Alongside the constant pressure of innovation from within the industry, Fantoni faces the chronically poor availability of fresh wood in Italy, the company’s homeland, as well as being confronted by a shortage of high-quality recyclable wood. There is also growing demand on the market for more sustainable products. At least 50% of panels are to be manufactured from recycled material by 2030, so an environmental approach to resources doesn’t just make ecological sense but is an economic necessity too.
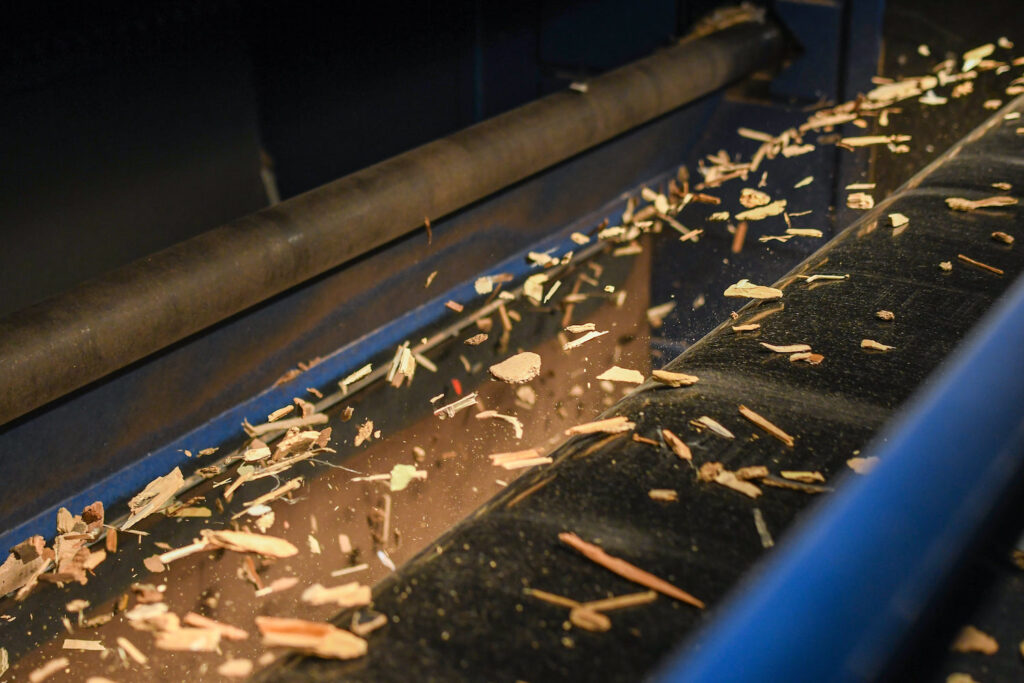
Investing in a sustainable future
Fantoni has invested €150 million in sustainability over the last four years, resulting in innovative processes, automated logistics, the longest continuous MDF press in Europe and a modern sorting facility for wood waste, which forms the basis for sustainable MDF: clean wood fibers for producing the first medium-density fibreboard (MDF) with a higher proportion of old wood than fresh wood.
Magnetic separation and sensor technology from one source
In cooperation with STEINERT, Fantoni developed a sorting concept in which impurities are removed in three steps. Once the material flow has been split into two-grain sizes, metals are removed using magnet and eddy-current technology. Then X-ray and near-infrared technology cleans the wood from residues such as glass, stone and plastic, deploying exclusively STEINERT
separation and sorting machines. The carefully selected and perfectly coordinated machines ensure optimum performance and therefore optimum sorting quality of the 250 000 tons of wood waste they process a year.
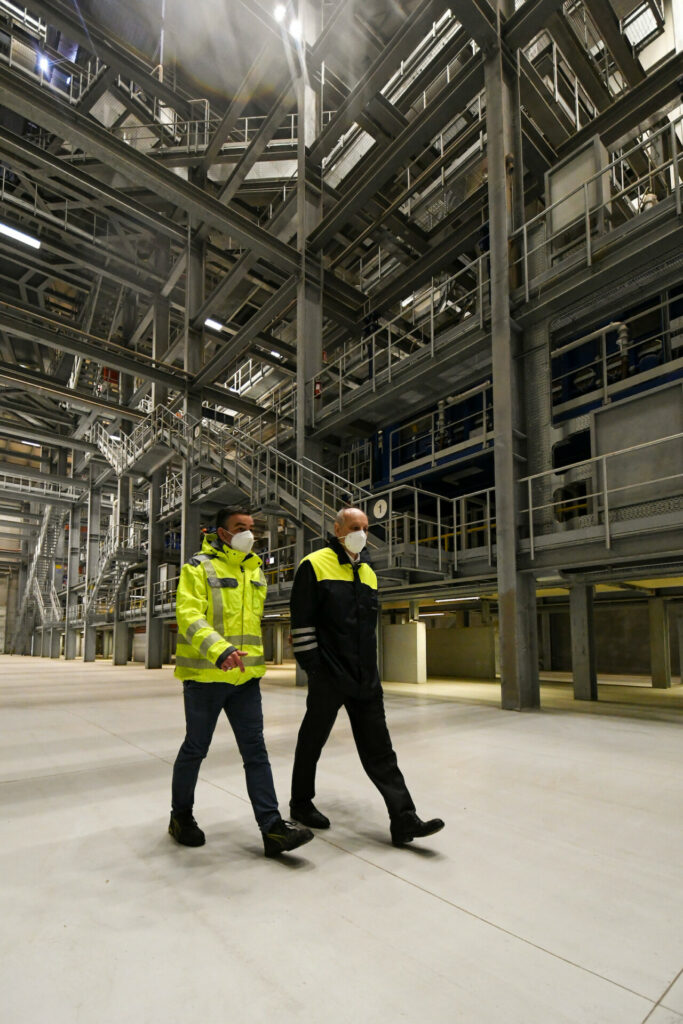
Making objective decisions
To safeguard its investments, Fantoni tested its own sorting material at the STEINERT Test Center at the headquarters in Cologne, Germany. “The option to do this was a key factor in our decision. Not only to get a guarantee of the sorting performance we targeted but also to be able to see the machines in action and convince ourselves of their build quality. After all, we hope they will run for 20-50 years,” reflects Umberto Meroni, Technical Director at Fantoni. “Ultimately, we were won over by the robustness of the STEINERT machines and the UniSort technology for detecting black objects, which felt more sophisticated than those of the competition.”
Working with STEINERT
The entire project phase ran through the ongoing pandemic, during a time when the scope for contact and travel was increasingly complex. Marco Fantoni, member of the board at Fantoni Spa, is happy with the result and has only praise for STEINERT’s support: “We very much appreciated the STEINERT personalities. Especially during the commissioning and start-up phase, STEINERT has proven to be a reliable partner.”

A positive outlook
For Fantoni, this investment represents a milestone in MDF production, delivering a much more efficient product in both monetary and environmental terms. For the first time ever, furniture-grade wood can now be recovered from municipal solid waste. Being the first to develop and offer this system will give us significant competitive advantages”, says Marco Fantoni. The company is showing that tradition and innovation are not mutually exclusive but need one another to create history for future generations. But they are not resting on that and are keeping their sights firmly set on their long-term goal, a vision of a circular economy, and are already working on the next project.