The company binderholz manufactures at 29 locations in Europe and America. The product range includes sawn and profiled timber, single- and multi-layer glued solid wood panels, glued laminated timber and binderholz cross laminated timber BBS. In addition, there are products for the do-it-yourself sector such as multi-purpose boards, garden- and construction timber. At the binderholz site in Jenbach/Tyrol, the waste wood is completely processed in the sense of the zero-waste approach. There, the shredders of the Austrian premium manufacturer UNTHA, produce homogeneous, usable wood chips that can be further processed into biofuels and green electricity.
Biofuels from waste wood
“The love for wood as a valuable material has been the basis of our actions since the company was founded in That is why the responsible use of resources is also an important part of our philosophy. The shredders from UNTHA support us in processing residual wood to produce biofuels,” says Martin Mair, Head of factory 1 at binderholz. At the Jenbach site, around 100 m³ of waste wood accumulate every day. To be able to process this sensibly, it must first be shredded. Ten UNTHA shredders are available for this purpose, including one LR1000 model and nine RS30 models. The shredded residual wood is transported to silos via an extraction system. Part of it is then used as an energy source for factory buildings, production halls and drying chambers. The rest is processed into pellets. This procedure ensures that all wood residues are sensibly utilised.
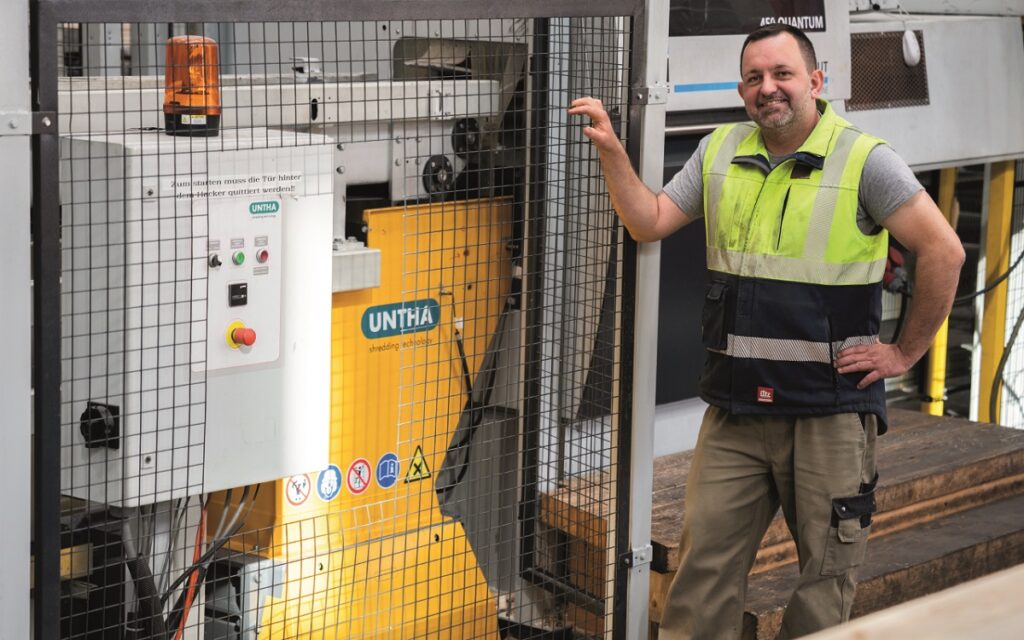
Reliable shredders, convincing service
The shredding process of the residual wood takes place simultaneously with the ongoing production operation. binderholz has been using wood shredders from UNTHA for years. The compact shredders of the RS30 series are directly integrated into the production lines and run in 24-hour operation. The resulting wood residues fall from above into the hopper of the shredder and are immediately shredded. The larger shredder stands outdoors in a pit, with only the hopper protruding. This makes it easier to feed the shredder with the wood residues using a wheel loader or a conveyor belt.
The company’s requirements for a new shredder included: a high throughput capacity, automatic feeding, and low noise pollution. “Most of the residual wood is processed outside, so the lowest possible noise level was an important criterion for us. At the same time, the machine should be able to process large quantities of residual wood as quickly as possible. Not many shredders can manage this combination. But this shredder meets all the requirements,” Martin Mair says. The quick availability of wear and spare parts was also an important criteria. binderholz takes care of all necessary repairs and adjustments itself. The necessary parts are ordered directly by the employees of the UNTHA Service Competence Centre. “UNTHA offers not only reliable machines but also uncomplicated service – a quick phone call or e-mail is all it takes, and the parts are on their way to us. We are very satisfied with our decision to buy shredders from UNTHA,” says Martin Mair, summarising the purchase decision.
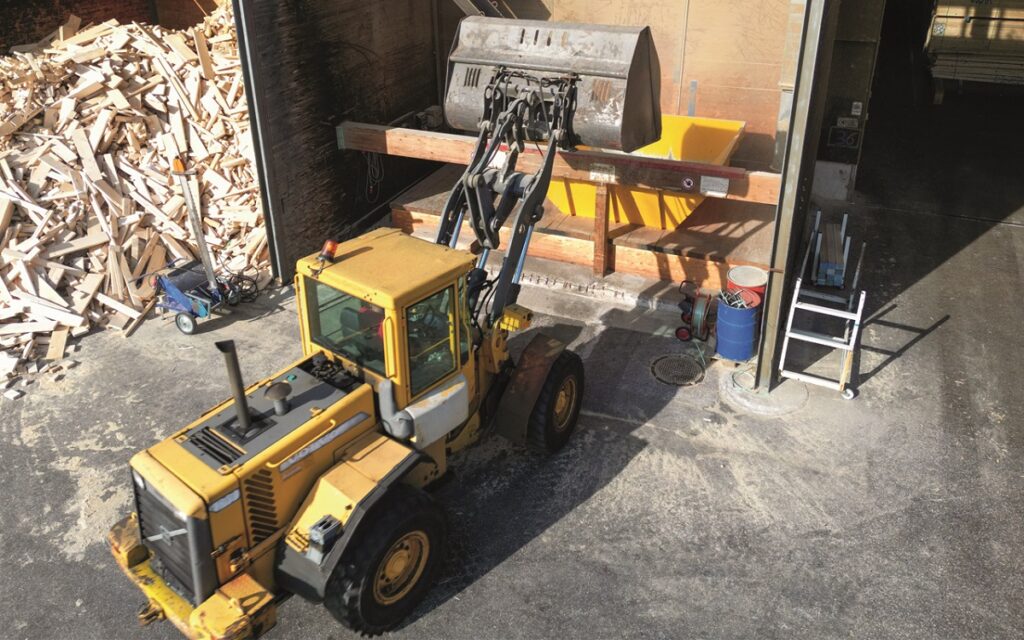
The LR1000 and RS30 shredders at a glance
The UNTHA LR1000 is characterised by particularly high throughput, reliable shredding of large quantities of wood and the wide hopper – this is perfect for feeding with a wheel loader. The 1-shaft shredder is ideally suited for continuous operation. The cutting tool with a special knife geometry ensures energy-efficient shredding. If no material is fed for three minutes, the motor switches off automatically, thus saving electricity.
The 4-shaft shredders of the RS series from UNTHA are robust and compactly designed. They are suitable for shredding different materials. The slow-running shredders are particularly insensitive to disturbances and require little maintenance. The low speed of the cutting shafts ensures low noise and dust pollution.