As part of this strategy, it commissioned STADLER, the globally active German company specialized in the planning, production, and assembly of turnkey recycling and sorting plants, to design and install a new state-of-the-art light packaging sorting facility in Eitting.
The new facility is the most advanced light packaging sorting plant in Europe, capable of sorting the packaging fractions by color and, very importantly, even filtering black plastics. This results in extremely high-quality output that can be recycled into new products. With an annual throughput of approximately 120,000 tons, it is also the biggest light packaging plant in Europe.
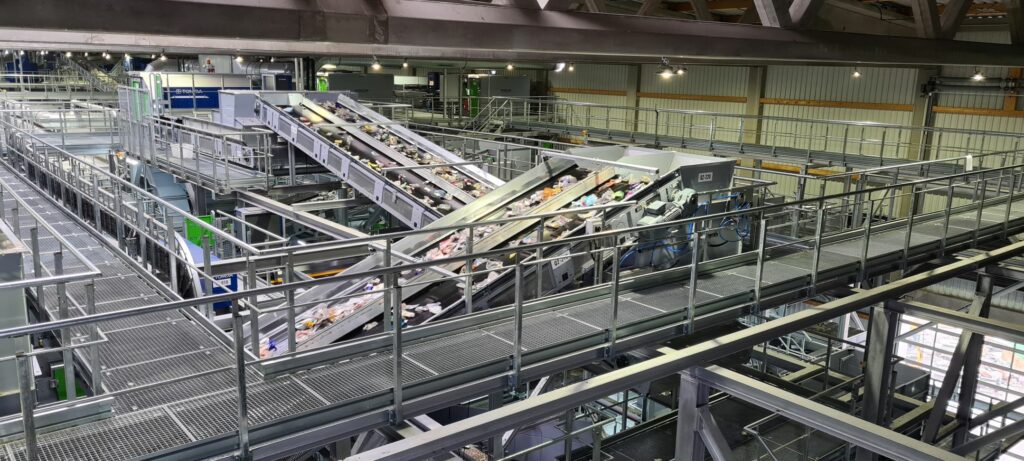
Forward-thinking innovation for high capacity and accurate sorting
The sorting plant receives light packaging made up of tin foil, ferrous and non-ferrous scrap, aluminum, composites with aluminum content, film PE plastics, nets and foam, PP and PS plastics, EPS, PET bottles, other PET, PVC and plastic packaging, TetraPak cartons, paper, and cardboard. The process, which includes advanced fines preparation and automated film color sorting results in 18 different output fractions separated by material and color.
The design required the innovative thinking that is the hallmark of STADLER’s design teams: “This was the largest project to date for us, with 272 conveyor belts installed filling the hall on five levels and supported by over 1,000 tons of steelwork,” explains Wolfgang Köser, joint Project Manager. “To achieve the high-quality sorting PreZero was looking for, we used state-of-the-art technology in our design,” adds Benny Kalmbach, joint Project Manager. “The advanced equipment included 38 NIR (Near Infrared) optical sorters, our ballistic separators, and robot-assisted secondary sorting.”
STADLER’s design team developed a design that not only delivered the required quality output and capacity but also eases of operation. “The continuous level concept facilitates the operation of the system and ensures good accessibility to all the equipment for cleaning and maintenance,” says Wolfgang Köser.
The fully automated bunker management at the plant is another state-of-art process: “This means, for example, that there are no longer staff members permanently tied to the baler. In addition, the desired bale weights – and consequently bale lengths – can be achieved according to the customer’s specifications through the weighing cells under all bunkers. This has the advantage that the trucks can be loaded optimally for the best possible transport result,” explains Benny Kalmbach.
