High-torque shredding for diverse materials
With their 48 spirally arranged tools on their 3.6 m long rotor shaft as well as the high torque the ARCTOS BM and OM 36 shredders can process even difficult materials quite easily – the same accounts for the ARCTOS BM 21 with its 28 tools on a 2.1 m long rotor shaft. To make them fit individual requirements, the ARCTOS are available with several drive options and two different kinds of easily exchangeable rotor tools. Being thus able to handle a broad spectrum of materials with precision and reliability the shredders can be used in numerous industrial and commercial applications. Among these are the production of Refuse Derived Fuel (RDF) for power plants and cement production as well as the pre-shredding or bale breaking in lightweight package recycling facilities. They are also already in use preparing biomass for fermentation and composting. Even monocharges – such as tyres – and contaminated municipal waste can be processed.
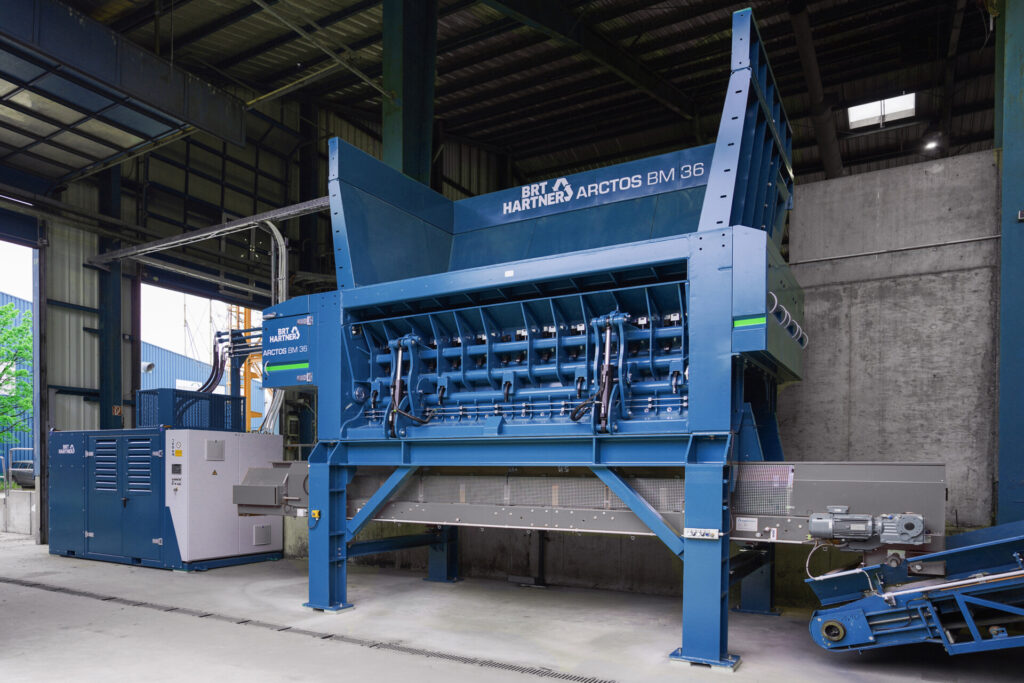
Size reduction to the point
To ensure the efficiency of the shredding process, it is often necessary to stay inside a certain range with the output particle size. To predefine the desired size as precise as possible, the ARCTOS shredding line has adopted the proven cutting gap adjustment and the screen basket system of the TEUTON series.
- Cutting gap adjustment
The cutting gap can be set in six different steps, allowing for specific adaption to the required outcome. The adjustment of the cutting gap itself is as simple as effective: the hydraulic shredding hood will swing out via remote control. Then the suspension of the shredding hood can be changed by replacing or turning a small metal plate on either side. No tools are required. The adjustment is part of the many standard features. - Screen basket system
For even more precision in predefining the final particle size the ARCTOS can optionally be equipped with a screen basket. There are stripe and hex shaped screen baskets with different hole sizes depending on the material and the required output. The change of the screen basket works by opening the shredding hood too.
This flexibility in pre-defining the final grain size does not only ensure that the material is perfectly suited for its next phase of processing, but operators can even achieve the desired granulation for specific recycling needs in one single step.
Large-volume infeed
Handling large materials often poses challenges in recycling operations, but the ARCTOS shredders overcome these hurdles with ease. Especially the ARCTOS BM and OM 36 with their loading width of around 3.8 meters and intake widths of 3.6 meters allow for efficient feeding of bulky materials using wide wheel loader buckets. The spacious hopper further enhances storage capacity, ensuring continuous operation with minimal interruptions. To fit precisely to the costumers needs, the hopper volume and loading width can be customized.
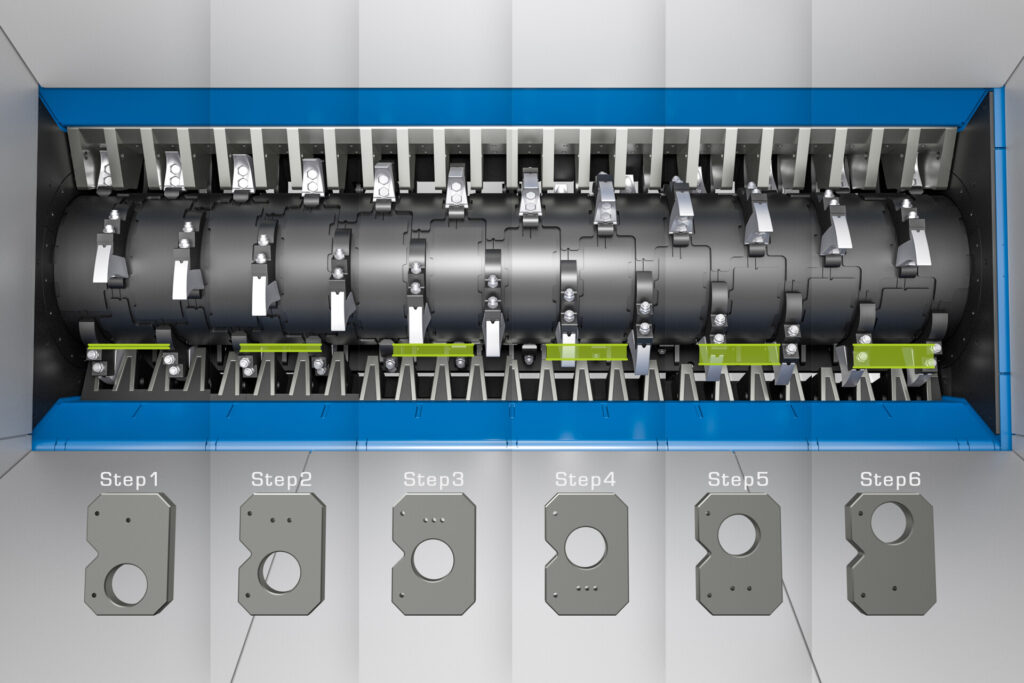
Efficient and durable design
The ARCTOS shredders are designed for maximum machine availability. The most important features are:
- QuickChange rotor tools
The double bolted Twincut or Multigrip tools can be easily exchanged. - Marathon plate segments
Whole segments of the rotor surface can be replaced. - Segmented counter tools
Fast change of the counter tools due to socket pin system. - Screwed comb elements
Modular design enables spare parts to be sent by post. - Plug-and-play setup
Shipment in standard freight containers and pre-wired control units simplify the installation.