This was the case in 2019 when Blue Machinery (Southern) Ltd secured a multi-million pound deal for a MRF plant at Amgen Cymru (in association with Rhondda Cynon Taf County Borough Council) in Wales. The plant was designed using equipment from several leading manufacturers such as Westeria, Tomra and BRT Hartner. When it came to baling the sorted materials at the end of the process, Blue Machinery turned to CK International, a market leader in waste compaction services, to come up with an ideal baling solution that would fit the customer’s requirements within the new plant design.
Working closely throughout the design phase
CK International had to be involved from the early stages of the design process. It was important for the customer that the balers integrated into the plant and that the sorted waste was delivered to them without any issues. The material was designed to come from bunkers and into the balers via large Westeria conveyors. The collaboration between Blue and CK in the design process was essential to the smooth running of the plant. For example, if there wasn’t enough material coming off the conveyors, then the plant was designed to recirculate the waste until there was the right amount to make a full bale. It also meant that the balers supplied needed to able to handle a large amount of waste. The decision was made early on that two CKTR82 Twin Ram balers would be the best solution for this project – this would ensure the bunkers were cleared quickly and at different times. One baler needed to cope with the high throughput alone and not negatively impact the running of the overall plant. Space-saving was also a priority within the design of the plant. CK International was able to change the location of the power packs to ensure the equipment fitted into the optimum position.
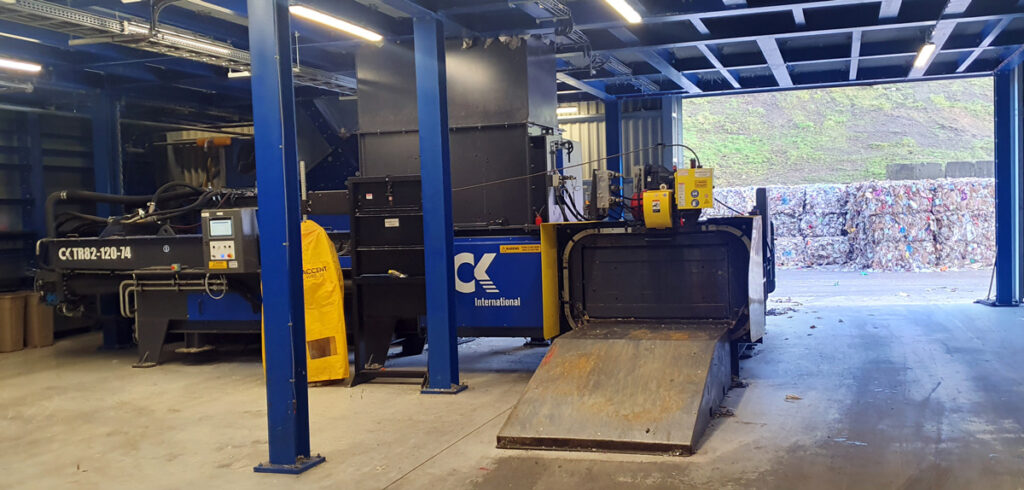
Baling equipment
In Amgen’s previous plant, they had two channel press balers. However, it was clear that these machines were not going to be sufficient to achieve the bale density that they now required. They also had seven different materials that they needed to bale. It was essential that the baling equipment selected would allow for the changeover of materials easily without any contamination. It was for this reason that a CKTR82 Twin Ram baler was the ideal option. This model is also designed to produce high-density mill-size bales, optimising space in shipping containers and maximising payloads. With regards to the channel press balers that were in the previous plant, CK International decommissioned these machines, took them to the customer’s other site and set them up there.
Delivering on commitments

One of the customer’s key requirements in this project was to have improved throughputs. CK International committed to a figure of 8T/hr on each baler to meet the performance criteria specified. Although this was a big commitment, CK International knew that their balers could achieve this and Blue had the confidence in them to deliver.
