection, especially in times of increasing scarcity of resources. For this reason, many consumer goods and consumable products made with plastic, such as PVC windows, PET beverage bottles, old cables, electrical appliance housings, among others, are collected, shredded, sorted, and recycled at the end of their service life. The aim is to recover as high a proportion as possible of recyclable materials contained in these goods. This applies equally to waste and rejects arising from production.
Mechanical recycling often fails, however, because the plastics are present as a mixture of materials. As a rule, only pure plastic fractions, i.e. neither mixed nor contaminated ones, can be introduced into the production cycle in an ecologically sensible and economically reasonable manner.
Many processes for the production of pure plastic fractions from recycled materials have become established in recent years. Nevertheless, there are still numerous plastic mixtures that cannot be separated at all, or only with low economic efficiency, when using common separation methods such as density separation or optical sorting. This is because many mixtures of different plastic materials contain plastics that have the same specific weight, color, and mechanical behavior.
By using electrostatic separation and systems, valuable raw materials can be recovered from many of the plastic mixtures that are traditionally difficult to separate. hamos GmbH in Penzberg has developed a series of modern electrostatic separators that are used with great success in the industry, especially in the recycling of plastic mixtures. Contrary to many conventional processes for the processing of old plastics, the hamos EKS electrostatic plastics separators (Fig. 1) work without the use of liquids or chemical additives, and are characterized by high throughputs, low sorting costs, and maximum achievable product purities.
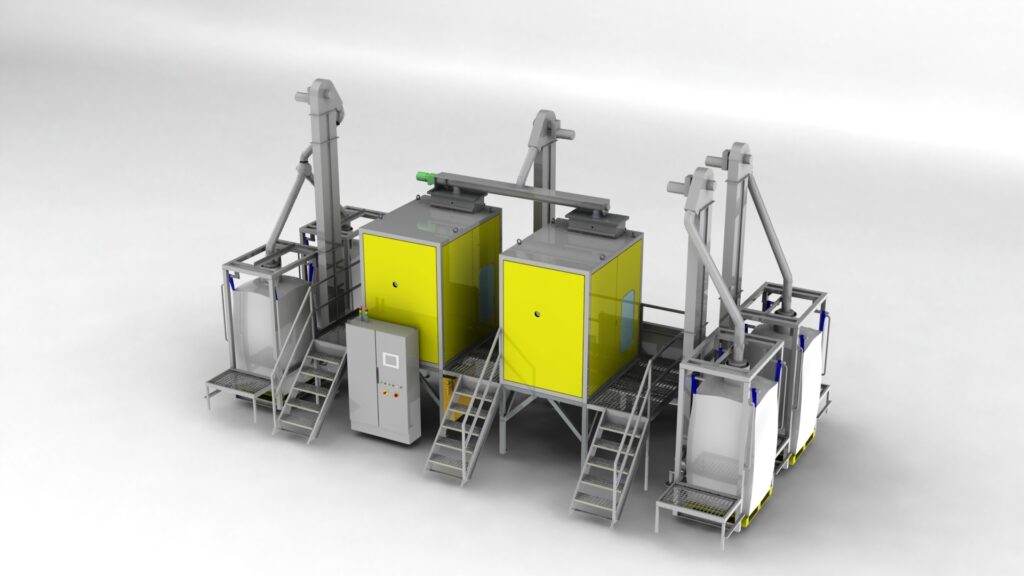
Electrostatic separators use the different triboelectric charges on different plastics for separation: certain plastics become negatively charged when there is friction or direct contact between the particles due to electron transfer, whereas other plastics acquire a positive charge (Fig. 2). A prerequisite for charging is that the plastic particles differ from each other in their dielectric constant. The charged product mixtures can be separated with a subsequent separation unit integrated in the EKS. An electrode system supplied with high voltage is used for this: negatively charged particles are attracted by a positive electrode, whereas positively charged particles are repelled (Fig. 3).
Fig. 2 Tribo-electric charging of plastics by electron transfer Fig. 3 Separation of polarised plastics in a high voltage field
As the physical, as well as chemical properties of the individual plastic particles, play a significant role, dust, soiling, moisture, etc. must be removed before separation, in order to obtain a satisfactory separation result. A particle size of 2 – 12 mm is ideal.
The process can be used for both production waste and post-consumer plastics. With minor modifications, one and the same machine can be used to separate different plastic mixtures. Thousands of different mixtures have been so far successfully separated into pure fractions in industrial applications or laboratory tests. The electrostatic separation technology from hamos, which is used by companies worldwide, is particularly convincing for separation tasks that are difficult to solve with conventional processes. Examples are the separation of PET and PVC in the recycling of PET beverage bottles or the separation of PVC and rubber in PVC window profile recycling.