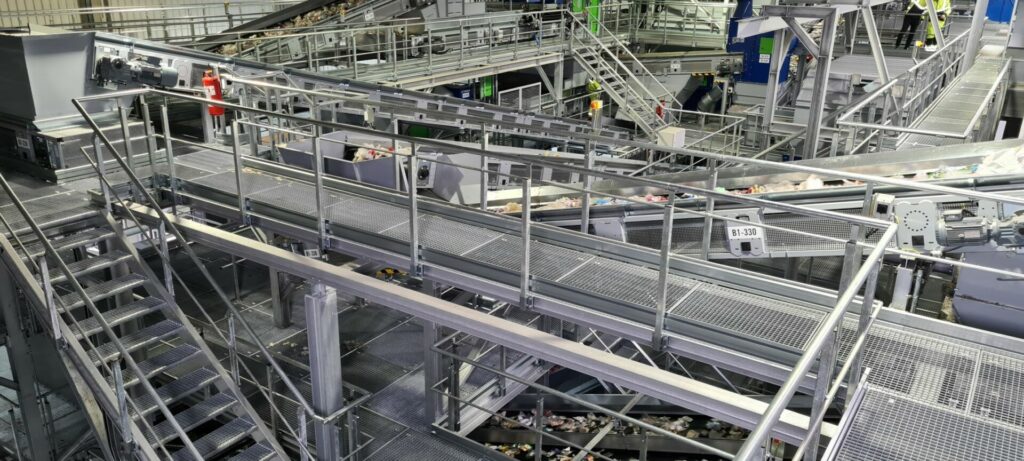
A complex project delivered on time, on a tight schedule
Thanks to a successful close collaboration of the teams at STADLER and PreZero, the project was completed in a very short time, as Wolfgang Köser explains: “We had a very tight schedule, with just 12 months from signing the contract to start-up with material, but we succeeded with good and close cooperation between us at STADLER, and the teams at PreZero and the other companies involved in the project. Short decision-making processes and a target-oriented approach enabled us to move forward quickly at every stage.”
Stefan Kaiser, Head of Engineering Sorting Systems International PreZero Recycling Deutschland, is very satisfied with the whole process, and “the open communication, straightforward thinking, focused and time-efficient collaboration, and on-time delivery. I particularly appreciated how STADLER’s team listens to the customer and their proactive thinking of new ideas, acting as partners.”
The start-up of the sorting plant was on schedule in early January 2022, and “the ramp-up phase is running perfectly,” says Stefan Kaiser.
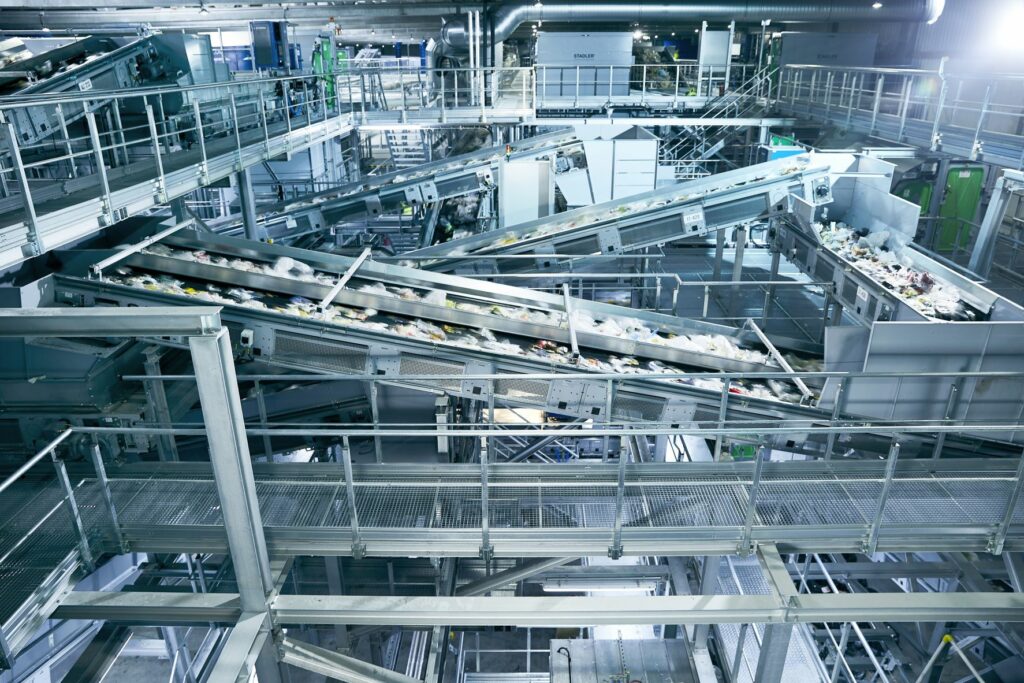
On the path towards a world where resources are not wasted
With the view that any waste that is not recycled is a wasted piece of raw material, PreZero strives for a continuous improvement of its processes, working towards the creation of a world where resources are no longer wasted through closed loops – aiming for 100 percent reusable material. As part of the Schwarz Group, a leading food retail company in Europe, it is able to develop innovative solutions along the entire value chain – from production to retail, collection, sorting, and recycling to reuse – in order to close the loop.
The new light packaging plant designed by STADLER is part of PreZero’s strategy to achieve this goal: “For us, this is the first step in the transition from a waste plant to a production plant of industrial standards,” explains Stefan Kaiser.
For STADLER, the project provided a further opportunity to develop innovative solutions to serve the recycling industry with high-quality recyclates, supporting the transition to an efficient circular economy.