Lithium, cobalt, and nickels are the key minerals that are used to make lithium-ion batteries. Also, graphite, manganese, alumina, tin, tantalum, magnesium, and vanadium are other battery minerals. Many of these minerals can be recovered when batteries reach the end of their life. This process is economically beneficial and eliminates the risk of explosion from dead batteries. For this recovery, it is necessary to design the process working with high efficiency and establish a facility. One of the main steps to achieve this efficiency is to identify the type of materials to be processed and classify them accurately. For example, although batteries used in electric vehicles (EV) and batteries used in mobile phones are li-ion batteries, their subtypes, and recycling methods are different. EV batteries use LMO (lithium manganese and oxide) and they are made from hundreds of individual lithium-ion cells, that need to be disassembled. On the other hand, cell phone batteries are made of lithium cobalt oxide, and they are in the form of a single cell.
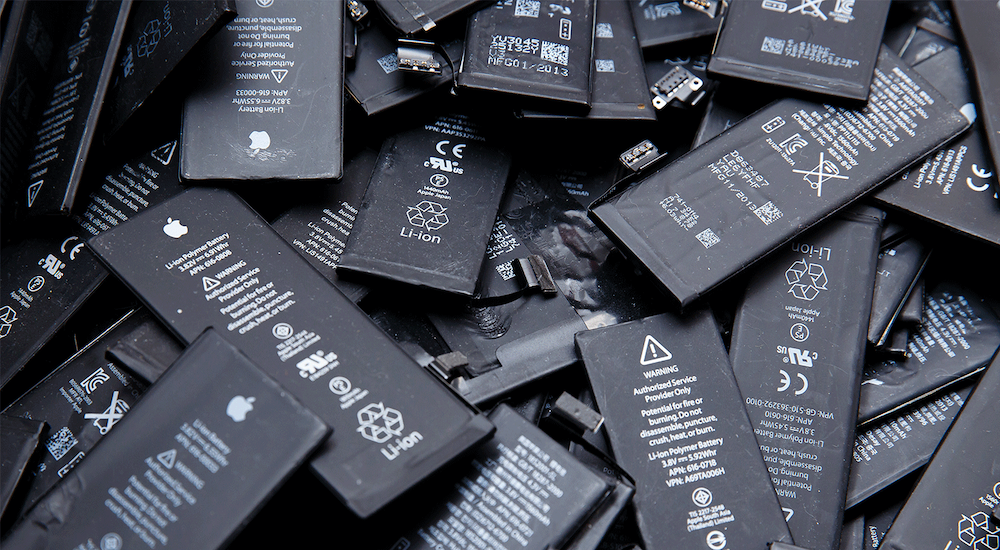
Facilities should be established by considering these chemical differences. The aluminum, copper, cobalt, lithium, nickel, and manganese in the batteries must be separated and recovered separately. Aluminum, copper can be recovered by physical processes, while lithium, manganese, nickel, cobalt in black mass can be recovered by chemical processes. When starting the process, size reduction should be done as a beginning. Then using eddy current, aluminum is separated. The material goes to the air separator where it is separated according to the density, size, and shape difference. Zigzag classification unit is one of the devices that successfully performs this operation by separating copper and black mass. In this unit heavy material is discharged from the base of the zigzag separation enclosure, whilst the lighter material and fine dust particles are transported in the airstream and discharged at the base of the rotary material separator. After these steps to recover high purity copper, manganese, cobalt, nickel, graphite, lithium, the process should be continued with chemical treatments.
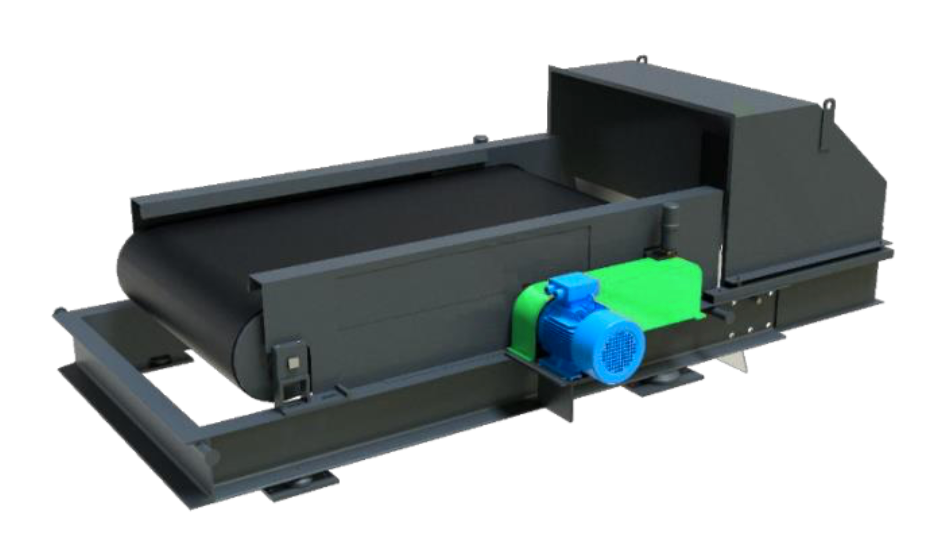
As a Process Machine Company, we design and manufacture Li-Ion battery recycling systems in both physical and chemical processes. We have completed various R&D studies about EV Battery recycling, and it still continues to achieve highest efficiency for each of our customers.