Undesirable contamination by PVC flakes repeatedly occurs when recycling PET beverage bottles. The PET flakes become unusable for many applications if the level of this PVC contamination exceeds a certain limit. Separation is not possible using conventional processing methods, as PET and PVC have the same color, specific weight, and particle shape. This separation task is however no problem for the EKS electrostatic separator. As it achieves PET separation efficiency of 90 to 95% against PVC, it can bring PET flake impurities down from, for example, 1,000 ppm (parts per million) to a value of less than 50 ppm, making the PET flakes suitable for high‑quality applications. Customers have been impressed by the high separation efficiency, low energy consumption, and the fact that other impurities are also separated together with the PVC.
It is also possible to equally well electrostatically separate the PE/PP fractions in bottle caps from a washing line into pure PE and PP fractions. These process steps are practiced by customers as far away as Honduras.
Another practical application of electrostatic plastic separation is the recycling of PVC window plastics. PVC windows meanwhile have the largest market share in most European countries, as they impress with their perfect design and universal adaptation to design requirements. They are also easy to maintain and – what is particularly important – can be recycled as often as desired. Not only production waste and profile off-cuts resulting from window production are recycled, but also old windows and doors, roller shutter slats, and similar parts.
PVC window profiles (Fig. 4) are made of particularly high-grade PVC. Additives such as UV stabilizers, color pigments, fillers, etc. result in a durable, long-life, and high‑quality PVC plastic compound with optimum usage properties and universal recycling capability. This means that recycled plastic windows can be turned into new high-tech profiles that easily meet the high-quality standards required of plastic windows. Pure PVC recyclate is used for profile cores and inner layers, only outer cover layers consist of virgin PVC.
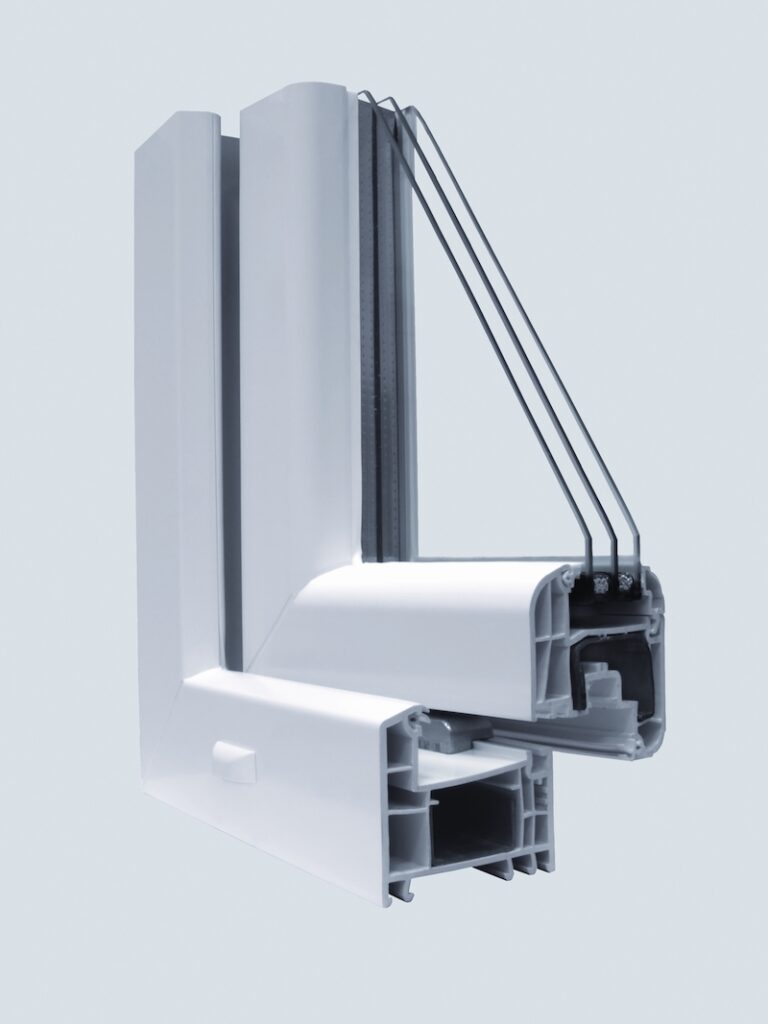
In order to be able to reuse PVC from window profiles, profile sections, or old windows, it is essential however that all materials not made of PVC are completely separated before processing. Rubber and flexible PVC sealing lips, which are inserted into or extruded onto the profile to seal the sash, frame, and glass pane, pose particular problems during recycling.
Flexible PVC mixes with rigid PVC without any problems. There are problems after extrusion, however, in that the color of the granulate varies considerably and the hardness is also negatively affected. The finished product becomes increasingly grey and unsightly, especially with higher proportions of colored (black) profiles.
It is even more problematic if rubber seals are present in the ground material. Rubber seals do not melt in the extruder and do not bond with the PVC. If a profile is extruded from such granulate containing rubber contamination, it can lead not only to unsightly impurities on the surface but also to blockage of extrusion tool channels, which can lead to rejects or even to the loss of production.