The reliability of the equipment was also important, mainly because the waste material is coming directly off the plant – so if a baler breaks down it can affect the entire plant. CK International have an excellent backup service and fast response rate, so this was also an area where Blue had complete confidence in their partner to deliver on. With a plant of this size and considering the cost of downtime, delivering this project on schedule was essential. Blue had to be confident that their partners would stick to their lead times.
Integration of data management systems
This is a high-tech, automated plant where the control centre and remote data management is key. CK International had a programmer on-site for one week, working in partnership with Blue to ensure that the two balers were fully integrated with the plant’s SCADA system. The CK International Data Management System means that the customer can alter the materials that they are baling at the push of a button. They also have the capability of changing the material through this system. The system allows the plant manager to view how many bales have been processed on a daily, monthly or annual basis and gives them a breakdown of material types baled and also any downtime in the machines. All this data is available on a web browser or mobile phone and is extremely useful when making any future business decisions.
Reaping the rewards
Three years on and this MRF facility is still going strong as are the two twin ram balers. The throughput of 8T/hr has been as promised. In terms of backup, any call-outs or breakdowns have been quickly responded to.
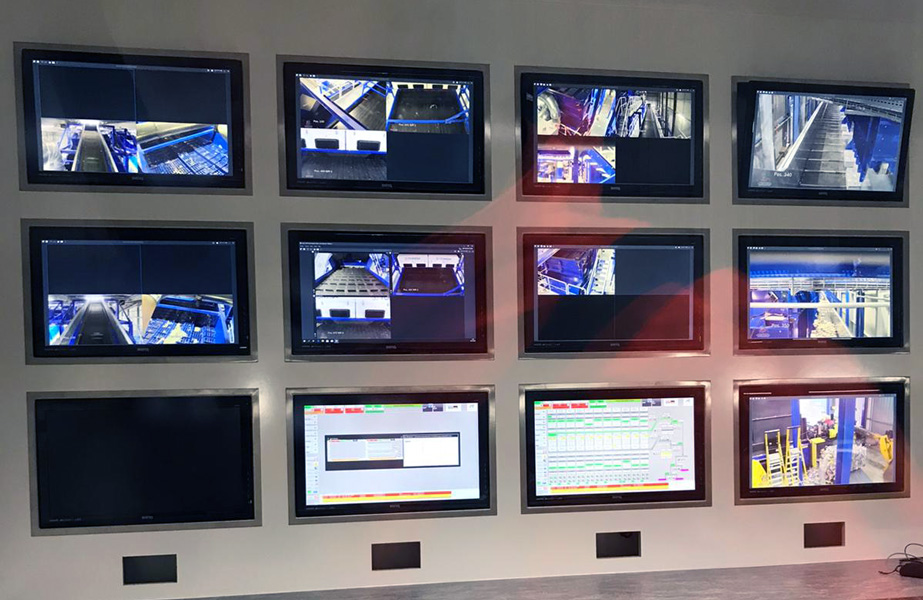
Tom Rutherford, Blue Machinery (Southern) Ltd explains, “The exceptional build quality of CK International’s baling equipment is well-known, however, it was their experience and expertise that shone through with this project. They offered unique solutions and suggestions throughout this project which not only benefited the customer but also assisted our team. Their focus on providing exceptional customer support meant that we were confident they wouldn’t let us or the customer down. We wouldn’t hesitate to work alongside CK International again for any future projects. Their expertise in waste compaction equipment is invaluable.”
Amgen’s Operations Manager, Ian McAlister commented on the benefits they are seeing from the new plant: “This has been a fantastic project for us. The knowledge and expertise from everyone involved has been really impressive. The new MRF has given us the versatility to bale all materials on-site. It has a processing capacity of 18-20 tonnes per hour and around 65,000 tonnes per annum – where previously we were processing around 32,000 tonnes per annum. With regards to our bales, we have greatly improved on our bale density and can better optimise loads for transport.”