The influence of foreign materials such as wood, metal, glass, etc. in the granulate is obvious. Damage to extruders, tools and the product will occur. While these materials can usually be separated without problems using known separation technologies (magnets, setting tables, etc.), the separation of flexible PVC seals and especially rubber seals are not so easy.
Manual sorting attempts to “pull off” rubber seals from profiles and profile sections. This is a very laborious process, as in modern window profiles the rubber seals are inserted into the grooves in the profile with practically no play. Despite the use of pliers or other tools, one sorting employee cannot sort more than 60 – 100 kg of material per hour. Sorting costs incurred in window recycling consequently amount to approx. up to 200 € per tonne for rubber separation alone – a particularly high-cost factor. For this reason, attempts are being made to achieve cost advantages by means of fully automatic processes for the separation of foreign matter.
Therefore our customers – the largest recycling companies for PVC windows in the world – process several hundred thousand tonnes of window material per year fully automatically. Window profile sections, complete profiles, and old windows can be used as feed material.
These products are crushed unsorted in a heavy shredder with a throughput of several tonnes per hour. This is followed by various shredding and separation steps to separate ferrous and non-ferrous metals, stones, glass, and other impurities. Separation of rubber and flexible PVC (Fig. 5) is carried out by hamos EKS electrostatic separators. The separators achieve PVC purities of over 99.5 % in one pass. Throughputs of approx. 1,000 kg/h are possible with standard hamos EKS units. Two or more EKS units are connected in parallel for higher throughputs. A downstream optoelectronic color sorting system from Cimbria separates the small amount of rubber and possible color impurities still remaining in the ground material, so that the PVC regrind is subsequently characterized by purity of over 99.995 % and a high-grade white color.
All the regrind produced in this way is now extruded by high-performance extruders. Possible color variations are compensated by the addition of white pigment, and any possible minor impurities that may still be present are separated out by melt filters. The purity of the white material is almost identical to that of the original material so that this product can be used without any problems in the production of new windows.
Even the “reject or waste fractions” arising in the individual sorting steps are electrostatically re-sorted in order to recover any residual PVC that may possibly be present. This results in highly concentrated waste streams and, on the other hand, maximum PVC yield through minimum PVC losses.
Clean rigid PVC is a valuable raw material because of its excellent reusability and its high proportion of additives and pigments. The prices that can be obtained on the market for PVC window recyclate are high. Due to the high performance of electrostatic sorters, almost one hundred percent clean PVC regrind is produced with minimal separation costs. The separation processes require low energy, operate practically fully automatically, and are therefore particularly economical. Fast amortization of the electrostatic separators is therefore guaranteed.
An equally effective line of business is recycling of consumer “white goods”. Here the focus is on a highly concentrated white polystyrene (PS) fraction.
After appropriate pre-treatment of the input material by shredding, metal separation, sorting by density, and color sorting, the resulting bright white PS/ABS fraction is separated further by electrostatics into clean PS and ABS fractions.
A unique field of application for electrostatic plastics separators is the recycling of black plastics from existing mixtures such as WEEE. Typical electronics scrap consists mainly of metals. On average, however, about 20 percent of mixed plastics also accumulate. Given the large amount of electrical equipment recycled annually in Europe, this ultimately amounts to several 100,000 tonnes of plastics.
Mixed plastics from electronic waste consist of many different types of plastics, which arise in varying quantities. If “unwanted”, flame-retardant, or PVC plastics are excluded, the result is a good product share of around 55 percent, consisting of ABS, PS, and PP. In practice, it has been shown that this “good fraction” consists of approximately 50 to 70 percent black plastics.
A combination of dry and wet separation processes is used to process mixed plastics from electronic scrap. Undesired films, fibers, dust, and similar materials are first separated by sieving and air classification. Float-sink separation with liquids of different densities is then used to recover a PS/ABS concentrate, as well as a polyolefin fraction. The mixture of PS and ABS is “selectively dried” during subsequent shredding down to a particle size of below 10 mm. This means that wood, which is found in large quantities in electronics scrap, remains moist, while the plastic is already dry on the surface. It is therefore possible to separate the disturbing wood fraction and other conductive materials by the “corona roller” type of electrostatic separator.
Highly concentrated PS and ABS fractions with purities above 98.5 percent are produced in the subsequent electrostatic plastic-plastic separation process, (Fig. 6). This separation takes place irrespective of the color of the plastics. Black-colored components do not play a role here. An additional effect of this separation stage is that 20% talc-filled polypropylene (PP TV20) can be separated as a separate fraction, as it has the same specific weight as PS and ABS (around 1.05 kg/dm³).

Electrostatic separators for ABS-PS separation are used by various companies worldwide with great success to separate mixed plastics from electronic scrap (Fig. 7).